The Proper Quantity Of Safety Stock Is Typically Determined By
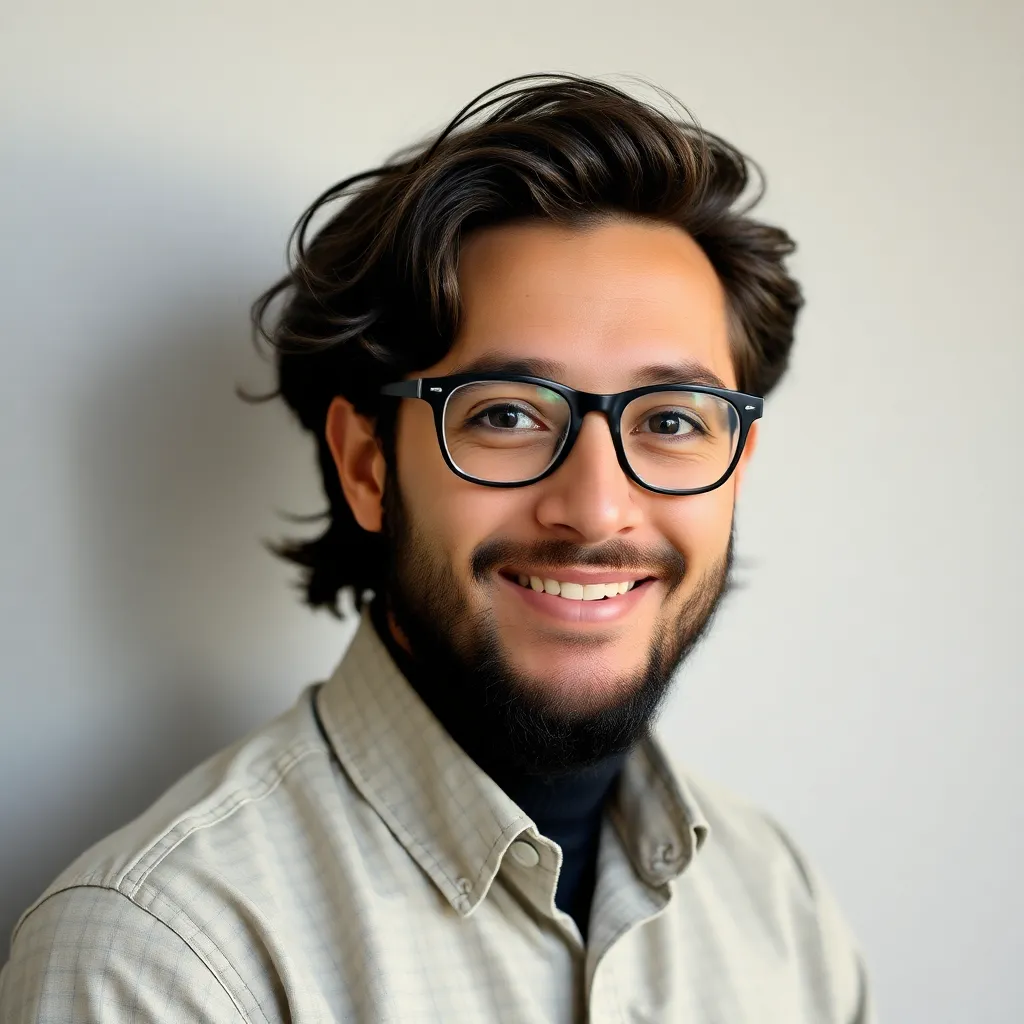
Onlines
May 04, 2025 · 7 min read

Table of Contents
Determining the Proper Quantity of Safety Stock: A Comprehensive Guide
Maintaining optimal inventory levels is crucial for any business. Holding too much inventory ties up capital and increases storage costs, while holding too little can lead to stockouts, lost sales, and dissatisfied customers. A key component of inventory management is safety stock – the buffer stock held to protect against unexpected demand surges, lead time variations, and supply chain disruptions. Determining the proper quantity of safety stock is a delicate balancing act, requiring a thorough understanding of several factors. This guide delves into the methods and considerations involved in calculating the right safety stock level for your business.
Understanding the Need for Safety Stock
Before diving into the calculations, it's vital to understand why safety stock is necessary. Without it, even the most meticulously planned inventory system can be thrown off by unforeseen events. These events can include:
Fluctuations in Demand:
- Seasonality: Demand for certain products often fluctuates throughout the year. Christmas trees sell well in December, but not in July. Safety stock accounts for these predictable peaks and troughs.
- Unexpected Spikes: Unforeseen events, such as a viral social media trend or a competitor's stockout, can dramatically increase demand overnight. Safety stock provides a cushion against these sudden surges.
- Random Variations: Even with careful forecasting, day-to-day demand can vary randomly. This inherent unpredictability is another reason to maintain a safety stock.
Lead Time Variability:
- Supplier Delays: Suppliers may experience unexpected delays due to production issues, transportation problems, or other unforeseen circumstances. Safety stock ensures you can meet customer demand while waiting for your replenishment order.
- Shipping Issues: Shipping delays can occur due to weather, port congestion, or logistical bottlenecks. Safety stock mitigates the impact of these delays.
- Internal Processing Time: Even after receiving goods, there may be delays in processing and making them available for sale. Safety stock covers this internal lead time variation.
Methods for Calculating Safety Stock
Several methods exist for calculating the appropriate safety stock level. The best method depends on the complexity of your inventory system, the availability of data, and your risk tolerance. Here are some of the most common approaches:
1. The Simple Approach: Using a Percentage of Average Demand
This is the simplest method, suitable for businesses with relatively stable demand and consistent lead times. It involves calculating safety stock as a percentage of average demand during the lead time.
