The 5ss Developed By The Japanese Do Not Include
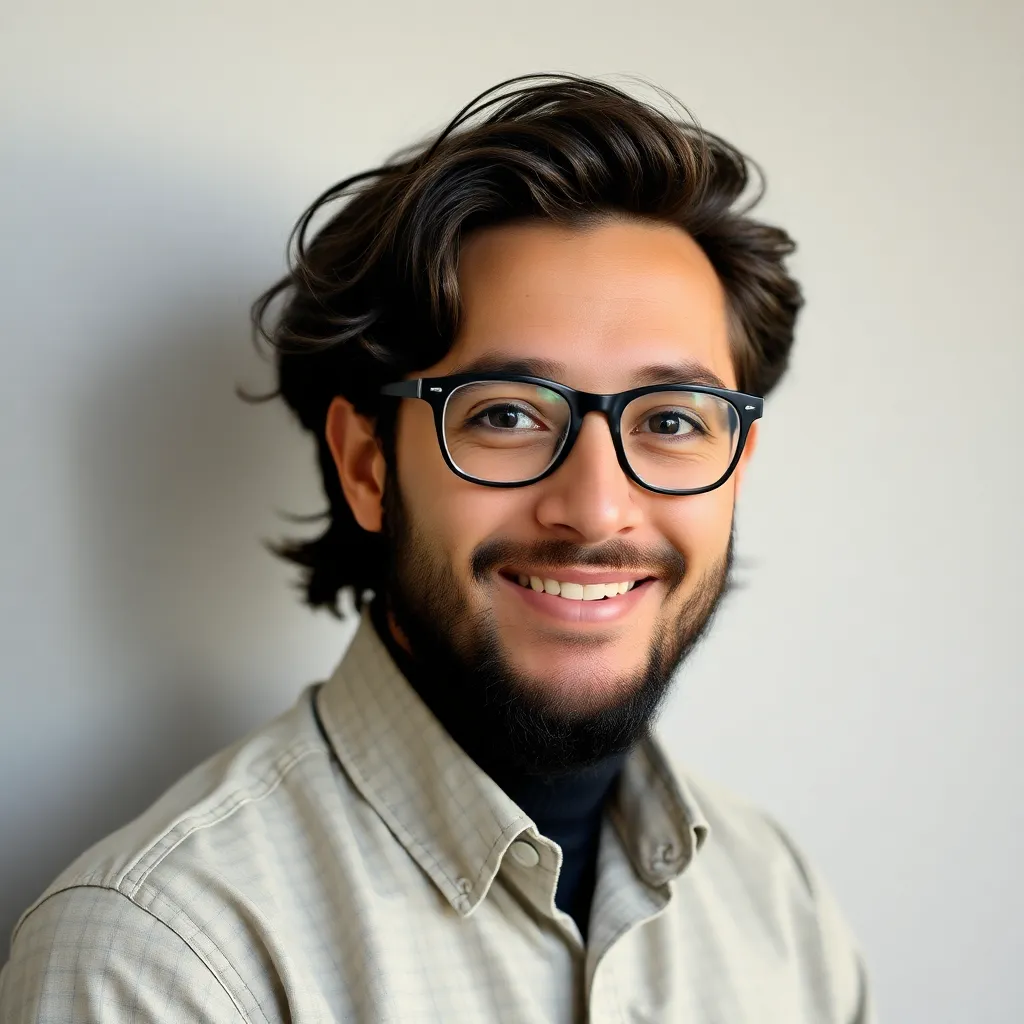
Onlines
Apr 19, 2025 · 6 min read
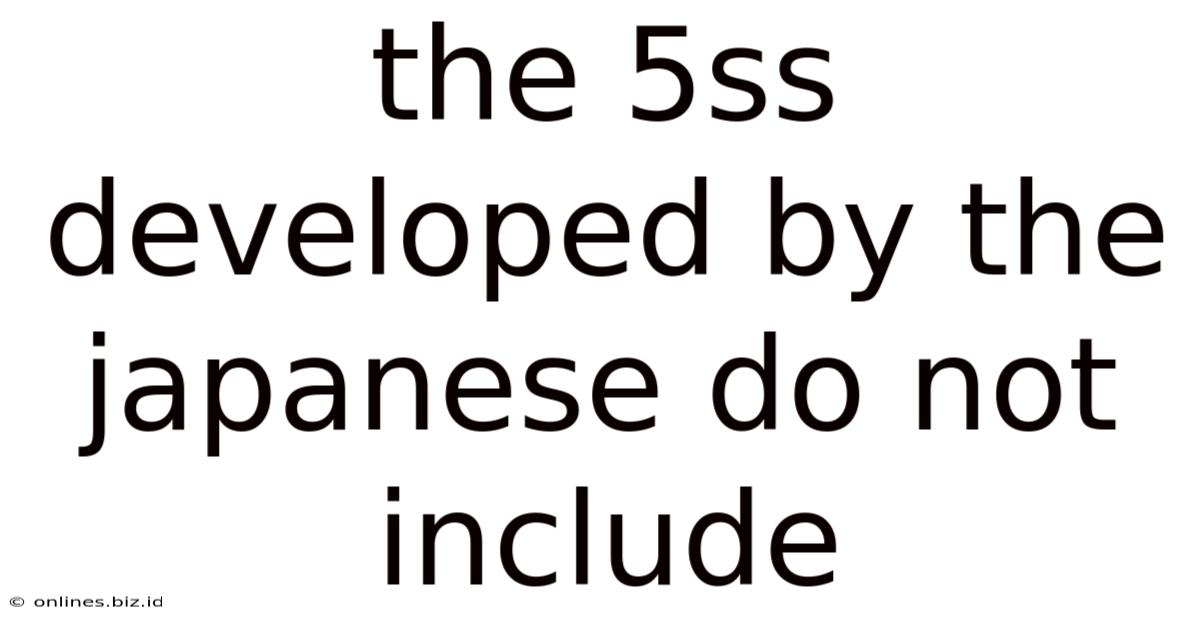
Table of Contents
- The 5ss Developed By The Japanese Do Not Include
- Table of Contents
- The 5S Developed by the Japanese: What It Doesn't Include
- Understanding the Core Principles of 5S
- What 5S is NOT: Common Misconceptions and Exclusions
- 1. 5S is NOT a Complete Quality Management System
- 2. 5S is NOT a Substitute for Process Improvement
- 3. 5S is NOT a One-Time Implementation
- 4. 5S is NOT Merely About Tidiness and Aesthetics
- 5. 5S is NOT a Standalone Solution for Every Problem
- 6. 5S Doesn't Automatically Lead to Increased Productivity
- 7. 5S Does Not Include Advanced Technology Integration
- 8. 5S Doesn't Guarantee Safety Improvements
- 9. 5S is NOT a Quick Fix
- 10. 5S Doesn't Replace Employee Training and Development
- Conclusion: Effective 5S Implementation
- Latest Posts
- Latest Posts
- Related Post
The 5S Developed by the Japanese: What It Doesn't Include
The 5S methodology, originating in Japan, is a powerful lean manufacturing technique designed to optimize workplace organization and efficiency. While widely adopted and adapted across various industries, understanding what 5S doesn't encompass is just as crucial as understanding what it does. This comprehensive guide delves into the core principles of 5S, highlighting its limitations and exploring areas often mistakenly included within its framework. By clarifying these distinctions, we aim to provide a more nuanced and practical understanding of 5S's application and its limitations.
Understanding the Core Principles of 5S
Before exploring the exclusions, let's briefly review the five core principles of 5S:
-
Seiri (Sort): This involves eliminating unnecessary items from the workplace. This is about identifying and removing anything that doesn't contribute to the production process, including broken tools, outdated documents, and excess inventory. The goal is to create a clean and organized space.
