Production Runs Can Be Scheduled In
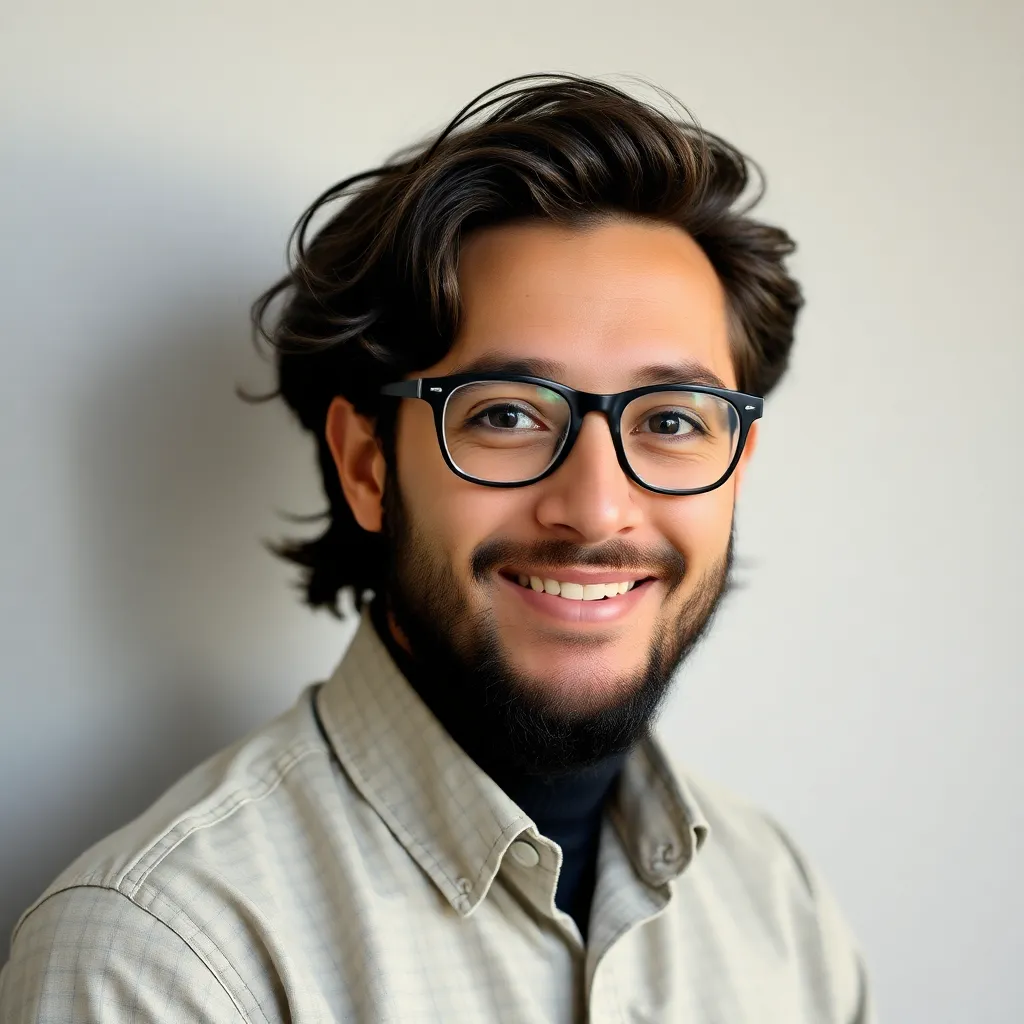
Onlines
Apr 25, 2025 · 6 min read

Table of Contents
Production Runs Can Be Scheduled In: A Comprehensive Guide to Optimizing Your Manufacturing Process
Production scheduling is the backbone of any successful manufacturing operation. Getting it right can mean the difference between profitability and significant losses. This comprehensive guide explores the various methods and considerations involved in scheduling production runs, helping you optimize your processes for maximum efficiency and output.
Understanding the Fundamentals of Production Scheduling
Before diving into specific scheduling methods, it's crucial to understand the underlying principles. Effective production scheduling involves:
-
Forecasting Demand: Accurately predicting future demand is paramount. This involves analyzing historical sales data, market trends, and seasonal fluctuations. Inaccurate forecasting can lead to overproduction or shortages, both equally detrimental.
-
Capacity Planning: Assessing your available resources – machinery, labor, raw materials – is vital. Understanding your production capacity allows you to create realistic schedules and avoid over-committing your resources.
-
Material Requirements Planning (MRP): MRP systems ensure you have the necessary raw materials and components available when needed. This prevents production delays caused by material shortages.
-
Shop Floor Control: Real-time monitoring of the production process allows for quick identification and resolution of any bottlenecks or delays. This requires robust tracking systems and communication channels.
-
Order Prioritization: Not all orders are created equal. Prioritizing orders based on factors like urgency, profitability, and customer importance ensures that the most critical tasks are completed first.
Key Methods for Scheduling Production Runs
Several established methods can be used to schedule production runs. The optimal choice depends on factors such as the complexity of your production process, the type of products you manufacture, and your specific business needs.
1. First-Come, First-Served (FCFS):
This is the simplest scheduling method. Orders are processed in the order they are received. While straightforward, FCFS can be inefficient, as it doesn't consider factors like order urgency or processing time. It’s best suited for small-scale operations with relatively simple processes and minimal order variations.
Advantages: Simple to implement and understand.
Disadvantages: Inefficient, doesn't optimize resource utilization, can lead to long lead times.
2. Shortest Processing Time (SPT):
This method prioritizes jobs with the shortest processing times. This minimizes the average completion time and maximizes throughput. However, it might lead to longer lead times for larger jobs. SPT is suitable for environments with a mix of small and large jobs where minimizing overall completion time is a priority.
