The Number Of Shots Needed To Produce A Specific Bend.
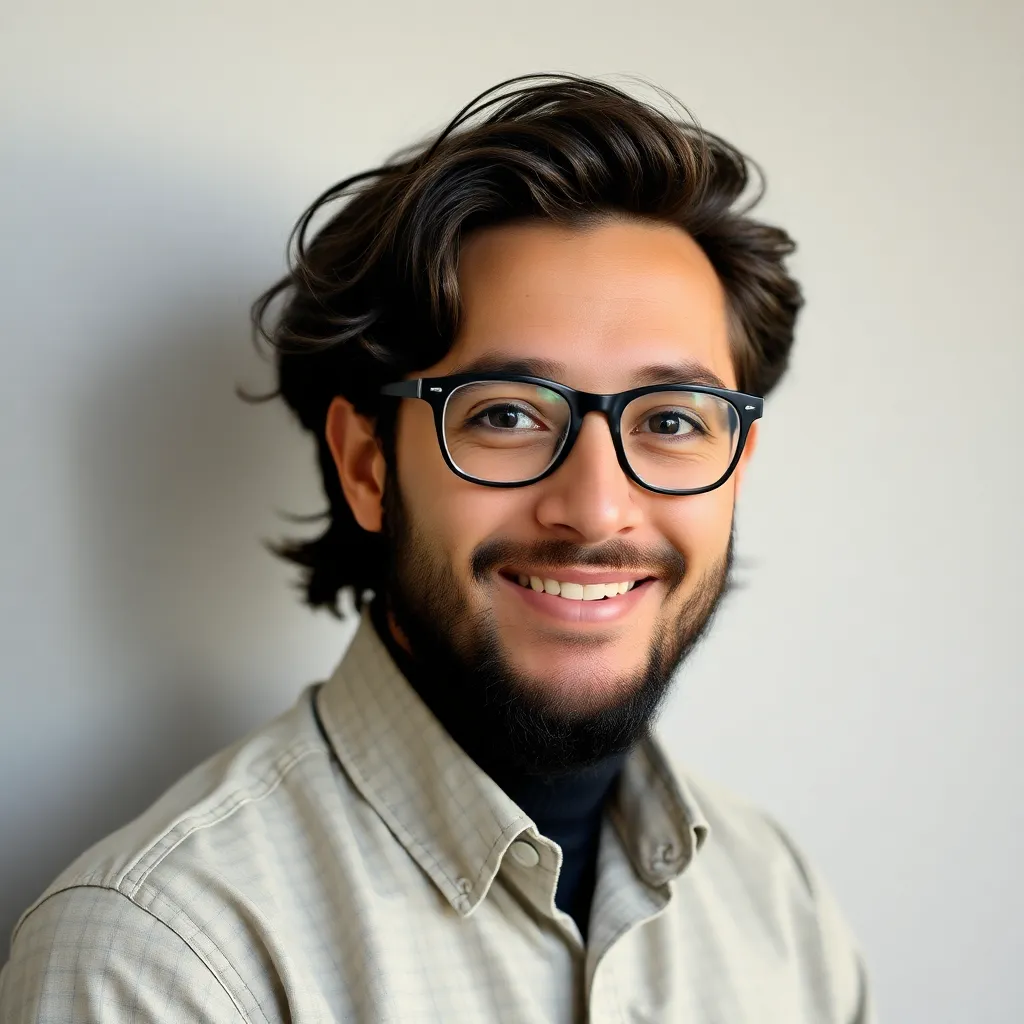
Onlines
May 11, 2025 · 6 min read
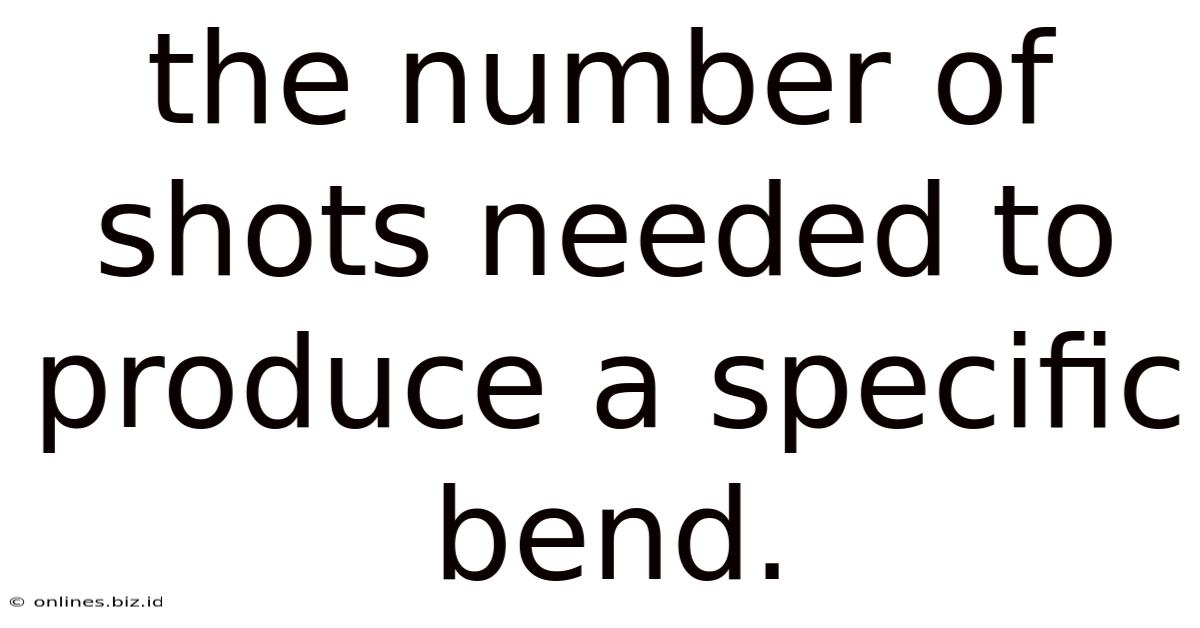
Table of Contents
The Number of Shots Needed to Produce a Specific Bend: A Deep Dive into Sheet Metal Forming
The precise number of shots required to achieve a specific bend in sheet metal forming is a complex question, influenced by numerous intertwined variables. There's no single, simple formula. Instead, understanding the underlying physics and the interplay of factors allows for accurate prediction and control, leading to consistent, high-quality results. This article delves into the intricacies of this process, exploring the key elements that determine the shot count and offering strategies for optimization.
Understanding the Bending Process
Sheet metal bending is a fundamental process in manufacturing, transforming flat sheets into desired three-dimensional shapes. This is typically achieved through a press brake, utilizing a punch and die to create the bend. The process involves plastic deformation of the metal, forcing it beyond its yield strength but remaining within its ultimate tensile strength to avoid fracture. The final bend angle is a function of several interacting factors:
Key Factors Influencing Bend Angle and Shot Count:
-
Material Properties: The type of sheet metal plays a crucial role. Material properties like yield strength, tensile strength, elastic modulus, and ductility directly impact how much the metal deforms under pressure. Thicker materials naturally require more shots to achieve the same bend angle. Steel, aluminum, and brass each exhibit different responses to bending forces.
