The First Step In Making A Custom Tray Is To
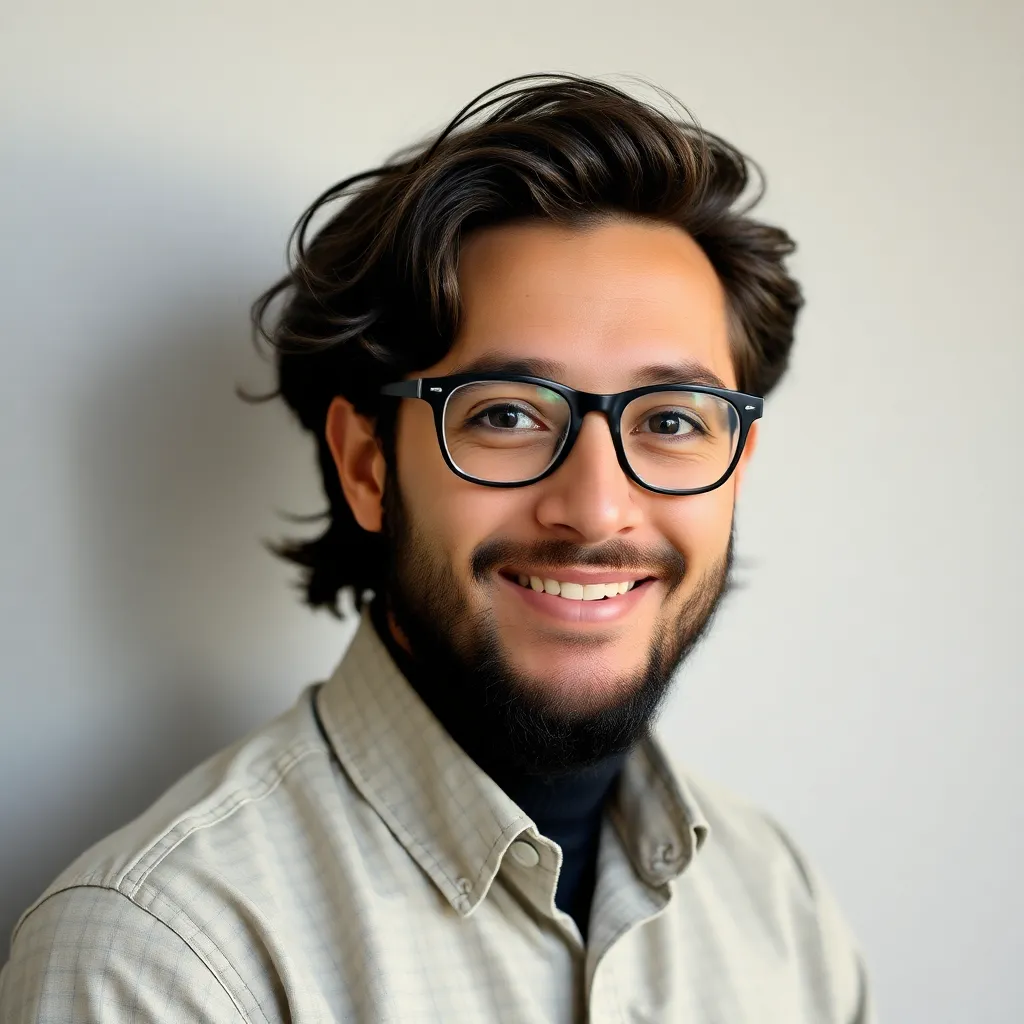
Onlines
Apr 24, 2025 · 5 min read

Table of Contents
The First Step in Making a Custom Tray: Planning and Design
Creating a custom tray is a rewarding project, blending artistry with practicality. Whether you're crafting a rustic wooden tray for a farmhouse aesthetic, a sleek modern resin tray, or an intricate mosaic tray, the very first step determines the success of your entire project: meticulous planning and design. This crucial initial phase sets the foundation for a stunning, functional, and unique piece. Ignoring this stage often leads to frustration, wasted materials, and a less-than-satisfactory final product.
Understanding Your Vision: Defining the Purpose and Style
Before even picking up a tool, clearly define the purpose and style of your custom tray. Ask yourself these questions:
1. What will the tray be used for?
This dictates size, material choices, and even design elements. A serving tray for appetizers will differ significantly from a catch-all tray for bedside essentials or a decorative tray for showcasing jewelry.
- Serving Tray: Consider larger dimensions, durable materials resistant to spills (like resin or lacquered wood), and perhaps even handles for easy carrying.
- Catch-All Tray: This might require compartments or dividers for organization. Size is determined by the intended items. Materials could range from simple wood to stylish metal.
- Decorative Tray: Focus on aesthetics. Intricate designs, unique materials (like mosaic tiles or repurposed metal), and a visually appealing finish are key.
2. What style are you aiming for?
Your personal style and the intended environment significantly influence the design. Do you prefer rustic charm, minimalist elegance, bohemian flair, or something else entirely?
- Rustic: Think natural wood, possibly distressed finishes, simple shapes, and earthy tones.
- Modern: Clean lines, geometric shapes, sleek materials like resin or polished metal are characteristic of this style.
