Sketch And Label Five Edge Preparations Used For Welding Joints
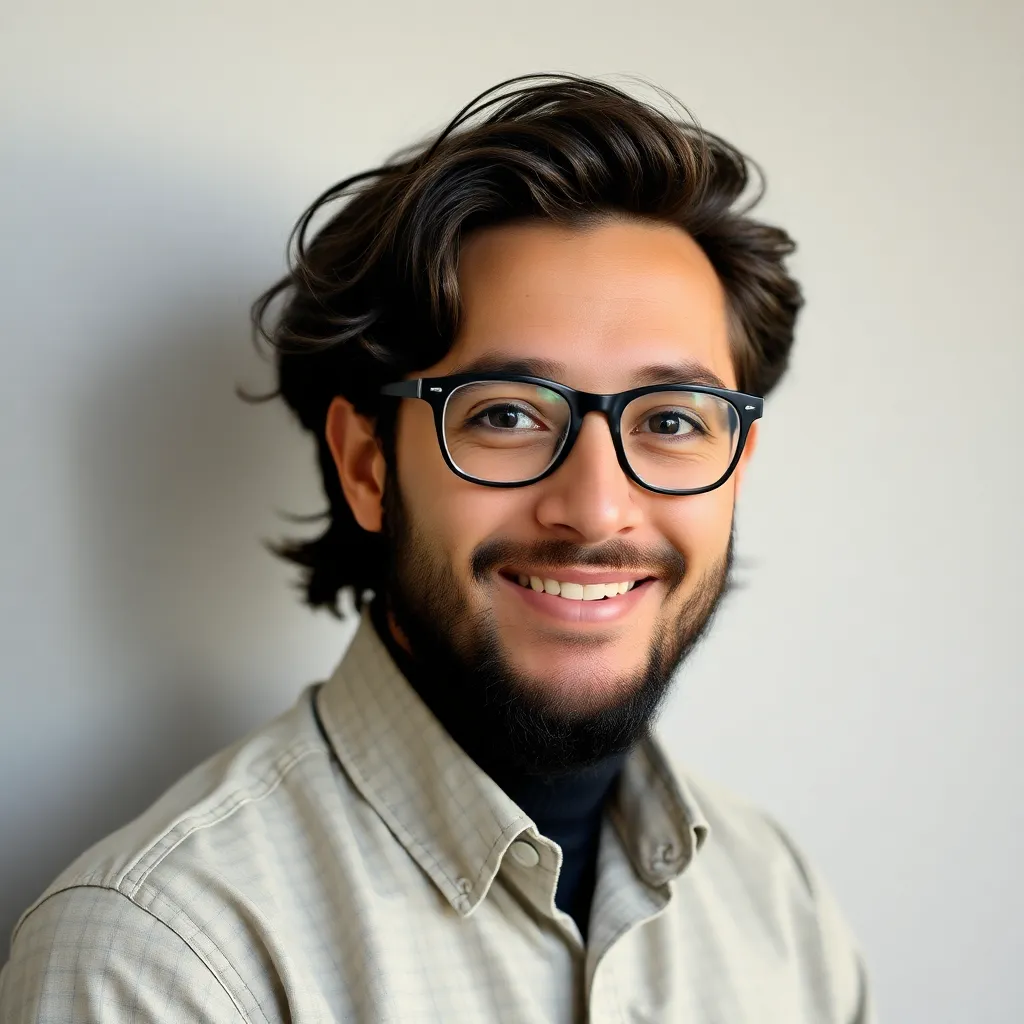
Onlines
Apr 08, 2025 · 5 min read

Table of Contents
Sketch and Label Five Edge Preparations Used for Welding Joints
Welding is a fundamental process in various industries, from construction and manufacturing to automotive and aerospace. The strength and integrity of a weld are heavily reliant on proper joint preparation. Edge preparation, also known as joint design, refers to the shaping of the metal edges before welding to ensure complete penetration, minimize distortion, and achieve the desired weld quality. This article will delve into five common edge preparations used for welding joints, providing detailed sketches, labels, and explanations of their applications. We'll explore their advantages and disadvantages, helping you choose the appropriate preparation for your specific welding project.
1. Square Butt Joint
This is the simplest form of edge preparation. Both edges of the materials to be joined are cut square, meeting at a 90-degree angle. It's often used for thin materials where complete penetration is easily achieved.
Sketch and Labels:
+-----------------+ +-----------------+
| | | |
| Material 1 | | Material 2 |
| | | |
+-----------------+-----+-----------------+
^
| Weld
V
Labels:
- Material 1: The first piece of metal.
- Material 2: The second piece of metal.
- Weld: The area where the two materials are fused together.
Advantages:
- Simple and fast: Requires minimal preparation time.
- Economical: No specialized tools or techniques are needed.
Disadvantages:
- Limited penetration for thicker materials: May not achieve complete fusion in thicker sections, leading to weaker welds.
- Increased risk of undercutting: Requires precise alignment and careful welding technique to prevent incomplete fusion at the edges.
- High distortion potential: Significant distortion can occur due to the lack of edge preparation to control the heat input.
2. Single-Bevel Butt Joint
The single-bevel butt joint involves beveling one edge of the material at a specific angle, typically between 30 and 60 degrees. This allows for better penetration and reduces the amount of filler metal required compared to the square butt joint.
