The Two Basic Types Of Cost Accounting Systems Are
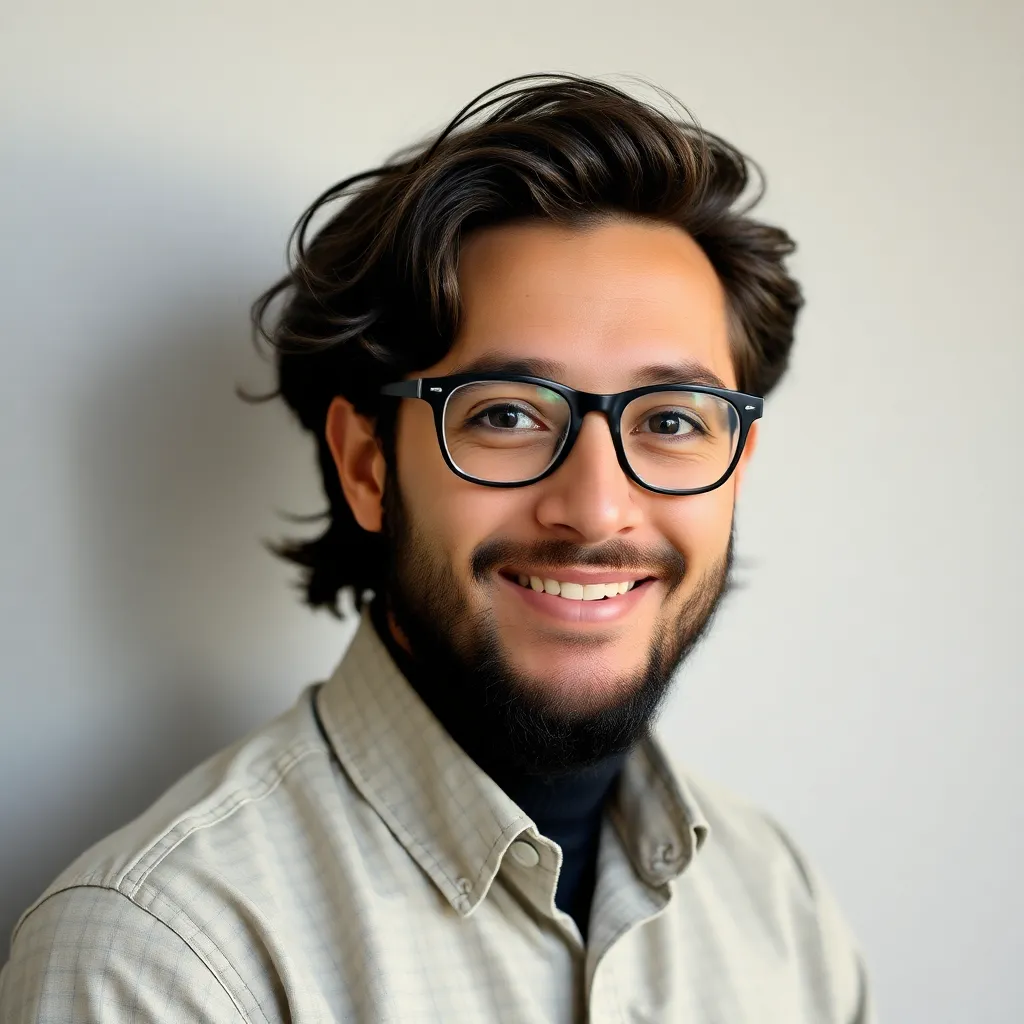
Onlines
Apr 05, 2025 · 6 min read
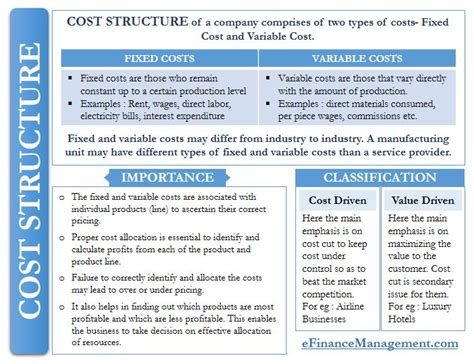
Table of Contents
The Two Basic Types of Cost Accounting Systems Are: A Deep Dive into Job Order and Process Costing
Cost accounting, a crucial aspect of managerial accounting, provides businesses with insights into the costs associated with producing goods or services. Understanding these costs is vital for pricing strategies, performance evaluation, and overall profitability. While numerous cost accounting methods exist, two fundamental systems form the cornerstone: job order costing and process costing. This comprehensive guide will delve into the nuances of each, highlighting their applications, advantages, and limitations.
