The P-system Of Inventory Submits Inventory Orders At Random Times
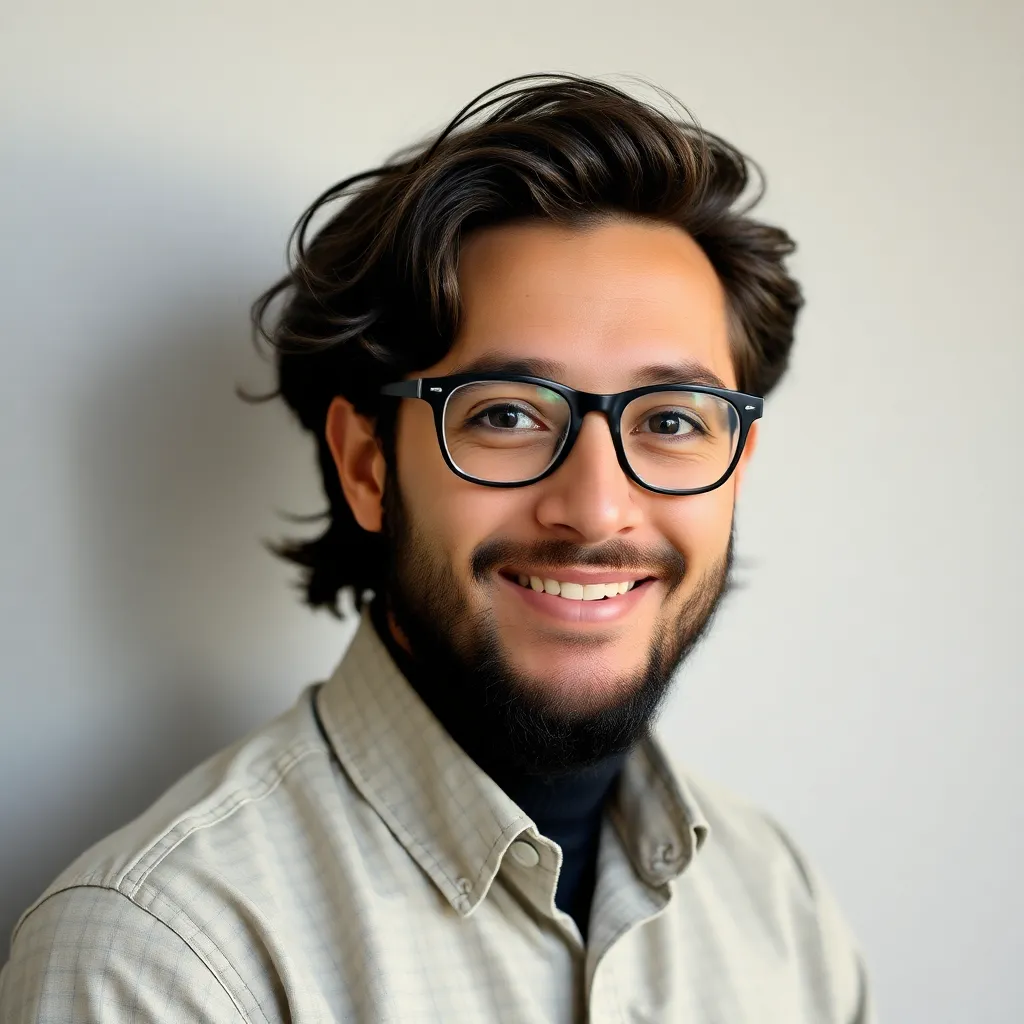
Onlines
May 08, 2025 · 6 min read
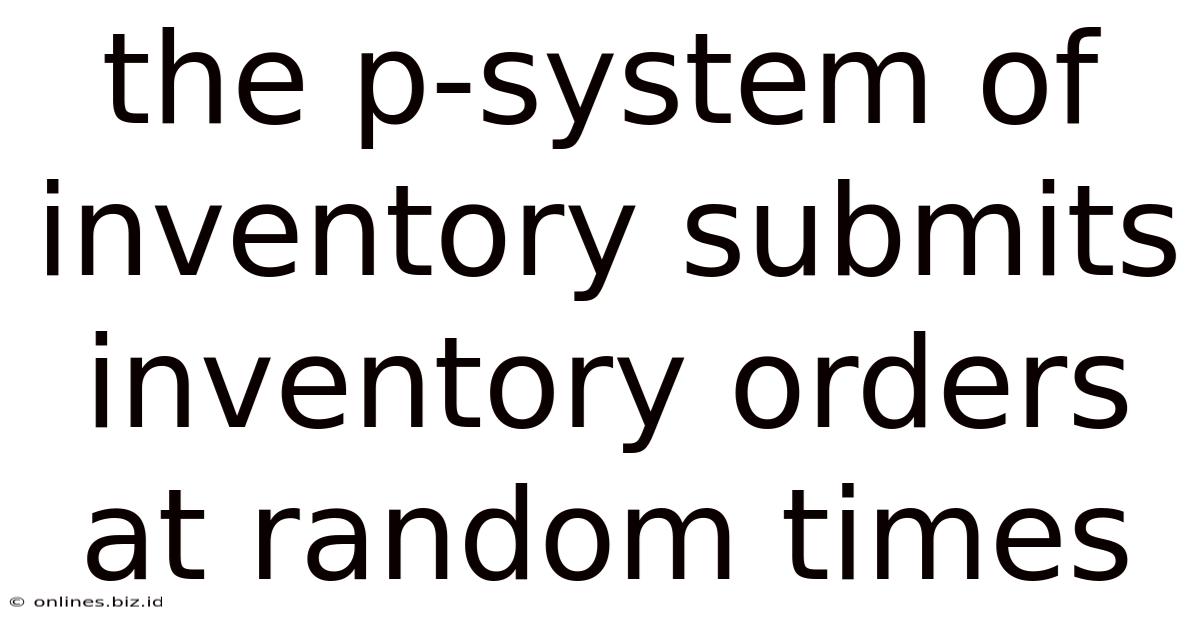
Table of Contents
The P-System of Inventory: Random Order Submissions & Their Implications
The P-system, or Periodic Review System, is a popular inventory management method where orders are placed at fixed intervals, regardless of the current inventory level. Unlike the Q-system (continuous review), which triggers orders based on reaching a predetermined reorder point, the P-system reviews inventory at regular intervals (e.g., weekly, monthly) and places an order to bring the inventory up to a target level. While seemingly straightforward, the introduction of randomness in order submission times significantly complicates the system and introduces several challenges. This article will delve deep into the implications of random order submission times within a P-system, exploring its impact on inventory levels, order costs, and overall efficiency.
Understanding the Core Mechanics of a P-System
Before diving into the complexities of random order submissions, let's establish a firm understanding of the basic P-system. At its heart, the P-system operates on a fixed review period, denoted as 'P'. At the end of each period 'P', the inventory level is checked. The difference between the desired inventory level (also known as the target inventory level or order-up-to level) and the current inventory level determines the order quantity. This ensures that, ideally, the inventory level is replenished to the target level at the end of each review period.
The target inventory level itself is a crucial parameter, carefully calculated to balance the risks of stockouts (running out of inventory) against the costs of holding excessive inventory. Factors considered in determining the target inventory level include:
