Melting Of The Anode Commonly Occurs
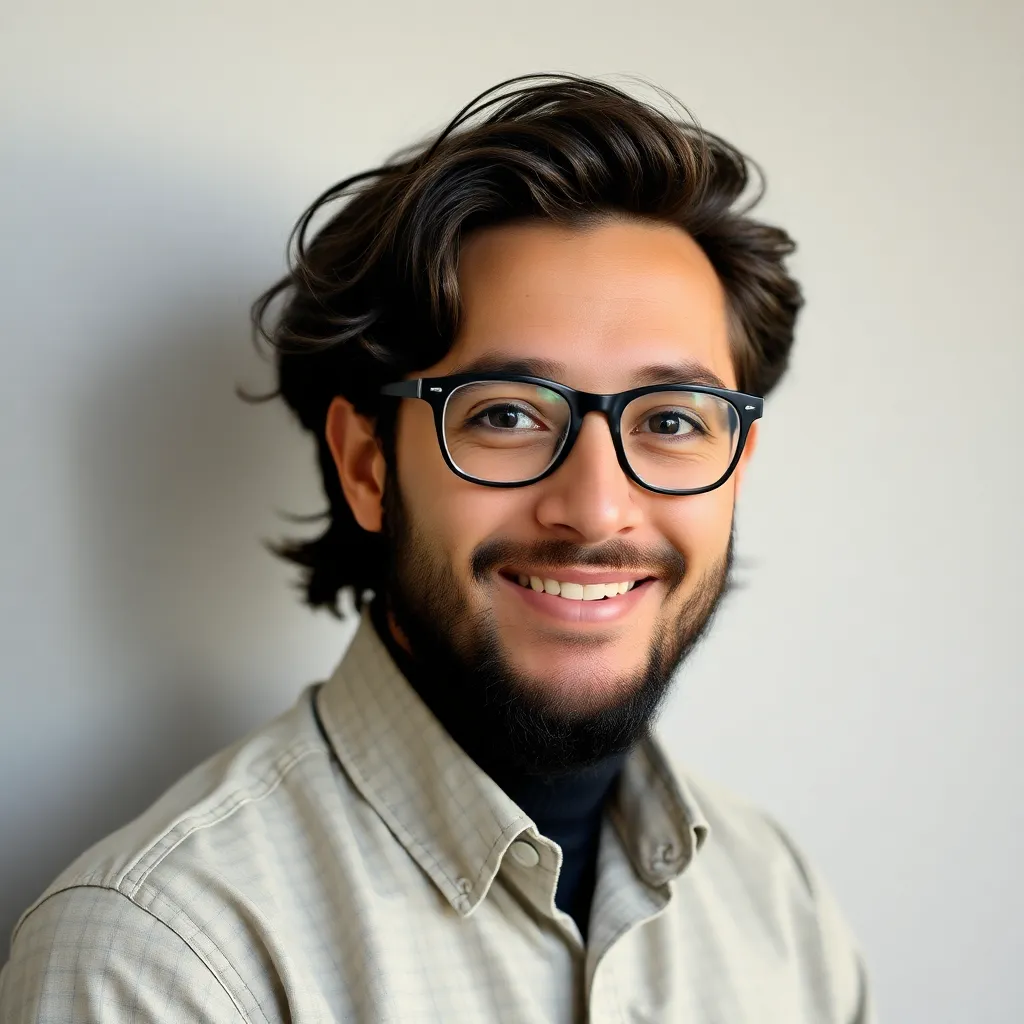
Onlines
May 05, 2025 · 7 min read

Table of Contents
Melting of the Anode: Common Causes, Prevention, and Mitigation Strategies
Anode melting is a significant concern in various electrochemical processes, including electroplating, electrowinning, and electrochemical machining. This phenomenon, characterized by the localized or widespread melting of the anode material, can lead to process disruptions, equipment damage, reduced efficiency, and compromised product quality. Understanding the causes of anode melting is crucial for implementing effective preventive and mitigation strategies. This comprehensive article delves into the intricacies of anode melting, exploring its underlying causes, exploring effective prevention techniques, and outlining mitigation strategies to minimize its occurrence.
