The Presence Of Galvanic Corrosion In Water Is Signaled By
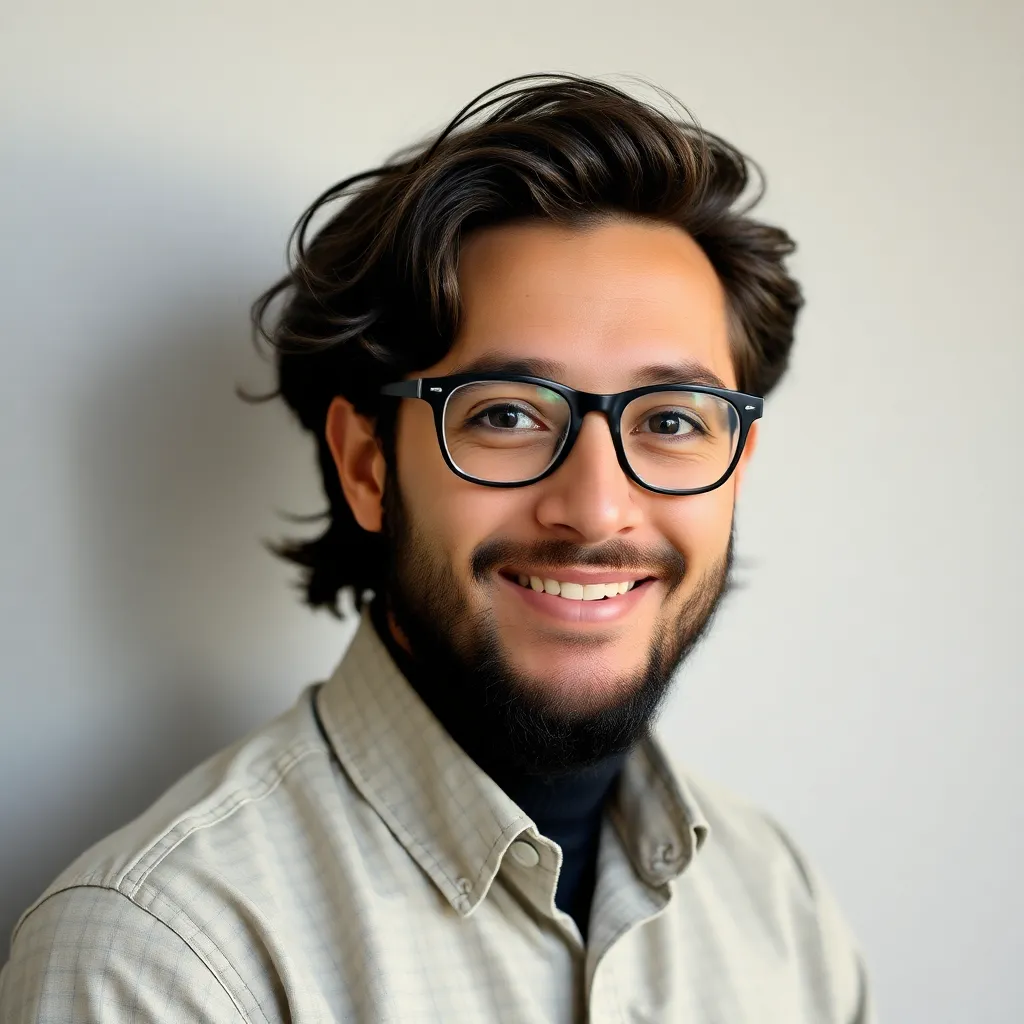
Onlines
May 09, 2025 · 6 min read
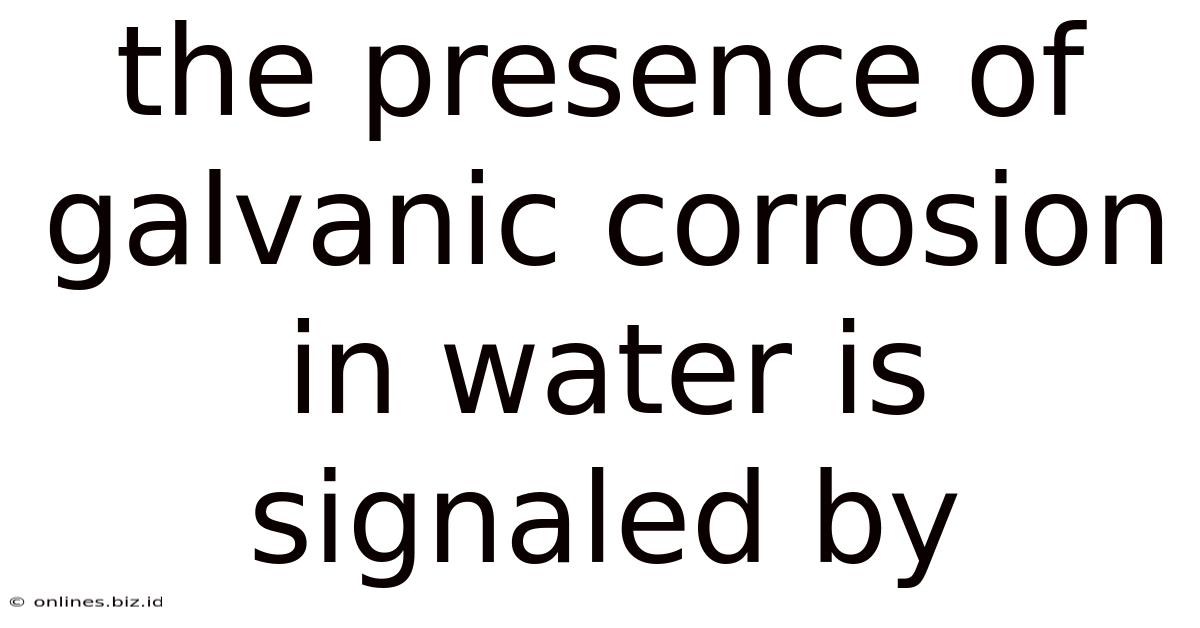
Table of Contents
The Presence of Galvanic Corrosion in Water: Signals and Solutions
Galvanic corrosion, also known as dissimilar metal corrosion, is a serious problem that can significantly impact the lifespan and functionality of submerged metallic structures. Understanding the subtle signals of its presence in water is crucial for preventative maintenance and avoiding costly repairs. This comprehensive guide delves into the telltale signs of galvanic corrosion in aquatic environments, exploring the underlying electrochemical processes and offering practical solutions for mitigation.
Understanding the Electrochemical Process
Before diving into the signs, it's essential to grasp the fundamental mechanism of galvanic corrosion. This electrochemical process occurs when two dissimilar metals are in electrical contact in the presence of an electrolyte, such as water. One metal, the anode, becomes anodic (more reactive) and undergoes oxidation, losing electrons. The other metal, the cathode, becomes cathodic (less reactive) and gains those electrons, undergoing reduction.
This electron flow creates an electric current, and the anode corrodes at an accelerated rate. The severity of galvanic corrosion depends on several factors, including:
- The difference in electrochemical potential: The larger the difference between the potentials of the two metals, the greater the corrosion rate. A comprehensive electrochemical series table can provide a guide to the relative reactivity of different metals.
- The conductivity of the electrolyte: Higher conductivity increases the rate of electron flow and accelerates corrosion. Water quality, including its salinity and temperature, plays a significant role here.
