The Composite Bar Consists Of A 20-mm-diameter
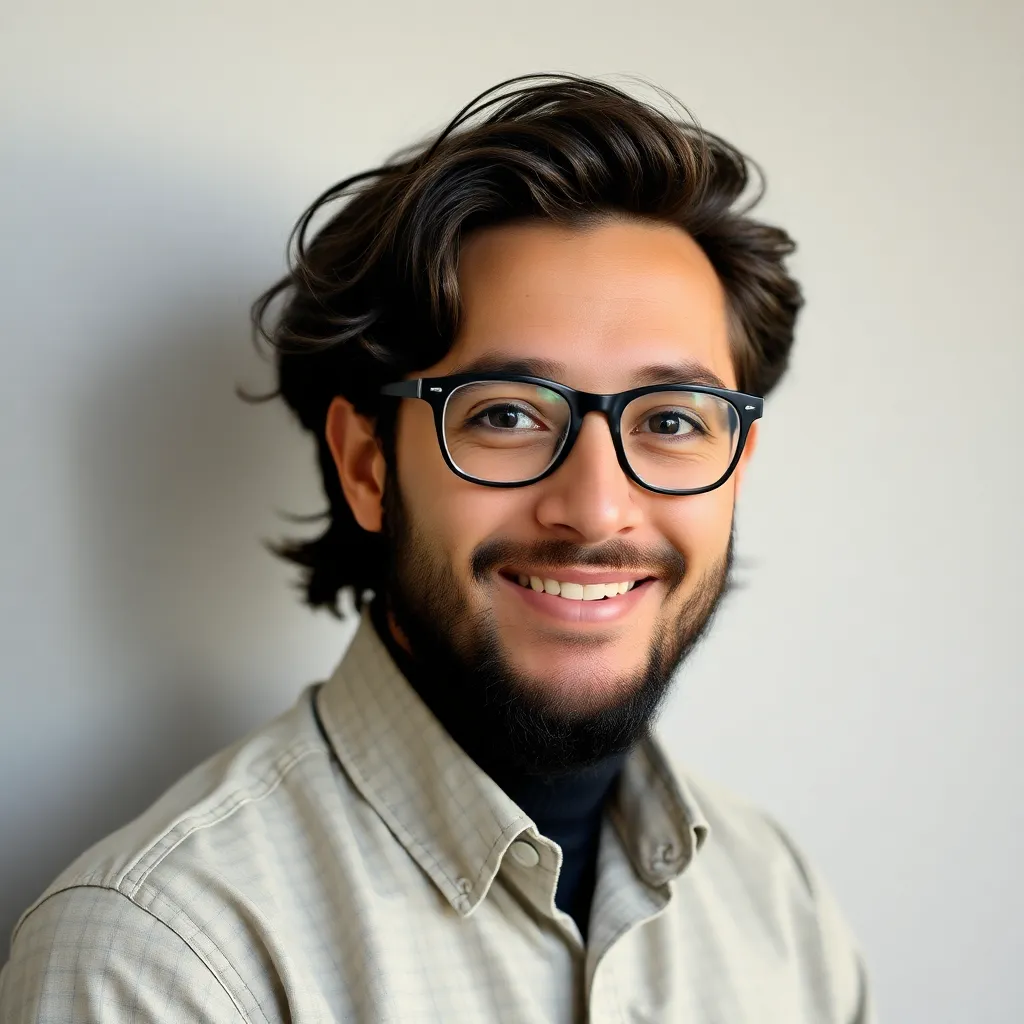
Onlines
May 09, 2025 · 5 min read
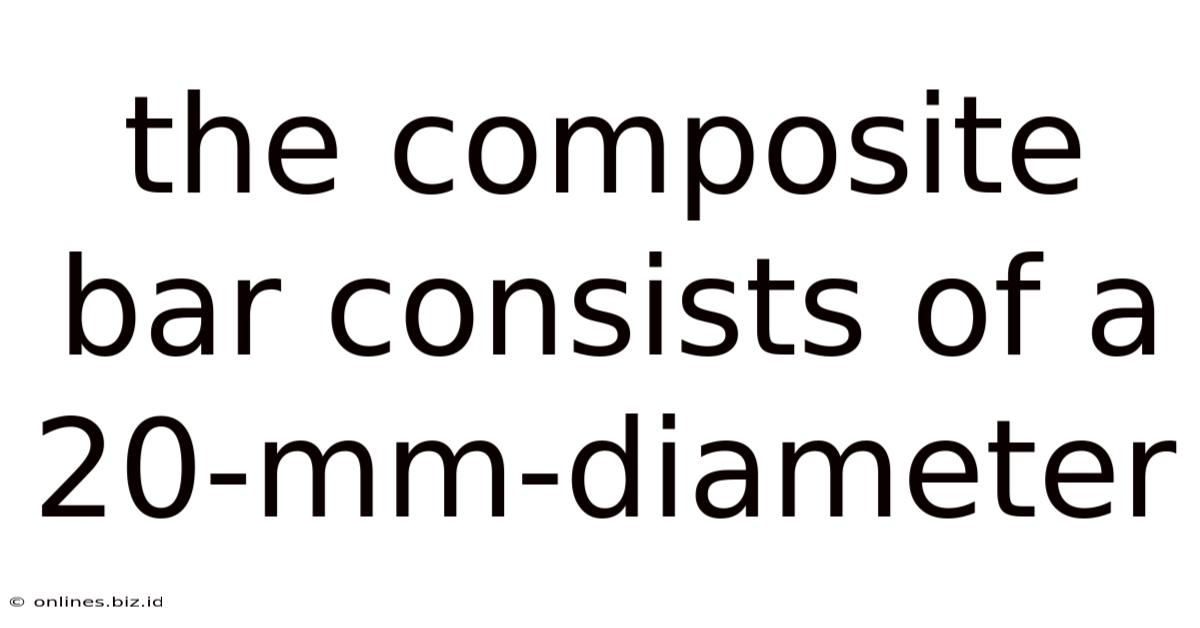
Table of Contents
Analyzing a 20-mm Diameter Composite Bar: Stress, Strain, and Material Properties
The analysis of composite materials is crucial in various engineering applications, from aerospace to civil engineering. Understanding the behavior of these materials under stress is paramount for designing safe and efficient structures. This article delves into the intricacies of analyzing a composite bar with a 20-mm diameter, exploring key concepts like stress, strain, material properties, and failure mechanisms. We'll also touch upon practical considerations and advanced analytical techniques.
Understanding Composite Materials
Before diving into the specifics of our 20-mm diameter bar, it's essential to establish a firm understanding of composite materials. These materials are formed by combining two or more constituent materials with significantly different properties. The resulting composite possesses properties superior to those of its individual components. Common examples include fiber-reinforced polymers (FRP), where strong fibers (e.g., carbon, glass, aramid) are embedded in a matrix material (e.g., epoxy resin). The fibers provide high strength and stiffness, while the matrix protects the fibers and transfers loads between them.
The properties of a composite material are highly dependent on:
-
Fiber type and orientation: Different fibers (carbon, glass, Kevlar) possess different strengths, stiffness, and failure modes. The orientation of the fibers relative to the applied load significantly influences the overall strength and stiffness of the composite.
-
Matrix material: The matrix material plays a crucial role in load transfer, protecting the fibers from environmental damage and distributing stress evenly. The properties of the matrix influence the toughness and durability of the composite.
-
Fiber volume fraction: The proportion of fibers to matrix material affects the overall properties of the composite. A higher fiber volume fraction generally leads to a stronger and stiffer composite.
Stress and Strain in the Composite Bar
When a load is applied to the 20-mm diameter composite bar, it experiences stress and strain. Stress is defined as the force applied per unit area, while strain represents the deformation of the material under load. These two quantities are related through the material's elastic modulus (Young's modulus).
Stress Calculation:
The stress (σ) in a cylindrical bar under axial loading is calculated using the following formula:
σ = F / A
where:
- F is the applied axial force.
