Listed Below Are Five Procedures Followed By Eikenberry Company
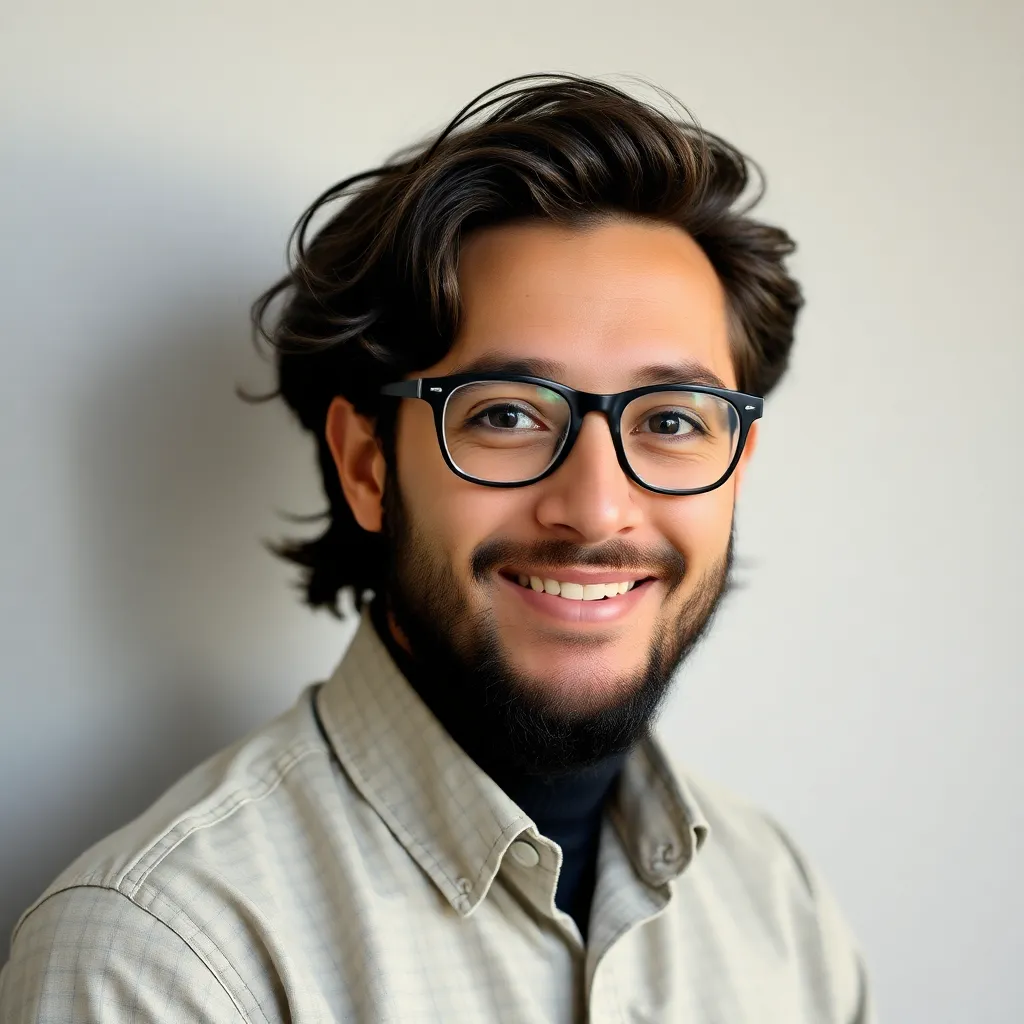
Onlines
Apr 22, 2025 · 8 min read

Table of Contents
Five Key Procedures at Eikenberry Company: A Deep Dive into Operational Excellence
Eikenberry Company, a hypothetical example for illustrative purposes, prides itself on its robust and efficient operational procedures. This article delves into five key procedures that underpin Eikenberry's success, examining their implementation, impact, and contribution to overall operational excellence. Understanding these processes offers valuable insights for businesses striving for improved efficiency and streamlined workflows. We'll analyze each procedure, exploring best practices and highlighting potential areas for adaptation and improvement in various organizational contexts.
1. Streamlined Procurement Process: From Requisition to Receipt
Eikenberry’s procurement process prioritizes speed and accuracy, minimizing delays and reducing costs. The process unfolds in five distinct stages:
1.1 Requisition:
This initial stage involves a formal request for goods or services, submitted through a centralized online system. The system automatically routes the requisition to the appropriate approving authority based on pre-defined budget limits and departmental responsibilities. This automated routing dramatically reduces processing time compared to manual systems. The system also includes features that identify potential duplicate requisitions, preventing unnecessary spending. Detailed descriptions, including item specifications, quantity, and required delivery date, are crucial for avoiding misunderstandings and delays.
