The Formula To Compute The Budgeted Direct Labor Cost Is
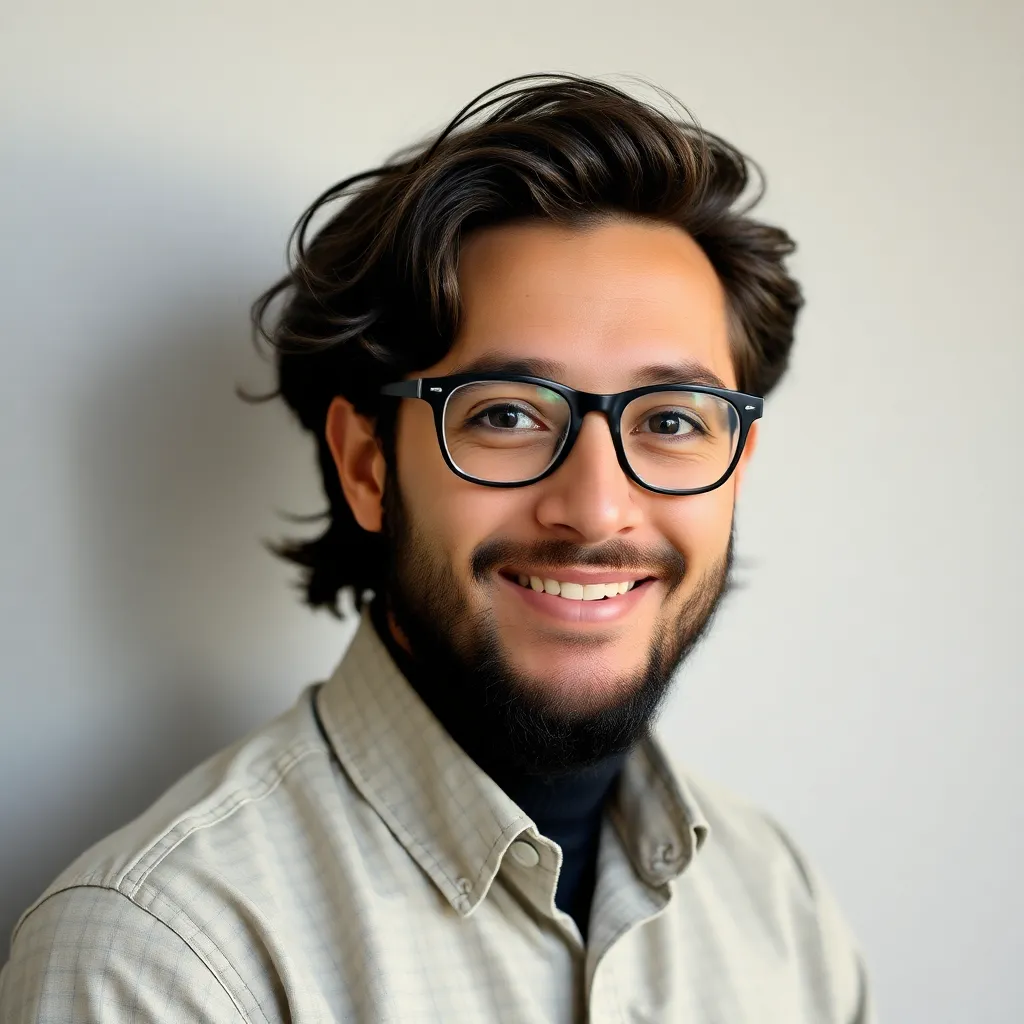
Onlines
Apr 23, 2025 · 5 min read

Table of Contents
The Formula to Compute the Budgeted Direct Labor Cost: A Comprehensive Guide
Budgeting is a crucial aspect of effective financial management for any organization. Accurate budgeting allows businesses to plan for future expenses, allocate resources efficiently, and make informed decisions. One of the key components of any budget is the budgeted direct labor cost. Understanding how to compute this accurately is vital for maintaining a healthy financial outlook. This comprehensive guide will delve into the formula, its components, and the nuances involved in calculating budgeted direct labor cost.
Understanding Direct Labor Cost
Before diving into the formula, let's define what direct labor cost actually is. Direct labor cost represents the total cost of labor directly involved in producing goods or services. It's crucial to differentiate between direct and indirect labor. Direct labor includes the wages, salaries, and benefits of employees who physically work on the product or service. This contrasts with indirect labor, which encompasses the wages of employees who support the production process but don't directly work on the product itself (e.g., supervisors, maintenance staff).
Examples of direct labor costs include:
- Wages paid to assembly line workers.
- Salaries of production supervisors directly overseeing production.
- Benefits (health insurance, retirement contributions) paid for direct labor employees.
Examples of indirect labor costs include:
- Salaries of factory managers.
- Wages of janitorial staff working in the factory.
- Compensation of human resources personnel supporting the production team.