Formula: Safety Stock = Average Lead Time Demand * Percentage Safety Stock
For example, if your average lead time demand is 100 units and you choose a 20% safety stock level, your safety stock would be 20 units (100 * 0.20). The percentage you choose will depend on your risk tolerance and the variability of your demand and lead times. A higher percentage indicates a higher level of protection but also higher inventory costs.
2. Using Standard Deviation and Service Level: A More Sophisticated Approach
This method accounts for the variability of demand and lead time. It requires more data and a deeper understanding of statistical concepts. The core of this method is to determine the standard deviation of demand during lead time. This measures the dispersion of demand around the average.
Formula: Safety Stock = Z * √(LT * σ²)
Where:
- Z: The Z-score corresponding to your desired service level. The Z-score represents the number of standard deviations from the mean. A higher Z-score corresponds to a higher service level (lower risk of stockout) but also higher safety stock. You can find Z-scores in a standard normal distribution table. For example, a 95% service level corresponds to a Z-score of approximately 1.645.
- LT: Lead time in periods (days, weeks, etc.).
- σ²: Variance of demand per period. This is the square of the standard deviation (σ) of demand.
This method provides a more accurate estimate of safety stock than the simple percentage method, particularly when demand and lead times are variable.
3. Incorporating Multiple Products and Dependencies
Many businesses manage hundreds or even thousands of products, and some products might be dependent on others (e.g., a finished product needs multiple components). For these scenarios, more advanced inventory optimization techniques are necessary. These may include:
- ABC Analysis: Categorizing inventory items into A (high value), B (medium value), and C (low value) categories. More safety stock is typically allocated to A-items.
- Multi-echelon Inventory Optimization: Managing safety stock across multiple locations within a supply chain, taking into account transportation times and inventory levels at different stages.
- Simulation Modeling: Using computer simulations to model different scenarios and assess the impact of various safety stock levels.
Factors Affecting Safety Stock Calculations
Several factors influence the appropriate level of safety stock. Ignoring these can lead to inaccurate calculations and suboptimal inventory management.
1. Demand Variability:
The more volatile your demand, the higher your safety stock should be. Historical sales data is crucial for determining demand variability. Analyze trends, seasonality, and unexpected spikes to get a realistic picture.
2. Lead Time Variability:
Uncertainties in your lead time directly impact your safety stock requirements. Longer and more variable lead times necessitate higher safety stock levels to cover potential delays. Monitor your supplier's performance and identify potential bottlenecks in your supply chain to improve lead time predictability.
3. Service Level:
Your desired service level dictates the risk you're willing to accept regarding stockouts. A higher service level (e.g., 99%) means a lower risk of stockouts but necessitates more safety stock. Choosing the appropriate service level involves balancing the cost of holding excess inventory with the cost of potential stockouts.
4. Cost of Stockouts:
The cost of a stockout can vary dramatically depending on the product and the customer's reaction. For critical items or products with high demand, the cost of a stockout could be significantly higher than the cost of holding extra inventory. Carefully consider these costs when setting your safety stock level.
5. Cost of Holding Inventory:
Inventory holding costs include storage, insurance, obsolescence, and capital costs. These costs influence the trade-off between safety stock and the risk of stockouts. Reducing holding costs through efficient warehouse management and inventory control can free up capital and reduce the overall cost of safety stock.
6. Product Perishability:
Perishable products have a limited shelf life. Safety stock for these products must consider spoilage and obsolescence. Accurate demand forecasting and efficient inventory rotation are crucial for managing safety stock for perishable goods.
Implementing and Monitoring Safety Stock
Calculating the right safety stock level is only the first step. Effective implementation and continuous monitoring are essential for optimizing inventory management.
- Regular Reviews: Your safety stock calculations shouldn't be a one-time event. Demand patterns, lead times, and other factors can change over time. Regularly review your safety stock levels and adjust them as needed based on updated data and market conditions.
- Technology Integration: Inventory management software can automate safety stock calculations, track inventory levels in real-time, and generate alerts when stock levels fall below predetermined thresholds. These systems can significantly improve efficiency and accuracy.
- Supplier Relationships: Strengthening relationships with your suppliers can help reduce lead time variability. Good communication and collaborative planning can improve supply chain predictability and reduce the need for excessive safety stock.
- Demand Forecasting: Invest in sophisticated demand forecasting techniques to improve the accuracy of your demand predictions. Advanced statistical methods and machine learning algorithms can provide more accurate forecasts, reducing the need for overly conservative safety stock levels.
Conclusion
Determining the proper quantity of safety stock is a critical aspect of inventory management. The right approach balances the cost of holding excess inventory against the risk of stockouts. While simple methods exist, more sophisticated techniques, like those using standard deviation and service level, provide more accurate results, particularly when demand and lead times are variable. Regular review, technological integration, and strong supplier relationships are crucial for optimizing safety stock levels and maintaining a healthy inventory balance. By carefully considering all these factors, businesses can significantly improve their efficiency, reduce costs, and enhance customer satisfaction.
Latest Posts
Latest Posts
-
Dr Guttierez Is Examining A Research Question
May 05, 2025
-
This Biome Is Characterized By Long Dry Seasons
May 05, 2025
-
Characters Of A Good Man Is Hard To Find
May 05, 2025
-
Select The True Statements About Unsupervised Learning
May 05, 2025
-
Surfaces Must Be Sanitized Before They Are Cleaned
May 05, 2025
Related Post
Thank you for visiting our website which covers about The Proper Quantity Of Safety Stock Is Typically Determined By . We hope the information provided has been useful to you. Feel free to contact us if you have any questions or need further assistance. See you next time and don't miss to bookmark.