Sketch and Labels:
+-----------------+
| |
| Material 1 |
| |
+--------/--------+-----+-----------------+
^ | |
| Weld | Material 2 |
V | |
+-----------------+
Labels:
- Material 1: The beveled piece of metal. Note the beveled edge.
- Material 2: The square-edged piece of metal.
- Weld: The area where the two materials are fused together.
- Bevel Angle: The angle at which the edge of Material 1 is beveled (typically 30-60 degrees).
Advantages:
- Improved penetration: Allows for better fusion in thicker materials.
- Reduced filler metal: Less filler metal is needed compared to a square butt joint.
- Better control over heat input: The bevel helps manage the heat distribution during welding.
Disadvantages:
- More complex preparation: Requires more time and skill to prepare the bevel.
- Possible distortion: Distortion can still occur, although typically less than with a square butt joint.
3. Double-Bevel Butt Joint
In this preparation, both edges of the materials are beveled at the same angle, usually meeting at a point. This is a common preparation for thicker materials where complete penetration is crucial.
Sketch and Labels:
+--------\--------+-----+--------/--------+
| | | |
| Material 1 | | Material 2 |
| | | |
+--------\--------+-----+--------/--------+
^
| Weld
V
Labels:
- Material 1: The first beveled piece of metal.
- Material 2: The second beveled piece of metal.
- Weld: The area where the two materials are fused together.
- Bevel Angle: The angle of the bevel on both materials (typically 30-60 degrees).
Advantages:
- Excellent penetration: Ensures complete fusion in thick materials.
- Reduced distortion: The symmetrical bevel helps minimize distortion.
- Stronger weld: Provides a stronger and more reliable weld.
Disadvantages:
- Time-consuming preparation: Requires more time and skill than simpler preparations.
- Higher cost: The increased preparation time leads to a higher cost per weld.
4. Single-J Butt Joint
Similar to the single-bevel joint, the single-J butt joint has one edge beveled, but the bevel is shaped like a "J". This provides better penetration and root reinforcement. The "J" shape helps to prevent undercutting and ensures complete fusion at the root of the weld.
Sketch and Labels:
+-----------------+
| |
| Material 1 |
| |
+------J------+-----+-----------------+
^ | |
| Weld | Material 2 |
V | |
+-----------------+
Labels:
- Material 1: The piece of metal with the "J" bevel.
- Material 2: The square-edged piece of metal.
- Weld: The area where the two materials are fused together.
- J-Bevel: The "J" shaped bevel.
Advantages:
- Excellent root penetration: Provides better root penetration and reinforcement.
- Reduced undercut: Minimizes the risk of undercut at the root of the weld.
- Stronger weld: Results in a stronger and more reliable weld.
Disadvantages:
- Complex preparation: Requires specialized tools and skills for accurate preparation.
- Increased preparation time: Takes longer to prepare compared to simpler joints.
5. Double-J Butt Joint
This is the symmetrical counterpart to the single-J butt joint, with both edges beveled in a "J" shape. This preparation is typically used for thicker sections where maximum strength and penetration are required.
Sketch and Labels:
+------J------+-----+------J------+
| | | |
| Material 1 | | Material 2 |
| | | |
+------J------+-----+------J------+
^
| Weld
V
Labels:
- Material 1: The first piece of metal with a "J" bevel.
- Material 2: The second piece of metal with a "J" bevel.
- Weld: The area where the two materials are fused together.
- J-Bevel: The "J" shaped bevel on both materials.
Advantages:
- Superior root penetration: Provides excellent root penetration and reinforcement.
- Reduced distortion: The symmetrical design helps to minimize distortion.
- Maximum strength: Creates a weld with maximum strength and durability.
Disadvantages:
- Most complex preparation: Requires significant skill and specialized tools for precise preparation.
- High cost: The increased preparation time and complexity leads to higher costs.
- Requires experienced welders: Proper execution needs experienced welders to ensure the quality of the weld.
Choosing the Right Edge Preparation
Selecting the appropriate edge preparation depends on several factors, including:
- Material thickness: Thicker materials generally require more complex preparations like double-bevel or double-J joints to ensure complete penetration.
- Joint type: The specific type of joint (butt, lap, T-joint, etc.) dictates the suitable edge preparation.
- Weldability of the material: The material's properties affect the choice of preparation and welding process.
- Required weld strength: Applications requiring high strength necessitate a preparation that provides maximum penetration and root reinforcement.
- Cost and time constraints: Simpler preparations are faster and cheaper but may not be suitable for all applications.
Understanding the characteristics of different edge preparations is crucial for achieving high-quality, strong, and reliable welds. This knowledge allows welders and engineers to select the optimal preparation for each specific application, maximizing weld integrity and minimizing potential defects. Remember always to prioritize safety and follow proper welding procedures.
Latest Posts
Latest Posts
-
Which Statement Describes How Connotation Is Used In This Passage
Apr 17, 2025
-
The Shotgun Approach To Keyword Searches Involves
Apr 17, 2025
-
Chapter 4 Lesson 4 Activity Credit Is Costly
Apr 17, 2025
-
Ample Evidence That Chuck Should Not Be Served
Apr 17, 2025
-
Student Exploration Unit Conversions Gizmo Answers
Apr 17, 2025
Related Post
Thank you for visiting our website which covers about Sketch And Label Five Edge Preparations Used For Welding Joints . We hope the information provided has been useful to you. Feel free to contact us if you have any questions or need further assistance. See you next time and don't miss to bookmark.