Understanding Anode Melting: A Comprehensive Overview
Anode melting is a complex process influenced by a multitude of factors, all intertwined to varying degrees. The primary cause often stems from excessive current density at the anode surface. This can lead to Joule heating, where electrical energy is converted into heat, exceeding the anode material's melting point. This effect is amplified by poor anode design, insufficient cooling, and the presence of impurities. The consequences can range from minor surface melting to catastrophic failure, completely destroying the anode and halting the electrochemical process.
The Role of Current Density: A Key Factor
Current density, measured in amperes per square centimeter (A/cm²), represents the amount of current passing through a unit area of the anode surface. Higher current densities generate greater heat, making them a primary driver of anode melting. This is governed by Ohm's law and the relationship between resistance, current, and voltage. Anode materials with higher electrical resistivity generate more heat for the same current density, increasing the risk of melting.
The Influence of Anode Material Properties
The physical and chemical properties of the anode material play a vital role in its susceptibility to melting. Melting point, thermal conductivity, and electrical resistivity are crucial parameters. Materials with low melting points are inherently more prone to melting at high current densities. Those with low thermal conductivity are less efficient at dissipating heat, increasing the risk of localized overheating. High electrical resistivity materials generate more heat at a given current, exacerbating the problem.
The Impact of Electrolyte Composition and Temperature
The electrolyte's composition and temperature significantly influence anode melting. The presence of impurities or contaminants in the electrolyte can increase its resistance, leading to increased Joule heating and a higher risk of anode melting. Similarly, higher electrolyte temperatures can reduce the electrolyte's viscosity and increase its conductivity, potentially leading to increased current densities and anode overheating. Changes in electrolyte pH can also affect the electrochemical reactions at the anode surface, influencing the rate of heat generation.
The Effect of Anode Geometry and Design
The shape and size of the anode can significantly influence the distribution of current density. Sharp edges and corners concentrate the current, leading to localized hotspots and a higher risk of melting. A poorly designed anode with insufficient surface area for a given current can also lead to excessive current densities and subsequent melting. The overall anode geometry and its interaction with the cathode and electrolyte flow are critical design considerations to prevent melting.
Prevention Strategies: Proactive Measures to Avoid Anode Melting
Preventing anode melting is always preferable to dealing with the consequences. Implementing proactive measures significantly reduces the risk of this detrimental phenomenon. These strategies are primarily focused on controlling current density, optimizing anode design, and maintaining optimal electrolyte conditions.
Optimizing Current Density: The Foundation of Prevention
Maintaining a low and uniform current density across the anode surface is the cornerstone of prevention. This requires careful consideration of the anode's surface area, the total current applied, and the uniformity of the current distribution. Techniques include using anodes with large surface areas, employing multiple anodes to distribute the current, and ensuring uniform electrolyte flow to minimize variations in current density.
Strategic Anode Design: Enhancing Heat Dissipation
A well-designed anode plays a vital role in preventing melting. Optimizing anode geometry to minimize current concentration is crucial. This involves avoiding sharp corners and edges and ensuring a smooth, even surface. The use of internal cooling channels within the anode can significantly enhance heat dissipation, preventing localized overheating. The material selection itself is critical; choosing anodes with high melting points and high thermal conductivity is essential.
Maintaining Optimal Electrolyte Conditions: Purity and Temperature Control
Maintaining a clean and pure electrolyte is paramount. Impurities increase resistance, leading to increased Joule heating. Regular electrolyte filtration and purification are essential. Controlling the electrolyte temperature is equally important. Keeping the electrolyte at an optimal temperature minimizes variations in conductivity and helps prevent excessive current densities. Regular monitoring of electrolyte parameters is crucial for early detection of potential problems.
