Typically Osha Views All These Job-related Circumstances
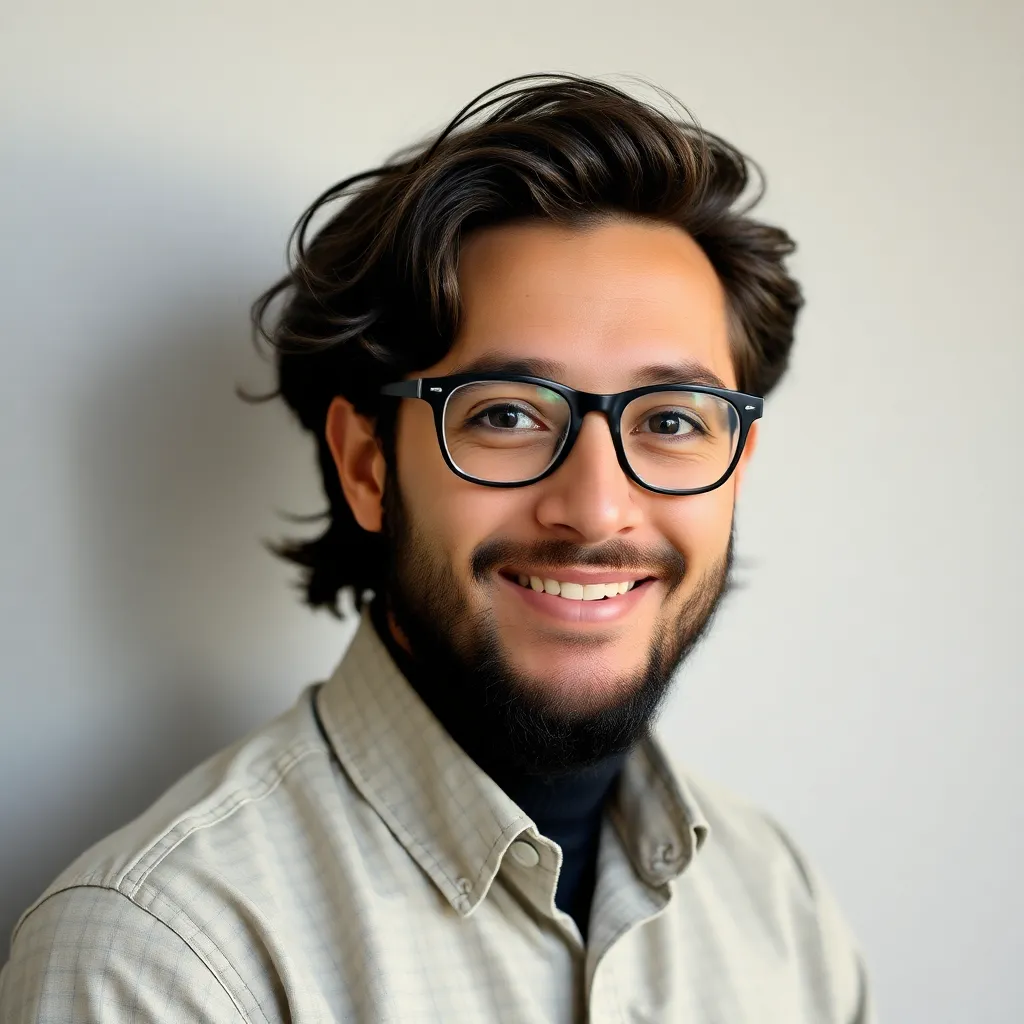
Onlines
May 11, 2025 · 6 min read
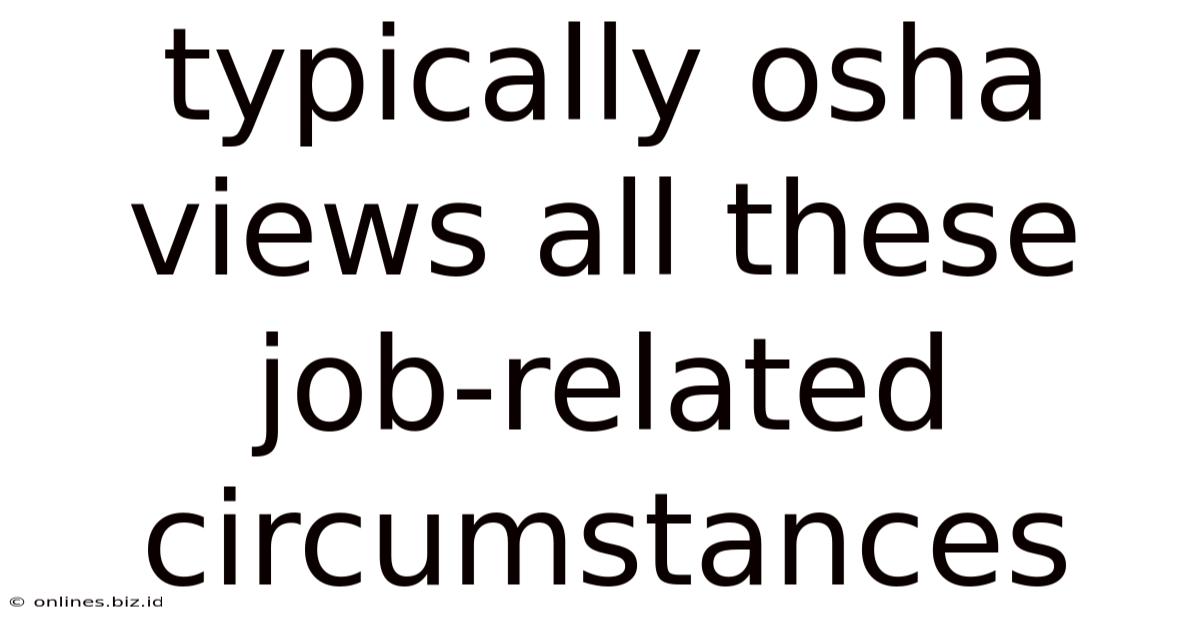
Table of Contents
OSHA's View on Job-Related Circumstances: A Comprehensive Guide
The Occupational Safety and Health Administration (OSHA) plays a crucial role in ensuring safe and healthful working conditions for millions of American workers. Understanding how OSHA views various job-related circumstances is vital for employers to maintain compliance and prevent workplace accidents. This comprehensive guide delves into OSHA's perspectives on a range of workplace scenarios, offering insights into their regulatory approach and the potential consequences of non-compliance.
OSHA's Mission and Regulatory Framework
At its core, OSHA's mission is to prevent work-related injuries, illnesses, and deaths. This overarching goal guides their interpretation and enforcement of regulations across numerous industries and work settings. OSHA achieves this through a multi-pronged approach involving:
- Developing and enforcing safety and health standards: These standards cover a broad spectrum of hazards, from fall protection and machine guarding to chemical exposure and respiratory protection.
- Providing education and training: OSHA offers numerous resources to help employers and employees understand their rights and responsibilities under the law.
- Conducting workplace inspections: Inspections are conducted to identify hazards and ensure compliance with established standards. These inspections can be triggered by employee complaints, fatalities, or other events.
- Imposing penalties for violations: Penalties range from warnings to significant fines, depending on the severity and nature of the violation. In extreme cases, employers can face criminal charges.
OSHA's regulatory framework is complex, encompassing numerous statutes, regulations, and interpretations. Understanding this framework is crucial for employers to navigate the often-challenging landscape of workplace safety.
OSHA's View on Specific Job-Related Circumstances
OSHA's perspective on job-related circumstances varies widely depending on the specific hazard, the industry, and the context of the situation. Let's examine some key areas:
1. Workplace Hazards and Risk Assessment
OSHA strongly emphasizes the importance of proactive hazard identification and risk assessment. Employers are expected to conduct thorough assessments to identify potential hazards in their workplaces, evaluate the associated risks, and implement appropriate control measures to mitigate those risks. This includes:
- Identifying physical hazards: This encompasses hazards such as falls, slips, trips, electrical hazards, machinery hazards, and fire hazards. OSHA has specific standards addressing each of these hazard categories.
- Identifying chemical hazards: OSHA's Hazard Communication Standard requires employers to inform employees about the hazards associated with the chemicals they handle. This includes providing Safety Data Sheets (SDS) and conducting employee training.
- Identifying ergonomic hazards: Ergonomic hazards relate to the design of the workplace and the tasks employees perform. Prolonged repetitive motions, awkward postures, and heavy lifting can lead to musculoskeletal disorders. OSHA provides guidance on ergonomic principles and best practices.
- Identifying biological hazards: Exposure to bloodborne pathogens, infectious diseases, and other biological agents poses significant risks in healthcare and other industries. OSHA's Bloodborne Pathogens Standard sets stringent requirements for handling these hazards.
- Identifying psychosocial hazards: While newer to the forefront, OSHA recognizes the impact of stress, harassment, and violence on worker health and safety. Addressing these psychosocial hazards requires a multifaceted approach that includes promoting a positive work environment and implementing effective policies to address harassment and violence.
2. Personal Protective Equipment (PPE)
OSHA views Personal Protective Equipment (PPE) as a critical component of a comprehensive safety program. However, PPE is considered a last line of defense, and its use should be coupled with engineering and administrative controls to minimize workplace hazards. OSHA's PPE standards specify the types of PPE required for various hazards and emphasize the importance of proper training, fit testing, and maintenance of PPE.