- The surface area ratio: A smaller anode coupled with a larger cathode leads to intensified corrosion of the smaller anode.
- The presence of oxygen: Oxygen acts as a depolarizer, facilitating the cathodic reaction and thus accelerating the overall corrosion process.
Recognizing the Signals of Galvanic Corrosion in Water
Detecting galvanic corrosion in its early stages is critical for effective mitigation. While the visual signs might be subtle initially, diligent inspection and monitoring can reveal their presence. Here are some key indicators:
1. Visible Pitting and Degradation of the Anode
One of the most evident signs of galvanic corrosion is localized pitting on the anodic metal. These pits are often deep and irregularly shaped, unlike the uniform corrosion that affects the entire surface. The metal around the pits may appear rough and discolored, indicating significant material loss. Regular visual inspections, particularly in areas with known dissimilar metal junctions, are crucial. The anode, being the metal more prone to oxidation, will exhibit the most severe pitting and deterioration.
2. Discoloration and Coating Breakdown
The presence of galvanic corrosion can lead to discoloration of the affected metal. This discoloration might manifest as a change in hue, staining, or the formation of corrosion products. Moreover, protective coatings, if present, will typically break down or peel off near the corrosion sites, providing further evidence of galvanic activity. Regularly assess the integrity of any protective coatings on submerged metallic structures.
3. White or Colored Deposits near the Cathode
While pitting is dominant on the anode, the cathode also displays signs, though typically less dramatic. You might notice white or colored deposits forming near the cathode. These deposits are often corrosion products from the anode that have migrated and accumulated at the cathodic surface. The color depends on the involved metals and the water chemistry.
