Managers Are Considered Within An Organization Osha
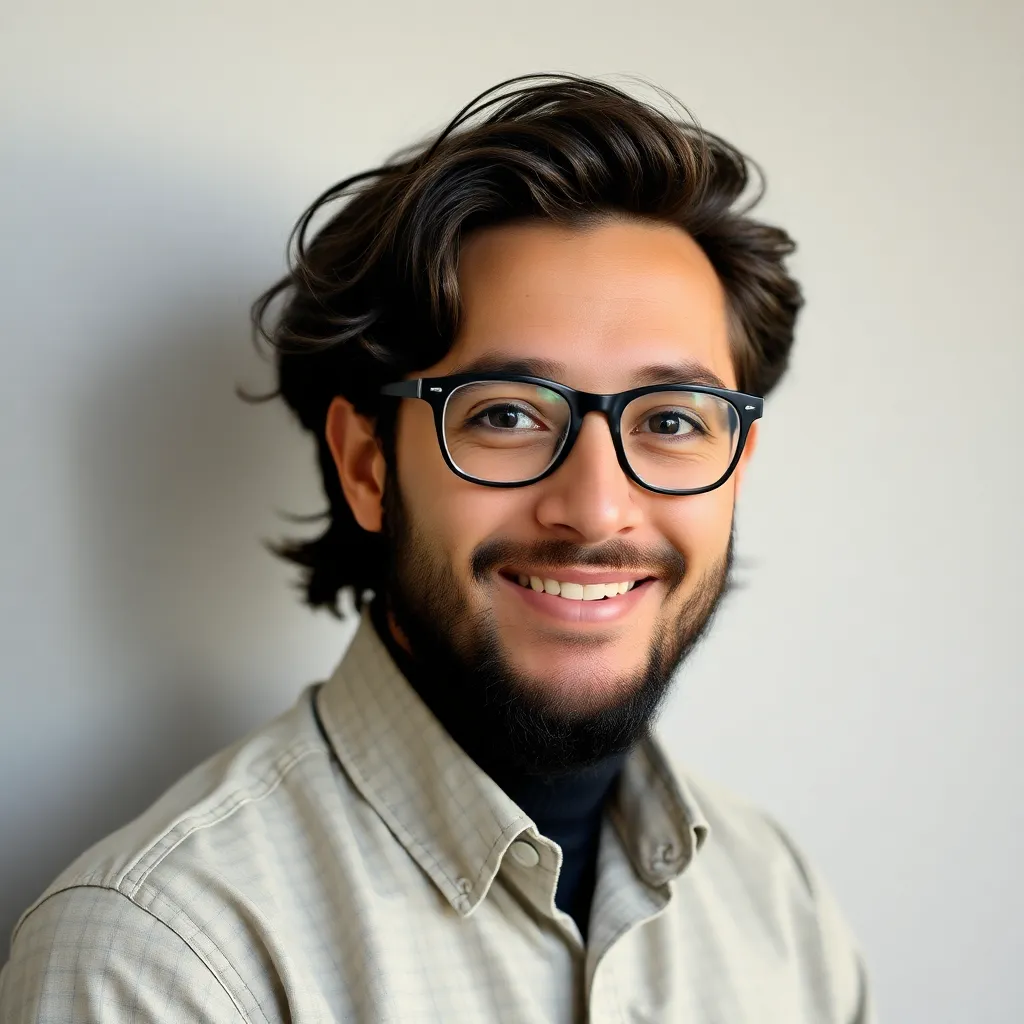
Onlines
May 09, 2025 · 6 min read
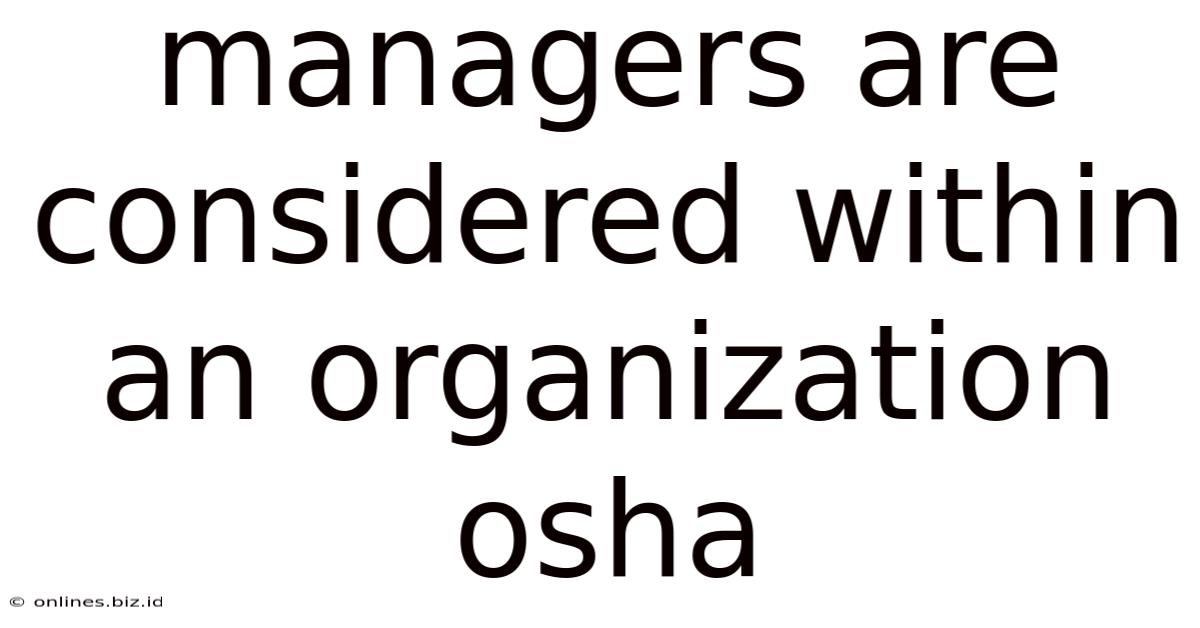
Table of Contents
Managers: The Crucial Link in OSHA Compliance Within an Organization
Managers play a pivotal role in ensuring a safe and healthy work environment, a cornerstone of Occupational Safety and Health Administration (OSHA) compliance. They aren't simply supervisors; they are the frontline leaders responsible for translating OSHA regulations into actionable practices and fostering a culture of safety within their teams. This article delves deep into the multifaceted responsibilities of managers concerning OSHA, exploring their duties, the consequences of non-compliance, and best practices for building a robust safety program.
The Manager's Role: Beyond Supervision
While the legal responsibility for OSHA compliance rests with the employer, managers are the critical link between the organization's overall safety policy and its practical application on the ground. Their involvement extends far beyond simply assigning tasks; it's about actively leading and participating in safety initiatives. This involves several key responsibilities:
1. Understanding and Implementing OSHA Standards
Managers must possess a thorough understanding of the OSHA standards relevant to their specific industry and workplace. This isn't simply about passively reading the regulations; it requires actively interpreting and applying them to daily operations. This includes:
- Identifying Hazards: Managers must proactively identify potential hazards within their work areas. This involves regular inspections, employee feedback sessions, and the diligent review of incident reports.
- Implementing Control Measures: Once hazards are identified, managers need to implement appropriate control measures to mitigate risks. This can range from engineering controls (e.g., installing safety guards on machinery) to administrative controls (e.g., implementing safe work procedures) and personal protective equipment (PPE) provision.
