Welding Cable Must Be Spliced ____ The Electrode Holder.
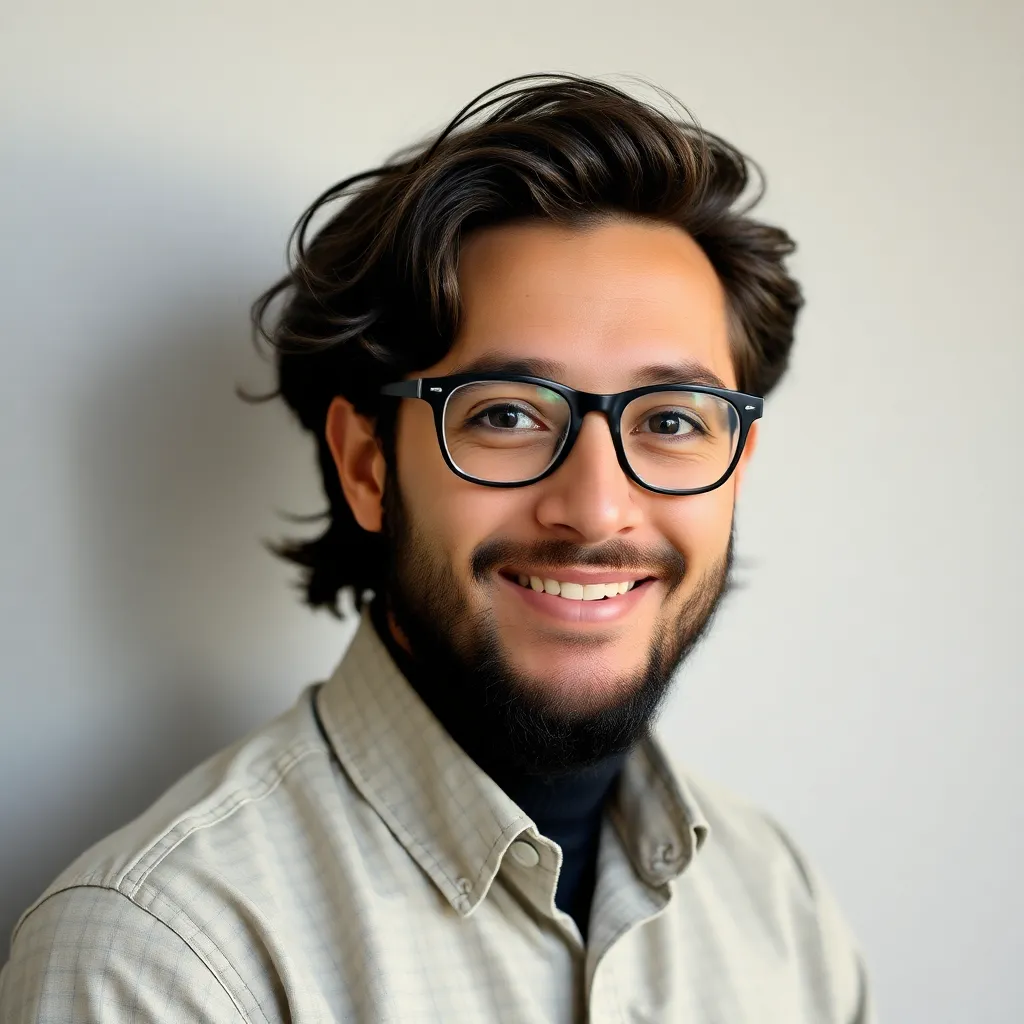
Onlines
Mar 17, 2025 · 6 min read

Table of Contents
Welding Cable Must Be Spliced Near the Electrode Holder: A Comprehensive Guide to Safety and Efficiency
Welding is a crucial process in various industries, from construction and manufacturing to automotive repair and shipbuilding. The safety and efficiency of welding operations heavily depend on the proper handling and maintenance of equipment, including welding cables. One frequently asked question revolves around the optimal location for splicing welding cables: Welding cable must be spliced near the electrode holder. This article delves deep into the reasons behind this practice, exploring the implications of incorrect splicing locations, and offering practical advice for safe and efficient cable management.
Why Splice Welding Cables Near the Electrode Holder?
The strategic placement of a splice near the electrode holder is not arbitrary; it's a safety and efficiency measure born from practical experience and understanding the inherent challenges of welding cable management.
1. Minimizing Cable Length and Resistance:
Welding cables carry high amperage currents. Longer cables mean higher resistance, leading to increased voltage drop. This voltage drop translates to reduced welding power, affecting the quality of the weld and potentially leading to inconsistent results. Splicing near the electrode holder minimizes the length of the high-current carrying portion of the cable, thus reducing resistance and maximizing power delivery to the welding arc. Think of it like this: a shorter, thicker pipe will carry more water (electricity) than a longer, thinner one.
2. Enhanced Flexibility and Maneuverability:
Welding often requires working in tight spaces or awkward positions. A long, heavy welding cable can be cumbersome and dangerous, increasing the risk of tripping, entanglement, and accidental contact with hot materials. By splicing near the electrode holder, you reduce the overall length of the heavily-used section of the cable, making it more manageable and improving maneuverability. This enhanced flexibility translates to greater control and improved safety, particularly in confined spaces or complex welding projects. Improved flexibility means increased safety and efficiency.
