Serviceability Is The Dimension Of Quality That Refers To _____.
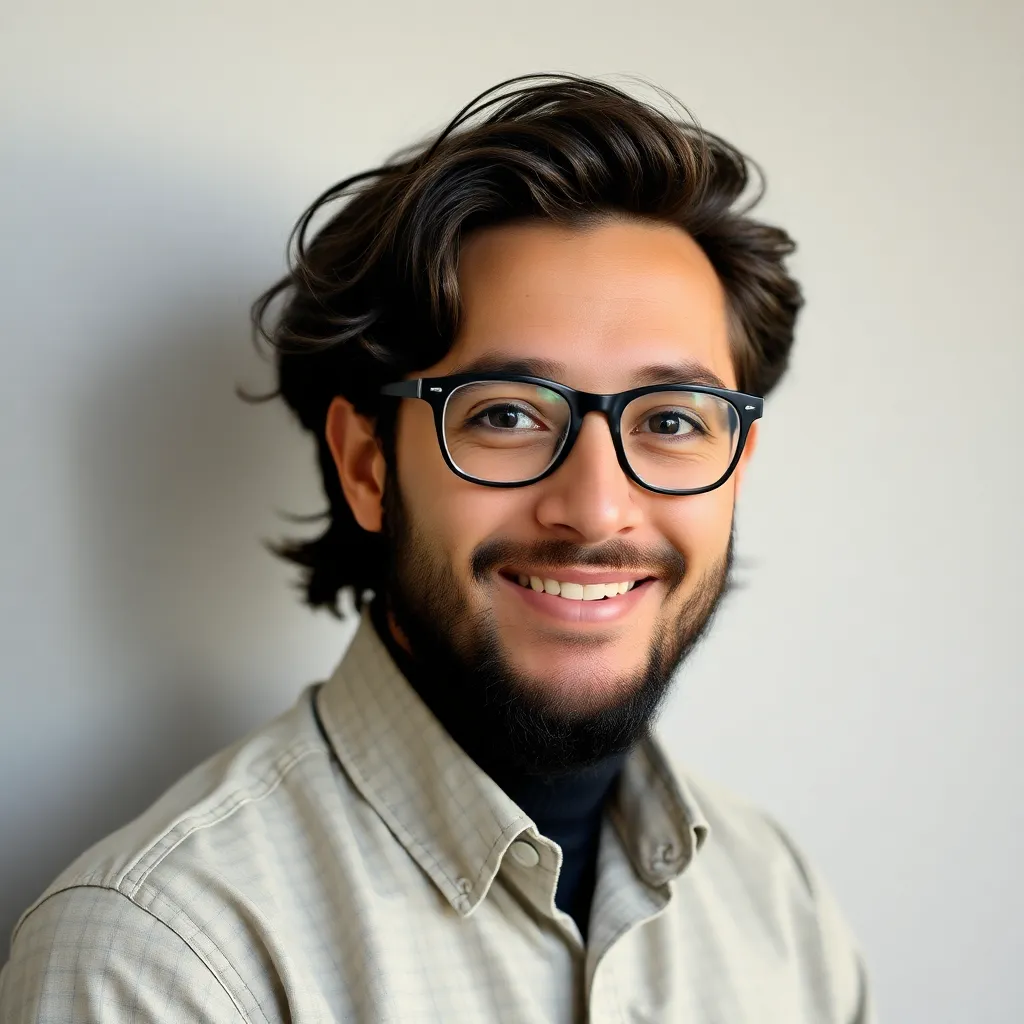
Onlines
Apr 22, 2025 · 5 min read

Table of Contents
Serviceability: The Unsung Hero of Product Quality
Serviceability is the dimension of quality that refers to the ease and cost of maintaining, repairing, and improving a product or service. It encompasses the entire lifecycle of a product, from its initial design and manufacturing to its eventual disposal. While often overlooked in favor of flashier features or aesthetics, serviceability is a critical factor influencing customer satisfaction, operational efficiency, and overall product success. This article will delve deep into the multifaceted nature of serviceability, exploring its key components, benefits, and how to effectively integrate it into your product development strategy.
Understanding the Pillars of Serviceability
Serviceability isn't a monolithic concept; rather, it's a composite of several interconnected factors that collectively determine a product's maintainability and repairability. These pillars are crucial for establishing a robust and effective serviceability strategy:
1. Accessibility: Getting to the Problem
Accessibility refers to the ease with which a technician or even a user can access the components of a product that require maintenance or repair. This involves:
- Modular Design: A modular design allows for easy replacement of individual components without requiring the dismantling of the entire product. This significantly reduces repair time and costs. Consider smartphones; their modular design, while not fully realized in all models, allows for independent battery or screen replacements.
- Clear Documentation: Comprehensive and user-friendly manuals, diagrams, and online resources are essential for guiding technicians and even DIY-inclined users through the repair process. Good documentation significantly reduces troubleshooting time.
- Intuitive Component Labeling: Clearly labeled components make identification and access during maintenance much simpler.
- Tool Accessibility: Consideration should be given to the types of tools required for maintenance and repair. Overly specialized or difficult-to-obtain tools can increase repair costs and time.
