The Traditional Operations Management Definition Of Throughput Is
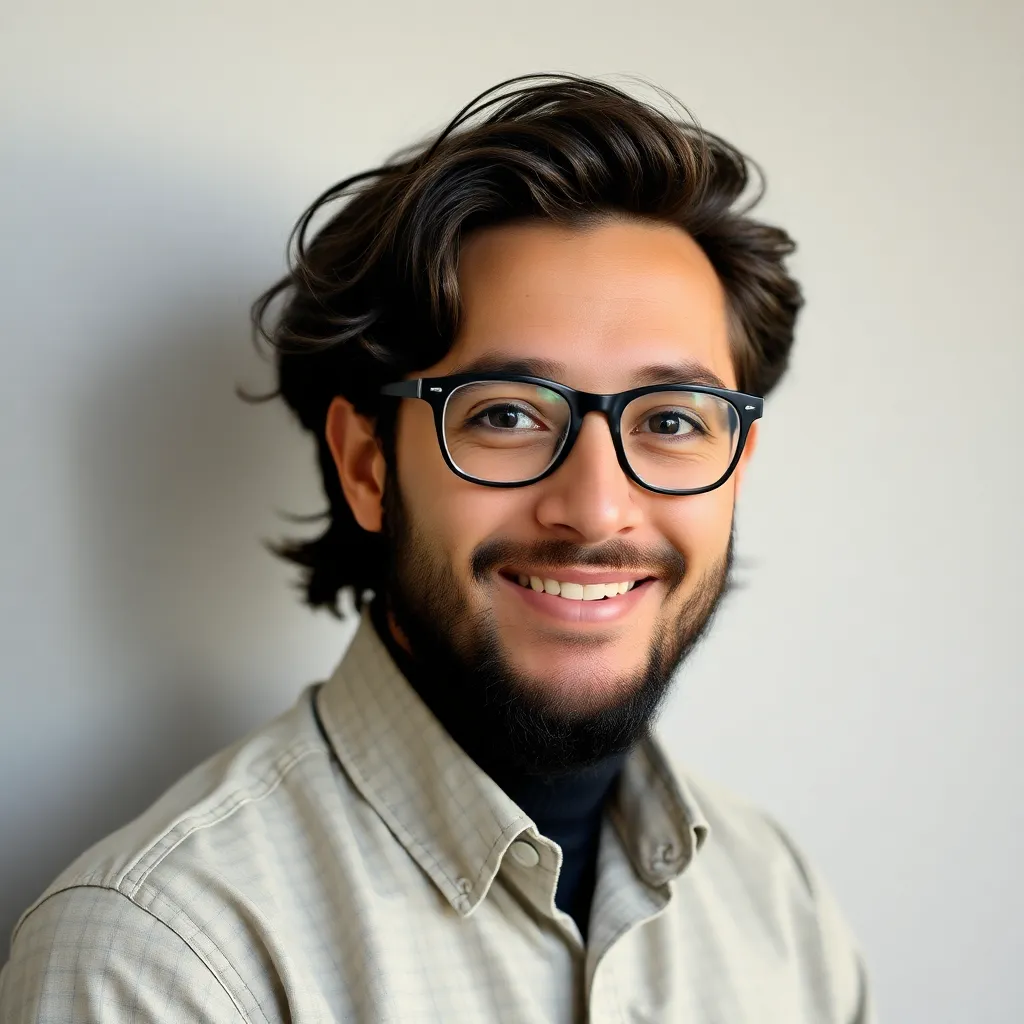
Onlines
Apr 08, 2025 · 6 min read

Table of Contents
The Traditional Operations Management Definition of Throughput: A Deep Dive
The traditional definition of throughput in operations management is deceptively simple: the rate at which a system produces outputs. However, understanding its nuances and implications requires a deeper dive into its various facets, its relationship with other key performance indicators (KPIs), and its crucial role in optimizing operational efficiency. This article will explore the traditional definition, its complexities, and its application across various industries.
Understanding Throughput: Beyond a Simple Definition
While the basic definition is straightforward, the devil is in the details. Throughput isn't just about the sheer number of units produced; it considers the rate of production within a specific timeframe. This timeframe can be an hour, a day, a week, or even a month, depending on the context and the nature of the production process. A crucial element often overlooked is the quality of the output. A system might churn out a high volume of products, but if a significant portion is defective, the effective throughput is drastically reduced.
Key considerations for accurate throughput measurement:
- Defining the "system": Clearly identifying the boundaries of the system being measured is critical. Is it a single machine, an entire production line, a department, or the entire organization? Inconsistent system definition leads to misleading throughput data.
- Measuring the "output": Defining what constitutes a "finished" output is equally important. Are partially completed products included? What about rework or scrap? Precise definition avoids ambiguity and ensures consistent measurement.
- Timeframe consistency: Choosing and consistently applying a specific timeframe is crucial for accurate comparisons and trend analysis. Switching timeframes arbitrarily can obscure meaningful patterns in throughput data.
- Quality considerations: Defective outputs should be excluded from the throughput calculation unless specifically analyzing defect rates alongside throughput. This provides a more realistic picture of operational efficiency.