-
Seiton (Set in Order): Once unnecessary items are removed, the remaining items need to be organized logically and efficiently. This includes creating a clear system for storing and retrieving items, ensuring everything has a designated place, and implementing visual aids like labels and shadow boards.
-
Seiso (Shine): This step focuses on cleaning and maintaining the workspace. This goes beyond simply tidying up; it involves regular cleaning and inspection to identify potential problems before they escalate. The aim is to maintain a consistently clean and well-maintained environment.
-
Seiketsu (Standardize): This crucial step establishes clear standards and procedures for maintaining the workplace organization achieved through the previous three steps. This involves creating checklists, training employees, and documenting best practices to ensure consistency and prevent backsliding.
-
Shitsuke (Sustain): This is the final and arguably most important step, focusing on maintaining the improvements achieved through the previous four steps. It emphasizes continuous improvement, regular audits, and a commitment to consistently upholding the established standards. This involves building a culture of organization and efficiency within the workplace.
What 5S is NOT: Common Misconceptions and Exclusions
While 5S is a highly effective methodology, it's crucial to understand its limitations and what it doesn't inherently encompass. Many organizations mistakenly include elements that fall outside the core principles:
1. 5S is NOT a Complete Quality Management System
While 5S contributes significantly to quality improvement by fostering a more organized and efficient workplace, it's not a complete quality management system (QMS) in itself. A comprehensive QMS encompasses far broader aspects, including quality planning, quality control, quality assurance, and continuous improvement methodologies like Six Sigma or Kaizen, which go beyond the scope of workplace organization. 5S can be part of a QMS, but it's not a substitute.
