The Installation Of Production Improvement Option D
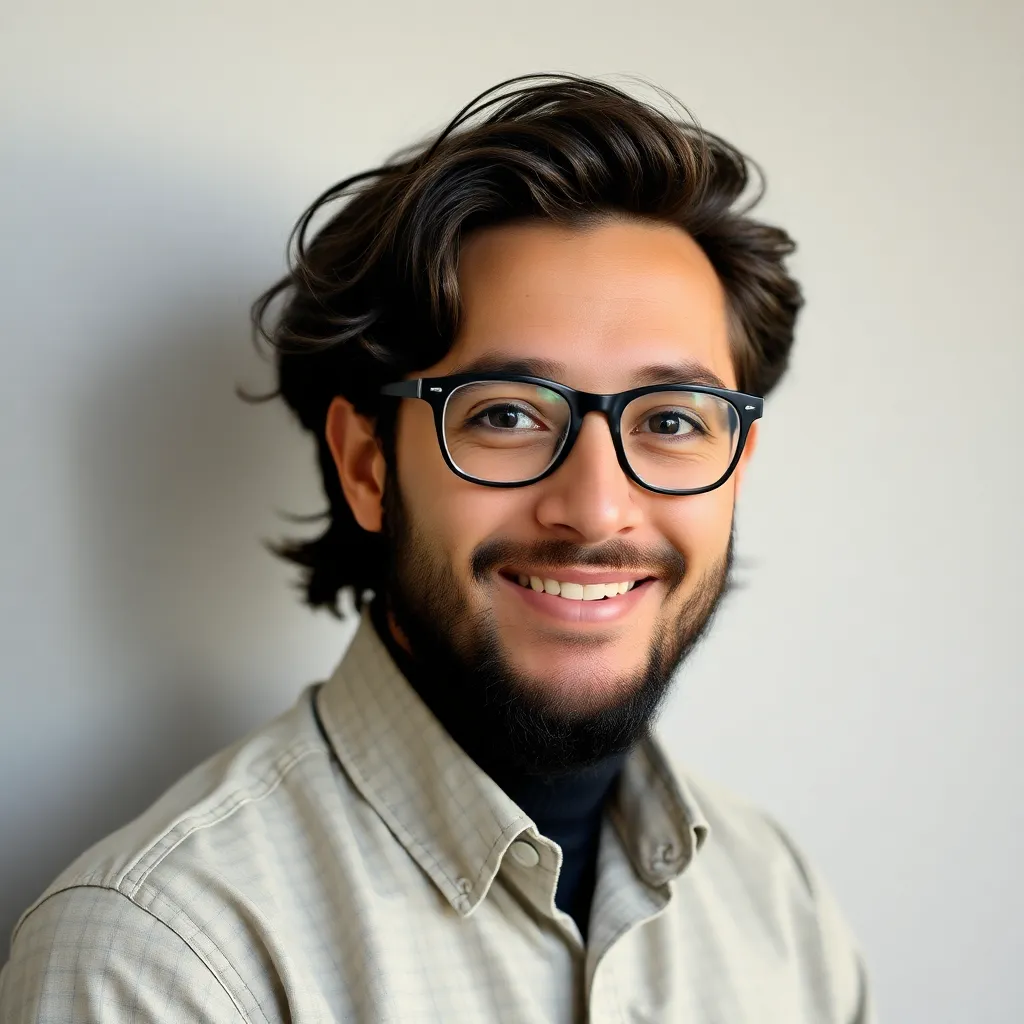
Onlines
Mar 28, 2025 · 6 min read
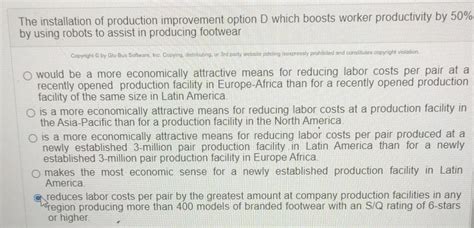
Table of Contents
The Installation of Production Improvement Option D: A Comprehensive Guide
Production Improvement Option D (PIO-D) represents a significant upgrade for many manufacturing processes. This detailed guide will walk you through the entire installation process, from initial planning to final testing and validation. We'll cover crucial aspects, including pre-installation checks, hardware and software requirements, the installation steps themselves, troubleshooting common issues, and post-installation verification. Understanding these steps will ensure a smooth and efficient implementation, maximizing the benefits of PIO-D for your operations.
I. Pre-Installation Planning: Laying the Foundation for Success
Before even considering the physical installation of PIO-D, thorough planning is paramount. This phase lays the groundwork for a seamless transition and minimizes potential disruptions to your production line.
A. Needs Assessment and System Requirements:
- Define Objectives: Clearly articulate what you aim to achieve with PIO-D. This might include increased throughput, reduced downtime, improved product quality, or lower operational costs. Quantifiable goals will help measure the success of the installation.
- Hardware Compatibility: Verify that your existing hardware infrastructure meets the minimum requirements specified in the PIO-D documentation. This includes servers, workstations, network equipment, and any specialized peripherals. Outdated hardware might necessitate upgrades before installation.
- Software Compatibility: Ensure compatibility with your current operating systems, databases, and other software applications. Conflicts can lead to unforeseen problems and delays. Check for any required software updates or patches.
- Training Requirements: Identify the personnel who will be operating and maintaining PIO-D. Plan for comprehensive training sessions to ensure they possess the necessary skills and knowledge.
B. Resource Allocation and Scheduling:
- Personnel: Assign dedicated personnel to oversee the installation process. This team should include IT specialists, production engineers, and representatives from affected departments.
- Time Allocation: Develop a realistic timeline for the entire installation project, factoring in potential delays and unforeseen circumstances. A well-defined schedule keeps the project on track.
