The Control Devices Used In Pneumatics Are Called
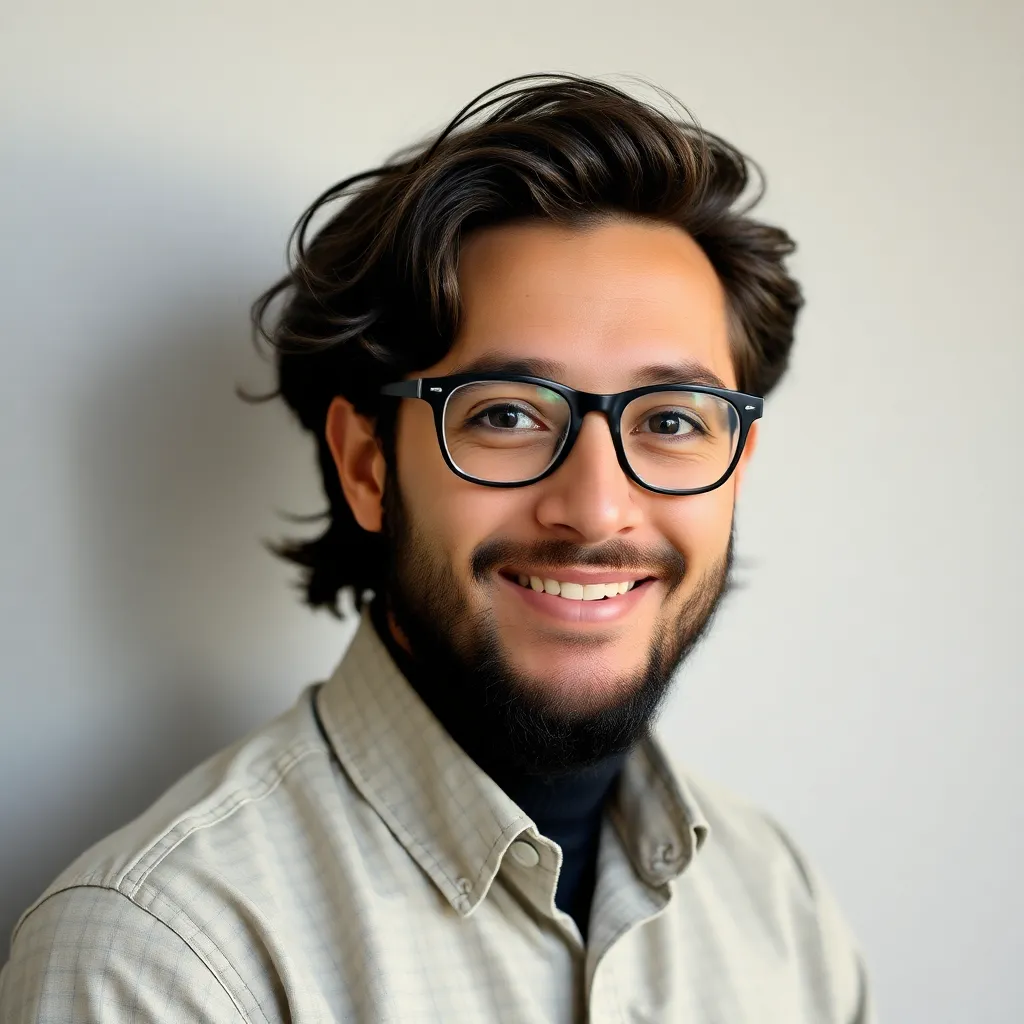
Onlines
Apr 28, 2025 · 7 min read
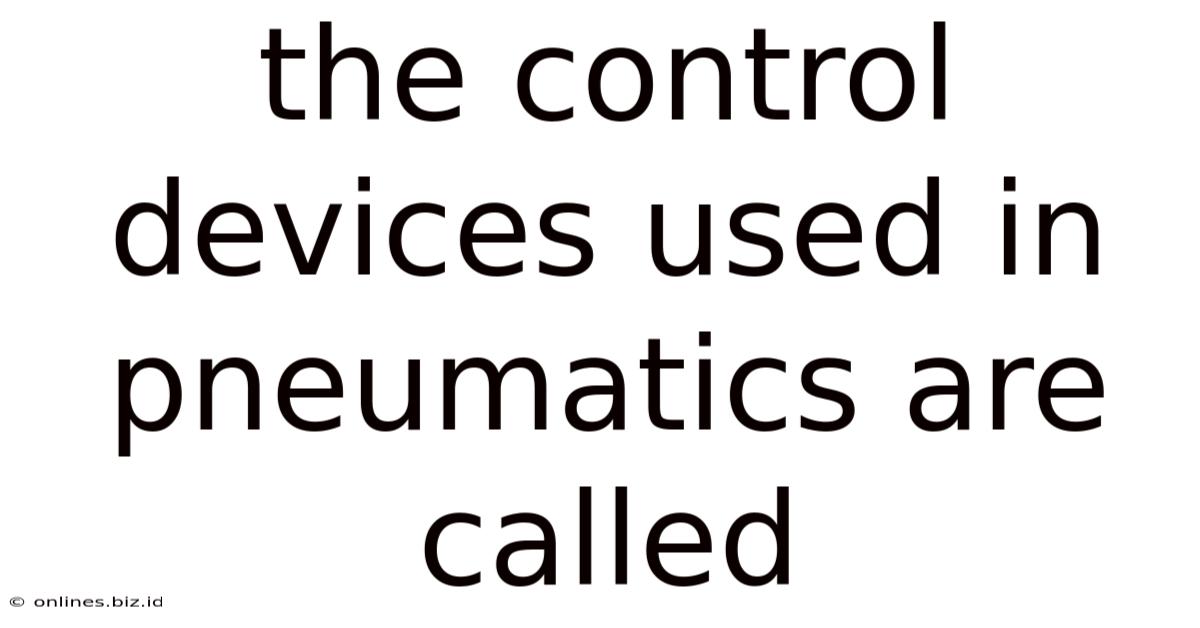
Table of Contents
- The Control Devices Used In Pneumatics Are Called
- Table of Contents
- The Control Devices Used in Pneumatics are Called Pneumatic Control Valves
- What are Pneumatic Control Valves?