- Ensuring Proper Training: Managers are responsible for ensuring their employees receive adequate training on relevant OSHA standards, safe work practices, hazard recognition, and the proper use of PPE. This training should be regular and tailored to the specific tasks performed.
- Maintaining Accurate Records: Detailed records of safety training, inspections, incidents, and corrective actions are crucial for demonstrating compliance. Managers play a vital role in maintaining these records accurately and completely.
2. Fostering a Safety-Conscious Culture
Creating a culture of safety is paramount. Managers achieve this through:
- Leading by Example: Employees are more likely to prioritize safety if their managers do the same. Managers must demonstrate a visible commitment to safety through their own actions and behaviors.
- Open Communication: Managers should establish open channels of communication to encourage employees to report hazards and near misses without fear of retribution. This fosters a culture of transparency and trust.
- Employee Involvement: Actively involving employees in safety planning and implementation fosters ownership and commitment. This could involve safety committees, suggestion boxes, or regular safety meetings.
- Recognizing and Rewarding Safe Behavior: Positive reinforcement is a powerful tool for motivating safe behaviors. Managers should recognize and reward employees who consistently demonstrate a commitment to safety.
3. Responding to Incidents and Near Misses
Effective incident investigation is crucial for preventing future accidents. Managers' roles in this process include:
- Prompt Investigation: Investigations should be conducted promptly and thoroughly after any incident or near miss. This involves gathering evidence, interviewing witnesses, and identifying root causes.
- Corrective Actions: Based on the investigation, managers must implement appropriate corrective actions to prevent similar incidents from occurring. This could involve modifying equipment, improving procedures, or providing additional training.
