The Crimp Indent Is Properly Placed On The
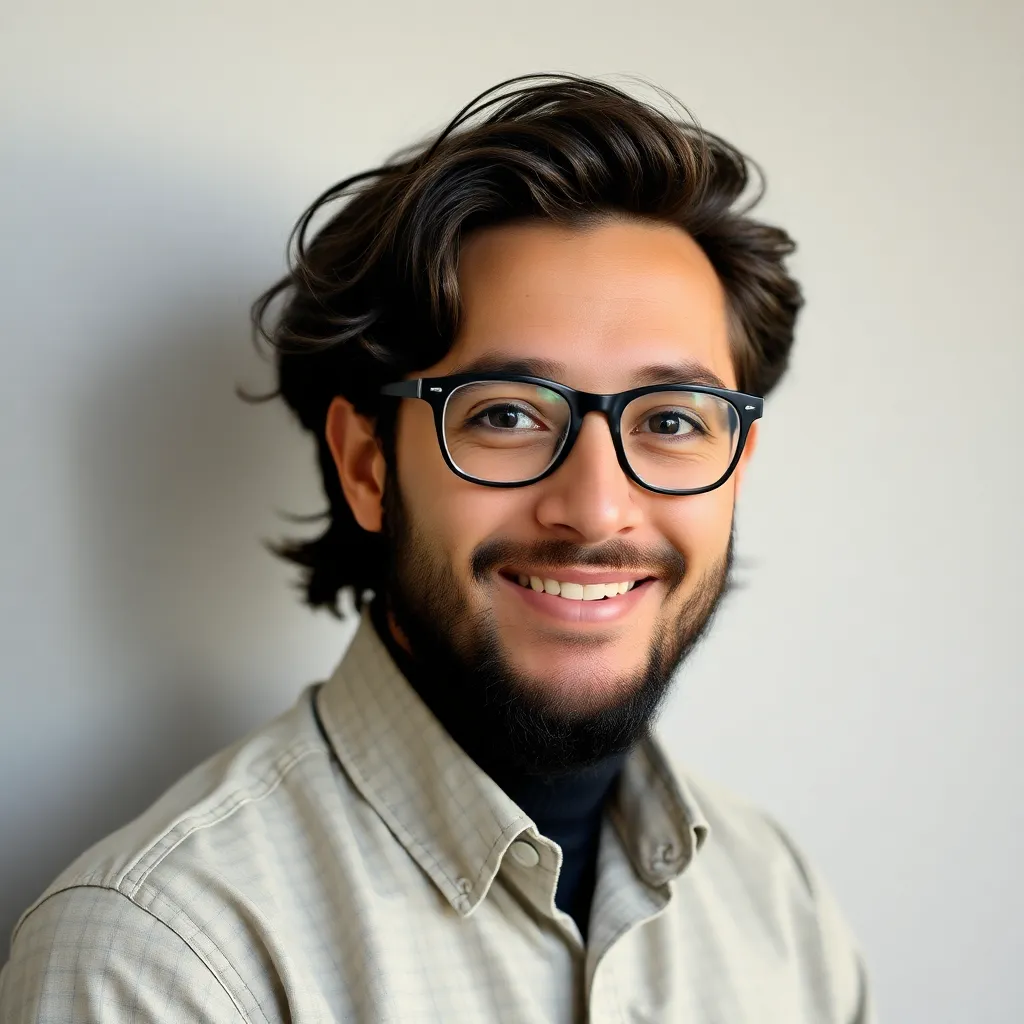
Onlines
Apr 17, 2025 · 5 min read
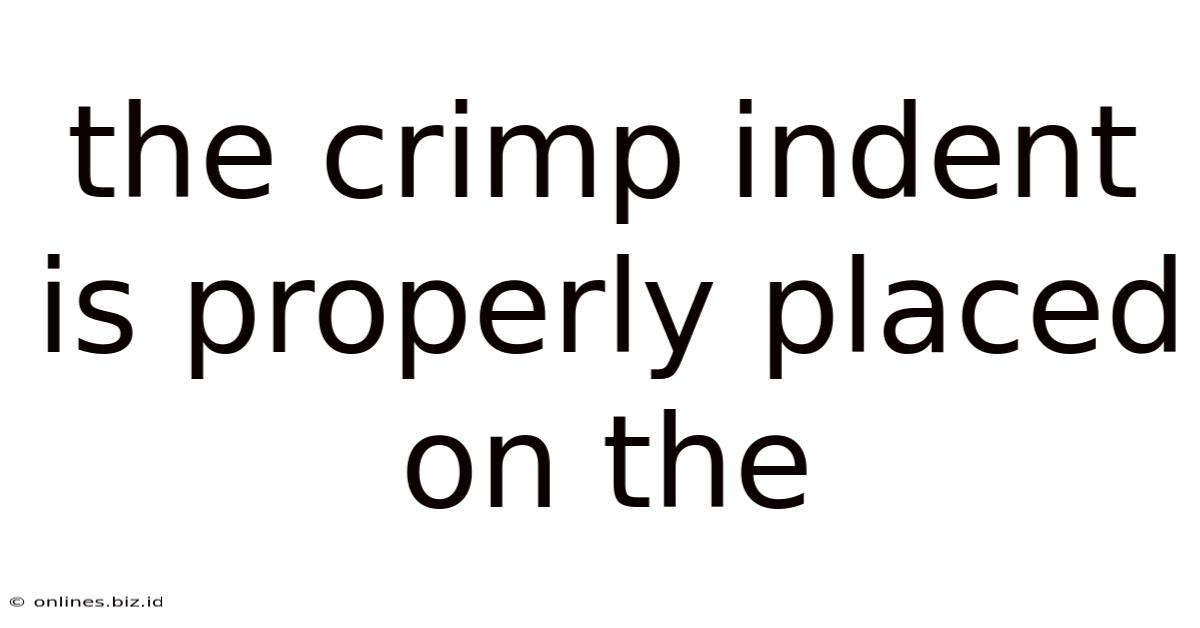
Table of Contents
- The Crimp Indent Is Properly Placed On The
- Table of Contents
- The Crimp Indent: Properly Placed for Optimal Performance
- Understanding Crimp Indents and Their Importance
- Factors Influencing Optimal Crimp Indent Placement
- 1. Crimp Tool Calibration and Selection:
- 2. Wire Type and Gauge:
- 3. Connector Terminal Design:
- 4. Crimping Technique:
- 5. Environmental Factors:
- Identifying and Troubleshooting Common Crimp Indent Issues
- 1. Misaligned Indent:
- 2. Partial Crimp:
- 3. Over-Crimp:
- 4. Cold Solder Joint (In Soldering Applications):
- Best Practices for Achieving Perfect Crimp Indents
- Advanced Considerations for Specialized Applications
- Conclusion: The Importance of Precision in Crimp Indent Placement
- Latest Posts
- Latest Posts
- Related Post
The Crimp Indent: Properly Placed for Optimal Performance
The seemingly small detail of a crimp indent's placement significantly impacts the reliability and performance of numerous applications, from electronics to aerospace engineering. Getting it right is crucial for ensuring a secure, consistent, and long-lasting connection. This comprehensive guide delves deep into the intricacies of crimp indent placement, exploring its importance, the factors influencing optimal positioning, common issues, and best practices for achieving perfect crimps every time.
Understanding Crimp Indents and Their Importance
A crimp indent is the physical deformation of a conductor (wire) within a connector terminal. This deformation creates a mechanical lock, securing the conductor and ensuring a low-resistance electrical connection. The precision of this indent is paramount; a misaligned or poorly formed crimp can lead to a range of problems, including:
- Intermittent Connections: A poorly positioned crimp might not make full contact with the connector's contact area, leading to unreliable signal transmission or power delivery. This is especially problematic in sensitive applications.
- Increased Resistance: Incomplete crimping results in a higher electrical resistance at the connection point, causing heat buildup, signal degradation, and potentially component failure.
- Signal Degradation: In high-frequency applications, a poorly placed crimp can introduce significant signal noise and attenuation, hindering performance.
- Mechanical Failure: An improperly crimped connection is prone to loosening or breakage under stress, vibration, or temperature fluctuations. This can lead to complete connection failure.
- Safety Hazards: In high-power applications, a faulty connection can cause overheating, short circuits, and even fires.
Therefore, precise placement of the crimp indent is non-negotiable for ensuring optimal performance, reliability, and safety.
Factors Influencing Optimal Crimp Indent Placement
Several factors contribute to the ideal placement of a crimp indent. Ignoring any of these can compromise the connection's integrity.
1. Crimp Tool Calibration and Selection:
The crimp tool is the primary determinant of crimp quality. A poorly calibrated or inappropriate tool can result in improperly formed and positioned indents. Regular calibration is vital to ensure consistent crimping force and die alignment. Selecting the correct tool for the specific connector and wire gauge is also crucial. Using the wrong tool can lead to damage to the wire or connector, or an ineffective crimp.