- Types of Pneumatic Control Valves
- 1. Based on Function:
- 2. Based on Construction:
- 3. Based on Control Method:
- Selecting the Right Pneumatic Control Valve
- Advanced Pneumatic Control Concepts
- Applications of Pneumatic Control Valves
- Maintenance and Troubleshooting
- Future Trends in Pneumatic Control Valves
- Latest Posts
- Related Post
The Control Devices Used in Pneumatics are Called Pneumatic Control Valves
Pneumatics, the science and technology of controlling and transmitting power using compressed air, plays a crucial role in various industries. From automated manufacturing processes to medical equipment, pneumatic systems offer advantages like simplicity, cost-effectiveness, and safety. Understanding the components of these systems is vital for engineers, technicians, and anyone interested in the field. A core element of any pneumatic system is its control devices, which are primarily pneumatic control valves. This article delves deep into the world of pneumatic control valves, exploring their types, functions, and applications.
What are Pneumatic Control Valves?
Pneumatic control valves are the brains of a pneumatic system. They regulate the flow of compressed air, controlling the speed, direction, and pressure of actuators like cylinders and motors. These valves act as switches, modulating the air supply to precisely control the movement and force of pneumatic components. Their function is critical; without precise control, pneumatic systems would be unpredictable and unreliable. Think of them as the traffic controllers of your compressed air network, ensuring smooth and efficient operation.
Types of Pneumatic Control Valves
The world of pneumatic control valves is diverse, with numerous types categorized based on their function, construction, and control method. Some key classifications include:
1. Based on Function:
-
Directional Control Valves: These valves control the direction of airflow. They are arguably the most common type, directing air to extend or retract a pneumatic cylinder, for example. They come in various configurations, such as 2/2-way (two ports, two positions), 3/2-way, 4/2-way, and 5/2-way valves. The numbers indicate the number of ports and positions. A 3/2-way valve, for instance, has three ports and two positions: one for air flow and one for no air flow. 4/2-way valves are often used for double-acting cylinders, allowing air to enter and exit both sides.
-
Flow Control Valves: These valves regulate the flow rate of compressed air. They are crucial for controlling the speed of pneumatic actuators. Needle valves provide precise adjustments, while flow restrictors offer less precise but often more robust control. Proper flow control prevents jerky movements and protects delicate components from damage caused by rapid pressure changes.
-
Pressure Control Valves: These valves maintain a constant pressure within a pneumatic system or a portion of it. Pressure regulators reduce high-pressure supply air to a lower, controlled pressure. Pressure relief valves protect the system from overpressure by automatically venting excess air. Maintaining consistent pressure is key to consistent actuator performance.
-
Shut-off Valves: These valves simply stop or start the flow of air. They are often simpler in design than other valves and are used for isolation or emergency shutdowns. Ball valves, gate valves, and globe valves are common examples that might be adapted for pneumatic systems.
2. Based on Construction:
-
Poppet Valves: These use a poppet (a conical or disc-shaped plug) to control airflow. They're known for their robustness and are suitable for high-pressure applications. The simple design also makes them relatively inexpensive.
-
Spool Valves: These use a sliding spool to direct airflow. They offer a wider range of configurations and are often preferred for more complex applications requiring precise control. Spool valves can be designed for multiple functions within a single valve body.
-
Diaphragm Valves: These valves use a flexible diaphragm to control airflow. They're often used in applications requiring leak-tight sealing.
3. Based on Control Method:
-
Manually Operated Valves: These valves are controlled by a human operator using a lever, knob, or button. They are simple and inexpensive but are less suited for automated systems.