- Budgeting: Allocate sufficient resources to cover the costs associated with installation, including hardware, software, training, and potential downtime. Accurate budgeting prevents cost overruns.
C. Risk Assessment and Mitigation:
- Potential Risks: Identify potential risks associated with the installation, such as hardware failures, software glitches, or unforeseen compatibility issues.
- Mitigation Strategies: Develop strategies to mitigate these risks. This might involve creating backups, implementing fail-safe mechanisms, or having contingency plans in place.
II. Hardware and Software Installation: The Practical Steps
Once the pre-installation planning is complete, you can proceed with the actual installation of PIO-D. This phase involves both hardware and software components, each requiring careful attention to detail.
A. Hardware Installation:
- Preparation: Power down all relevant equipment and disconnect any unnecessary devices. Ensure a clean and organized workspace.
- Physical Installation: Install the PIO-D hardware components according to the manufacturer's instructions. This might involve installing new servers, network devices, or specialized peripherals. Proper grounding and cabling are crucial.
- Connectivity: Connect the hardware components to the existing network infrastructure, ensuring proper network configuration. This often involves assigning IP addresses, configuring network settings, and testing connectivity.
B. Software Installation:
- Software Deployment: Install the PIO-D software on the designated servers and workstations. Follow the manufacturer's instructions carefully, ensuring the correct installation options are selected.
- Database Configuration: Configure the database system to interact correctly with the PIO-D software. This might involve creating new databases, tables, and users, and ensuring data integrity.
- Configuration Files: Configure any necessary configuration files to match your specific environment and requirements. Incorrect configuration can lead to functionality issues.
- Testing: After installation, thoroughly test the software to ensure all components are functioning as expected. This includes running various test cases and checking for any errors.
III. Integration and Testing: Ensuring Seamless Functionality
This crucial phase focuses on integrating PIO-D with your existing systems and rigorously testing its functionality.
A. System Integration:
- Data Integration: Integrate the PIO-D system with your existing databases and other software applications to ensure seamless data exchange.
- API Integration: If required, integrate PIO-D with external systems via Application Programming Interfaces (APIs).
- Workflow Integration: Integrate PIO-D into your existing production workflows to ensure smooth operation.
B. Functional Testing:
- Unit Testing: Test individual components of the PIO-D system to ensure they are functioning as expected.
- Integration Testing: Test the interaction between different components of the system.
- System Testing: Test the entire system as a whole to ensure it meets the specified requirements.
- User Acceptance Testing (UAT): Involve end-users in testing the system to ensure it meets their needs and expectations.
C. Performance Testing:
- Load Testing: Test the system under various load conditions to determine its performance characteristics.
- Stress Testing: Test the system under extreme conditions to identify its breaking point.
- Performance Tuning: Optimize the system’s performance by addressing any bottlenecks or inefficiencies.
IV. Post-Installation Procedures and Maintenance: Long-Term Success
Once the installation and testing are complete, focus shifts to post-installation procedures and ongoing maintenance to ensure the long-term success of PIO-D.
A. Documentation:
- Detailed Documentation: Create comprehensive documentation detailing the installation process, configuration settings, troubleshooting procedures, and best practices.
- User Manuals: Develop clear and concise user manuals for end-users to guide them on using the system effectively.
B. Training and Support:
- Ongoing Training: Provide ongoing training to users and administrators to ensure they are up-to-date on the latest features and best practices.
- Technical Support: Establish a reliable technical support system to address any issues or questions that may arise.
C. Monitoring and Maintenance:
- System Monitoring: Implement a system for monitoring the performance of PIO-D to detect any potential problems early on.
- Regular Maintenance: Perform regular maintenance tasks, such as software updates, security patches, and database backups.
D. Continuous Improvement:
- Feedback Mechanisms: Establish mechanisms for gathering feedback from users to identify areas for improvement.
- Iterative Improvements: Continuously improve the system based on user feedback and performance data.
V. Troubleshooting Common Issues: Addressing Potential Problems
Despite meticulous planning, issues can still arise during the installation of PIO-D. Being prepared for common problems is crucial for minimizing downtime and ensuring a successful implementation.
- Network Connectivity Issues: Troubleshoot network connectivity problems by checking cables, network settings, and firewall configurations.
- Software Conflicts: Resolve software conflicts by carefully reviewing software compatibility and addressing any potential issues.
- Database Errors: Troubleshoot database errors by checking database connectivity, table structures, and data integrity.
- Hardware Failures: Replace any faulty hardware components promptly.
VI. Conclusion: Maximizing the Benefits of PIO-D
The successful installation of Production Improvement Option D requires meticulous planning, careful execution, and ongoing maintenance. By following the steps outlined in this comprehensive guide, you can ensure a smooth transition, maximize the benefits of PIO-D, and reap significant improvements in your manufacturing processes. Remember that proactive planning, thorough testing, and ongoing support are key to realizing the full potential of this valuable upgrade. Investing time and resources in these areas will ensure a long-term return on your investment and contribute significantly to the success of your operations.
Latest Posts
Latest Posts
-
El Restaurante El Pimiento Rojo Abre El Proximo Sabado
Mar 31, 2025
-
Ap Lang 2020 Practice Exam 2 Mcq
Mar 31, 2025
-
3 Adjectives To Describe Shakespeares Life
Mar 31, 2025
-
Mathematical Statistics With Applications 7th Edition Solutions
Mar 31, 2025
-
6 1 Additional Practice The Polygon Angle Sum Theorems
Mar 31, 2025
Related Post
Thank you for visiting our website which covers about The Installation Of Production Improvement Option D . We hope the information provided has been useful to you. Feel free to contact us if you have any questions or need further assistance. See you next time and don't miss to bookmark.