Match The Process Capability Improvement Methods With The Appropriate Examples.
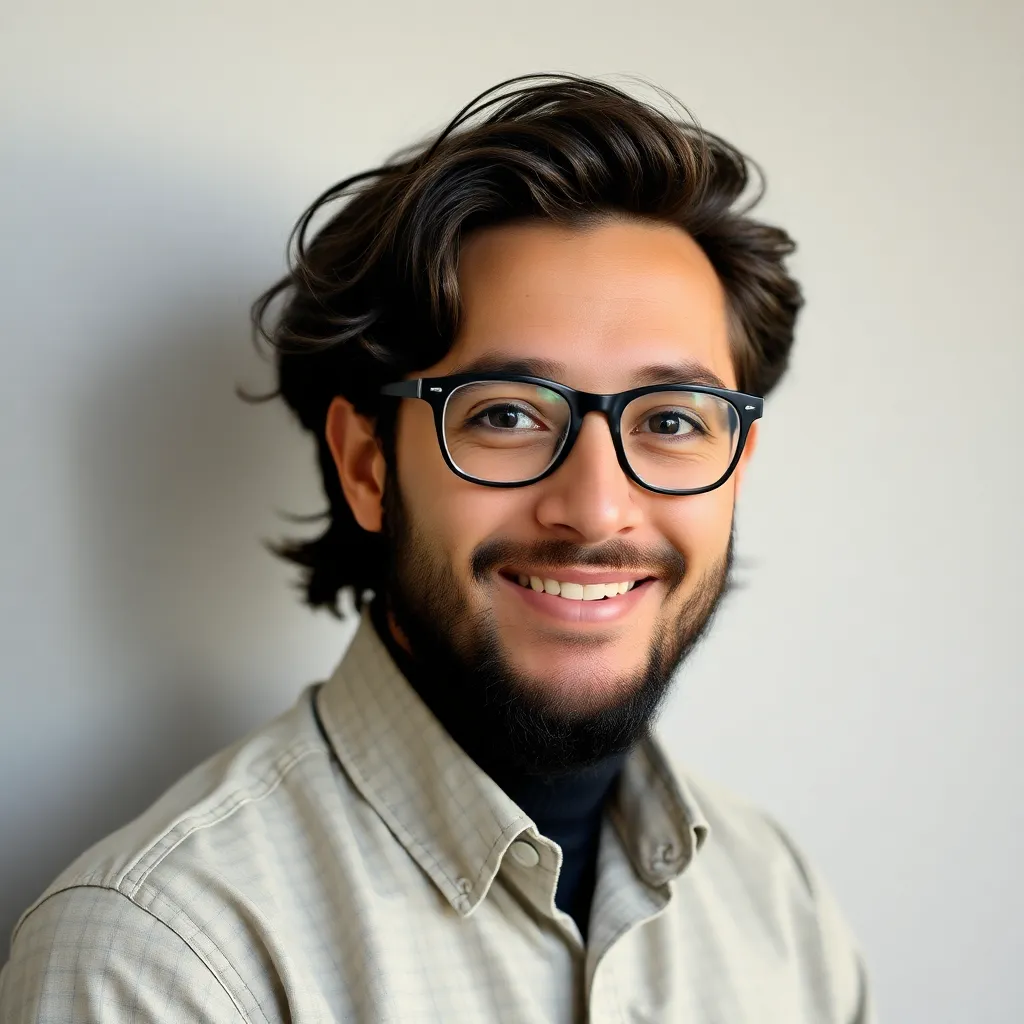
Onlines
Apr 10, 2025 · 6 min read

Table of Contents
Matching Process Capability Improvement Methods with Appropriate Examples
Process capability is a crucial metric that assesses a process's ability to consistently produce outputs meeting pre-defined specifications. When a process falls short, improvement methods must be employed to enhance its performance. This article delves into various process capability improvement methods, illustrating their application with practical examples. Understanding these methods is essential for organizations striving for operational excellence and continuous improvement.
Understanding Process Capability Indices (Cp, Cpk, Pp, Ppk)
Before diving into improvement methods, it's vital to understand the key process capability indices:
-
Cp (Process Capability Index): Measures the inherent capability of a process, assuming the process is centered on the target. It assesses the spread of the process output relative to the specification width. A higher Cp indicates better capability.
-
Cpk (Process Capability Index): Accounts for both the process spread and its centering relative to the target. It's a more realistic indicator of process capability as it considers potential deviations from the target. A higher Cpk indicates better capability and less deviation.
-
Pp (Process Performance Index): Similar to Cp, but uses the actual data range observed over a longer period, potentially including variations not reflected in Cp.
-
Ppk (Process Performance Index): Similar to Cpk, considering both spread and centering from actual data over a longer timeframe, providing a more comprehensive picture of long-term process performance.
Process Capability Improvement Methods and Examples
Several methods can improve process capability. The most effective approach depends on the specific cause of the capability deficiency, whether it's excessive variation, poor centering, or a combination of both.
1. Statistical Process Control (SPC)
SPC involves using statistical techniques to monitor and control processes. It helps identify sources of variation and implement corrective actions.
Examples:
-
Control Charts: A manufacturing plant produces ball bearings with a specified diameter. Control charts (X-bar and R charts) track the average diameter and range of sample measurements over time. Out-of-control points signal potential problems like machine wear or inconsistent material supply, enabling timely intervention to prevent defects.
-
Process Behavior Charts: A call center measures average call handling time. Using a process behavior chart, they identify special cause variation leading to excessively long call times, pinpointing issues like inadequate training or system glitches. Addressing these issues improves average call handling time and overall efficiency.