- Reporting: Accidents and near misses must be reported to OSHA as required by law. Managers are responsible for ensuring that these reports are accurate, complete, and submitted within the designated timeframe.
Consequences of Non-Compliance
The consequences of non-compliance with OSHA standards can be severe, impacting both the organization and its managers:
- Fines and Penalties: OSHA can levy significant fines for violations, ranging from thousands to hundreds of thousands of dollars, depending on the severity of the violation. Repeat offenders face even steeper penalties.
- Legal Liability: Managers can face legal liability, including criminal charges, in cases of serious safety violations resulting in employee injury or death.
- Reputational Damage: OSHA violations can severely damage an organization's reputation, leading to loss of customers, investors, and employees.
- Increased Insurance Premiums: A poor safety record can lead to significantly higher insurance premiums, increasing the organization's operating costs.
- Loss of Productivity: Workplace accidents lead to lost productivity due to employee absences, investigations, and remediation efforts.
Best Practices for OSHA Compliance
Implementing robust safety programs requires a multifaceted approach. Managers can significantly contribute to this by adopting several best practices:
1. Regular Safety Training
Regular, comprehensive safety training is not a one-time event; it's an ongoing process. Managers should ensure that all employees receive adequate training on:
- Hazard Recognition: Training should equip employees to identify potential hazards in their work areas.
- Safe Work Practices: Employees must be trained on the correct procedures for performing their tasks safely.
- Emergency Procedures: Employees should know what to do in case of an emergency, including evacuation procedures and first aid.
- Use of PPE: Proper training on the use and maintenance of PPE is crucial for protecting employees from hazards.
2. Conducting Regular Safety Inspections
Regular safety inspections are vital for identifying potential hazards before they cause accidents. Managers should:
- Schedule Regular Inspections: Inspections should be conducted at regular intervals, with the frequency determined by the level of risk in the workplace.
- Involve Employees: Involving employees in the inspection process can help identify hazards that management might miss.
- Document Findings: All findings from inspections should be documented, along with any corrective actions taken.
3. Implementing a Robust Incident Reporting System
A robust incident reporting system is essential for identifying trends and preventing future accidents. Managers should:
- Encourage Reporting: Create a culture where employees feel comfortable reporting incidents and near misses without fear of reprisal.
- Thorough Investigation: All incidents should be thoroughly investigated to determine the root cause.
- Corrective Actions: Appropriate corrective actions should be implemented to prevent similar incidents from occurring.
4. Utilizing Technology for Safety Management
Technology can play a significant role in improving OSHA compliance. Managers can utilize tools such as:
- Safety Management Software: This software can help manage safety training, inspections, incident reports, and other safety-related tasks.
- Mobile Apps: Mobile apps can provide employees with access to safety information and allow them to report hazards easily.
- Wearable Sensors: Wearable sensors can monitor employee movements and provide real-time alerts about potential hazards.
5. Continuous Improvement
OSHA compliance isn't a destination; it's a journey. Managers should adopt a continuous improvement mindset by:
- Regularly Reviewing Safety Programs: Safety programs should be reviewed and updated regularly to ensure they remain effective.
- Seeking Feedback: Regularly seek feedback from employees on safety-related issues.
- Staying Updated on OSHA Regulations: Keep abreast of changes in OSHA regulations and ensure that the organization's safety program remains compliant.
Conclusion: Managers – The Guardians of Workplace Safety
Managers are not merely supervisors; they are the critical frontline leaders in ensuring a safe and healthy work environment. Their understanding of OSHA regulations, their commitment to fostering a safety-conscious culture, and their proactive approach to hazard mitigation are paramount to effective OSHA compliance. By embracing the responsibilities outlined in this article and implementing best practices, managers can significantly contribute to a safer and more productive workplace for everyone. Ignoring these responsibilities, however, carries significant risks, impacting not only the organization's bottom line but also the well-being of its employees. The role of the manager in OSHA compliance is not just a job requirement; it’s a moral imperative.
Latest Posts
Latest Posts
-
A 38 Year Old Male With A History Of Schizophrenia
May 11, 2025
-
7 Keys To Divine Healing By Kenneth Hagin Pdf
May 11, 2025
-
Encouraging Responsibility And Promoting Self Help Are
May 11, 2025
-
Public Partnerships Llc 100 Kimball Place Suite 150 Alpharetta Ga
May 11, 2025
-
For Kant What Makes Someone Human
May 11, 2025
Related Post
Thank you for visiting our website which covers about Managers Are Considered Within An Organization Osha . We hope the information provided has been useful to you. Feel free to contact us if you have any questions or need further assistance. See you next time and don't miss to bookmark.