- Demand Variability: How much does demand fluctuate during the review period? Higher variability necessitates a higher target inventory level to buffer against potential shortages.
- Lead Time: How long does it take to receive an order once it's placed? Longer lead times require a higher target inventory level to cover demand during the replenishment process.
- Service Level: What percentage of demand should be met without stockouts? A higher service level demands a larger safety stock, contributing to a higher target inventory level.
- Holding Costs: How much does it cost to store one unit of inventory for a given period? Higher holding costs encourage lower target inventory levels to minimize storage expenses.
Introducing Randomness: The Impact of Irregular Order Submissions
Now, let's introduce the element of randomness. Instead of perfectly adhering to the fixed review period 'P', let's assume that order submissions are subjected to unpredictable delays or early submissions. This randomness could stem from various factors:
- Supplier Delays: Unexpected production issues, transportation problems, or logistical hiccups at the supplier's end can delay order fulfillment.
- Internal Processing Bottlenecks: Internal delays in order processing, data entry errors, or communication breakdowns can postpone order submission.
- Unforeseen Circumstances: Natural disasters, strikes, or other unforeseen events can disrupt the order submission process.
These random delays and early submissions significantly alter the predictability of the P-system. The once-regular replenishment becomes erratic, leading to several potential issues:
1. Increased Inventory Variability
With inconsistent order arrival times, inventory levels fluctuate more dramatically. Periods with delayed submissions might lead to stockouts, while periods with unexpectedly early submissions could result in excessive inventory and increased holding costs. This heightened variability makes accurate inventory forecasting and management considerably more challenging.