- Fall Protection: OSHA requires fall protection for workers at heights of six feet or more. This includes harness systems, guardrails, safety nets, and other fall protection measures.
- Respiratory Protection: When employees are exposed to airborne hazards, such as dust, fumes, or gases, appropriate respiratory protection must be provided and used correctly. This includes proper fit testing and training.
- Hearing Protection: In noisy environments, employers must provide and ensure the use of hearing protection to prevent noise-induced hearing loss.
- Eye and Face Protection: Appropriate eye and face protection is required to protect workers from flying objects, chemicals, and other eye and face hazards.
- Hand Protection: Gloves and other hand protection must be provided and used to prevent cuts, burns, and chemical exposure.
3. Training and Education
OSHA emphasizes the importance of adequate training and education for all employees. This includes training on hazard recognition, safe work practices, and the proper use of PPE. Effective training is essential to ensure that employees understand their rights and responsibilities under the law and can work safely without compromising their health. Training must be provided:
- Initially: Upon hiring or assignment to a new job.
- Periodically: To refresh knowledge and address changes in procedures or regulations.
- As needed: When new hazards are introduced or when incidents occur.
4. Emergency Action Plans
OSHA mandates the development and implementation of emergency action plans for most workplaces. These plans detail procedures for responding to various emergencies, including fires, evacuations, and medical emergencies. Effective emergency action plans are critical to ensure the safety and well-being of employees in the event of an emergency. They should include:
- Procedures for reporting emergencies: Clear procedures for notifying emergency responders and supervisors.
- Evacuation procedures: Clearly defined escape routes and assembly points.
- Emergency escape procedures: Training on how to safely exit the building during an emergency.
- Emergency response procedures: Procedures for dealing with specific hazards, such as fires or chemical spills.
- Training for all employees: Ensure all employees understand the plan and their roles in an emergency.
5. Recordkeeping and Reporting
OSHA requires employers to maintain accurate records of workplace injuries and illnesses. This data is used to track workplace safety trends and identify areas for improvement. Employers must also report certain workplace accidents and illnesses to OSHA, such as fatalities, hospitalizations, and amputations. Accurate recordkeeping is vital for:
- Tracking workplace injuries and illnesses: Identify patterns and trends to better understand workplace risks.
- Measuring the effectiveness of safety programs: Evaluate the effectiveness of safety interventions and identify areas for improvement.
- Complying with OSHA regulations: Failure to maintain accurate records can result in penalties.
- Providing information to OSHA: Facilitate OSHA inspections and investigations.
6. Inspections and Citations
OSHA conducts workplace inspections to ensure compliance with safety and health regulations. These inspections can be triggered by employee complaints, fatalities, or other events. During an inspection, an OSHA compliance officer will identify any violations and issue citations for non-compliance. Citations can result in penalties, ranging from warnings to significant fines. Employers should:
- Cooperate with OSHA inspections: Provide access to the workplace and relevant records.
- Correct violations promptly: Address any violations identified during the inspection.
- Appeal citations if necessary: Challenge citations if they believe they are unjustified.
7. Consequences of Non-Compliance
Non-compliance with OSHA regulations can have serious consequences for employers, including:
- Fines: Significant financial penalties can be levied for violations.
- Citations: Public records of violations can damage an employer's reputation.
- Increased insurance premiums: Higher workers' compensation premiums can result from a poor safety record.
- Loss of business: Customers may choose to do business with safer companies.
- Criminal charges: In some cases, severe violations can lead to criminal charges.
Conclusion
OSHA's view on job-related circumstances is grounded in the fundamental principle of protecting worker safety and health. By understanding OSHA's regulations, conducting thorough risk assessments, implementing effective safety programs, and maintaining accurate records, employers can create safer workplaces, reduce injuries and illnesses, and avoid the serious consequences of non-compliance. Proactive safety management not only protects workers but also fosters a more productive and positive work environment. Remember, a safe workplace is a productive workplace. Consistent adherence to OSHA's guidelines is crucial for any employer committed to creating a safe and healthy environment for their employees.
Latest Posts
Latest Posts
-
Draw The Structural Formula Of 4 5 Diisopropylnonane
May 12, 2025
-
Nihss Group B Answers 2024 Quizlet
May 12, 2025
-
Peis Are Activities Behaviors Or Circumstances That May Be Indicative
May 12, 2025
-
Plot Diagram For The Gift Of Magi
May 12, 2025
-
Examples Of An Iterative Launch Strategy Would Be
May 12, 2025
Related Post
Thank you for visiting our website which covers about Typically Osha Views All These Job-related Circumstances . We hope the information provided has been useful to you. Feel free to contact us if you have any questions or need further assistance. See you next time and don't miss to bookmark.