The I Beam Wooden Spar Is Routed To
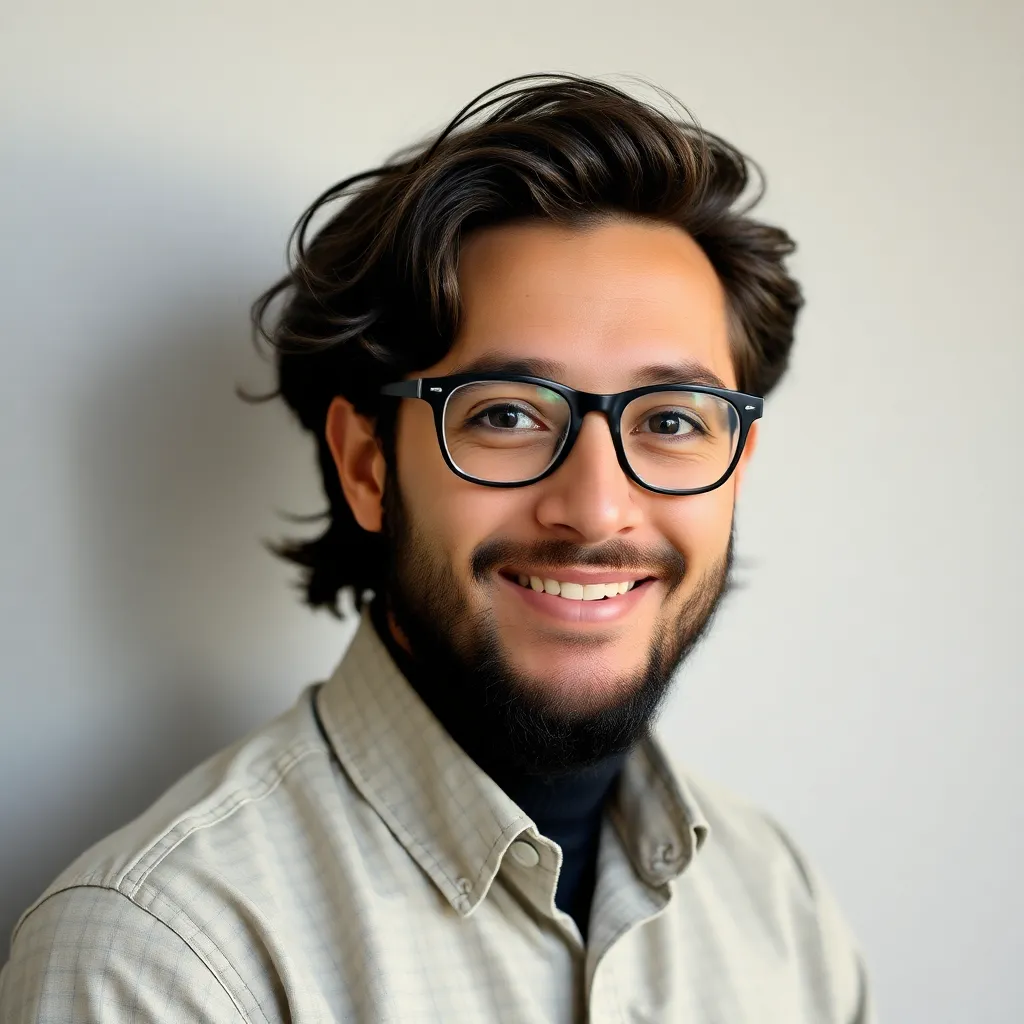
Onlines
May 12, 2025 · 6 min read
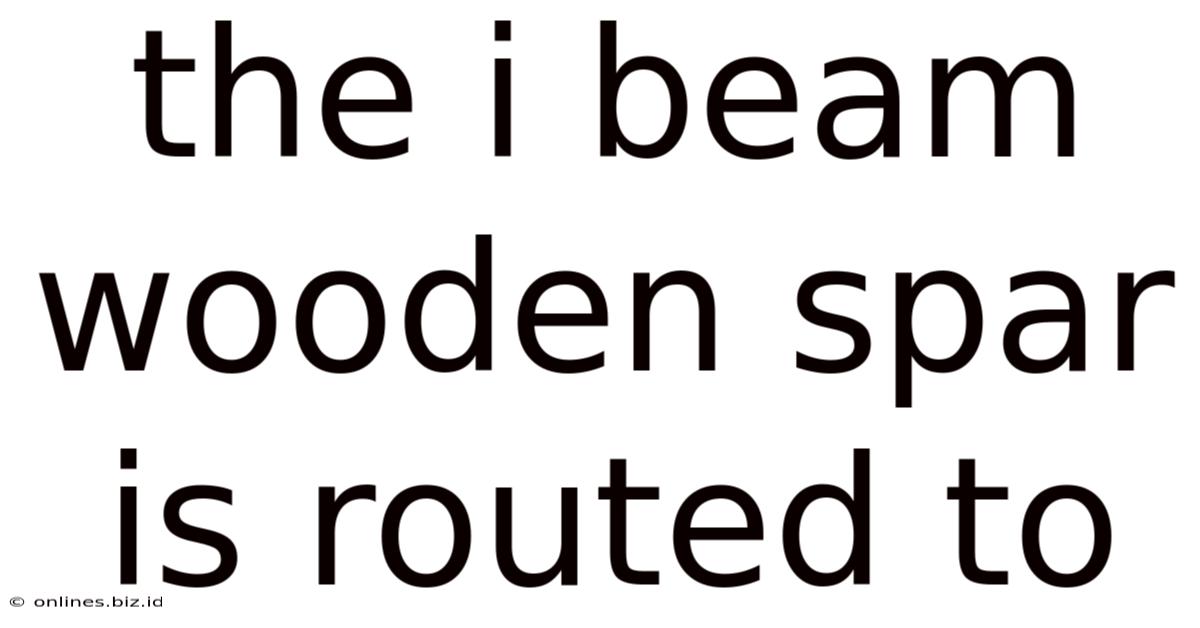
Table of Contents
The I-Beam Wooden Spar: Routing Techniques and Applications
The I-beam, a ubiquitous structural element in steel construction, finds a fascinating parallel in woodworking with the creation of I-beam wooden spars. These aren't simply aesthetically pleasing; they represent a significant advancement in lightweight yet strong structural components for various applications. This article dives deep into the routing techniques employed to craft these spars, exploring the intricacies of the process, the tools involved, and the diverse applications where their unique properties shine.
Understanding the I-Beam Wooden Spar
Before delving into the routing process, it's crucial to understand what constitutes an I-beam wooden spar. Unlike a solid, rectangular piece of wood, an I-beam spar consists of three distinct parts:
- A web: This is the central, vertical piece of the spar, typically thinner than the flanges. It provides the primary vertical strength and stiffness.
- Two flanges: These are the horizontal pieces that run along the top and bottom of the web. They are typically thicker than the web and contribute significantly to the spar's overall bending strength.
The I-beam design maximizes strength-to-weight ratio. By strategically distributing the wood mass in the flanges, the spar can withstand significant bending loads while minimizing weight. This makes it ideal for applications where lightness and strength are paramount.
Routing Techniques for I-Beam Wooden Spars
Creating an I-beam wooden spar requires precision and the right tools. While various methods exist, routing stands out as the most effective technique for achieving clean, accurate cuts and a high-quality finish. Several techniques fall under the umbrella of routing I-beam spars:
1. Using a Router Table with a Straight Bit