2. 5S is NOT a Substitute for Process Improvement
5S focuses on workplace organization and cleanliness, but it doesn't inherently address process inefficiencies or bottlenecks. While a well-organized workspace can indirectly improve efficiency, 5S doesn't directly tackle issues like workflow optimization, process redesign, or eliminating waste in the production process itself. Process improvement methodologies like Lean Manufacturing or Value Stream Mapping are necessary for addressing these issues.
3. 5S is NOT a One-Time Implementation
Many organizations approach 5S as a one-time project, implementing the five steps and then considering it complete. However, the true power of 5S lies in its sustained application. The "Sustain" (Shitsuke) phase is critical; without ongoing commitment to maintaining standards and continuously improving, the initial gains will likely be lost over time. 5S requires continuous monitoring, review, and adaptation.
4. 5S is NOT Merely About Tidiness and Aesthetics
Although a cleaner and more organized workspace is a significant outcome of 5S, its core purpose extends beyond simple tidiness. The underlying goal is to improve efficiency, reduce waste, and enhance productivity. While aesthetics are a positive byproduct, focusing solely on the visual appeal can distract from the core objectives of improved efficiency and reduced waste.
5. 5S is NOT a Standalone Solution for Every Problem
While 5S can significantly contribute to various workplace challenges, it's not a universal solution for all problems. Complex organizational issues, such as inadequate training, poor communication, or systemic process failures, require more comprehensive solutions beyond the scope of 5S. It's crucial to accurately diagnose the root causes of problems and apply the appropriate solution, using 5S where it's most effective.
6. 5S Doesn't Automatically Lead to Increased Productivity
While a well-implemented 5S program can significantly boost productivity, it's not a guaranteed outcome. The success of 5S depends heavily on factors like management commitment, employee buy-in, and proper training. Without these crucial elements, even a perfectly executed 5S implementation may fail to yield significant productivity gains. It requires careful planning and consistent effort to achieve the desired results.
7. 5S Does Not Include Advanced Technology Integration
While a well-organized workplace can certainly facilitate the integration of technology, 5S itself doesn't inherently involve or require the implementation of specific technological tools or systems. The focus is on optimizing the existing workplace through organization and standardization, irrespective of the technological tools employed. Technological advancements can complement 5S but are not integral to its core principles.
8. 5S Doesn't Guarantee Safety Improvements
Although a clean and organized workspace contributes to a safer environment, 5S alone doesn't guarantee safety improvements. Comprehensive safety programs, including risk assessments, safety training, and the implementation of safety protocols, are crucial for achieving a truly safe workplace. 5S supports safety by creating a more organized and visually clear environment, but it's not a complete safety management system.
9. 5S is NOT a Quick Fix
Implementing 5S effectively requires a significant investment of time, resources, and commitment. It's not a quick fix solution to solve immediate problems. The benefits of 5S are achieved gradually through a systematic process of implementation and continuous improvement. It's a long-term strategy for optimizing workplace efficiency and maintaining a sustainable, organized environment.
10. 5S Doesn't Replace Employee Training and Development
While 5S can contribute to a more efficient and productive work environment, it doesn't replace the need for employee training and development. Effective employee training remains crucial for achieving optimal performance and maximizing the benefits of a well-organized workplace. 5S supports effective training by creating a more conducive learning environment, but it’s not a substitute for targeted skill development.
Conclusion: Effective 5S Implementation
The 5S methodology is a powerful tool for improving workplace organization and efficiency. However, its successful implementation depends on a clear understanding of its scope and limitations. By avoiding the common misconceptions outlined above and focusing on the core principles, organizations can leverage 5S to create a more productive, efficient, and sustainable work environment. Remember, 5S is a journey, not a destination—continuous improvement and sustained effort are key to its long-term success. Properly understanding what 5S doesn't include is as important as understanding what it does for successful implementation and maximizing its benefits. Only then can you truly unlock the potential of this powerful Japanese methodology.
Latest Posts
Latest Posts
-
The Acronym Score Is Used To Help Guide
May 08, 2025
-
Which Of The Following Is A Legitimate Purpose Of Discovery
May 08, 2025
-
A Companys Strategy Is At Full Power
May 08, 2025
-
Drag Each Microdensitometer Graph To The Appropriate Bin
May 08, 2025
-
With Remote Acquisitions What Problems Should You Be Aware Of
May 08, 2025
Related Post
Thank you for visiting our website which covers about The 5ss Developed By The Japanese Do Not Include . We hope the information provided has been useful to you. Feel free to contact us if you have any questions or need further assistance. See you next time and don't miss to bookmark.