Advantages: Reduces average completion time, improves throughput.
Disadvantages: Can lead to longer lead times for larger jobs, may not be suitable for all types of production environments.
3. Earliest Due Date (EDD):
This method prioritizes jobs with the earliest due dates. This minimizes the number of late jobs and improves customer satisfaction. However, it can lead to starvation for longer jobs. EDD is suitable when meeting deadlines is critical, like in just-in-time (JIT) manufacturing.
Advantages: Minimizes late jobs, improves customer satisfaction.
Disadvantages: Can lead to starvation for longer jobs, might not optimize resource utilization.
4. Critical Ratio (CR):
The critical ratio method considers both the remaining processing time and the remaining time until the due date. The formula is: CR = (Due Date - Today's Date) / Remaining Processing Time
. Jobs with a lower critical ratio are prioritized. This method balances the need to meet deadlines with the need to utilize resources efficiently.
Advantages: Balances meeting deadlines with efficient resource utilization.
Disadvantages: More complex to calculate than other methods.
5. Priority Rules-Based Scheduling:
This involves creating a set of rules to prioritize jobs. These rules can be based on various factors like due date, processing time, priority level, or a combination thereof. This offers flexibility but requires careful consideration of the rules to avoid conflicts or inefficiencies.
Advantages: Highly flexible, allows for customization based on specific business needs.
Disadvantages: Requires careful planning and management of the rules to avoid conflicts and inefficiencies.
6. Advanced Planning and Scheduling (APS) Software:
For complex manufacturing environments with many variables, APS software is indispensable. These sophisticated systems use advanced algorithms to optimize scheduling, taking into account numerous constraints like machine capacity, material availability, and labor resources. APS software can significantly improve efficiency, reduce lead times, and minimize costs.
Advantages: Optimizes scheduling across multiple constraints, improves efficiency and reduces lead times, provides real-time visibility into the production process.
Disadvantages: Can be expensive to implement and maintain, requires specialized expertise.
Factors Influencing Production Run Scheduling Decisions
Several factors beyond the scheduling method itself heavily influence the effectiveness of your production plan.
1. Production Process Complexity:
The complexity of your manufacturing process significantly impacts scheduling. Simple, repetitive processes are easier to schedule than complex ones with multiple stages and intricate dependencies. Consider the number of steps, the sequence of operations, and the potential for bottlenecks.
2. Product Variety:
A high degree of product variety adds complexity to scheduling. Managing multiple SKUs, different materials, and varied processing requirements demands more sophisticated planning and scheduling techniques.
3. Demand Volatility:
Unpredictable demand fluctuations make accurate forecasting challenging, impacting the effectiveness of any scheduling method. Robust forecasting techniques and flexible scheduling approaches are crucial in volatile markets.
4. Resource Availability:
Limited resources, whether machinery, labor, or materials, constrain your scheduling options. Accurate capacity planning and efficient resource allocation are vital in such scenarios.
5. Lead Time Requirements:
Meeting customer lead time expectations is critical. The chosen scheduling method should be able to accommodate the required lead times while optimizing resource utilization.
6. Quality Control:
Integrating quality control checks into the schedule is essential. Allocating time for inspections and rework prevents defective products from reaching the customer.
7. Maintenance Scheduling:
Planned machine maintenance needs to be incorporated into the schedule to minimize downtime and production disruptions. This requires coordinating maintenance schedules with production schedules to optimize overall efficiency.
Optimizing Your Production Scheduling: Best Practices
-
Data-Driven Decisions: Rely on accurate data from sales forecasts, historical production data, and real-time shop floor monitoring to inform your scheduling decisions.
-
Continuous Improvement: Regularly review and refine your scheduling processes. Identify bottlenecks, areas for improvement, and adapt your methods based on performance data.
-
Collaboration and Communication: Effective communication between different departments, including production, planning, and purchasing, is essential for seamless production scheduling.
-
Flexibility and Adaptability: Be prepared to adjust your schedules in response to unforeseen events, like material shortages, machine breakdowns, or changes in customer demand.
-
Technology Adoption: Consider implementing advanced planning and scheduling software to enhance your scheduling capabilities, especially for complex manufacturing environments.
-
Employee Training: Ensure your employees are adequately trained in using the chosen scheduling method and the relevant software systems.
-
Regular Performance Monitoring: Continuously monitor key performance indicators (KPIs) such as on-time delivery, throughput, lead times, and inventory levels to assess the effectiveness of your scheduling strategies.
Conclusion: The Key to Efficient Manufacturing
Effective production run scheduling is crucial for optimizing your manufacturing process. By understanding the various scheduling methods, considering the influencing factors, and implementing best practices, you can significantly enhance your efficiency, reduce costs, and improve customer satisfaction. The selection of the most suitable scheduling method will always depend on your specific operational context and the overall goals of your manufacturing operation. Remember that continuous monitoring, adaptation, and improvement are key to maintaining a lean and efficient production process.
Latest Posts
Latest Posts
-
1984 Summary Part 2 Chapter 1
Apr 26, 2025
-
Romeo And Juliet Act Iii Reading And Study Guide
Apr 26, 2025
-
How Dna Determines Traits Answer Key
Apr 26, 2025
-
A Trend That Ascends From Left To Right Means
Apr 26, 2025
-
A Companys Documented Philosophy Is Called Its
Apr 26, 2025
Related Post
Thank you for visiting our website which covers about Production Runs Can Be Scheduled In . We hope the information provided has been useful to you. Feel free to contact us if you have any questions or need further assistance. See you next time and don't miss to bookmark.