3. Reducing Cable Wear and Tear:
Welding cables experience significant wear and tear, especially near the electrode holder where they are subjected to bending, flexing, and abrasion. A shorter section of cable between the splice and the electrode holder means less overall stress on the cable itself. This translates to a longer lifespan for the cable, reducing the frequency of replacements and associated costs. Proper cable management is a key component of cost-effective welding.
4. Improved Safety:
The proximity of the splice to the electrode holder plays a crucial role in safety. If a splice fails, it's better for it to occur closer to the holder than further away. This minimizes the risk of a live conductor falling to the ground or creating a fire hazard. A localized failure near the holder is easier to identify and address, reducing the risk of serious accidents. Safety should always be the paramount concern in any welding operation.
5. Easier Inspection and Maintenance:
Regular inspection of welding cables is crucial to ensure safety and optimal performance. By splicing near the electrode holder, you make it easier to visually inspect the splice for signs of damage or wear and tear. Regular inspection and prompt repair or replacement of damaged cables prevent costly downtime and potential safety hazards. Preventative maintenance is crucial for efficient and safe welding operations.
The Dangers of Incorrect Splicing Locations:
Placing the splice too far away from the electrode holder presents significant risks, both to the quality of the weld and to the safety of the welder.
1. Voltage Drop and Poor Weld Quality:
As mentioned earlier, longer cables increase resistance and voltage drop. This can result in:
- Insufficient arc energy: leading to weak, inconsistent welds prone to cracking or failure.
- Inconsistent penetration: making the weld less strong and reliable.
- Increased spatter: causing wasted material and potential safety issues.
2. Increased Risk of Cable Damage:
A long cable section running from the power source to the far-off splice is subjected to more stress and strain during operation. This increased stress can lead to:
- Cable abrasion: causing damage to the insulation and potentially creating short circuits or electrical hazards.
- Cable breakage: leading to a complete interruption of the welding process and potential safety hazards.
- Excessive heating: causing premature failure of the cable insulation and posing a fire risk.
3. Safety Hazards:
Incorrectly placed splices can create significant safety concerns:
- Increased risk of electric shock: damaged cables can expose live wires, posing a risk of severe injury or fatality.
- Fire hazards: damaged insulation can overheat and cause fires, especially in the presence of flammable materials.
- Tripping hazards: long, trailing cables increase the risk of accidents, especially in busy work areas.
Best Practices for Splicing Welding Cables:
Proper splicing is crucial for both safety and performance. Here are some best practices to follow:
- Use appropriate connectors and materials: Choose connectors and insulating materials that are rated for the amperage and voltage of your welding machine. Never compromise on quality.
- Follow manufacturer's instructions: Carefully follow the manufacturer's instructions for connecting and installing connectors. Incorrect installation can compromise safety and performance.
- Ensure a clean and secure connection: Dirt, grease, or moisture can compromise the connection. Make sure the contact surfaces are clean and dry before connecting. Tighten the connectors to the manufacturer’s specified torque.
- Use proper crimping tools: For crimped connectors, use the correct crimping tool to ensure a secure connection. Improper crimping can weaken the connection, leading to failure.
- Protect the splice with proper insulation: Once the splice is made, ensure it is well-protected with heavy-duty heat-shrink tubing or other appropriate insulating materials. This protects the connection from moisture, abrasion, and other environmental factors.
- Regular inspection: Regularly inspect your welding cables and splices for any signs of damage or wear. Promptly repair or replace any damaged components. Proactive maintenance is key to preventing accidents.
Choosing the Right Cable for the Job:
Selecting the correct welding cable is just as crucial as proper splicing. Consider these factors:
- Amperage rating: Ensure the cable has an amperage rating that exceeds the maximum output of your welding machine.
- Cable length: Choose a cable length that minimizes unnecessary extra length while allowing sufficient flexibility.
- Cable insulation: Choose cables with robust insulation that can withstand the harsh conditions of the welding environment.
- Cable type: Select the appropriate cable type based on the welding process and environment. For example, some cables are better suited for outdoor use, while others are designed for specific welding processes.
Conclusion:
Splicing welding cables near the electrode holder is not simply a matter of convenience; it's a critical practice for maximizing safety and efficiency. Minimizing cable length reduces voltage drop, improves maneuverability, reduces cable wear and tear, and enhances overall safety. By following best practices for splicing and selecting appropriate cables, welders can ensure safe, efficient, and high-quality welding operations. Always prioritize safety, and remember that regular inspection and maintenance are essential for preventing accidents and maximizing the lifespan of your welding equipment. Ignoring these crucial steps can lead to serious consequences, including equipment damage, injury, and even fatalities. Prioritize safety. Prioritize proper splicing.
Latest Posts
Latest Posts
-
Introduction To Health Assessment 3 0 Test
Mar 17, 2025
-
Lord Of The Flies Student Workbook Answers Pdf
Mar 17, 2025
-
In Time Of The Butterflies Quotes
Mar 17, 2025
-
Which Of The Following Is Not Part Of Feminist Psychology
Mar 17, 2025
-
Which Puritan Value Most Influenced The Emerging Neoclassical Style
Mar 17, 2025
Related Post
Thank you for visiting our website which covers about Welding Cable Must Be Spliced ____ The Electrode Holder. . We hope the information provided has been useful to you. Feel free to contact us if you have any questions or need further assistance. See you next time and don't miss to bookmark.