Job Order Costing: Tracking Costs for Unique Projects
Job order costing is a method that meticulously tracks the costs associated with individual projects or jobs. This approach is particularly well-suited for businesses producing unique or customized products or services, where each item or service possesses distinct characteristics and requires a separate cost calculation. Think bespoke tailoring, custom-built homes, or specialized software development—each project is distinct, requiring its own cost record.
Key Characteristics of Job Order Costing:
- Individual Job Tracking: The core principle is assigning costs directly to specific jobs. This involves tracking direct materials, direct labor, and manufacturing overhead for each individual project.
- Direct Cost Assignment: Direct materials and direct labor are easily traceable to specific jobs. For example, the fabric used in a tailor-made suit or the labor hours spent by a software developer on a specific project are directly attributable.
- Overhead Allocation: Manufacturing overhead, encompassing indirect costs like factory rent, utilities, and depreciation, is allocated to jobs using predetermined overhead rates. This often involves selecting an allocation base, such as direct labor hours or machine hours, to distribute the overhead costs fairly across different projects.
- Cost Accumulation: A job cost sheet is utilized to accumulate all costs related to a specific job. This document provides a comprehensive overview of all expenses incurred, offering valuable insights for pricing and profitability analysis.
Examples of Industries Utilizing Job Order Costing:
- Construction: Each building project represents a unique job with its own specific materials, labor, and overhead costs.
- Printing: Custom print jobs, such as personalized brochures or specialized packaging, require a job order costing system to track costs effectively.
- Advertising Agencies: Each advertising campaign is a unique project with its own budget and expenses, necessitating individual cost tracking.
- Custom Furniture Makers: Unique furniture pieces, tailored to customer specifications, require careful cost tracking for each individual project.
- Legal Services: Each case handled by a law firm represents a distinct job, with associated legal fees, staff time, and other costs.
Advantages of Job Order Costing:
- Accurate Cost Tracking: Provides detailed cost information for each job, enabling precise pricing and profitability analysis.
- Improved Cost Control: Detailed cost tracking facilitates better control over expenses and identifies areas for potential cost reduction.
- Effective Pricing Strategies: Accurate cost information allows businesses to set competitive and profitable prices.
- Enhanced Decision Making: Provides valuable data for informed decision-making related to project acceptance, resource allocation, and pricing.
Limitations of Job Order Costing:
- Complexity: Can be complex and time-consuming, especially for businesses with a high volume of jobs.
- Overhead Allocation Challenges: Accurately allocating overhead costs can be challenging, potentially leading to inaccuracies in job costs.
- Not Suitable for Mass Production: Inefficient for businesses producing large quantities of identical products.
Process Costing: Averaging Costs for Mass Production
Process costing is a cost accounting method employed by businesses that manufacture large quantities of identical or similar products. Unlike job order costing, which tracks costs for individual jobs, process costing aggregates costs for entire production processes and then averages them across all units produced. Think of companies producing canned goods, beverages, or mass-produced clothing—products that are largely uniform.
Key Characteristics of Process Costing:
- Production Processes: Costs are tracked at each stage of the production process, rather than for individual units.
- Cost Aggregation: Costs are accumulated for the entire production process, rather than for individual products.