Throughput vs. Other Key Performance Indicators (KPIs)
Throughput is rarely considered in isolation. Its effectiveness and meaning are heavily intertwined with other operational KPIs, including:
-
Inventory: High inventory levels can mask inefficiencies in the production process, leading to an artificially inflated perception of throughput. Conversely, excessively low inventory can lead to production bottlenecks and decreased throughput. The ideal balance requires careful management of inventory levels to support optimal throughput without excessive holding costs. Just-in-time (JIT) inventory management techniques aim to minimize inventory while maximizing throughput.
-
Lead Time: This refers to the time it takes to complete a product or service from the start of the process to its completion. High throughput ideally coincides with shorter lead times, indicating efficient resource utilization. However, solely focusing on maximizing throughput without considering lead time can lead to increased work-in-progress (WIP) and higher inventory costs.
-
Capacity: This represents the maximum output a system can achieve under ideal conditions. Throughput is always less than or equal to capacity due to various factors like machine downtime, operator errors, and material shortages. Understanding the relationship between throughput and capacity helps identify bottlenecks and areas for improvement.
-
Utilization: This represents the percentage of time a resource (machine, employee, etc.) is actively engaged in production. High utilization doesn't automatically translate to high throughput; inefficient utilization can lead to lower output despite high resource engagement.
-
Cycle Time: This is the time taken to complete one unit of output. Reducing cycle time directly improves throughput. Lean manufacturing principles, including value stream mapping and process optimization, target cycle time reduction to enhance throughput.
Throughput in Different Industries
The concept of throughput applies across various industries, but its measurement and interpretation vary significantly:
Manufacturing: In manufacturing, throughput is typically measured in units produced per hour, day, or week. Factors influencing throughput include machine capacity, worker efficiency, material availability, and production line layout. Lean manufacturing methodologies focus on optimizing each element to enhance throughput and reduce waste.
Healthcare: In healthcare, throughput might measure the number of patients treated or procedures performed per day or week. Efficient patient flow and resource allocation are crucial for maximizing throughput without compromising patient care quality. This often involves optimizing appointment scheduling, staffing levels, and resource utilization.
Software Development: In software development, throughput can be measured by the number of features implemented, bugs fixed, or lines of code written within a given timeframe. Agile methodologies, such as Scrum and Kanban, employ iterative development and continuous integration to optimize throughput and deliver value incrementally.
Retail: In retail, throughput can refer to the number of customers served, transactions processed, or units sold per hour or day. Effective store layout, staffing levels, and efficient checkout processes directly impact throughput and overall sales.
Optimizing Throughput: Strategies and Techniques
Improving throughput requires a systematic approach focusing on identifying and eliminating bottlenecks, optimizing resource utilization, and improving process efficiency. Key strategies include:
-
Bottleneck identification and elimination: Analyzing the production process to pinpoint bottlenecks – stages where the flow of work is constrained – is crucial. Addressing these bottlenecks, through increased capacity, process improvement, or resource reallocation, can significantly enhance throughput.
-
Process optimization: Streamlining workflows, eliminating redundant steps, and improving efficiency at each stage of the production process directly impact throughput. Techniques such as value stream mapping, Six Sigma, and Lean manufacturing provide structured approaches to process optimization.
-
Inventory management: Implementing efficient inventory management practices, such as JIT, minimizes inventory holding costs while ensuring sufficient materials are available to support optimal throughput. This requires careful forecasting and demand planning.
-
Capacity planning: Accurately estimating capacity requirements and ensuring sufficient resources are available prevents bottlenecks and maximizes throughput. This involves considering factors such as machine capacity, employee availability, and material supply.
-
Employee training and development: Well-trained and skilled employees are essential for efficient operations. Investing in employee training and development enhances their efficiency and reduces errors, contributing to improved throughput.
-
Technology adoption: Implementing advanced technologies, such as automation, robotics, and data analytics, can significantly improve efficiency and throughput. This requires careful consideration of the costs and benefits of technology adoption.
-
Continuous improvement: Adopting a culture of continuous improvement, embracing feedback mechanisms, and regularly reviewing operational processes helps to identify areas for ongoing optimization and enhance throughput over time.
Conclusion: The Ongoing Relevance of Throughput
The traditional definition of throughput, while seemingly basic, underpins effective operations management. Its accurate measurement and interpretation, in conjunction with other key performance indicators, are crucial for understanding operational efficiency and identifying opportunities for improvement. By systematically analyzing the production process, identifying bottlenecks, and implementing targeted strategies, organizations across various industries can optimize their throughput, enhance productivity, and achieve their business objectives. The ongoing focus on efficiency and continuous improvement makes the understanding and optimization of throughput a crucial aspect of modern operations management. The pursuit of higher throughput isn't merely about producing more; it's about producing more efficiently, effectively, and profitably.
Latest Posts
Latest Posts
-
Signing Naturally Units 1 6 Pdf Answers
Apr 08, 2025
-
Label The Muscles In The Following Illustration
Apr 08, 2025
-
Correctly Label The External Anatomy Of The Anterior Heart
Apr 08, 2025
-
What Is The Theme Of Button Button
Apr 08, 2025
-
Cress Insurance Company Completing A Flyer
Apr 08, 2025
Related Post
Thank you for visiting our website which covers about The Traditional Operations Management Definition Of Throughput Is . We hope the information provided has been useful to you. Feel free to contact us if you have any questions or need further assistance. See you next time and don't miss to bookmark.