Sierra Company Manufactures Soccer Balls In Two Sequential Processes
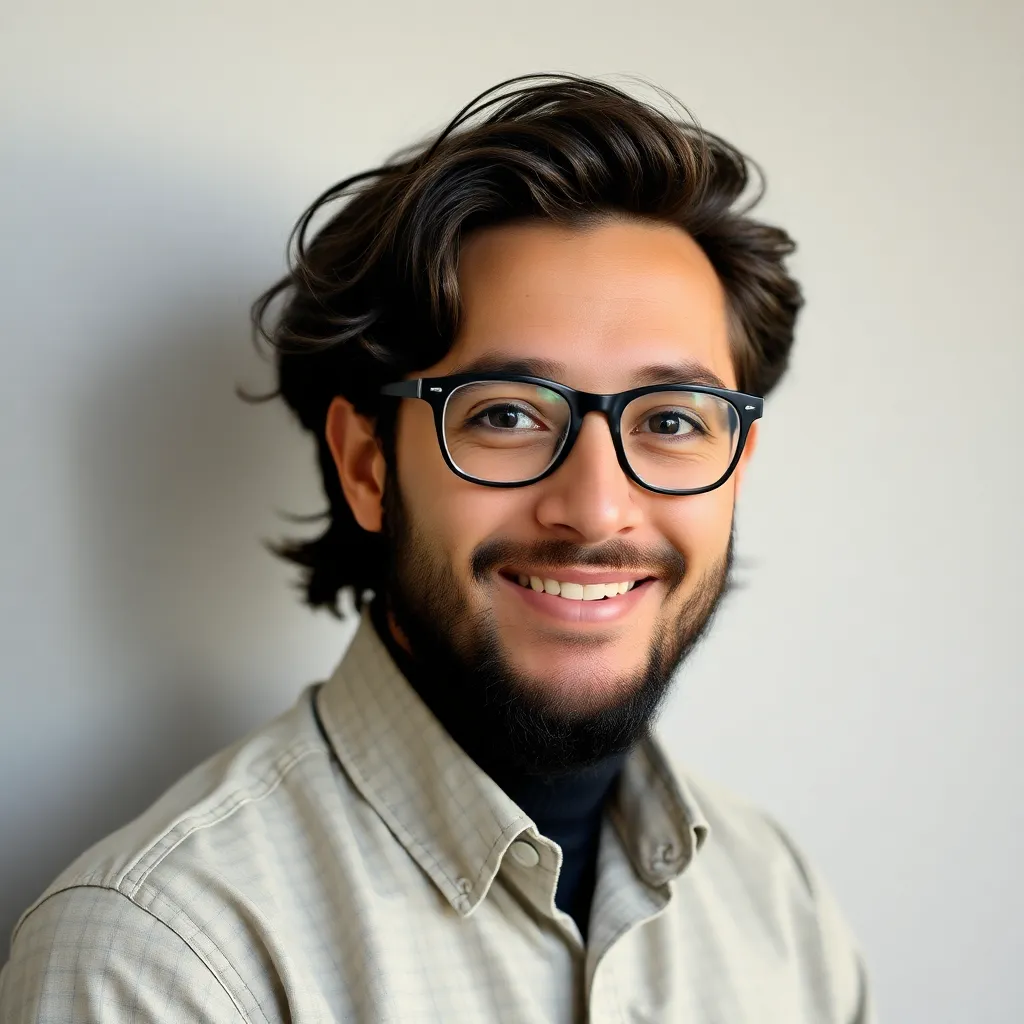
Onlines
Apr 16, 2025 · 6 min read

Table of Contents
Sierra Company: Soccer Ball Manufacturing – A Deep Dive into Sequential Processes
Sierra Company's success in the competitive soccer ball market hinges on its efficient two-process manufacturing system. This article delves deep into the intricacies of Sierra's production, examining each stage, potential bottlenecks, and strategies for optimization. Understanding this process provides valuable insights into efficient manufacturing practices within the sporting goods industry.
Process 1: Cutting and Sewing the Soccer Ball Panels
This initial stage is crucial, setting the foundation for the final product's quality and durability. Let's break it down:
1.1 Material Selection and Preparation
Sierra Company likely sources high-quality PU (polyurethane) leather or synthetic leather for its soccer balls. Careful selection ensures consistent texture, durability, and water resistance. The materials are inspected for defects— imperfections can lead to significant issues later in the process. This initial inspection minimizes waste and maximizes efficiency.
1.2 Panel Cutting
Precise cutting is paramount. Sophisticated automated cutting machines, perhaps utilizing laser or CNC (Computer Numerical Control) technology, are likely employed. This ensures consistency in panel size and shape, vital for the seamless assembly of the soccer ball. High-precision cutting minimizes material waste and enhances the aesthetic appeal of the finished product. Regular maintenance and calibration of these machines are essential to maintaining accuracy and minimizing downtime.
1.3 Panel Sewing
This phase traditionally relies on skilled labor, though automation is increasingly incorporated. Specialized sewing machines, potentially featuring advanced stitching techniques, are used to stitch together the individual panels. The stitching must be strong and even to ensure the ball's integrity. Quality control checks are implemented throughout to identify and correct any stitching flaws before proceeding. Sierra likely employs a multi-stage inspection process: initial checks after each panel is sewn, and a final check before moving to the next process. This reduces the likelihood of defective balls reaching the final stage. Efficient workplace design and training are key to minimizing errors and maximizing worker productivity in this labor-intensive stage.
