The Combination Coupling In Figure 1is Used To Connect
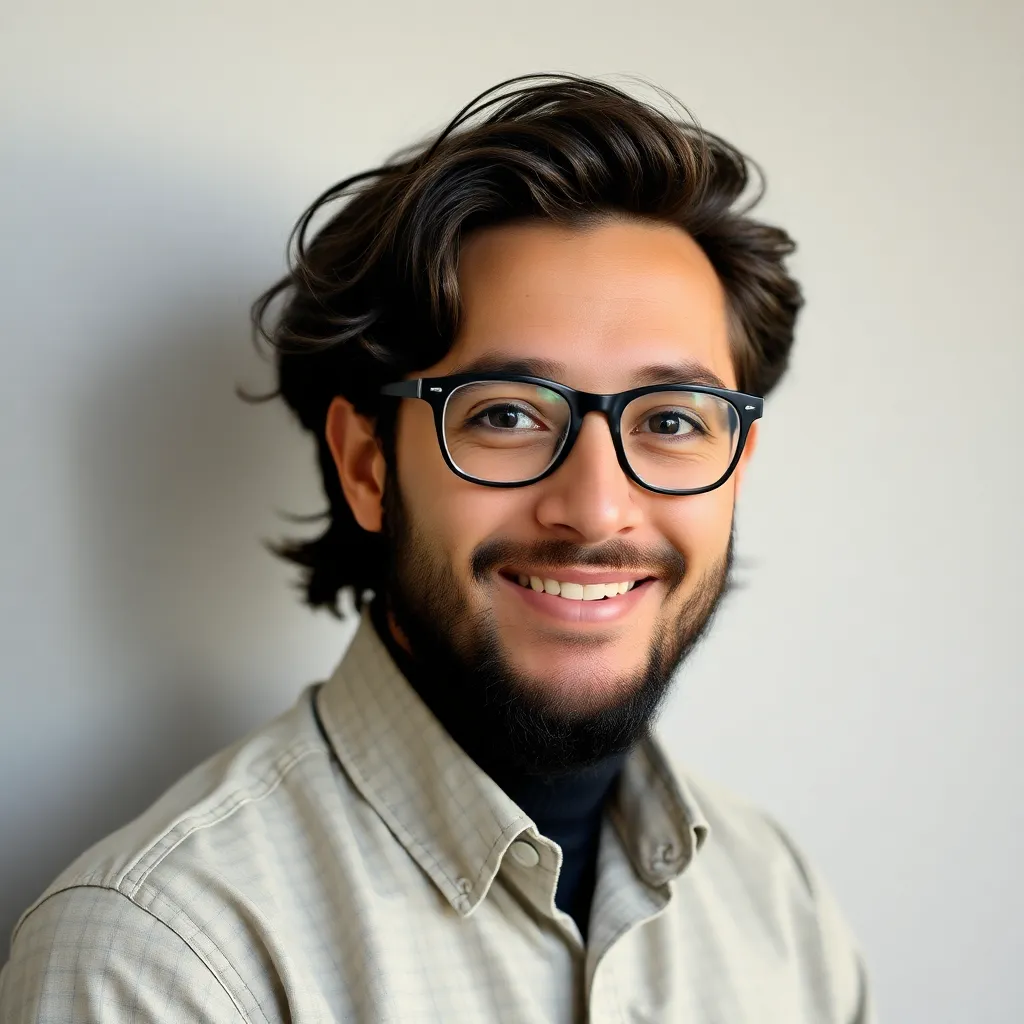
Onlines
Apr 15, 2025 · 6 min read

Table of Contents
The Combination Coupling: A Deep Dive into Design, Application, and Selection
Figure 1 (which would be included here if this were a visual document) depicts a combination coupling, a versatile mechanical device crucial for transmitting torque between rotating shafts. This article delves into the intricacies of combination couplings, exploring their design principles, diverse applications, selection criteria, and the critical factors ensuring optimal performance and longevity.
Understanding Combination Couplings: A Blend of Functionality
Combination couplings, as the name suggests, combine the characteristics of multiple coupling types into a single, integrated unit. This strategic design approach offers a robust and adaptable solution for a wide spectrum of power transmission applications. Unlike simple couplings which only address one specific issue, combination couplings effectively tackle multiple challenges simultaneously, leading to improved efficiency, reduced maintenance, and enhanced overall system reliability.
The precise combination of coupling types within a combination coupling is dictated by the specific application requirements. Common constituent types include:
-
Jaw Couplings: These couplings are known for their robust construction and ability to accommodate moderate misalignments (both angular and parallel). Their simple design and ease of installation make them popular choices across diverse industries.
-
Flexible Couplings: Often incorporating elastomeric elements (rubber or polyurethane), these couplings effectively absorb vibrations and shock loads, protecting connected equipment from damage. They are particularly valuable in applications involving fluctuating torques or significant vibrational stresses.
-
Rigid Couplings: Designed for precise alignment and high torque transmission, rigid couplings offer minimal flexibility. While simple and efficient, their inability to compensate for misalignment necessitates careful shaft alignment during installation.
-
Oldham Couplings: These couplings excel at accommodating parallel misalignment while maintaining a constant velocity ratio. This is crucial in applications demanding precise rotational synchronization.
The synergistic integration of these different coupling types within a combination coupling allows for a customized solution tailored to the specific application's needs, offering advantages that individual coupling types cannot match.