The Formula: Deconstructing the Budgeted Direct Labor Cost Calculation
The core formula for calculating the budgeted direct labor cost is relatively straightforward:
Budgeted Direct Labor Cost = (Number of Units to be Produced) x (Direct Labor Hours per Unit) x (Direct Labor Cost per Hour)
Let's break down each component of this formula:
1. Number of Units to be Produced: The Foundation of Your Budget
This is the projected number of units your organization plans to produce during the budget period (e.g., a month, quarter, or year). This number is derived from sales forecasts, market analysis, and historical production data. Accuracy in this prediction is crucial, as it forms the base for the entire calculation. Underestimating production can lead to cost underestimation and potential production bottlenecks, while overestimating can result in unnecessary labor costs. Therefore, rigorous forecasting methods are recommended.
2. Direct Labor Hours per Unit: Efficiency and Productivity
This represents the estimated number of labor hours required to produce one unit of your product or service. This value depends heavily on your production process, employee skill levels, and available technology. It requires a careful analysis of the production process, including time studies or historical data on production time. Improving efficiency by streamlining the production process can significantly reduce this number and, consequently, the overall budgeted direct labor cost.
3. Direct Labor Cost per Hour: The Total Employee Cost
This is the total cost per hour of employing a direct labor worker. This figure isn't solely the hourly wage; it incorporates all labor-related costs:
- Hourly Wage/Salary: The base pay rate of the employee.
- Overtime Premiums: Additional pay for hours worked beyond regular hours. Budgeting should include projections for potential overtime based on production demands.
- Employee Benefits: Costs associated with employee benefits like health insurance, retirement contributions, paid time off, and other fringe benefits. These are often expressed as a percentage of the employee's base pay.
Accurate determination of this cost is crucial. Failing to factor in all components can lead to significant underestimation of the total direct labor cost.
Beyond the Basic Formula: Adding Nuances for Accuracy
While the basic formula provides a foundation, several factors can influence the accuracy and completeness of your budgeted direct labor cost. Consider incorporating these elements for a more comprehensive and reliable budget:
1. Labor Rate Variations: Accounting for Different Skill Levels
If your production process involves workers with varying skill levels and, therefore, different pay rates, you'll need a more granular approach. Break down the labor hours per unit by skill level, assigning the corresponding labor cost per hour for each skill level. This will provide a more realistic calculation.
2. Projected Changes in Labor Rates: Anticipating Wage Increases
Consider anticipated changes in labor rates due to annual raises, collective bargaining agreements, or market adjustments. Incorporate these projected changes into your calculation to accurately reflect future labor costs.
3. Learning Curve Effect: Improving Efficiency Over Time
The efficiency of workers often improves with experience. This learning curve effect means that as workers become more proficient, the labor hours per unit may decrease over time. This can be factored into the budget by adjusting the direct labor hours per unit progressively during the budget period. This is especially relevant for new product introductions or significant process changes.
4. Downtime and Inefficiency: Accounting for Unexpected Delays
Incorporate potential for downtime due to equipment malfunctions, material shortages, or other unexpected delays. A contingency buffer should be added to the budget to account for such unforeseen events. This buffer could be a percentage added to the total direct labor cost.
5. Seasonal Variations: Fluctuations in Production
If your production fluctuates seasonally, adapt your budget to reflect these changes. Different periods might require different numbers of workers, leading to variations in the direct labor cost. A segmented approach, budgeting for each season individually, is often necessary.
Example Calculation
Let's illustrate the formula with a hypothetical example. Suppose a company plans to produce 10,000 units of a product. Each unit requires 2 direct labor hours to produce, and the direct labor cost per hour is $25 (including wages and benefits).
Budgeted Direct Labor Cost = (10,000 units) x (2 hours/unit) x ($25/hour) = $500,000
This example shows a straightforward calculation. However, in reality, the process is often more complex due to the factors discussed above, requiring a more detailed breakdown and refined estimations.
Conclusion: The Importance of Accurate Budgeting
Accurate budgeting of direct labor costs is vital for successful financial management. While the core formula is simple, achieving accurate results requires a comprehensive understanding of all contributing factors, including labor rates, production efficiency, and potential disruptions. By incorporating these nuances and utilizing appropriate forecasting techniques, businesses can create a robust budget that provides a realistic picture of their future expenses and allows for informed decision-making. Regular monitoring and adjustments to the budget are also crucial to ensure it remains relevant and aligned with actual performance. A well-planned direct labor budget is a fundamental building block for a healthy and thriving business.
Latest Posts
Latest Posts
-
All Of The Following Are True About Prepaid Cards Except
Apr 23, 2025
-
In Relation To Fraud Detection The Acronym Scam Stands For
Apr 23, 2025
-
Which Of The Following About Using Outside Information Is False
Apr 23, 2025
-
The Communication Related Activity Organizations Role Is To
Apr 23, 2025
-
When Counting A Residents Pulse The Nurse Aide Should
Apr 23, 2025
Related Post
Thank you for visiting our website which covers about The Formula To Compute The Budgeted Direct Labor Cost Is . We hope the information provided has been useful to you. Feel free to contact us if you have any questions or need further assistance. See you next time and don't miss to bookmark.