1.4 Panel Inspection and Quality Control
Before the panels move to the next stage, rigorous quality control measures are essential. This involves a thorough visual inspection to check for stitching inconsistencies, material defects, and dimensional inaccuracies. Advanced techniques such as automated optical inspection systems might be utilized to enhance the speed and accuracy of this inspection process. Rejected panels are reworked or discarded, minimizing defects in subsequent stages. This stage directly impacts the overall quality of the final product and reduces the need for rework in later stages.
Process 2: Bladder Inflation, Bonding, and Finishing
The second process focuses on transforming the sewn panels into a functional soccer ball. Let’s examine each subprocess:
2.1 Bladder Insertion and Inflation
A high-quality rubber bladder is crucial for the soccer ball’s bounce and air retention. Specialized equipment is required for accurately inserting the bladder into the panel structure. The bladder is then carefully inflated to a precise pressure using calibrated equipment. Consistent inflation is critical to ensuring the ball’s roundness and performance characteristics. Any inconsistencies at this stage can lead to defects later on.
2.2 Panel Bonding and Shaping
This is a critical juncture. Once the bladder is inflated, the panel edges are bonded together using a specialized adhesive. This forms the seamless spherical shape of the soccer ball. The process requires precision to ensure a uniform bond and prevent leaks. Advanced techniques, such as ultrasonic welding or high-frequency bonding, may be employed to provide strong and durable bonds. Quality control at this stage involves pressure testing to identify any leaks or weaknesses in the bonding.
2.3 Finishing Touches and Decoration
This phase involves adding the final touches that transform the functional ball into a marketable product. This may include:
- Valve insertion and sealing: A secure valve is fitted to the bladder to allow inflation and deflation. Sealing is crucial to prevent air leakage.
- Logo and branding: Sierra’s logo and any sponsor logos are applied, typically through screen printing or heat transfer. The quality of the printing directly impacts the ball's visual appeal.
- Final inspection: A comprehensive final inspection is done to ensure the ball meets Sierra’s quality standards. This includes checking for defects, proper inflation, and accurate branding.
2.4 Packaging and Distribution
Once the balls pass final inspection, they are carefully packaged to prevent damage during shipping and storage. The packaging also plays a crucial role in the brand's presentation to customers. Efficient warehousing and logistics are needed to ensure timely delivery to retailers and consumers.
Potential Bottlenecks and Optimization Strategies
Identifying potential bottlenecks is crucial to optimizing Sierra's manufacturing process. Potential bottlenecks could arise in:
- Panel sewing: This labor-intensive process can be slowed by skill shortages or machine malfunctions. Automation and advanced training programs can mitigate this.
- Bladder insertion: This delicate process requires precision and skill. Ergonomic workspaces and advanced equipment can improve efficiency and reduce errors.
- Panel bonding: Inconsistencies in the adhesive application or bonding process can lead to delays and defects. Regular equipment maintenance and operator training can address this.
- Quality control: Inefficient inspection processes can create bottlenecks. Automation and advanced inspection technologies can significantly improve speed and accuracy.
To optimize the process, Sierra could implement:
- Lean manufacturing principles: Eliminating waste (time, materials, effort) throughout the process.
- Six Sigma methodologies: Reducing defects and variability in the production process.
- Automated guided vehicles (AGVs): Moving materials between stages efficiently.
- Predictive maintenance: Minimizing downtime through proactive equipment maintenance.
- Data analytics: Analyzing production data to identify and address inefficiencies.
- Investing in advanced technologies: Embracing cutting-edge machinery for higher precision and efficiency.
The Importance of Quality Control at Every Stage
The success of Sierra Company hinges on its commitment to quality. Robust quality control measures throughout both manufacturing processes are critical to maintaining its reputation and ensuring customer satisfaction. This includes thorough inspections at each stage, utilizing a blend of manual and automated checks to identify and rectify defects before they progress through the production line. A rigorous quality control system minimizes waste, improves efficiency, and builds customer trust.
Sustainability and Ethical Considerations
Beyond efficiency, Sierra Company should consider the environmental and ethical aspects of its production. This involves:
- Sustainable material sourcing: Using eco-friendly materials, minimizing environmental impact, and sourcing materials from ethical and responsible suppliers.
- Waste reduction: Implementing strategies to minimize waste throughout the process, including recycling and reusing materials.
- Fair labor practices: Ensuring fair wages and safe working conditions for all employees.
- Energy efficiency: Optimizing energy consumption in the manufacturing process.
By addressing these elements, Sierra can enhance its brand reputation and appeal to increasingly environmentally conscious consumers.
Conclusion
Sierra Company's soccer ball manufacturing process exemplifies a sophisticated blend of traditional craftsmanship and modern technology. By continually optimizing its two-stage system and integrating principles of lean manufacturing, quality control, and sustainability, Sierra can maintain a competitive edge in the market and deliver high-quality, durable soccer balls to consumers worldwide. The ongoing analysis of bottlenecks, the implementation of advanced technologies, and a firm commitment to quality control remain key to the company's continued success. Adapting to changing market demands and embracing innovative practices will ensure Sierra maintains its position as a leading manufacturer in the sporting goods industry.
Latest Posts
Latest Posts
-
Screen Addiction Among Teens Is There Such A Thing Answers
Apr 19, 2025
-
Short Speech To My Friends By Amiri Baraka
Apr 19, 2025
-
Plant Cell Organelles And Structures Answer Key
Apr 19, 2025
-
Although The Majority Of Americans Think Budgeting Is Important About
Apr 19, 2025
-
Drag The Appropriate Labels To Their Respective Targets Digestive System
Apr 19, 2025
Related Post
Thank you for visiting our website which covers about Sierra Company Manufactures Soccer Balls In Two Sequential Processes . We hope the information provided has been useful to you. Feel free to contact us if you have any questions or need further assistance. See you next time and don't miss to bookmark.