2. Design of Experiments (DOE)
DOE is a powerful technique for identifying the factors significantly impacting process output. It helps pinpoint the key variables to control for optimal process performance.
Examples:
-
Factorial Design: A food company experiments with different baking times, temperatures, and ingredient combinations to optimize cookie texture. DOE helps determine the optimal settings for consistent texture, minimizing variation and maximizing customer satisfaction.
-
Response Surface Methodology (RSM): A chemical manufacturer seeks to maximize product yield. RSM guides experiments to optimize process parameters like temperature, pressure, and reactant concentration, leading to improved yield and reduced waste.
3. Lean Manufacturing Principles
Lean principles focus on eliminating waste and improving efficiency. Applying these principles often significantly enhances process capability.
Examples:
-
5S Methodology: A warehouse implements 5S (Sort, Set in Order, Shine, Standardize, Sustain) to optimize storage and retrieval processes. By eliminating unnecessary clutter and improving organization, they reduce errors and improve efficiency, resulting in improved capability.
-
Value Stream Mapping: A company maps out its entire production process to identify non-value-added steps. Eliminating these steps directly leads to increased efficiency and reduced variability, thereby improving process capability.
4. Six Sigma Methodology
Six Sigma employs a structured approach to process improvement, aiming to reduce defects to near zero. It utilizes various tools and techniques, including DMAIC (Define, Measure, Analyze, Improve, Control).
Examples:
-
DMAIC Cycle: A bank experiencing high error rates in loan processing applies the DMAIC cycle. They define the problem, measure the current error rate, analyze the root causes, improve processes through automation and improved training, and then control the improved process to maintain low error rates.
-
Failure Mode and Effects Analysis (FMEA): A medical device manufacturer uses FMEA to identify potential failure modes in their manufacturing process and assess their impact. This allows them to prioritize improvements to mitigate risks and improve product reliability.
5. Poka-Yoke (Mistake-Proofing)
Poka-yoke focuses on designing processes to prevent errors from occurring in the first place. This proactive approach eliminates many sources of variability.
Examples:
-
Interlocks: A machine requires a specific sequence of steps to operate correctly; an interlock prevents the machine from starting unless the steps are completed in order, preventing incorrect operation.
-
Color-Coding: A hospital color-codes medication containers to prevent medication errors, minimizing the risk of incorrect dosages or administration.
6. Automation and Technology
Automating processes reduces human error and variability, leading to consistent output and improved capability.
Examples:
-
Robotic Process Automation (RPA): A company automates repetitive data entry tasks using RPA, reducing manual errors and improving consistency.
-
Computer Numerical Control (CNC) Machining: A manufacturing company uses CNC machines for precise part production, reducing variability and improving dimensional accuracy.
7. Training and Development
Investing in employee training can significantly enhance process capability by improving skills and knowledge.
Examples:
-
Operator Training: Manufacturing operators receive comprehensive training on machine operation and quality control, reducing errors and improving consistency.
-
Statistical Process Control Training: Employees are trained to interpret control charts and identify potential process issues, enabling quicker corrective actions.
8. Improved Materials and Equipment
Using higher quality materials and well-maintained equipment can directly improve process capability.
Examples:
-
High-Quality Raw Materials: A food manufacturer uses high-quality ingredients with consistent properties to reduce variability in the final product.
-
Regular Equipment Maintenance: A printing company regularly maintains its printing presses to ensure consistent ink application and print quality.
9. Process Standardization
Standardizing processes ensures consistent execution, reducing variability and improving capability.
Examples:
-
Standard Operating Procedures (SOPs): A company develops detailed SOPs for all critical processes, ensuring consistent execution by all employees.
-
Work Instructions: Clear work instructions provide guidance for performing tasks correctly, minimizing deviations and errors.
10. Root Cause Analysis (RCA)
RCA techniques help identify the underlying causes of process problems, enabling focused improvements.
Examples:
-
5 Whys: A company repeatedly experiences equipment failures. By asking "Why?" five times, they uncover the root cause – inadequate lubrication, leading to preventive maintenance improvements.
-
Fishbone Diagram: A service center experiences long wait times. A fishbone diagram helps brainstorm potential causes (staffing, system issues, training), leading to targeted solutions.
Conclusion
Improving process capability requires a multifaceted approach. Selecting the appropriate methods depends on the specific process and its challenges. By strategically applying these methods, organizations can enhance their process efficiency, reduce defects, and achieve higher levels of quality and productivity. Remember that continuous monitoring and improvement are crucial for maintaining long-term process capability. The key is to implement a system for ongoing evaluation and refinement, ensuring your processes remain robust and capable. Choosing the correct methods often involves a combination of techniques, a strategic approach, and ongoing evaluation to ensure sustained improvement.
Latest Posts
Latest Posts
-
Which Aspect Of Corporate Branding Is Represented In This Image
Apr 18, 2025
-
Which Professional Organization Evaluates A New Dental Material
Apr 18, 2025
-
A Nurse Is Taking An Adult Clients Temperature Rectally
Apr 18, 2025
-
3 01 Quiz Participial And Absolute Phrases
Apr 18, 2025
-
What Can I Expect From My Astronomy Class At Epcc
Apr 18, 2025
Related Post
Thank you for visiting our website which covers about Match The Process Capability Improvement Methods With The Appropriate Examples. . We hope the information provided has been useful to you. Feel free to contact us if you have any questions or need further assistance. See you next time and don't miss to bookmark.