- Bohemian: Embrace vibrant colors, eclectic materials, intricate patterns, and a free-flowing, less structured design.
- Farmhouse: Combine rustic elements with a touch of vintage charm.
3. Who is the intended user (or audience)?
This helps tailor the design to specific needs and preferences. A tray for a child might require sturdier construction and potentially more playful aesthetics, while a tray for an elderly person could benefit from ergonomic considerations like easy-grip handles.
Material Selection: Choosing the Right Foundation
The choice of material is paramount. Different materials offer unique properties, influencing the look, durability, and construction process. Consider the following:
1. Wood:
A classic and versatile choice, wood offers warmth, natural beauty, and a range of finishes. Consider:
- Types of Wood: Hardwoods like oak, maple, and walnut offer durability and a luxurious feel. Softer woods like pine are easier to work with but less durable.
- Wood Finishing: Consider staining, painting, varnishing, or leaving the wood in its natural state. The finish significantly impacts the final aesthetic and protection.
- Wood Preparation: Proper sanding and preparation are essential for a smooth, even finish.
2. Resin:
Resin allows for incredible creativity and customization. Its versatility enables embedding various materials for unique effects.
- Resin Types: Epoxy resin is popular for its clarity and durability. Polyester resin offers a more affordable option.
- Mold Making: Creating a suitable mold is crucial for resin trays. Silicone molds are reusable and easy to work with.
- Coloring and Adding Inclusions: Resin can be tinted with pigments and embellished with materials like glitter, dried flowers, or metallic flakes.
3. Metal:
Metal trays offer durability and a modern or industrial feel.
- Types of Metal: Aluminum, steel, and copper are common choices, each offering different properties and aesthetic qualities.
- Metalworking Techniques: Metal trays may require more advanced skills, including cutting, shaping, and welding.
- Finishing: Metal trays can be left with a raw finish, polished to a high shine, or coated with paint or powder coating.
4. Mosaic Tiles:
Mosaic tiles offer limitless design possibilities, allowing you to create intricate patterns and vibrant colors.
- Tile Types: Ceramic, glass, and even repurposed materials can be used to create a unique mosaic tray.
- Adhesive: A strong adhesive is crucial for securely attaching the tiles.
- Grouting: Grouting fills the spaces between tiles, creating a finished, water-resistant surface.
Designing Your Tray: Dimensions, Shape, and Details
Once you've chosen your materials and style, it's time to finalize the design:
1. Dimensions:
Determine the length, width, and depth of your tray. Consider its intended use and the space it will occupy. Sketch different sizes to visualize the proportions.
2. Shape:
The shape significantly impacts the overall aesthetic. Common shapes include rectangular, square, round, oval, and even freeform designs.
3. Handles (if applicable):
If your tray requires handles, consider their style, material, and attachment method. They should be comfortable and secure.
4. Compartments or Dividers (if applicable):
For catch-all trays, consider adding compartments or dividers to improve organization.
5. Detailed Sketch or Digital Design:
Create a detailed sketch or use digital design software to visualize your tray. This helps refine the design, identify potential problems, and accurately measure materials.
Gathering Your Supplies and Tools: Preparing for Construction
With your design finalized, gather all necessary materials and tools. This prevents interruptions during the construction process. The specific tools and materials will depend on your chosen material and design, but generally include:
- Measuring Tools: Ruler, tape measure, square
- Cutting Tools: Saw (for wood), metal shears (for metal), tile cutter (for mosaic tiles)
- Sanding Tools: Sandpaper, sanding block
- Adhesives: Wood glue, resin, tile adhesive
- Finishing Supplies: Paint, stain, varnish, sealant, grout
- Protective Gear: Safety glasses, gloves, dust mask
Beyond the First Step: A Roadmap to Success
While planning and design are paramount, they're just the beginning. Successfully completing your custom tray requires careful execution of each subsequent step. This includes:
- Precise Cutting and Shaping: Accuracy is vital to ensure all components fit together perfectly.
- Proper Assembly: Follow your design plan meticulously, ensuring strong and secure joints.
- Meticulous Finishing: A well-executed finish enhances the beauty and durability of your tray.
- Quality Control: Inspect your work at each stage to identify and correct any flaws.
Creating a custom tray is a journey, not a race. By meticulously focusing on the first step – planning and design – you set yourself up for a successful and fulfilling project, resulting in a unique, functional, and beautiful addition to your home or a thoughtful, personalized gift. Remember to embrace the process, enjoy the creativity, and take pride in your handcrafted creation.
Latest Posts
Latest Posts
-
Post Test Molecular Level Forces And Solutions
Apr 24, 2025
-
The Io Should Evaluate Or Be Involved In Evaluating
Apr 24, 2025
-
Translate The Medical Term Eupepsia As Literally As Possible
Apr 24, 2025
-
Marketing Managers Need To Pay Attention To Culture Because
Apr 24, 2025
-
If A School Official With Authority Has Knowledge
Apr 24, 2025
Related Post
Thank you for visiting our website which covers about The First Step In Making A Custom Tray Is To . We hope the information provided has been useful to you. Feel free to contact us if you have any questions or need further assistance. See you next time and don't miss to bookmark.