1.2 Vendor Selection:
Eikenberry maintains a pre-approved vendor list, rigorously vetted based on factors such as quality, reliability, pricing, and ethical practices. This pre-qualification process significantly streamlines vendor selection, allowing for quicker sourcing of goods and services. The system also incorporates a competitive bidding process for high-value purchases, ensuring cost-effectiveness. Transparency in vendor selection is crucial for maintaining trust and accountability.
1.3 Purchase Order Generation:
Upon approval of the requisition, the system automatically generates a purchase order (PO), containing all relevant details, including item descriptions, quantities, pricing, payment terms, and delivery schedule. The PO is electronically transmitted to the selected vendor, minimizing the risk of errors and accelerating the procurement cycle. Electronic tracking of POs allows for real-time monitoring of the order's progress.
1.4 Goods Receipt and Inspection:
Upon delivery, the receiving department conducts a thorough inspection of the goods, verifying quantity, quality, and conformance to specifications. Discrepancies are immediately reported to the procurement department for resolution. The system integrates seamlessly with inventory management, updating stock levels upon successful receipt. Robust quality control at this stage is paramount in ensuring product quality and minimizing potential losses.
1.5 Payment Processing:
Once the goods are inspected and approved, the system triggers the payment process, automatically generating invoices and transmitting them to the finance department for processing. Eikenberry employs automated payment systems, reducing manual effort and enhancing efficiency. Reconciliation of invoices against purchase orders ensures accuracy and prevents payment errors. This entire process is designed to ensure efficiency and transparency in procurement.
2. Robust Inventory Management System: Optimizing Stock Levels
Eikenberry employs a sophisticated inventory management system based on Just-In-Time (JIT) principles. This minimizes storage costs while ensuring sufficient stock to meet production demands. Key aspects of their system include:
2.1 Demand Forecasting:
The system utilizes historical sales data, market trends, and seasonal variations to predict future demand accurately. This predictive capability enables Eikenberry to optimize inventory levels, avoiding overstocking or stockouts. Accurate forecasting is crucial for minimizing holding costs and maximizing production efficiency.
2.2 Real-Time Inventory Tracking:
The system uses barcodes and RFID technology to track inventory in real-time, providing an up-to-the-minute view of stock levels across all locations. This allows for proactive identification of low-stock items and prompt reordering, preventing production delays. Real-time visibility is critical for effective inventory management.
2.3 Automated Reordering:
The system automatically triggers purchase orders when stock levels fall below pre-defined thresholds. This automated reordering eliminates manual intervention, saving time and reducing the risk of human error. Automated reordering significantly reduces lead times and improves supply chain efficiency.
2.4 Regular Inventory Audits:
Eikenberry conducts regular physical inventory audits to reconcile physical stock levels with system records. This helps to identify discrepancies and ensure the accuracy of inventory data. Regular audits are crucial for maintaining the integrity of inventory records.
2.5 Waste Reduction Initiatives:
The system also incorporates features to track and minimize waste, identifying areas for improvement in the production process and reducing material costs. Continuous improvement in inventory management is essential for achieving operational excellence.
3. Effective Communication Channels: Fostering Collaboration and Transparency
Eikenberry recognizes the critical role of effective communication in operational efficiency. Their communication strategy leverages various channels to ensure seamless information flow across departments and with external stakeholders.
3.1 Internal Communication Platforms:
Eikenberry uses a comprehensive internal communication platform, integrating various tools like instant messaging, email, project management software, and a company intranet. This centralized platform ensures that employees have access to the information they need, when they need it. Clear and concise communication is essential for avoiding misunderstandings and delays.
3.2 Regular Team Meetings:
Regular team meetings are held to discuss project updates, address challenges, and foster collaboration. These meetings promote open communication and facilitate timely problem-solving. Structured agendas and clear meeting objectives are crucial for maximizing the effectiveness of these meetings.
3.3 Feedback Mechanisms:
Eikenberry has established mechanisms for collecting feedback from employees, customers, and suppliers. This feedback is used to identify areas for improvement and enhance operational processes. Active listening and responsiveness to feedback are essential for continuous improvement.
