Safety Controls Must Meet The Following Order Of Priority
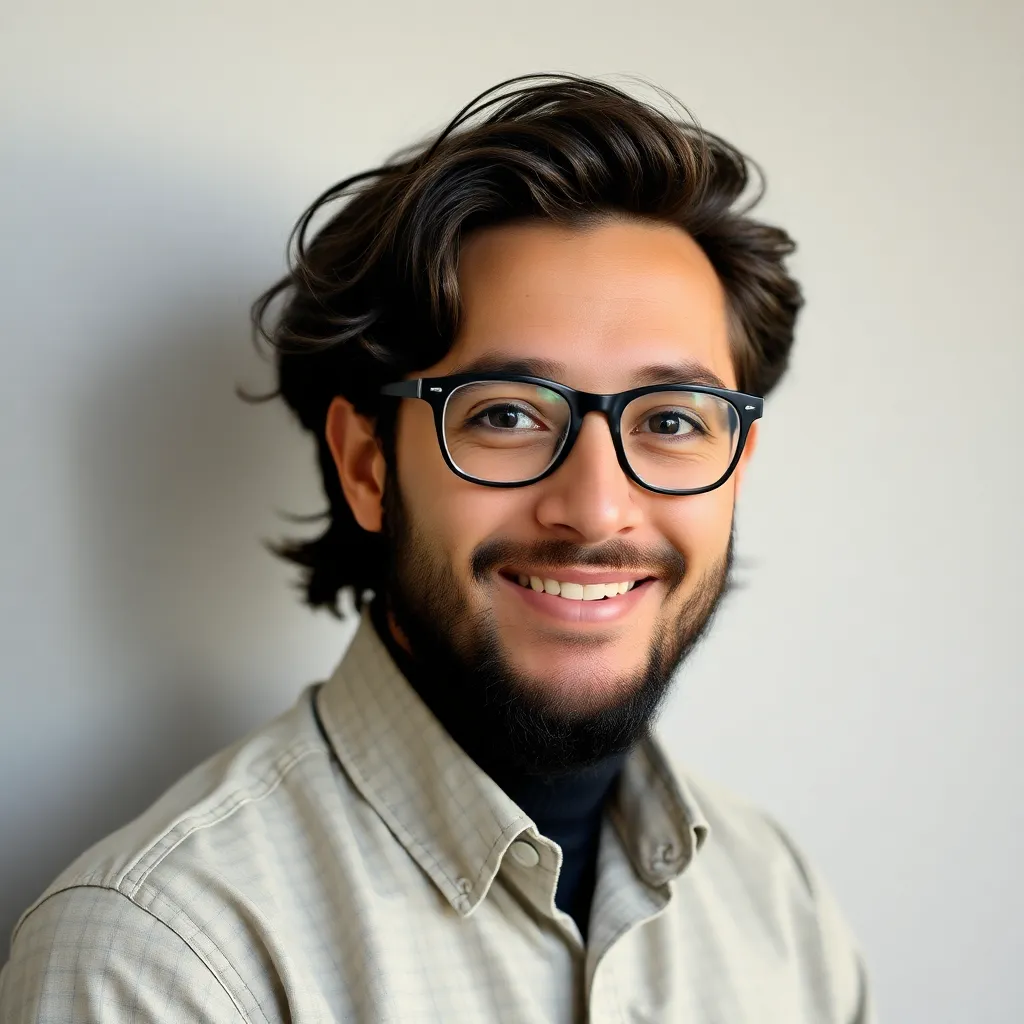
Onlines
May 11, 2025 · 6 min read
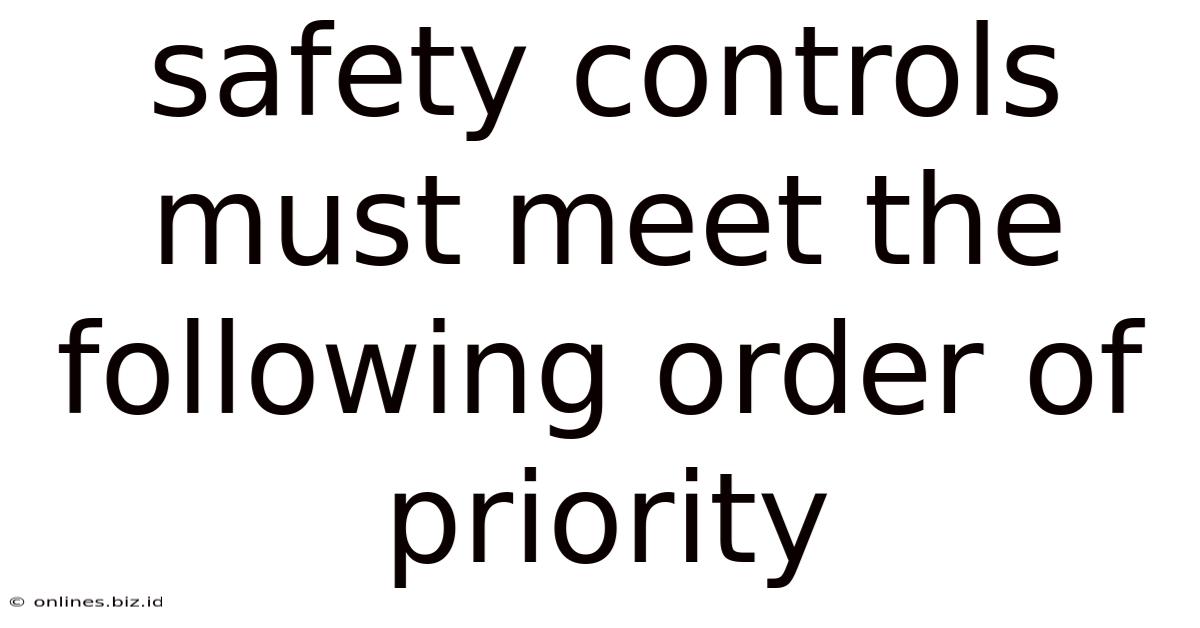
Table of Contents
Safety Controls: A Prioritized Approach to Risk Management
Ensuring workplace safety is paramount. It's not merely a legal requirement; it's a moral imperative reflecting a commitment to the well-being of employees. However, implementing effective safety controls isn't a simple checklist. It requires a structured, prioritized approach to mitigate risks effectively. This article delves into the crucial order of priority for implementing safety controls, exploring each level in detail and offering practical examples to illustrate the importance of a layered safety system.
The Hierarchy of Safety Controls: A Prioritized Approach
The hierarchy of safety controls is a fundamental principle in risk management. It prioritizes control measures based on their effectiveness in eliminating or reducing hazards. This hierarchy isn't merely a suggestion; it's a structured approach proven to minimize workplace incidents and enhance overall safety. The order of priority, from most to least effective, generally follows this sequence:
- Elimination: This is the gold standard. If a hazard can be completely removed from the workplace, that's the optimal solution.
- Substitution: If elimination isn't feasible, replacing the hazardous substance or process with a safer alternative is the next best step.
- Engineering Controls: These controls modify the workplace environment to reduce exposure to hazards. They're often permanent and don't rely on human behavior.
- Administrative Controls: These controls involve changes to work practices, procedures, or policies to minimize risk. They rely on human behavior and require ongoing training and reinforcement.
