Simon And Sean Both Manage Factories
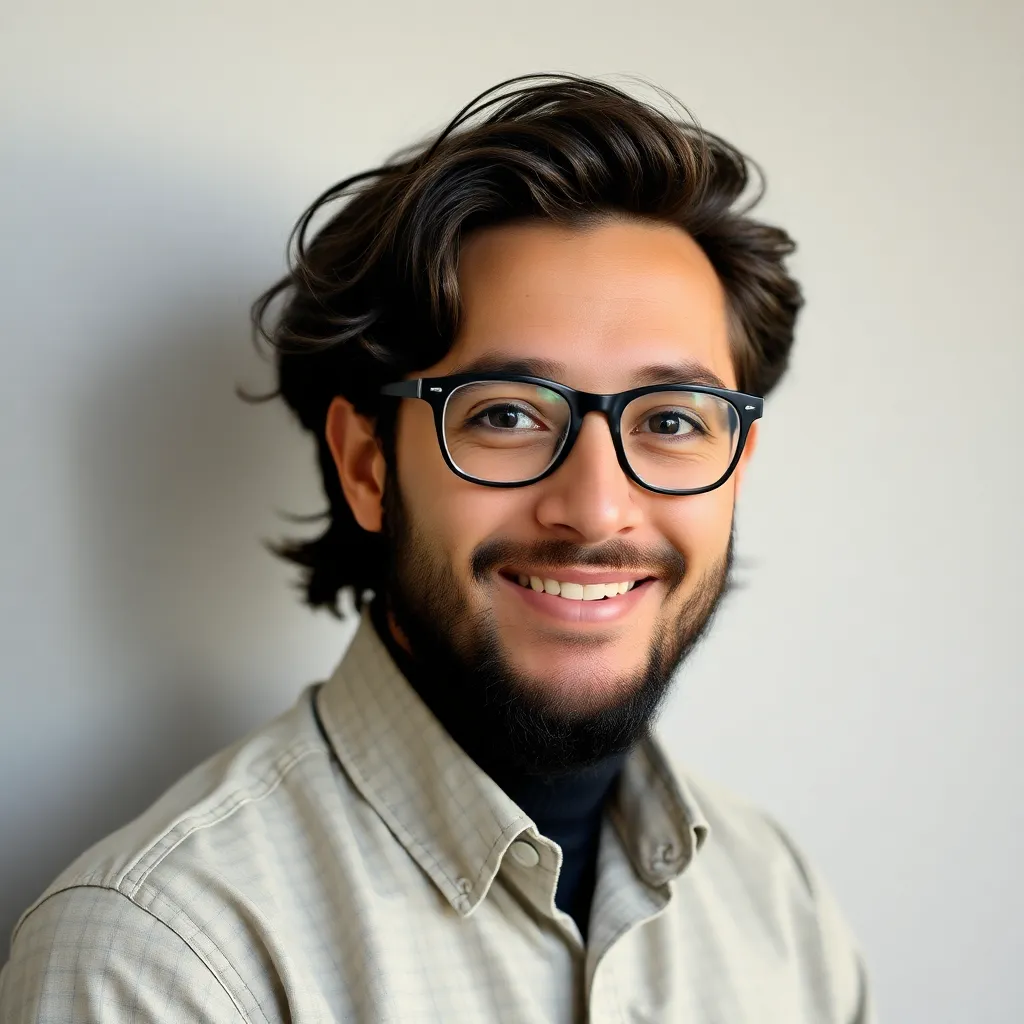
Onlines
May 09, 2025 · 6 min read
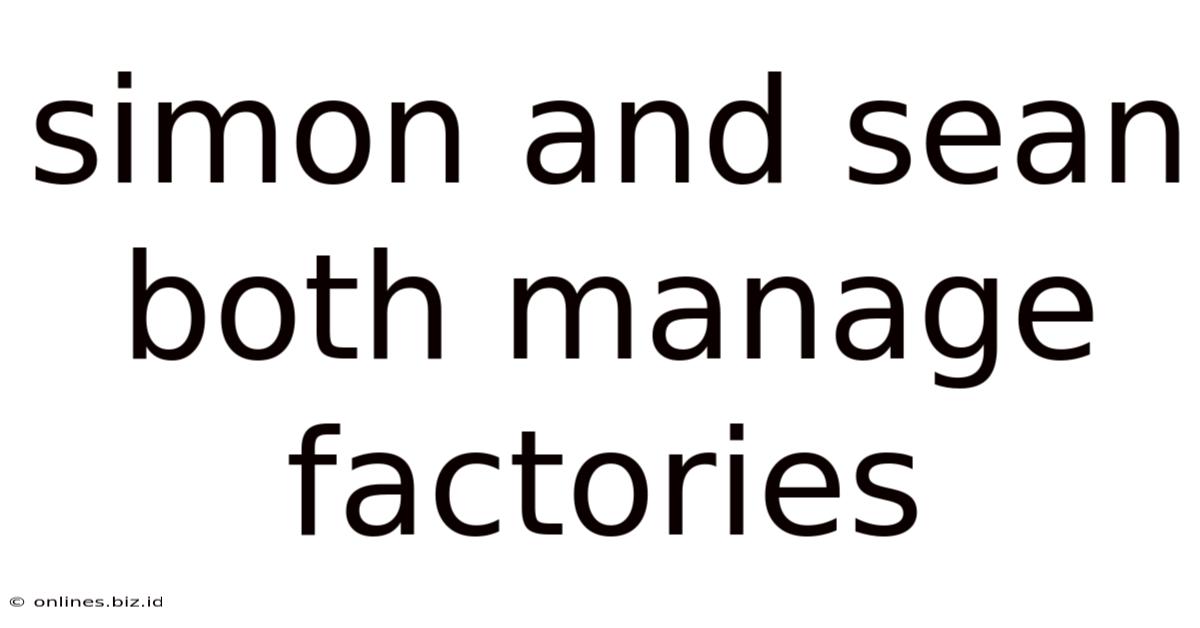
Table of Contents
Simon and Sean: A Tale of Two Factory Managers
Two factory managers, Simon and Sean, each oversee bustling production facilities. While both strive for efficiency and profitability, their management styles, approaches to problem-solving, and leadership philosophies differ significantly, leading to contrasting results and workplace cultures. This article delves deep into their individual approaches, exploring the strengths and weaknesses of each style, and ultimately examining what constitutes effective factory management in the modern era.
Simon: The Data-Driven Dictator
Simon is a firm believer in the power of data. His factory floor is a meticulously documented ecosystem, with every process, every machine, and every employee's performance meticulously tracked and analyzed. He uses sophisticated software to monitor production output, identify bottlenecks, and predict potential problems before they arise. His management style is authoritarian, with clear lines of command and a strict adherence to procedure.
Simon's Strengths:
- Efficiency and Optimization: Simon's data-driven approach leads to significant efficiencies. By identifying and eliminating bottlenecks, he consistently maximizes output and minimizes waste. His relentless focus on metrics ensures that the factory operates at peak performance. He understands lean manufacturing principles and utilizes them effectively to streamline processes. This focus on process improvement is a key contributor to his factory's success.