2. Higher Stockout Risk
The possibility of delayed orders directly increases the risk of stockouts. If an order is significantly delayed, the inventory might deplete before the next planned review, leading to lost sales, disappointed customers, and potentially damage to brand reputation.
3. Increased Safety Stock Requirements
To mitigate the increased stockout risk resulting from random order submission times, companies often resort to increasing the safety stock. This, however, directly translates into higher holding costs, impacting overall profitability. The challenge lies in finding the optimal balance between safety stock and the associated cost implications.
4. Inefficient Resource Allocation
The unpredictability introduced by random order submissions makes efficient resource allocation difficult. Warehouse space, personnel, and transportation resources might be over- or underutilized depending on the actual inventory levels, leading to inefficiencies and increased costs.
5. Difficulty in Forecasting and Planning
Forecasting demand and planning production becomes significantly more complex when order submissions are random. The lack of consistent data makes it harder to develop accurate models and predictions, impacting decision-making regarding procurement, production, and resource allocation.
Mitigating the Effects of Random Order Submissions
While the randomness of order submissions introduces significant challenges, several strategies can be employed to mitigate their negative effects:
1. Improved Communication and Collaboration with Suppliers
Establishing robust communication channels and fostering strong collaborations with suppliers can help anticipate and reduce the impact of supplier-related delays. Regular communication, shared information systems, and proactive problem-solving can minimize disruptions.
2. Streamlining Internal Processes
Identifying and eliminating bottlenecks in internal order processing workflows can reduce delays from within the organization. Improving data entry accuracy, automating processes where feasible, and strengthening internal communication are key steps.
3. Robust Contingency Planning
Developing comprehensive contingency plans to address potential disruptions can minimize the impact of unforeseen events. This involves identifying potential risks, assessing their likelihood and impact, and developing mitigation strategies. These plans could involve alternative suppliers, emergency stockpiles, or flexible production schedules.
4. Utilizing Advanced Inventory Management Systems
Implementing advanced inventory management systems (IMS) equipped with sophisticated forecasting algorithms and real-time tracking capabilities can provide better visibility into inventory levels and order status. These systems can also assist in optimizing safety stock levels and dynamically adjusting order quantities based on real-time data.
5. Implementing Buffer Stock Strategies
Strategic deployment of buffer stocks can help cushion the impact of random order submissions. These stocks are strategically placed at various points in the supply chain to absorb unexpected fluctuations and prevent stockouts.
6. Employing Statistical Process Control (SPC)
SPC techniques can be used to monitor the order submission process and identify patterns or anomalies that contribute to randomness. By identifying the root causes of delays, organizations can implement targeted improvements.
7. Adopting a Hybrid Inventory System
In certain scenarios, a hybrid approach that combines elements of both P-system and Q-system might prove beneficial. This hybrid system could leverage the advantages of both systems while mitigating the weaknesses associated with random order submission times in a pure P-system.
Conclusion: Navigating the Challenges of Randomness in P-Systems
The P-system, while simple in its core concept, becomes considerably more intricate when order submissions are subjected to randomness. The resulting inventory variability, increased stockout risk, and inefficient resource allocation demand careful consideration and proactive mitigation strategies. By improving communication with suppliers, streamlining internal processes, implementing robust contingency plans, utilizing advanced inventory management systems, and considering alternative inventory control methods, organizations can effectively navigate the challenges and harness the potential benefits of the P-system even in the face of unpredictable order submission times. The key is to proactively address the root causes of randomness, improve forecasting accuracy, and optimize inventory management strategies to minimize the negative impacts and maximize efficiency. Successfully managing inventory in a dynamic environment requires a combination of technological sophistication, strategic planning, and a collaborative approach across the supply chain.
Latest Posts
Latest Posts
-
Which Three Pairs Of Concepts Best Describe The Roaring 20s
May 11, 2025
-
A Problem Facing Many People Who Never Marry Is That
May 11, 2025
-
Which Expression Corresponds To The Shaded Region
May 11, 2025
-
Compare And Contrast Mlk And Malcolm X Venn Diagram
May 11, 2025
-
Which Technological Tool Is Important For Storing Critical Files
May 11, 2025
Related Post
Thank you for visiting our website which covers about The P-system Of Inventory Submits Inventory Orders At Random Times . We hope the information provided has been useful to you. Feel free to contact us if you have any questions or need further assistance. See you next time and don't miss to bookmark.