Welding Principles And Applications 9th Edition Pdf Free Download
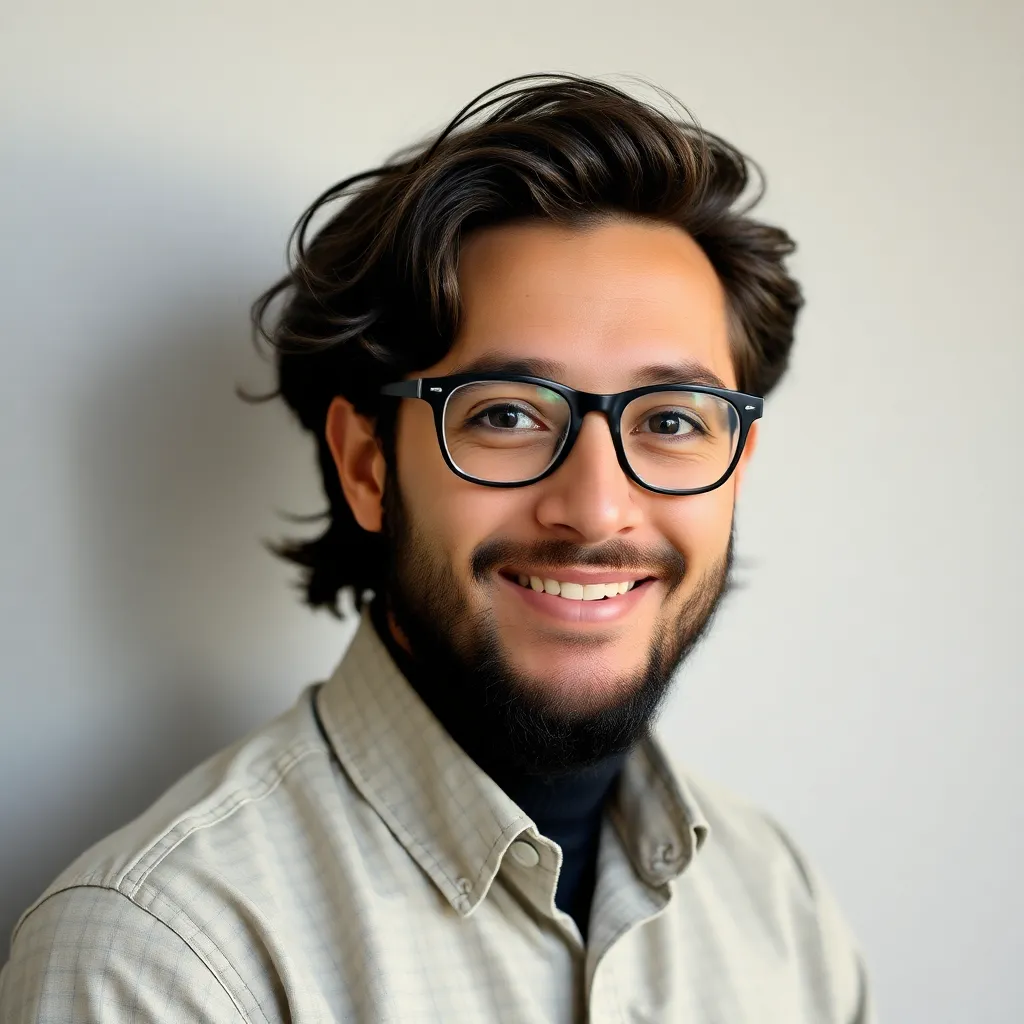
Onlines
Apr 05, 2025 · 7 min read
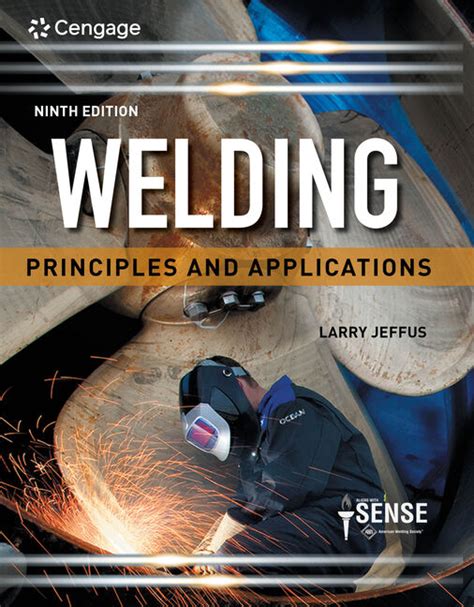
Table of Contents
Welding Principles and Applications 9th Edition PDF Free Download: A Comprehensive Guide
Finding a free download for the 9th edition of "Welding Principles and Applications" might prove difficult, as copyright restrictions protect the author's work. However, this comprehensive guide will provide you with an in-depth understanding of the principles and applications of welding, mirroring much of the content you'd find in a textbook. This article will equip you with the knowledge necessary to comprehend the core concepts and techniques, covering various welding processes, safety procedures, and application examples.
