Victoria A Shift Manager In A Shoe Factory
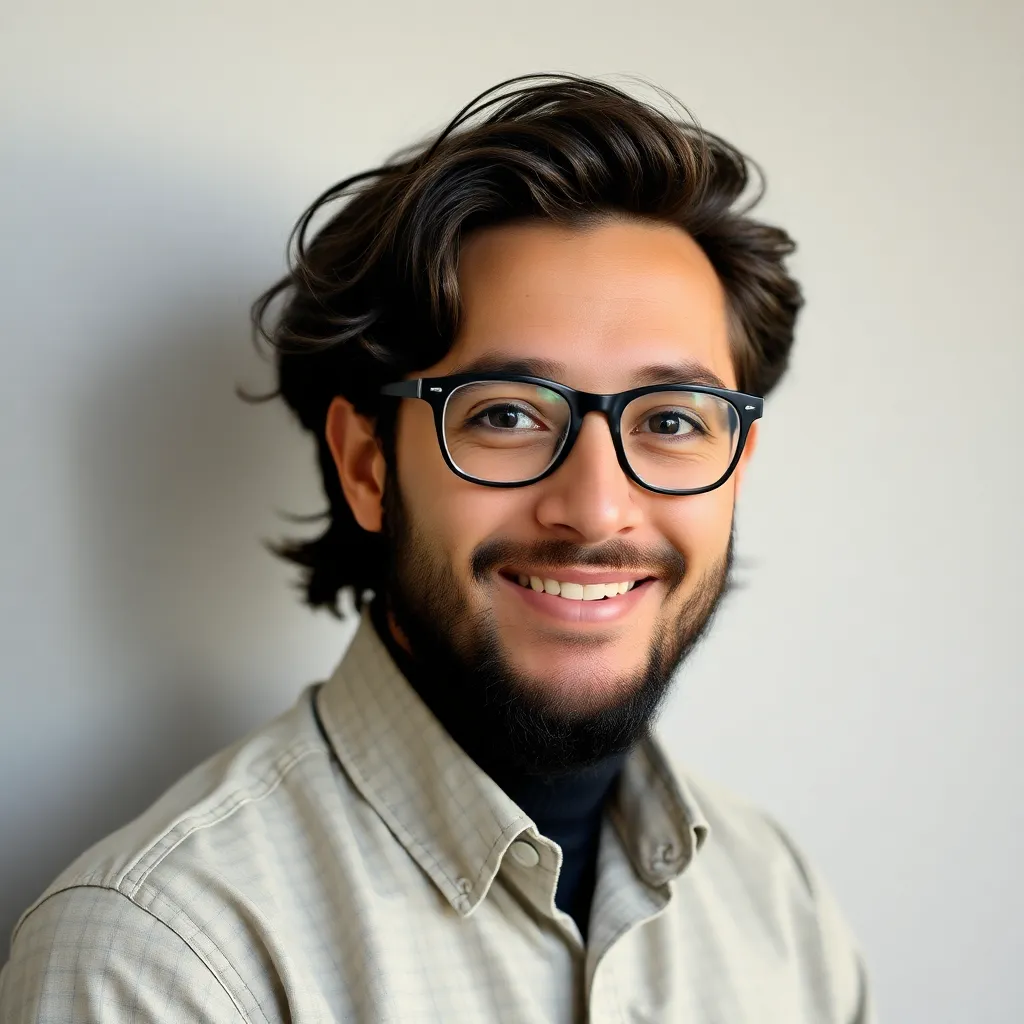
Onlines
Apr 25, 2025 · 6 min read

Table of Contents
Victoria: A Shift Manager in a Shoe Factory – A Day in the Life
Victoria’s alarm blared at 5:00 AM, a jarring sound that signaled the start of another day at the Acme Shoe Factory. She wasn't just any employee; Victoria was the shift manager, a role that demanded a unique blend of leadership, technical skill, and unwavering dedication. This wasn't about simply clocking in and clocking out; it was about orchestrating a complex ballet of human effort and machinery, all geared towards producing thousands of shoes each day.
The Early Bird Catches the… Production Line?
The first hour of Victoria's day was a whirlwind. Before the first worker even punched in, she was already on the factory floor, inspecting machinery, checking inventory levels, and ensuring the previous shift's cleanup was complete. This meticulous pre-shift inspection wasn't just about safety; it was about preventing costly production delays. A jammed machine or a shortage of raw materials could throw the entire day's schedule off kilter.
A Deep Dive into Pre-Shift Procedures:
- Equipment Check: Victoria meticulously examined each machine, from the automated stitching machines to the cutting presses, ensuring they were functioning optimally and safely. This involved checking for loose parts, lubricating moving components, and testing functionality. Any potential issues were immediately reported to maintenance.
- Materials Inventory: She verified the stock of leather, rubber, soles, laces, and other raw materials, comparing actual levels against the production plan for the day. Any discrepancies were flagged to prevent production bottlenecks.
- Team Briefing Preparation: While physically inspecting the factory, Victoria mentally reviewed the day's production goals and any anticipated challenges. This preparation ensured a smooth and efficient team briefing.
- Safety First: Victoria considered safety paramount. She walked the floor, checking for any potential hazards like spills, loose cables, or improperly stored materials, ensuring a safe working environment for her team.
Leading the Team: More Than Just Orders
At 6:00 AM, the first shift workers arrived. Victoria's role immediately shifted from meticulous inspection to dynamic leadership. The team briefing wasn't a dictatorial address; it was a collaborative discussion. Victoria outlined the day's production goals, but she also actively sought input from her team, addressing concerns and celebrating successes. Effective communication was, and always would be, her most valuable tool.