- Personal Protective Equipment (PPE): This is the last line of defense. PPE protects individuals from hazards, but it's only effective if used correctly and consistently. It's crucial to remember that PPE does not eliminate hazards; it only mitigates the risk of exposure.
Let's explore each level in more detail:
1. Elimination: Removing the Hazard Entirely
Elimination involves removing the hazard completely from the workplace. This is the most effective control measure because it prevents any potential for exposure. Consider these examples:
- Example 1: Manual Material Handling: If employees are constantly straining themselves lifting heavy boxes, the elimination approach would involve investing in automated lifting equipment or redesigning the process to minimize manual lifting altogether.
- Example 2: Hazardous Chemicals: If a particular chemical poses a significant health risk, eliminating its use entirely by switching to a safer alternative is the most effective solution. This might involve researching and adopting a new manufacturing process that doesn't require the hazardous chemical.
- Example 3: Trip Hazards: Removing obstacles from walkways, ensuring proper lighting, and repairing uneven flooring directly eliminates trip hazards.
2. Substitution: Replacing the Hazard with a Safer Alternative
When elimination is impractical, substitution offers a viable alternative. This involves replacing a hazardous substance, process, or piece of equipment with a safer counterpart. This method avoids the hazard entirely while maintaining productivity. Examples include:
- Example 1: Solvents: Substituting a highly volatile and flammable solvent with a water-based or less hazardous solvent minimizes fire risks and reduces health hazards.
- Example 2: Machinery: Replacing outdated machinery with newer, safer models equipped with modern safety features reduces the risk of accidents. This might involve investing in machines with automated safety shut-off mechanisms or improved guarding.
