The Charge In Glassworking Is Which One Of The Following
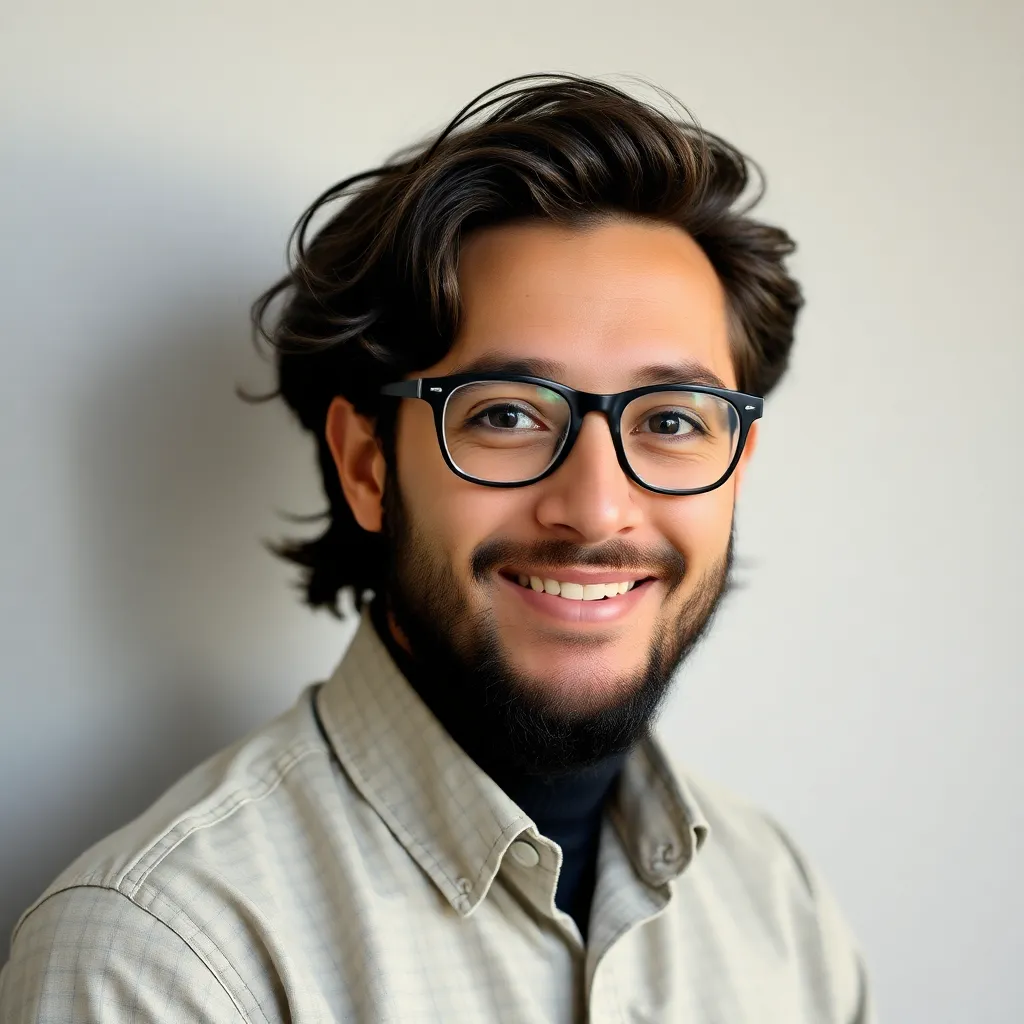
Onlines
Mar 14, 2025 · 6 min read
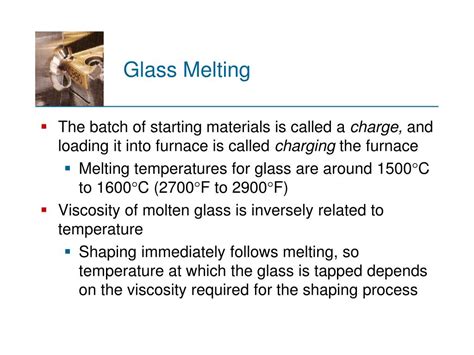
Table of Contents
The Charge in Glassworking: Understanding the Raw Materials and Their Impact
The term "charge" in glassmaking refers to the carefully measured and mixed batch of raw materials used to create molten glass. Understanding the charge is crucial for achieving the desired properties in the final glass product, impacting everything from color and clarity to durability and melting temperature. This comprehensive guide delves into the composition of a typical glass charge, exploring the individual components and their roles in the glassmaking process. We'll also examine how variations in the charge affect the final product's characteristics.
What Constitutes a Glass Charge?
A glass charge isn't a simple mixture; it's a precisely formulated blend of raw materials, each serving a specific purpose. The primary components are:
-
Silica (SiO₂): This is the fundamental building block of most glasses, forming the continuous network structure that gives glass its amorphous, non-crystalline nature. Silica is typically added in the form of sand, although other silica-rich materials may be used. The purity of the silica significantly impacts the final glass's clarity; impurities can lead to discoloration or undesirable bubbles.
-
Fluxing Agents: These materials lower the melting point of silica, making the glassmaking process more energy-efficient and less demanding on furnace equipment. Common fluxing agents include:
- Soda Ash (Na₂CO₃): Readily available and effective at lowering the melting point, soda ash is a staple in glassmaking. However, it introduces water solubility, making the glass susceptible to weathering.
- Potash (K₂CO₃): Similar to soda ash but contributes to greater durability and chemical resistance. Often used in combination with soda ash to balance properties.
- Limestone (CaCO₃): Provides stability and improves chemical resistance, reducing the glass's tendency to leach out components over time. It also contributes to the overall mechanical strength.