This method is best suited for producing multiple identical spars. The router table provides a stable and controlled environment for consistent cuts. The process involves:
- Preparing the Wood: Selecting appropriately sized and dried lumber is crucial. The wood species should be chosen based on the intended application, considering factors like strength, weight, and durability.
- Setting up the Router Table: A fence is essential for maintaining the consistent width of the web and flanges. The height of the bit must be precisely adjusted to achieve the desired thickness of each component. Safety precautions, including using a push stick and dust collection system, are paramount.
- Routing the Web: The first step typically involves routing the web to its final thickness. This is accomplished by carefully feeding the wood across the router bit, maintaining consistent pressure and speed.
- Routing the Flanges: After the web is complete, the flanges are routed. This might involve multiple passes to achieve the desired thickness and profile. Again, precise adjustment of the fence and bit height is critical.
This method allows for high-volume production of identical I-beam spars with remarkable accuracy and speed.
2. Using a Handheld Router with Jigs and Templates
For smaller projects or when producing a limited number of spars with varying dimensions, a handheld router with jigs and templates offers a flexible alternative. This method requires greater skill and precision but offers greater flexibility.
- Creating Templates: Accurate templates are crucial for this method. These can be made from sturdy materials like plywood or acrylic. The templates should precisely define the dimensions of the web and flanges.
- Using Jigs: Jigs provide a stable guide for the router, ensuring consistent depth and alignment of the cuts. Simple jigs can be constructed from scrap wood, while more complex jigs may require precise machining.