-
Bend Radius: The radius of the bend itself significantly affects the number of shots needed. A tighter radius (smaller radius) necessitates more deformation, leading to a higher shot count compared to a larger radius bend. This is because smaller radii concentrate the strain in a smaller area.
-
Die Geometry: The shape and dimensions of the die directly influence the bending process. The die's angle, its radius, and its overall design affect the distribution of force and the resulting bend angle. A V-die produces sharp bends, while a radius die produces a smoother bend. The chosen die type considerably impacts the required number of shots.
-
Punch Geometry: Similar to the die, the punch's geometry – its shape, sharpness, and surface finish – affects the distribution of force, and consequently, the bend angle and the number of shots required. A worn or poorly designed punch can lead to inconsistent results and increased shot counts.
-
Blank Holding Force: The force used to hold the blank (the sheet metal) in place during the bending operation is crucial. Insufficient clamping force can lead to material slippage and inconsistent bend angles, potentially increasing the necessary shot counts. Excessive force might cause damage to the sheet.
-
Machine Parameters: The press brake's tonnage (force applied), its speed, and accuracy influence the bending process and the consistency of bend angles. A machine with higher tonnage can achieve a desired bend with fewer shots than one with lower tonnage. Similarly, precise control over the press brake's speed reduces inconsistencies and minimizes the need for additional shots.