- Predictive Maintenance: The meticulous data collection allows for predictive maintenance. By analyzing machine performance data, Simon can anticipate potential equipment failures and schedule maintenance proactively, minimizing downtime and maximizing uptime. This reduces costly repairs and keeps production running smoothly. This proactive approach demonstrates a strong understanding of total productive maintenance (TPM).
- Clear Expectations and Accountability: Simon leaves no room for ambiguity. Employees know exactly what is expected of them, and performance is rigorously evaluated based on quantifiable metrics. This creates a highly accountable environment, where individual contributions are clearly measured and rewarded. This emphasis on Key Performance Indicators (KPIs) ensures that everyone is working towards common goals.
Simon's Weaknesses:
- Lack of Employee Morale: Simon's authoritarian style can stifle employee creativity and morale. The constant pressure to meet strict targets and the lack of autonomy can lead to burnout and high employee turnover. The absence of employee empowerment significantly impacts the overall work environment.
- Rigidity and Resistance to Change: Simon's reliance on data can make him resistant to innovative ideas or changes that are not supported by hard numbers. This inflexibility can hinder the factory's ability to adapt to changing market conditions or technological advancements. His focus on proven methods can limit the adoption of potentially beneficial new technologies.
- Over-reliance on Technology: While data analysis is crucial, Simon's over-reliance on technology can lead to a disconnect between management and the workers on the factory floor. He might fail to recognize the human element and the importance of employee feedback and engagement. Ignoring the soft skills aspect of management can be detrimental to long-term success.