- Cost Averaging: Costs are averaged across all units produced within a specific period.
- Equivalent Units: A crucial concept in process costing, equivalent units represent the number of completed units that would have been produced if all units were fully completed. This accounts for partially completed units at the end of a period.
- Cost Allocation: The total cost of the production process is allocated to completed and partially completed units based on their equivalent units.
Examples of Industries Utilizing Process Costing:
- Food Processing: Companies producing canned goods, beverages, or packaged foods often use process costing.
- Chemical Manufacturing: The production of chemicals frequently involves process costing due to the large volumes of identical products.
- Textile Manufacturing: Mass production of fabrics and clothing typically uses process costing.
- Oil Refining: The refining of crude oil into various petroleum products utilizes process costing to track and allocate costs.
- Paper Manufacturing: Producing large quantities of paper requires process costing to manage costs effectively.
Advantages of Process Costing:
- Simplicity: Simpler and less time-consuming than job order costing, especially for mass production.
- Cost Efficiency: Cost-effective for businesses with high production volumes of similar products.
- Easier to Implement: Relatively easy to implement and maintain compared to job order costing.
- Suitable for Mass Production: Ideal for businesses producing large quantities of identical products.
Limitations of Process Costing:
- Less Accurate Cost Information: Provides less detailed cost information for individual units compared to job order costing.
- Average Costs May Mask Inefficiencies: Averaging costs may obscure inefficiencies within specific parts of the production process.
- Not Suitable for Customized Products: Inefficient for businesses producing unique or customized products.
- Inventory Valuation Challenges: Inventory valuation can be complex, especially when dealing with work-in-process (WIP) inventory.
Choosing the Right Cost Accounting System: A Practical Approach
Selecting the appropriate cost accounting system depends heavily on the nature of the business and its production processes. Here's a practical approach to choosing between job order and process costing:
- Nature of Products: If your business produces unique or customized products, job order costing is the better choice. If you mass-produce identical or similar products, process costing is more appropriate.
- Production Volume: High-volume production generally favors process costing, while low-volume or custom production is better suited to job order costing.
- Cost Tracking Needs: If detailed cost tracking for each individual product or project is crucial, job order costing is essential. If overall cost control for the production process is sufficient, process costing is adequate.
- Complexity and Cost: Consider the complexity and cost of implementation and maintenance for each system. Process costing generally requires less administrative overhead.
Hybrid Costing Systems: Blending the Best of Both Worlds
It's important to note that many businesses employ hybrid costing systems, combining elements of both job order and process costing. This approach proves beneficial in situations where some products or services are customized while others are mass-produced. For example, a furniture manufacturer might use job order costing for custom-designed pieces and process costing for mass-produced furniture components.
Conclusion: Mastering Cost Accounting for Business Success
Understanding the nuances of job order and process costing is critical for effective cost management and informed business decision-making. By selecting the appropriate system based on the specifics of the business and production processes, companies can gain valuable insights into their costs, optimize pricing strategies, and enhance overall profitability. Regularly reviewing and refining the chosen cost accounting system is vital to ensure its continued effectiveness and relevance in a dynamic business environment. Accurate and timely cost information serves as a bedrock for sustainable growth and success in any industry.
Latest Posts
Latest Posts
-
Which Of The Following Conditions Respond To Light Therapy
Apr 05, 2025
-
Heat Of Neutralization Pre Lab Answers
Apr 05, 2025
-
Rob Is Planning His Housewarming Party
Apr 05, 2025
-
Edition 5 6 Magazine Quiz Answers Tfk
Apr 05, 2025
-
Employees Who Are Fully Engaged View Their Jobs As
Apr 05, 2025
Related Post
Thank you for visiting our website which covers about The Two Basic Types Of Cost Accounting Systems Are . We hope the information provided has been useful to you. Feel free to contact us if you have any questions or need further assistance. See you next time and don't miss to bookmark.