2. Wire Type and Gauge:
Different wire types (solid core, stranded, etc.) and gauges require different crimp techniques and tool settings. The material properties of the wire impact its deformation during crimping. Stranded wires, for example, require a different crimp profile than solid core wires to ensure all strands are properly compressed and secured. Failure to account for these differences can result in a loose or uneven crimp.
3. Connector Terminal Design:
The design of the connector terminal dictates the ideal location and shape of the crimp indent. Each terminal has a specific contact area designed to receive the crimped wire. The indent must fully engage this area to ensure a secure and low-resistance connection. Examining the terminal's specifications carefully is crucial.
4. Crimping Technique:
The operator's technique plays a vital role in crimp placement. Consistent hand pressure, proper tool alignment, and a smooth crimping action contribute to a well-placed indent. Inconsistent or forceful crimping can lead to misalignment or damage to the wire or connector.
5. Environmental Factors:
While less direct, environmental factors can affect crimp quality. Extreme temperatures or humidity can influence the wire's properties and the crimp's ability to maintain its integrity over time.
Identifying and Troubleshooting Common Crimp Indent Issues
Recognizing common problems with crimp indent placement is the first step towards improvement.
1. Misaligned Indent:
A misaligned indent indicates the wire was not properly positioned within the crimp tool's die before crimping. This results in an incomplete or uneven contact with the connector terminal.
Solution: Ensure proper wire insertion into the crimp tool, double-checking alignment before actuating the tool.
2. Partial Crimp:
A partial crimp indicates insufficient crimping force or improper tool calibration. Only part of the wire is properly compressed.
Solution: Check the crimp tool's calibration and ensure it's providing sufficient crimping force for the specific wire gauge.
3. Over-Crimp:
Excessive crimping force can damage the wire or connector, leading to a weak or broken connection.
Solution: Adjust the crimping force to the manufacturer's specifications.
4. Cold Solder Joint (In Soldering Applications):
If soldering is involved, a poorly formed crimp can hinder proper solder flow, leading to a "cold" solder joint.
Solution: Ensure a clean, properly placed crimp before soldering to facilitate proper solder wetting and a strong, reliable joint.
Best Practices for Achieving Perfect Crimp Indents
Implementing best practices minimizes errors and ensures consistently reliable crimps:
- Use the right tools: Employ crimp tools specifically designed for the wire gauge and connector type.
- Proper tool calibration: Regularly calibrate your crimp tools to maintain accuracy and consistency.
- Precise wire preparation: Ensure the wire ends are properly stripped and clean before crimping.
- Correct wire insertion: Carefully insert the wire into the crimp tool, ensuring proper alignment.
- Consistent crimping technique: Apply even pressure and a smooth crimping action.
- Visual inspection: After crimping, visually inspect the connection to confirm the indent is properly placed and the crimp is complete.
- Testing: Conduct electrical tests to verify a proper connection with low resistance.
- Documentation: Maintain detailed records of the crimping process, including the tools used, wire type, and crimping parameters.
Advanced Considerations for Specialized Applications
Specific applications often require more specialized considerations for crimp indent placement:
- High-frequency applications: In high-frequency circuits, the crimp indent's geometry and placement can impact signal integrity. Precision is paramount.
- High-power applications: High-current applications require crimps capable of withstanding significant heat generation. Special attention must be paid to ensuring a secure and low-resistance connection.
- Aerospace and military applications: These environments demand extremely reliable connections. Stringent quality control measures are essential.
Conclusion: The Importance of Precision in Crimp Indent Placement
The seemingly minor detail of crimp indent placement is critical to the overall reliability and performance of countless applications. A properly placed crimp ensures a secure, consistent, and long-lasting connection, minimizing the risk of failures and ensuring safety. By understanding the influencing factors, identifying common issues, and employing best practices, engineers and technicians can achieve consistently perfect crimps, leading to optimal performance and a high level of reliability. Ignoring these details can lead to costly failures and potentially dangerous situations. The emphasis on precision in crimp placement is not merely a best practice, but a critical aspect of ensuring quality and safety.
Latest Posts
Latest Posts
-
What Does Sagacity Mean In The Tell Tale Heart
May 09, 2025
-
Ap Chem Unit 9 Progress Check Mcq
May 09, 2025
-
A Network Administrator Enters The Service Password Encryption
May 09, 2025
-
The Five Step Marketing Research Approach Begins With
May 09, 2025
-
A Websites Analytics Report Shows That The Average
May 09, 2025
Related Post
Thank you for visiting our website which covers about The Crimp Indent Is Properly Placed On The . We hope the information provided has been useful to you. Feel free to contact us if you have any questions or need further assistance. See you next time and don't miss to bookmark.