- Routing the Spar: The router is guided along the template and jig, carefully removing the excess wood to create the I-beam shape. Multiple passes are usually required to achieve the final dimensions.
This method is more time-consuming but highly adaptable to individual needs and allows for the creation of custom-sized I-beam spars.
3. CNC Routing for High-Precision and Complex Designs
For large-scale production or the creation of intricately designed I-beam spars with complex curves or profiles, CNC routing is the optimal solution. CNC routers offer unparalleled precision, repeatability, and speed.
- Designing the Spar: The spar design is created using CAD software, defining the exact dimensions and profiles of the web and flanges.
- Programming the CNC Machine: The CAD design is translated into a CNC program that instructs the machine on how to execute the cuts.
- Routing the Spar: The CNC machine automatically routes the spar according to the programmed instructions, achieving a high level of accuracy and consistency.
CNC routing allows for mass production of highly intricate and precise I-beam spars, surpassing the capabilities of manual methods.
Tool Selection and Considerations
Regardless of the routing technique employed, the choice of tools significantly impacts the outcome. Here's a breakdown of essential tools:
- Routers: Both router tables and handheld routers are suitable, depending on the scale and complexity of the project. Choosing a router with sufficient power and speed is crucial for efficient and clean cuts.
- Bits: Straight bits are essential for creating the straight cuts required for the web and flanges. The bit diameter should be carefully chosen to match the desired dimensions of the spar.
- Jigs and Templates: These are critical for handheld routing, ensuring accurate and consistent results. They can be custom-made or purchased commercially.
- Clamps: Secure clamping is essential to hold the wood firmly in place during routing, preventing movement and ensuring safety.
- Safety Gear: Eye protection, hearing protection, and dust masks are paramount to protect the user from flying debris and dust.
Applications of I-Beam Wooden Spars
The unique properties of I-beam wooden spars—lightweight yet strong—open up a range of exciting applications:
- Model Aircraft: I-beam spars are ideal for model aircraft wings, providing structural integrity while minimizing weight for improved flight performance.
- Lightweight Furniture: They can be used in furniture construction, particularly where strength and a minimalist aesthetic are desired.
- Musical Instruments: Certain stringed instruments may utilize I-beam spars for their strength and resonance properties.
- Architectural Models: Architects and designers often employ I-beam spars in creating scale models, providing structural support while maintaining a lightweight and realistic representation.
- Boat Building: In smaller boat construction, I-beam spars can offer a lightweight yet robust alternative to traditional designs.
- Custom Signage: The versatility of the I-beam design allows for its use in constructing unique and eye-catching signage.
- Robotics and Automation: The lightweight and robust nature makes them suitable for robotic arm construction or other lightweight automation components.
Finishing and Refinement
After routing, the I-beam spar will require further finishing to achieve the desired aesthetic and protect the wood. This might include:
- Sanding: Smooth out any rough edges or imperfections left by the routing process.
- Finishing: Applying a suitable finish, such as varnish, paint, or oil, will protect the wood from moisture and wear, enhancing its durability and appearance.
Conclusion
Routing I-beam wooden spars is a rewarding process that combines precision woodworking techniques with the principles of structural engineering. By carefully selecting the right routing method, tools, and materials, you can create strong, lightweight, and aesthetically pleasing components suitable for a wide array of applications. The versatility of this design coupled with the accuracy achievable through modern routing techniques ensures that the I-beam wooden spar will continue to find its place in diverse creative and engineering projects. The careful consideration of safety measures and the appropriate application of finishing techniques contribute to the overall success and longevity of these unique structural elements. The strength-to-weight ratio and the resulting flexibility in design make the I-beam wooden spar a valuable asset for many applications, pushing the boundaries of what's possible with wood construction.
Latest Posts
Latest Posts
-
12 7 4 Lab Identify Ipv6 Addresses
May 12, 2025
-
Cooperative Advertising Refers To A Practice That Consists Of
May 12, 2025
-
Enzyme Rich Pancreatic Juice Contains All The Following Except
May 12, 2025
-
Which Of The Following Demonstrates Correct Punctuation Of A Quotation
May 12, 2025
-
How Are Modern Day Shona Similar To Their Ancestors
May 12, 2025
Related Post
Thank you for visiting our website which covers about The I Beam Wooden Spar Is Routed To . We hope the information provided has been useful to you. Feel free to contact us if you have any questions or need further assistance. See you next time and don't miss to bookmark.