-
Pneumatically Operated Valves: These valves are controlled by compressed air. This allows for remote control and integration into automated systems. The control signal is usually a small amount of pressurized air acting on a piston or diaphragm within the valve.
-
Electrically Operated Valves: These valves are controlled by an electrical signal, often using a solenoid. Solenoids are electromagnets that activate a valve when energized. This type offers precise and responsive control, suitable for integration into complex automated systems.
Selecting the Right Pneumatic Control Valve
Choosing the correct pneumatic control valve depends on several factors:
-
Application: The specific requirements of the pneumatic system will dictate the type of valve needed. For example, a double-acting cylinder will need a directional control valve, while controlling the speed of a cylinder would necessitate a flow control valve.
-
Pressure and Flow Rate: The operating pressure and flow rate of the compressed air must be considered to ensure the valve can handle the demands of the application. Overloading a valve can lead to failure or inconsistent performance.
-
Environmental Conditions: The valve must be able to withstand the temperature, humidity, and other environmental factors present in its operating environment. Some valves are designed for harsh conditions, while others are suited for cleaner, more controlled environments.
-
Cost: The cost of the valve must be balanced against its performance and reliability. Simpler valves are generally less expensive, but more complex valves may offer features that justify the higher cost.
-
Maintenance: Valves require periodic maintenance to ensure proper functioning and a long service life. Selecting a valve with easy maintenance access and readily available replacement parts is often beneficial in the long run.
Advanced Pneumatic Control Concepts
Beyond the basic valve types, more sophisticated concepts are employed in advanced pneumatic systems:
-
Proportional Valves: These valves provide continuous control of airflow, offering a precise level of regulation unavailable with simple on/off valves. This allows for smooth, controlled movements of pneumatic actuators.
-
Servo Valves: These are high-performance valves designed for demanding applications requiring precise and rapid control of airflow. They often incorporate feedback mechanisms to ensure accuracy.
-
Pneumatic Logic Circuits: Complex pneumatic control sequences can be achieved through the use of pneumatic logic circuits, combining multiple valves and other components to create automated processes.
Applications of Pneumatic Control Valves
Pneumatic control valves are integral components in a wide range of industries and applications:
-
Manufacturing Automation: Robots, assembly lines, and other automated systems rely heavily on pneumatic control valves for precise and repeatable movements.
-
Packaging Machinery: Pneumatic valves control the operation of grippers, conveyors, and other components used in packaging lines.
-
Material Handling: Pneumatic systems with integrated control valves are used for lifting, transporting, and manipulating materials in various industries.
-
Robotics: The movements and actions of industrial robots often depend on sophisticated pneumatic control systems incorporating advanced valve technologies.
-
Medical Equipment: Many medical devices use pneumatic systems, and the precise control offered by pneumatic valves is essential for their safe and reliable operation. Examples include surgical tools and respiratory equipment.
-
Automotive Industry: Pneumatic components and control valves are found in various automotive applications, from braking systems (in older vehicles) to seat adjustments.
Maintenance and Troubleshooting
Regular maintenance is crucial for maintaining the efficiency and longevity of pneumatic control valves. This typically includes:
- Visual Inspection: Checking for leaks, damage, or signs of wear.
- Cleaning: Removing dust, debris, and contaminants.
- Lubrication: Applying appropriate lubricant to moving parts.
- Testing: Verifying the proper operation of the valves.
Troubleshooting pneumatic system problems often involves systematically checking the valves for proper functioning. Issues can range from simple leaks to more complex malfunctions requiring specialized expertise.
Future Trends in Pneumatic Control Valves
The field of pneumatics is continually evolving, with several key trends shaping the future of pneumatic control valves:
-
Increased Integration: Valves are being integrated more closely with other system components, allowing for more streamlined and efficient control systems.
-
Improved Efficiency: New designs and materials are leading to more energy-efficient valves, reducing operational costs.
-
Smart Valves: The incorporation of sensors and advanced control algorithms is creating "smart valves" capable of self-diagnosis and predictive maintenance.
-
Miniaturization: Smaller and more compact valves are being developed to meet the demands of increasingly compact systems.
In conclusion, pneumatic control valves are essential components of pneumatic systems, responsible for regulating the flow and pressure of compressed air. A wide variety of valves are available, each designed for specific applications and operating conditions. Understanding the different types of pneumatic control valves, their selection criteria, and maintenance requirements is essential for anyone working with pneumatic systems, ensuring safe, efficient, and reliable operation. The ongoing advancements in this technology promise even more sophisticated and efficient pneumatic control in the years to come.
Latest Posts
Related Post
Thank you for visiting our website which covers about The Control Devices Used In Pneumatics Are Called . We hope the information provided has been useful to you. Feel free to contact us if you have any questions or need further assistance. See you next time and don't miss to bookmark.