- Example 3: Chemicals: Substituting a highly toxic cleaning agent with a less toxic, biodegradable alternative minimizes environmental impact and reduces the risk of employee exposure to harmful chemicals.
3. Engineering Controls: Modifying the Workplace Environment
Engineering controls focus on modifying the workplace environment to reduce or eliminate hazards at the source. These controls are often permanent solutions, independent of human behavior. Effective examples include:
- Example 1: Machine Guarding: Installing guards on machinery to prevent accidental contact with moving parts is a crucial engineering control. These guards physically prevent access to hazardous areas.
- Example 2: Local Exhaust Ventilation (LEV): LEV systems remove hazardous airborne substances at their point of generation, preventing their spread throughout the workplace. This is particularly important in areas where welding, grinding, or spraying is conducted.
- Example 3: Improved Lighting: Providing adequate lighting in all areas of the workplace reduces the risk of slips, trips, and falls. This seemingly simple measure can significantly improve safety.
- Example 4: Improved Ergonomics: Designing workstations to accommodate the human body's natural movements minimizes the risk of musculoskeletal disorders (MSDs). This may involve adjustable chairs, proper monitor placement, and optimized workspace layouts.
4. Administrative Controls: Modifying Work Practices and Procedures
Administrative controls involve changing work practices, procedures, or policies to mitigate hazards. These controls rely heavily on human behavior and require ongoing training, supervision, and reinforcement. Effective examples include:
- Example 1: Job Rotation: Rotating employees through various tasks helps prevent repetitive strain injuries by reducing the time spent performing a single, potentially hazardous task.
- Example 2: Safe Work Procedures: Implementing detailed, well-defined safe work procedures for all tasks minimizes the risk of errors and accidents. These procedures should be regularly reviewed and updated.
- Example 3: Training and Education: Providing comprehensive safety training and education to all employees ensures that they understand the hazards in their workplace and know how to work safely. Regular refresher training reinforces best practices.
- Example 4: Permit-to-Work Systems: Implementing permit-to-work systems for high-risk activities ensures that all necessary precautions are taken before the work commences. This requires a formal authorization process before potentially dangerous tasks can begin.
- Example 5: Regular Inspections: Conducting regular safety inspections allows for early identification of hazards and ensures that safety controls are functioning correctly.
5. Personal Protective Equipment (PPE): The Last Line of Defense
PPE is the last line of defense against workplace hazards. It's crucial to remember that PPE should only be used when other control measures are insufficient or impractical. PPE doesn't eliminate hazards; it only reduces the risk of exposure. Examples include:
- Example 1: Hard Hats: Protecting workers from falling objects.
- Example 2: Safety Glasses: Protecting eyes from flying debris.
- Example 3: Hearing Protection: Protecting ears from excessive noise.
- Example 4: Respirators: Protecting lungs from hazardous airborne substances.
- Example 5: Gloves: Protecting hands from chemicals, cuts, and abrasions.
Important Considerations for PPE:
- Proper Selection: PPE must be selected based on the specific hazards present in the workplace.
- Training and Fit Testing: Employees must be trained on how to use PPE correctly and receive proper fit testing to ensure optimal protection.
- Maintenance and Replacement: PPE should be regularly inspected and replaced when damaged or worn out.
- Compliance: Adherence to relevant safety standards and regulations is essential.
Conclusion: A Layered Approach to Safety
The hierarchy of safety controls is not a sequential list; rather, it represents a layered approach. Often, multiple control measures are implemented simultaneously to provide comprehensive protection. Prioritizing elimination and substitution whenever possible is key to achieving the highest level of safety. By understanding and applying this hierarchy, organizations can significantly reduce workplace accidents, improve employee well-being, and foster a safer and more productive work environment. Remember, proactive safety management is a continuous process of assessment, implementation, and improvement. Regularly reviewing safety procedures and adapting to evolving workplace conditions are critical for sustained success in risk management. A commitment to the prioritized approach ensures that safety remains paramount, not merely an afterthought.
Latest Posts
Latest Posts
-
According To The Chart When Did A Pdsa Cycle Occur
May 12, 2025
-
Bioflix Activity Gas Exchange The Respiratory System
May 12, 2025
-
Economic Value Creation Is Calculated As
May 12, 2025
-
Which Items Typically Stand Out When You Re Scanning Text
May 12, 2025
-
Assume That Price Is An Integer Variable
May 12, 2025
Related Post
Thank you for visiting our website which covers about Safety Controls Must Meet The Following Order Of Priority . We hope the information provided has been useful to you. Feel free to contact us if you have any questions or need further assistance. See you next time and don't miss to bookmark.