-
Stabilizers: Also known as fining agents, these counteract the effects of the fluxing agents, improving the glass's durability and chemical resistance. Key stabilizers include:
- Lime (CaO): A crucial stabilizer, lime improves the glass's resistance to water and other chemicals.
- Magnesia (MgO): Increases the glass's chemical durability and mechanical strength.
- Alumina (Al₂O₃): Enhances the glass's resistance to heat shock and improves its overall strength and durability. Often added in smaller amounts compared to other stabilizers.
The Importance of Precise Measurement and Mixing
The proportions of each component in the charge are critical. Slight variations can dramatically alter the final glass's properties. The exact recipe depends on the intended application of the glass. For instance, a charge for window glass will differ significantly from one designed for high-quality optical lenses or durable laboratory glassware. Careful weighing and mixing of the raw materials are essential for consistent results. Inconsistent mixing can lead to variations in composition throughout the molten glass, resulting in defects in the final product.
Beyond the Basics: Additives and Colorants
In addition to the primary components, various additives can be incorporated into the charge to modify the glass's properties or introduce specific characteristics. These include:
-
Colorants: Metal oxides and other compounds are added to create colored glass. Cobalt oxide produces blue, chromium oxide green, iron oxide various shades of yellow, brown, and green, and manganese oxide purple or pink. The careful selection and proportioning of colorants are essential to achieving the desired hue and intensity.
-
Decolorizers: These counteract the undesirable colors produced by impurities in the raw materials, leading to a clearer, more colorless glass. Common decolorizers include selenium, antimony, and cerium oxide.
-
Opacifiers: These are added to create opacity or translucence in the glass. Tin oxide creates opaque white, while bone ash can produce a milky, slightly yellowish opacity.
-
Fining Agents: These help remove bubbles from the molten glass, improving its clarity and optical properties. Common fining agents include arsenic trioxide and sodium sulfate.
The Impact of Charge Variations on Glass Properties
The composition of the charge directly influences the properties of the resulting glass. For example:
-
Increased soda ash content: Leads to a lower melting point but reduces chemical durability.
-
Increased lime content: Increases durability and chemical resistance but may make the glass harder to work with.
-
Increased silica content: Increases the viscosity and melting point, resulting in stronger glass but making it more difficult to process.
-
Presence of certain metal oxides: Introduces color and can alter other properties.
Understanding these relationships is vital for glassmakers to create glass with the desired properties for specific applications. The precise control over the charge composition allows glassmakers to tailor the glass to meet diverse needs.
Analyzing the Charge: Quality Control and Consistency
Maintaining the quality and consistency of the glass charge is essential for producing high-quality glass products consistently. Regular analysis of the raw materials and the final charge is therefore crucial. This typically involves:
-
Chemical analysis: Determining the exact composition of the raw materials and the blended charge, ensuring the correct proportions of each component.
-
Particle size analysis: Ensuring the appropriate particle size distribution for efficient melting and homogenous glass formation.
-
Impurity analysis: Identifying and quantifying any impurities in the raw materials, which can affect the glass's color, clarity, and other properties.
Different Types of Glass and Their Charges
The precise composition of the charge varies greatly depending on the type of glass being produced. Some examples include:
-
Soda-Lime Glass: The most common type, used for windows, bottles, and containers. Its charge typically consists of silica, soda ash, lime, and smaller amounts of magnesia and alumina.
-
Borosilicate Glass: Known for its high heat resistance, used for laboratory glassware and cookware. It contains a significant proportion of boric oxide (B₂O₃), which contributes to its thermal shock resistance.
-
Lead Glass (Crystal Glass): Characterized by its high refractive index, making it sparkle. It contains a substantial amount of lead oxide (PbO), which contributes to its brilliance.
-
Optical Glass: Used for lenses and prisms, requires highly purified raw materials and very precise control over the charge composition to achieve the desired optical properties.
The Future of Glass Charges: Sustainability and Innovation
The glass industry is increasingly focused on sustainability and reducing its environmental impact. This involves exploring alternative raw materials, optimizing the melting process to reduce energy consumption, and developing methods for recycling glass cullet (recycled glass). Innovations in charge composition are likely to continue, aiming for greater efficiency, improved properties, and reduced environmental footprint. Research into new fluxing agents, stabilizers, and colorants with less environmental impact will play a crucial role in this evolution.
Conclusion: A Complex but Crucial Aspect of Glassmaking
The charge in glassmaking is far more than a simple mixture of ingredients. It is a precisely formulated recipe that dictates the properties of the resulting glass. Understanding the role of each component—the silica network, the fluxing agents, the stabilizers, and the various additives—is crucial for producing glass with the desired characteristics. Maintaining quality control and adapting to evolving needs, such as environmental sustainability, are ongoing challenges and opportunities for innovation in the field of glassmaking. The charge, therefore, represents a critical point of control and optimization in the entire glassmaking process, influencing everything from cost-efficiency to the final aesthetic and functional properties of the glass.
Latest Posts
Latest Posts
-
The Island Of Dr Moreau Chapter Summary
Mar 15, 2025
-
Mi Abuela Ser Muy Trabajadora Y Amable
Mar 15, 2025
-
Advanced Hardware Lab 7 1 Work With Ip Addresses And Subnets
Mar 15, 2025
-
Ati Fluid Electrolyte And Acid Base Regulation
Mar 15, 2025
-
All Things Algebra Unit 3 Homework 2 Answer Key
Mar 15, 2025
Related Post
Thank you for visiting our website which covers about The Charge In Glassworking Is Which One Of The Following . We hope the information provided has been useful to you. Feel free to contact us if you have any questions or need further assistance. See you next time and don't miss to bookmark.