Design Principles and Key Components
The design of a combination coupling is far from arbitrary. It requires careful consideration of various factors to ensure optimal performance and reliability. Key design considerations include:
-
Material Selection: The choice of materials is paramount, impacting the coupling's strength, durability, corrosion resistance, and operating temperature range. Common materials include steel (for high strength), aluminum (for lightweight applications), and various polymers (for vibration damping).
-
Torque Capacity: The coupling must be adequately rated to handle the anticipated torque loads without failure. Overloading can lead to premature wear, component failure, and potential system damage.
-
Misalignment Compensation: The ability to accommodate misalignments is critical, especially in applications where perfect shaft alignment is difficult to achieve or maintain. Combination couplings excel in this area, providing superior tolerance for angular, parallel, and axial misalignments.
-
Vibration Damping: Many applications involve significant vibration, which can negatively impact connected equipment and reduce its lifespan. Combination couplings frequently incorporate features designed to mitigate these vibrations, enhancing the overall system's longevity and stability.
-
Ease of Installation and Maintenance: The design should prioritize ease of installation and maintenance, reducing downtime and minimizing labor costs. Features such as readily accessible fasteners and modular designs contribute significantly to this objective.
Diverse Applications Across Industries
Combination couplings find widespread application across diverse industries, each demanding unique performance characteristics:
-
Industrial Machinery: In heavy-duty industrial settings, combination couplings play a vital role in power transmission within machinery like conveyors, pumps, mixers, and other rotating equipment. Their ability to handle high torques, compensate for misalignments, and withstand harsh operating conditions makes them ideal for these demanding environments.
-
Robotics and Automation: The precision and flexibility offered by combination couplings are invaluable in robotic systems and automated manufacturing processes. They ensure smooth, reliable power transmission, facilitating intricate movements and precise control.
-
Power Generation: In power generation facilities, combination couplings contribute to efficient power transmission within turbines, generators, and other crucial components. Their reliability and ability to withstand significant loads are critical for ensuring uninterrupted power supply.
-
Automotive and Aerospace: While less common than in industrial settings, specialized combination couplings may find applications in automotive and aerospace industries where precise control and reliability are paramount.
-
Marine and Offshore: The robust nature and corrosion resistance of specific combination coupling designs make them suitable for use in marine and offshore applications, where exposure to harsh environments is a significant factor.
Selecting the Right Combination Coupling: Key Considerations
Choosing the appropriate combination coupling involves a careful evaluation of several critical factors:
-
Torque Requirements: Accurately determining the maximum torque the coupling will need to transmit is essential to avoid overloading and potential failure.
-
Speed Ratings: The coupling's speed rating must be compatible with the operating speed of the connected equipment. Operating beyond the rated speed can lead to premature wear and component failure.
-
Misalignment Capabilities: Assessing the anticipated level of misalignment is crucial in selecting a coupling that can effectively compensate for these imperfections. This includes evaluating both parallel and angular misalignments.
-
Environmental Conditions: The operating environment significantly impacts the choice of materials and design features. Factors such as temperature, humidity, and exposure to corrosive substances must be considered.
-
Maintenance Requirements: Understanding the required maintenance schedule and ease of access to components are critical for selecting a coupling that minimizes downtime and operational costs.
-
Cost: While performance is paramount, the overall cost of the coupling, including installation and maintenance, should also be taken into account.
Optimization and Maintenance for Extended Lifespan
Proper installation and ongoing maintenance are crucial for maximizing the lifespan and performance of any combination coupling:
-
Proper Alignment: Careful shaft alignment is paramount during installation to minimize stress and extend the coupling's operational life. Improper alignment is a leading cause of premature coupling failure.
-
Regular Inspections: Routine visual inspections can help detect early signs of wear, damage, or misalignment, allowing for timely intervention and preventative maintenance.
-
Lubrication: Many combination couplings require regular lubrication to ensure smooth operation and reduce wear. Following the manufacturer's lubrication recommendations is essential.
-
Replacement: When signs of significant wear or damage are observed, timely replacement is necessary to prevent catastrophic failures.
Conclusion: A Powerful Solution for Reliable Power Transmission
Combination couplings represent a powerful and versatile solution for transmitting torque between rotating shafts across a wide range of applications. Their ability to combine the advantages of multiple coupling types into a single unit results in superior performance, increased reliability, and reduced maintenance requirements. By carefully considering design principles, application needs, and selecting the appropriate coupling based on detailed assessment, engineers can leverage the benefits of combination couplings to create robust and efficient power transmission systems. Regular maintenance and attentive monitoring further contribute to their longevity and optimal performance, ensuring sustained operational effectiveness in even the most demanding environments. Understanding the nuances of combination couplings is therefore essential for maximizing system efficiency and minimizing downtime in diverse industrial settings.
Latest Posts
Latest Posts
-
Which Summarized Story Is Most Likely A Myth
Apr 16, 2025
-
Drag The Labels To Identify The Structures On A Vertebra
Apr 16, 2025
-
Cody Has Been Dealing With Chronic Stress
Apr 16, 2025
-
Amoeba Sisters Video Recap Monohybrid Crosses
Apr 16, 2025
-
Luis Fernando Compra Tres En La Libreria
Apr 16, 2025
Related Post
Thank you for visiting our website which covers about The Combination Coupling In Figure 1is Used To Connect . We hope the information provided has been useful to you. Feel free to contact us if you have any questions or need further assistance. See you next time and don't miss to bookmark.