- A is the cross-sectional area of the bar (πr², where r is the radius, which is 10mm in this case).
Strain Calculation:
The strain (ε) is calculated as the change in length (ΔL) divided by the original length (L):
ε = ΔL / L
The relationship between stress and strain is governed by Hooke's Law:
σ = Eε
where:
- E is Young's modulus (or modulus of elasticity) of the composite material. This is a crucial material property that dictates the stiffness of the composite. It's not a single value but depends on the fiber type, orientation, and volume fraction.
Material Properties of the Composite Bar
Determining the accurate material properties of the composite bar is crucial for accurate stress and strain calculations. These properties are typically obtained through experimental testing, such as tensile testing. Key material properties include:
-
Young's Modulus (E): Indicates the stiffness of the material. A higher E value implies a stiffer material.
-
Poisson's Ratio (ν): Represents the ratio of lateral strain to axial strain. It describes how much the material deforms in the transverse direction when subjected to axial loading.
-
Shear Modulus (G): Describes the material's resistance to shear deformation.
-
Ultimate Tensile Strength (UTS): The maximum stress the material can withstand before failure.
-
Yield Strength: The stress at which the material starts to deform plastically.
Failure Mechanisms in Composite Materials
Composite materials can fail through various mechanisms, including:
-
Fiber breakage: Individual fibers can break under excessive tensile stress.
-
Matrix cracking: Cracks can form in the matrix material, reducing the load-bearing capacity of the composite.
-
Fiber-matrix debonding: The interface between the fibers and the matrix can weaken, leading to debonding and reduced strength.
-
Buckling: Fibers or layers can buckle under compressive loads.
-
Shear failure: The composite can fail due to shear stresses, especially at the interfaces between layers.
Advanced Analysis Techniques
For more complex scenarios, advanced analysis techniques may be necessary:
-
Finite Element Analysis (FEA): FEA is a powerful computational technique used to model the behavior of complex structures under load. It allows for detailed stress and strain analysis, taking into account complex geometries and material properties.
-
Micromechanical Modeling: This approach focuses on the behavior of individual fibers and the matrix material at the microscopic level, providing insights into the overall macroscopic behavior of the composite.
Practical Considerations for the 20-mm Diameter Bar
The design and analysis of the 20-mm diameter composite bar require careful consideration of several practical factors:
-
Manufacturing process: The manufacturing process significantly impacts the final properties of the composite. Inconsistent manufacturing can lead to variations in material properties and strength.
-
Environmental factors: Temperature, humidity, and exposure to chemicals can affect the long-term performance of the composite.
-
Fatigue: Repeated loading and unloading can lead to fatigue failure, even at stresses below the yield strength.
-
Impact resistance: The composite's ability to withstand impact loads is crucial in many applications.
Conclusion
Analyzing a 20-mm diameter composite bar involves understanding the interplay of various factors, including material properties, stress, strain, and potential failure mechanisms. Accurate determination of material properties through experimentation or established literature is crucial for reliable analysis. For complex scenarios, advanced techniques like FEA and micromechanical modeling can provide more comprehensive insights. Finally, practical considerations like manufacturing processes and environmental factors must always be considered in the design and application of composite materials. This detailed analysis ensures the structural integrity and reliable performance of components fabricated from composite materials. The information provided here serves as a foundational understanding, and more specialized knowledge may be required for specific composite types and applications.
Latest Posts
Latest Posts
-
Identify The Most Likely Marketing Channel Structure For Fresh Oranges
May 10, 2025
-
The Padlike Menisci Of The Knee Joints Contain
May 10, 2025
-
Which Three Lines In The Poem Are Examples Of Alliteration
May 10, 2025
-
Which Aarp Entity Manages Provider Relationships And Performs Quality Control
May 10, 2025
-
The United States Is Not Truly Pluralistic Because
May 10, 2025
Related Post
Thank you for visiting our website which covers about The Composite Bar Consists Of A 20-mm-diameter . We hope the information provided has been useful to you. Feel free to contact us if you have any questions or need further assistance. See you next time and don't miss to bookmark.