The Art of Team Management:
- Motivational Leadership: Victoria understood that her team weren't just cogs in a machine; they were individuals with unique skills, experiences, and motivations. She fostered a positive and supportive work environment, recognizing individual contributions and celebrating team achievements. Positive reinforcement was a key component of her leadership style.
- Problem-Solving Prowess: Inevitably, problems arose. A machine malfunctioned, a delivery was late, or a worker faced a challenging task. Victoria's ability to swiftly assess the situation, identify solutions, and delegate tasks effectively was crucial to maintaining production flow.
- Conflict Resolution: Disagreements and conflicts were inevitable in a diverse team. Victoria's diplomatic approach focused on active listening, understanding perspectives, and finding mutually acceptable solutions. She prioritized fair treatment and equitable opportunities for all team members.
- Training and Development: Victoria actively sought opportunities for her team's professional development. She identified skill gaps and provided training, mentoring less experienced workers, and empowering them to take on more responsibility. This investment in her team not only improved productivity but also fostered loyalty and job satisfaction.
The Heart of the Factory Floor: Production and Problem-Solving
The majority of Victoria's day was spent on the factory floor, navigating the intricate dance of production. She wasn't just observing; she was actively involved, assisting workers, troubleshooting problems, and making sure the production line ran smoothly. This hands-on approach allowed her to identify potential issues before they escalated into major problems.
A Day in the Life of Production:
- Monitoring Production Rates: Victoria kept a close eye on the production rate of each station, ensuring it aligned with the daily targets. Any slowdown was immediately investigated, helping pinpoint bottlenecks and resolving issues promptly.
- Quality Control: Maintaining high-quality standards was a critical aspect of Victoria's role. She conducted regular quality checks, ensuring each pair of shoes met Acme's stringent standards. Any defects were promptly addressed, minimizing waste and maintaining product integrity.
- Machine Maintenance: While dedicated maintenance personnel handled major repairs, Victoria frequently dealt with minor machine malfunctions, often providing quick fixes to keep the production line moving. Her knowledge of the machines was as crucial as her leadership skills.
- Inventory Management: Victoria’s role extended beyond the immediate production line. She actively monitored inventory levels, ensuring there was a continuous supply of raw materials and preventing production stoppages due to shortages.
Afternoon Challenges and Strategic Decision-Making
The afternoon brought its own set of challenges. Fatigue could set in for the team, impacting productivity. Victoria's ability to maintain morale and keep the team focused was critical. This often involved small gestures – a word of encouragement, a quick break, or simply acknowledging hard work – that collectively boosted team spirit.
Afternoon Challenges and Solutions:
- Maintaining Morale: As the day progressed, Victoria's focus shifted towards maintaining team morale. She recognized signs of fatigue and implemented strategies to keep the team motivated and energized.
- Unexpected Issues: Unexpected issues were a constant possibility – a machine breakdown, a sudden drop in material supply, or a worker injury. Victoria's ability to react quickly and effectively, finding solutions and minimizing disruption, was tested constantly.
- End-of-Shift Reporting: Before the end of the shift, Victoria compiled detailed reports summarizing the day's production, highlighting achievements, and noting any issues requiring attention. This reporting was crucial for communication with upper management and for planning future production schedules.
Beyond the Factory Floor: Collaboration and Continuous Improvement
Victoria's responsibilities extended beyond the factory floor. She collaborated with other departments, including purchasing, quality control, and maintenance, to ensure smooth operations. She actively sought opportunities for continuous improvement, implementing lean manufacturing principles to optimize workflows and minimize waste.
Expanding Responsibilities:
- Cross-Departmental Collaboration: Victoria worked closely with other departments to ensure efficient communication and coordination. This involved regular meetings, exchanging information, and proactively addressing potential issues before they impacted production.
- Continuous Improvement Initiatives: Victoria championed continuous improvement initiatives, focusing on lean manufacturing principles to identify waste, streamline processes, and improve overall efficiency.
- Data Analysis and Reporting: She utilized data analytics to track key performance indicators (KPIs), identifying trends and areas for improvement. This data-driven approach ensured informed decision-making and continuous optimization of production processes.
The End of the Shift: Reflection and Planning
As the final whistle blew at 4:00 PM, Victoria’s day wasn’t over. She meticulously reviewed the day's production records, noted any areas for improvement, and began planning for the next shift. This involved checking upcoming orders, anticipating potential challenges, and ensuring sufficient materials were available. This forward-thinking approach ensured smooth operations and maximized productivity.
The End of Shift Routine:
- Production Review and Analysis: Victoria meticulously reviewed production data, identifying bottlenecks, areas for improvement, and successes.
- Planning for the Next Shift: She prepared for the next shift by ensuring sufficient materials were available, addressing any unresolved issues, and ensuring a smooth handover.
- Communication with Upper Management: Victoria maintained regular communication with upper management, providing updates on production, highlighting challenges, and suggesting solutions.
Victoria's role as a shift manager at Acme Shoe Factory is more than just a job; it's a demanding yet rewarding career that demands a blend of technical skills, leadership abilities, and unwavering dedication. It's a story of teamwork, problem-solving, and the pursuit of continuous improvement. It's a story of Victoria.
Latest Posts
Latest Posts
-
Is At The Core Of Most Business Failures
Apr 25, 2025
-
Summary Of Chapter 14 The Giver
Apr 25, 2025
-
Summary Of Chapter 12 The Giver
Apr 25, 2025
-
My Neighbors In A Foreign Place Commonlit Answers
Apr 25, 2025
-
Which Of The Following Is True About Broadband Connections
Apr 25, 2025
Related Post
Thank you for visiting our website which covers about Victoria A Shift Manager In A Shoe Factory . We hope the information provided has been useful to you. Feel free to contact us if you have any questions or need further assistance. See you next time and don't miss to bookmark.