Implementing Proper Cooling Systems: Effective Heat Removal
Effective cooling systems are essential to remove the heat generated during the electrochemical process. This can involve employing external cooling jackets around the electrolytic cell, circulating chilled electrolyte, or using immersion cooling techniques. The effectiveness of the cooling system is directly related to the ability to prevent excessive temperature rises at the anode surface.
Regular Inspection and Maintenance: Early Detection of Issues
Regular inspection and maintenance of the anode and the entire electrochemical system are vital for early detection of potential problems. Visual inspection can reveal signs of localized overheating or pitting, indicating potential issues. Monitoring the cell voltage and current can also identify abnormal conditions. Proactive maintenance prevents small problems from escalating into catastrophic anode melting.
Mitigation Strategies: Addressing Anode Melting When It Occurs
Despite preventative measures, anode melting can sometimes occur. In such cases, effective mitigation strategies are crucial to minimize damage and ensure the continued operation of the electrochemical process. These strategies focus on controlling the process parameters and managing the consequences of anode damage.
Immediate Process Shutdown: Preventing Further Damage
If anode melting is detected, the first step is to immediately shut down the electrochemical process. This prevents further damage to the anode and the electrolytic cell. Rapid shutdown minimizes the extent of damage and reduces the risk of further complications.
Assessment and Damage Control: Evaluating the Extent of Damage
Once the process is shut down, a thorough assessment of the damage is crucial. This involves inspecting the anode to determine the extent of melting, assessing any damage to the electrolytic cell, and analyzing the electrolyte for any changes in composition. This evaluation informs the subsequent repair or replacement strategies.
Repair or Replacement: Restoring Functionality
Depending on the extent of damage, the anode may be repairable or require replacement. Minor surface melting might be addressed through surface grinding or polishing. However, extensive damage necessitates complete replacement. The replacement anode should be carefully selected to match the process requirements and the lessons learned from the initial melting incident.
Process Optimization: Refining Operating Parameters
Following an anode melting incident, a comprehensive review of the process parameters is crucial. This involves analyzing the current density, electrolyte composition, temperature, and cooling system effectiveness. Based on the findings, adjustments can be made to optimize the process, reducing the likelihood of future occurrences. This iterative process ensures continuous improvement and enhanced process robustness.
Data Analysis and Predictive Maintenance: Proactive Approaches
Regular data analysis of process parameters, combined with predictive maintenance techniques, can significantly improve the reliability of the electrochemical process. Analyzing trends in current density, temperature, and electrolyte properties can reveal potential issues before they lead to anode melting. Predictive maintenance allows for proactive interventions, preventing catastrophic failures.
Conclusion: A Holistic Approach to Anode Melting Management
Anode melting is a multifaceted problem requiring a holistic approach to its management. By understanding the underlying causes, implementing effective prevention strategies, and developing robust mitigation techniques, the risk of anode melting can be significantly reduced. Regular monitoring, data analysis, and proactive maintenance are crucial for ensuring the long-term reliability and efficiency of electrochemical processes. A combined approach, encompassing proactive prevention and reactive mitigation, forms the cornerstone of a robust strategy to address the complexities of anode melting and maintain operational integrity within electrochemical systems.
Latest Posts
Latest Posts
-
A Way Of Talking Grace Quick Check
May 05, 2025
-
Choose The Answer That Best Describes Hco3
May 05, 2025
-
A Circle Could Be Circumscribed About The Quadrilateral Below
May 05, 2025
-
In Addition To Being An Accomplished Psychologist
May 05, 2025
-
What Document Outlines The Health And Safety Related Procedures
May 05, 2025
Related Post
Thank you for visiting our website which covers about Melting Of The Anode Commonly Occurs . We hope the information provided has been useful to you. Feel free to contact us if you have any questions or need further assistance. See you next time and don't miss to bookmark.