2. Diagnosability: Pinpointing the Issue
Diagnosability centers on the ease with which one can identify the root cause of a product malfunction. This is crucial for efficient and effective repairs:
- Built-in Diagnostics: Products can be designed with self-diagnostic capabilities, providing error codes or indicators that pinpoint the problem area. This speeds up troubleshooting significantly.
- Testing Points: Easy access to test points allows technicians to quickly assess the functionality of individual components.
- Remote Diagnostics: In the age of the internet of things (IoT), remote diagnostics allows for real-time monitoring and troubleshooting, minimizing downtime and reducing the need for on-site service visits.
3. Maintainability: The Ease of Repair
Maintainability involves the ease with which a product can be repaired or maintained. Key aspects include:
- Component Replaceability: Components should be easily removable and replaceable, minimizing downtime and repair costs.
- Standard Parts: Using standard, readily available parts avoids delays caused by sourcing specialized components.
- Repair Time: A well-designed product will minimize the time required for repair, thereby reducing labor costs.
- Repair Training: Comprehensive training programs for technicians are essential for efficient and effective repairs.
4. Supportability: Beyond the Repair
Supportability encompasses the resources available to support the product throughout its lifecycle. This includes:
- Customer Support: Excellent customer support can greatly enhance the customer experience, even when repairs are needed.
- Warranty and Service Contracts: Offering warranties and service contracts provides customers with peace of mind and reduces the perceived risk associated with product failure.
- Spare Parts Availability: Ensuring a consistent supply of spare parts is critical for maintaining a product's serviceability over its lifetime.
- Service Network: A well-established service network with qualified technicians readily available provides quick and efficient repairs.
The Benefits of Prioritizing Serviceability
Investing in serviceability may seem like an added expense upfront, but the long-term benefits far outweigh the initial costs. These benefits include:
- Increased Customer Satisfaction: Products that are easy to maintain and repair lead to higher customer satisfaction. Customers appreciate the convenience and reduced downtime.
- Reduced Downtime: Easy repairs minimize downtime, which is especially important for businesses relying on the product for operations.
- Lower Repair Costs: Efficient repairs translate into lower repair costs for both the manufacturer and the customer.
- Extended Product Lifespan: Well-designed products that are easy to maintain are more likely to have an extended lifespan, reducing the need for replacements.
- Improved Brand Reputation: A reputation for producing reliable and maintainable products enhances brand image and customer loyalty.
- Reduced Environmental Impact: Serviceability contributes to a circular economy by reducing waste and promoting repair over replacement. This minimizes the environmental impact associated with manufacturing new products.
- Cost Savings in the Long Run: While initial design and manufacturing costs may increase, the long-term cost savings from reduced downtime, repair costs, and waste management outweigh these initial investments.
Integrating Serviceability into Product Development
Integrating serviceability into the product development process requires a proactive approach. Here's a step-by-step guide:
- Early Stage Consideration: Serviceability should be a primary consideration from the very beginning of the design phase, not an afterthought. This involves incorporating serviceability requirements into design specifications and incorporating feedback from service technicians.
- Design for Disassembly (DFD): DFD is a crucial aspect of designing for serviceability. It involves creating a product that can be easily disassembled and reassembled for maintenance and repair.
- Modular Design: Employing a modular design allows for the easy replacement of individual components without requiring the dismantling of the entire product.
- Standardization of Parts: Using readily available standard parts simplifies repairs and reduces lead times.
- Diagnostics and Test Points: Integrating self-diagnostic capabilities and clear test points simplifies troubleshooting.
- Comprehensive Documentation: Creating user-friendly manuals, diagrams, and online resources makes maintenance and repairs easier.
- Serviceability Testing: Conducting rigorous serviceability testing throughout the development process ensures the product meets the required standards.
- Feedback Loop: Implementing a feedback loop from service technicians and customers ensures that any design flaws or areas for improvement are identified and addressed.
Conclusion: The Future of Serviceability
In a world increasingly focused on sustainability and efficiency, serviceability is no longer a secondary consideration but a vital aspect of product quality. By proactively incorporating serviceability into the product development process, businesses can enhance customer satisfaction, reduce costs, and minimize environmental impact. The future of serviceability lies in embracing innovative technologies like remote diagnostics and augmented reality (AR) to further improve the efficiency and ease of maintenance and repair, ultimately creating a more sustainable and customer-centric approach to product design and lifecycle management. Prioritizing serviceability is not just about fixing things; it’s about building a better, more sustainable future for both products and the planet.
Latest Posts
Latest Posts
-
Every Motor Vehicle Must Be Equipped With
Apr 22, 2025
-
Othello Act 1 Scene 1 Summary
Apr 22, 2025
-
Unit 8 Homework 5 Right Triangles And Trigonometry
Apr 22, 2025
-
A Nurse Manager Is Reviewing A Clients Medical Record
Apr 22, 2025
-
World History Shorts 1 Pdf Answer Key
Apr 22, 2025
Related Post
Thank you for visiting our website which covers about Serviceability Is The Dimension Of Quality That Refers To _____. . We hope the information provided has been useful to you. Feel free to contact us if you have any questions or need further assistance. See you next time and don't miss to bookmark.