4. Unexpected Metal Weight Loss
Measuring the weight of metal components before and after submersion in water can reveal significant and unexplained weight loss, a strong indication of accelerated corrosion, including galvanic corrosion. This is particularly useful in controlled environments or for specific components where accurate weighing is feasible. It's important to account for other sources of weight loss, such as erosion or abrasion.
5. Increased Electrical Conductivity of Water
While not a direct visual sign, an increase in the electrical conductivity of the surrounding water can hint at ongoing galvanic corrosion. This occurs due to the release of ions into the water during the corrosion process. Measuring the conductivity of water near suspected corrosion sites can be a valuable diagnostic tool.
6. Hydrogen Gas Evolution
In certain cases, particularly with metals like steel, the cathodic reaction involves the reduction of protons from water to form hydrogen gas. The evolution of hydrogen bubbles at the cathodic surface is a clear indication of galvanic corrosion activity.
7. Changes in Water pH
Galvanic corrosion alters the chemical composition of the surrounding water. The release of ions and the formation of corrosion products can lead to changes in the water's pH. Monitoring the pH of the water can help detect subtle changes associated with corrosion activity.
Mitigation Strategies: Preventing and Controlling Galvanic Corrosion
Once the presence of galvanic corrosion is confirmed, timely intervention is crucial to prevent further damage. Here are several effective strategies for mitigation:
1. Material Selection: Choosing Compatible Metals
The most effective approach is to avoid the problem altogether by using compatible materials. Selecting metals with similar electrochemical potentials minimizes the driving force for galvanic corrosion. Consulting an electrochemical series is vital when choosing materials for submerged applications. Using metals close together in the electrochemical series drastically reduces the galvanic current.
2. Cathodic Protection: Sacrificial Anodes
Cathodic protection is a widely employed technique where a more active metal (sacrificial anode) is connected to the structure to be protected. This sacrificial anode corrodes preferentially, protecting the primary structure. Materials like zinc, magnesium, or aluminum are commonly used as sacrificial anodes. The proper selection and sizing of the sacrificial anode are crucial for effective protection. Regular inspection and replacement of the sacrificial anodes are necessary to maintain protection.
3. Impressed Current Cathodic Protection (ICCP):
ICCP uses an external power source to impose a negative potential on the structure to be protected, suppressing corrosion. This is a more sophisticated technique than using sacrificial anodes, and it requires specialized equipment and expertise. However, it offers more precise control over the protection potential.
4. Coatings and Linings: Barrier Protection
Applying protective coatings or linings to the metal surfaces creates a barrier that prevents contact between the dissimilar metals and the electrolyte, reducing the rate of galvanic corrosion. Several coating materials, including paints, polymers, and specialized linings, are available, each suited for specific applications. The quality and integrity of the coatings are vital; proper application and regular inspection are essential.
5. Design Modifications: Minimizing Contact
In many cases, design changes can reduce the risk of galvanic corrosion. For instance, separating dissimilar metals electrically by using insulating materials or by ensuring that different metals do not come into direct contact can drastically reduce or eliminate the problem. Proper design considerations at the initial stages are more cost-effective than remedial actions.
6. Regular Monitoring and Inspection: Early Detection
Implementing a proactive monitoring and inspection program is paramount. Regular visual inspections, coupled with periodic measurements of metal weight loss, water conductivity, and pH, allow for early detection of galvanic corrosion and facilitate timely mitigation efforts. This preventative approach is far more cost-effective than dealing with severe corrosion damage.
Conclusion
Galvanic corrosion in water is a complex electrochemical process with potentially devastating consequences. Understanding the signals of its presence – from visible pitting and discoloration to subtle changes in water chemistry – is crucial for timely intervention. Adopting preventive measures, such as careful material selection, cathodic protection, and appropriate coatings, combined with regular monitoring and inspection, is key to minimizing the impact of galvanic corrosion and ensuring the longevity of submerged metallic structures. Early detection and proactive mitigation are the best approaches to avoid costly repairs and maintain the integrity of your systems. Remember, consulting with corrosion specialists can provide tailored solutions for your specific needs and environmental conditions.
Latest Posts
Latest Posts
-
Enpc Pre Course Study Guide Answers
May 09, 2025
-
Sir Gawain And The Green Knight Mastery Test
May 09, 2025
-
A Long Way Gone Chapter 10 Summary
May 09, 2025
-
Fixture Wire Is Available In Sizes From
May 09, 2025
-
The Theme Of The Lesson By Toni Cade Bambara
May 09, 2025
Related Post
Thank you for visiting our website which covers about The Presence Of Galvanic Corrosion In Water Is Signaled By . We hope the information provided has been useful to you. Feel free to contact us if you have any questions or need further assistance. See you next time and don't miss to bookmark.