Calculating the Number of Shots: An Iterative Approach
Predicting the precise number of shots required is not a straightforward calculation. Instead, it involves an iterative process based on experience, simulations, and careful experimentation.
1. Initial Estimate: Based on prior experience with similar materials, bend radii, and die geometries, an initial estimate can be made. This estimate serves as a starting point for experimentation.
2. Experimental Bending: A series of bending trials are conducted, incrementally increasing the number of shots until the desired bend angle is achieved. Careful measurements of the bend angle after each shot are essential to monitor the progress.
3. Data Analysis: The collected data on bend angle versus shot count allows for the analysis of the bending process. This analysis helps to refine the initial estimate and identify any inconsistencies in the process.
4. Process Adjustment: Based on the data analysis, adjustments can be made to various parameters. For example, if the bend angle is not progressing as expected, alterations to the blank holding force, die geometry, or press brake settings may be necessary.
5. Iteration and Refinement: This cycle of experimentation, data analysis, and adjustment is repeated until the desired bend angle is consistently achieved with a specific number of shots. This iterative process ensures optimization and consistency.
Advanced Techniques for Shot Count Optimization
Beyond the basic principles, advanced techniques can help further optimize the shot count:
-
Finite Element Analysis (FEA): FEA simulations can provide a detailed prediction of the bending process, allowing for optimization of parameters before actual experimentation. This helps to reduce the number of physical trials needed.
-
Incremental Forming: Incremental forming techniques utilize smaller incremental bends, gradually approaching the final angle. This can reduce the overall shot count required for more complex bends, especially for large angles.
-
Springback Compensation: Metal inherently springs back slightly after bending. This springback effect needs to be anticipated and compensated for during the process. By adjusting the initial bend angle to account for springback, the desired final angle can be achieved with fewer shots.
-
Material Selection: Choosing a material with greater ductility allows for achieving the target bend with fewer shots. The material's characteristics play a huge role in deformation behavior.
-
Regular Maintenance: Proper maintenance of the press brake and its components, especially the punch and die, ensures consistent performance and minimizes the risk of inconsistencies that could lead to increased shot counts.
Case Studies: Illustrative Examples
While specific numbers are highly context-dependent, let's illustrate the concept with hypothetical examples:
Case 1: Mild Steel Bending
Bending a 2mm thick mild steel sheet to a 90-degree angle with a 5mm bend radius might require 2-3 shots using a standard V-die. The specific number depends on the press brake's tonnage, blank holding force, and the material's exact properties.
Case 2: Aluminum Bending
Bending a 1mm thick aluminum sheet to a 45-degree angle with a 3mm bend radius might require only 1 shot, due to aluminum's higher ductility. However, a tighter radius or thicker sheet would necessitate more shots.
Case 3: Complex Bends
Achieving a complex bend with multiple radii and sharp transitions might require a significantly higher number of shots, potentially utilizing incremental forming techniques to minimize the risk of fracturing.
Conclusion: Precision and Consistency are Key
Determining the exact number of shots needed to produce a specific bend in sheet metal forming is a dynamic process heavily reliant on the specific materials, tools, and bending conditions. The iterative approach outlined, along with advanced techniques like FEA and incremental forming, enable optimization. Precise control over the process, coupled with careful monitoring and adjustments, ensures the production of consistent, high-quality bends with minimal wasted material and maximum efficiency. Remember that consistent results are paramount, and finding the optimal shot count is an iterative process of experimentation and refinement.
Latest Posts
Latest Posts
-
Different Businesses Are Said To Be Unrelated When
May 12, 2025
-
In Icd 10 Pcs Non Excisional Debridement Left Heel Ulcer
May 12, 2025
-
Changes To The Drawings Will Be Noted In The
May 12, 2025
-
What Written Justification Is Typically Needed For Not Purchasing
May 12, 2025
-
How Should A Project Manager Communicate The Current Focus
May 12, 2025
Related Post
Thank you for visiting our website which covers about The Number Of Shots Needed To Produce A Specific Bend. . We hope the information provided has been useful to you. Feel free to contact us if you have any questions or need further assistance. See you next time and don't miss to bookmark.