3.4 Transparent Reporting:
Eikenberry employs transparent reporting systems, providing regular updates on key performance indicators (KPIs) to all stakeholders. This transparency fosters trust and accountability, empowering employees to contribute to the company's success. Data-driven decision making relies heavily on accurate and timely reporting.
3.5 Cross-Functional Collaboration:
Eikenberry encourages cross-functional collaboration, breaking down silos between departments to foster seamless workflows and shared understanding. Collaborative projects and shared responsibilities promote a more cohesive and efficient organizational structure.
4. Rigorous Quality Control Procedures: Ensuring Product Excellence
Eikenberry maintains stringent quality control procedures throughout its operations, from raw material procurement to finished product delivery. This commitment to quality is reflected in several key procedures:
4.1 Incoming Material Inspection:
All incoming materials are rigorously inspected upon receipt to ensure they meet the required specifications. Materials failing to meet standards are rejected and returned to the supplier. Strict quality standards at the beginning of the process prevent downstream issues.
4.2 In-Process Quality Checks:
Regular quality checks are conducted throughout the production process to identify and correct any deviations from specifications. This proactive approach prevents defects from reaching the final product. Regular monitoring is key to early identification of potential problems.
4.3 Finished Goods Inspection:
Before shipment, all finished goods undergo a final inspection to ensure they meet the highest quality standards. This rigorous inspection process minimizes the risk of customer complaints and returns. Thorough final inspection ensures customer satisfaction.
4.4 Continuous Improvement Initiatives:
Eikenberry actively seeks ways to improve its quality control processes through continuous improvement initiatives like Six Sigma or Lean methodologies. This commitment to ongoing improvement ensures that quality standards remain high. Continuous improvement is essential in maintaining high-quality products.
4.5 Customer Feedback Integration:
Eikenberry actively collects and analyzes customer feedback to identify areas for improvement in its quality control processes. This customer-centric approach ensures that quality standards are aligned with customer expectations. Customer-centric approach drives continuous improvement and product excellence.
5. Employee Training and Development: Investing in Human Capital
Eikenberry recognizes its employees as its most valuable asset. The company invests heavily in employee training and development programs to enhance their skills and knowledge.
5.1 Onboarding Programs:
New employees undergo a comprehensive onboarding program that familiarizes them with company culture, policies, and procedures. This structured approach ensures that new hires are quickly integrated into the team and productive. Structured onboarding is crucial for effective employee integration.
5.2 Continuous Learning Programs:
Eikenberry offers continuous learning programs, including workshops, seminars, and online courses, to enhance employees' skills and knowledge. This ongoing development helps employees stay up-to-date with industry best practices and technological advancements. Continuous learning helps employees adapt to industry changes and grow within the company.
5.3 Skill Development Programs:
Eikenberry provides skill development programs tailored to individual employee needs and career aspirations. This personalized approach fosters employee growth and enhances their contribution to the company. Personalized training ensures effective skill enhancement.
5.4 Performance Management System:
A robust performance management system provides regular feedback to employees, enabling them to identify areas for improvement and track their progress. This system promotes employee growth and enhances performance. Regular performance reviews allow for timely feedback and guidance.
5.5 Employee Recognition Programs:
Eikenberry implements employee recognition programs to acknowledge and reward outstanding performance. This fosters a positive work environment and motivates employees to achieve their full potential. Employee recognition fosters a positive and motivating work environment.
By implementing these five key procedures, Eikenberry Company demonstrates a commitment to operational excellence, fostering efficiency, improving quality, and maximizing employee potential. These procedures, while specific to a hypothetical company, offer valuable lessons and best practices applicable to organizations of all sizes and across various industries seeking to enhance their operational effectiveness and achieve sustained growth. Remember that adaptation and refinement are crucial; what works for Eikenberry might need adjustments to fit your specific organizational context. Continuous evaluation and improvement are paramount to maintaining a high level of operational excellence.
Latest Posts
Latest Posts
-
A Researcher Wants To Observe Preschoolers
Apr 22, 2025
-
Equation Writing And Predicting Products Lab 25 Answer Key
Apr 22, 2025
-
8 2 Additional Practice Trigonometric Ratios Answer Key
Apr 22, 2025
-
Exploring The Behavior Of Gases Answer Key
Apr 22, 2025
-
Ap Lang 2020 Practice Exam 1 Mcq Answers
Apr 22, 2025
Related Post
Thank you for visiting our website which covers about Listed Below Are Five Procedures Followed By Eikenberry Company . We hope the information provided has been useful to you. Feel free to contact us if you have any questions or need further assistance. See you next time and don't miss to bookmark.