Sean: The Collaborative Cultivator
Sean takes a drastically different approach. He prioritizes employee engagement and collaboration. His management style is participative, fostering a culture of open communication and shared decision-making. He believes that empowering his employees is the key to unlocking their potential and driving innovation.
Sean's Strengths:
- High Employee Morale: Sean's collaborative approach fosters a positive and supportive work environment. Employees feel valued, heard, and empowered, leading to high morale and increased productivity. He understands the importance of team building and uses various methods to foster a strong sense of camaraderie among the workforce.
- Innovation and Adaptability: By encouraging open communication and collaboration, Sean cultivates a culture of innovation. Employees feel comfortable sharing their ideas and suggestions, leading to creative problem-solving and adaptability to changing circumstances. This emphasis on continuous improvement (Kaizen) ensures the factory remains competitive.
- Strong Employee Retention: The positive work environment and the feeling of being valued leads to high employee retention rates. This reduces training costs and maintains a skilled and experienced workforce. A low turnover rate is a significant advantage for any factory.
Sean's Weaknesses:
- Potential for Inefficiency: The collaborative approach can sometimes lead to slower decision-making processes and potential inefficiencies. Reaching consensus on every decision can be time-consuming. Balancing collaboration and efficiency requires careful planning and organization.
- Difficulty in Measuring Performance: While employee morale is important, it can be difficult to quantify the impact of Sean's approach on overall productivity. Traditional metrics might not fully capture the benefits of a collaborative environment. This lack of quantifiable results might be a challenge when reporting to higher management.
- Dependence on Employee Initiative: Sean's approach relies heavily on the initiative and commitment of his employees. If some employees lack motivation or are not fully engaged, it could negatively impact overall performance. Managing individual employee performance and motivation remains crucial even within a collaborative setting.
Comparing Simon and Sean: A Synthesis
Both Simon and Sean have achieved success in their respective factories, proving that there is no single "best" management style. However, a synthesis of their approaches could lead to an even more effective management model. The ideal factory manager needs to combine the data-driven precision of Simon with the employee-centric approach of Sean.
This involves:
- Data-informed Collaboration: Utilizing data to identify areas for improvement, but then engaging employees in the process of finding solutions. This combines the strength of data analysis with the innovative power of collaborative problem-solving.
- Transparent Communication: Sharing performance data with employees, but doing so in a way that encourages engagement and feedback rather than fostering fear and pressure. Open communication is crucial for a healthy and productive work environment.
- Empowered Teams: Setting clear goals and expectations, but allowing teams the autonomy to decide how best to achieve those goals. This balances accountability and empowerment, fostering both efficiency and creativity.
- Continuous Learning and Development: Investing in employee training and development to foster continuous improvement, both in individual skills and in overall factory processes. Investing in employees demonstrates commitment and promotes loyalty.
The Future of Factory Management
The future of factory management will likely involve a greater integration of technology and human capital. This means leveraging data analytics to improve efficiency while simultaneously empowering employees to participate actively in the decision-making process. The success of a factory will depend not only on its technological capabilities but also on its ability to create a positive, supportive, and innovative work environment where employees feel valued and respected. The best factory managers will be those who can master the art of combining these two seemingly disparate approaches to optimize both efficiency and employee well-being. This shift towards a more human-centered approach to management will be critical for success in the competitive landscape of the modern factory. Furthermore, integrating sustainable practices and a focus on corporate social responsibility will increasingly become crucial aspects of successful factory management, attracting skilled workers and enhancing the factory's reputation. Finally, the incorporation of automation and robotics necessitates a workforce capable of collaborating with these technologies, highlighting the need for ongoing training and adaptation.
Latest Posts
Latest Posts
-
Jacobs Favorite Poker Game Is Texas Hold Em
May 09, 2025
-
Nih Stroke Scale Quizlet Group A
May 09, 2025
-
What Additional Assessment And Stabilization Activities
May 09, 2025
-
The Girl Who Raised Pigeons Summary
May 09, 2025
-
Toni Morrison Song Of Solomon Quotes
May 09, 2025
Related Post
Thank you for visiting our website which covers about Simon And Sean Both Manage Factories . We hope the information provided has been useful to you. Feel free to contact us if you have any questions or need further assistance. See you next time and don't miss to bookmark.