Understanding the Fundamentals of Welding
Welding is a fabrication process that joins materials, usually metals or thermoplastics, by causing coalescence. This means the materials are fused together, forming a strong bond at the molecular level. The process relies on heat, pressure, or a combination of both, often utilizing filler material to bridge the gap between the base materials. A thorough understanding of the fundamental principles is crucial for success in any welding application.
Key Concepts in Welding:
- Heat Source: The type of heat source (electric arc, gas flame, laser, etc.) dictates the welding process used. Different materials require different heat inputs to achieve proper fusion.
- Filler Metal: This material is added to the weld joint to fill gaps and strengthen the bond. The composition of the filler metal must be compatible with the base metals being joined.
- Base Metals: These are the materials being joined together. Their properties, including melting point, thermal conductivity, and chemical composition, influence the welding process selection and parameters.
- Weld Joint Design: The geometry of the joint significantly impacts the weld's strength and integrity. Proper joint design is essential to prevent defects and ensure a strong weld.
- Weld Pool: This molten metal pool is formed during the welding process. Controlling the weld pool's size, shape, and temperature is crucial for producing a high-quality weld.
- Shielding Gas: Many welding processes require a shielding gas to protect the weld pool from atmospheric contamination, which can lead to defects.
- Welding Parameters: These include variables such as current, voltage, travel speed, and preheat temperature. Accurate control of these parameters is essential for consistent weld quality.
Major Welding Processes: A Detailed Overview
Numerous welding processes exist, each with its own advantages and disadvantages. The choice of process depends on factors such as the materials being welded, the joint design, the required weld quality, and the available equipment. Let's explore some of the most common processes:
1. Shielded Metal Arc Welding (SMAW) – Stick Welding:
SMAW, commonly known as stick welding, uses a consumable electrode coated with flux. The electrode melts, providing both filler metal and shielding gas. It's a versatile and relatively inexpensive process, suitable for various materials and applications. However, it's susceptible to porosity (gas bubbles) and requires considerable operator skill.
Advantages: Portable, inexpensive equipment, versatile in materials. Disadvantages: Relatively slow process, produces spatter, susceptible to porosity.
2. Gas Metal Arc Welding (GMAW) – MIG Welding:
GMAW, or MIG welding, uses a continuous wire electrode fed into a weld pool. A shielding gas protects the weld pool. This process is highly productive and produces high-quality welds. It's widely used in various industries, from automotive to shipbuilding.
Advantages: High deposition rates, good quality welds, relatively easy to learn. Disadvantages: Requires shielding gas, not suitable for all materials.
3. Gas Tungsten Arc Welding (GTAW) – TIG Welding:
GTAW, or TIG welding, uses a non-consumable tungsten electrode to generate the welding arc. Filler metal is added separately. This process produces exceptionally clean and precise welds, making it ideal for critical applications. However, it's relatively slow and requires a skilled operator.
Advantages: High-quality welds, excellent control, precise welds. Disadvantages: Relatively slow, requires skilled operator, more expensive equipment.
4. Flux-Cored Arc Welding (FCAW):
FCAW uses a tubular electrode filled with flux and filler metal. The flux provides shielding and promotes arc stability. This process is highly productive and well-suited for outdoor applications due to its self-shielding capability.
Advantages: High deposition rates, good penetration, less sensitive to wind. Disadvantages: Can produce more spatter than GMAW, less precise than GTAW.
5. Submerged Arc Welding (SAW):
SAW is a high-deposition-rate process where the arc is submerged in a blanket of granular flux. This process is highly productive and well-suited for mass production applications.
Advantages: High deposition rate, excellent penetration, less susceptible to atmospheric contamination. Disadvantages: Requires specialized equipment, less versatile than other processes.
6. Resistance Welding:
Resistance welding uses electrical resistance to heat and join materials. Common resistance welding methods include spot welding, seam welding, and projection welding. It's a fast and efficient process suitable for mass production.
Advantages: High speed, efficient, no filler material needed. Disadvantages: Limited to specific materials and joint geometries, requires specialized equipment.
Welding Safety: A Critical Aspect
Welding involves significant safety hazards, including burns, electric shock, eye injuries, and respiratory problems. Proper safety precautions are essential to protect welders and those working nearby.
Essential Safety Measures:
- Personal Protective Equipment (PPE): Welders must always use appropriate PPE, including welding helmets with appropriate shade lenses, welding gloves, protective clothing, and respiratory protection.
- Fire Prevention: Welding often involves sparks and molten metal, creating a fire hazard. Flammable materials should be kept away from the welding area, and appropriate fire extinguishers should be readily available.
- Ventilation: Welding fumes can be hazardous. Adequate ventilation is crucial to prevent the buildup of harmful gases and fumes.
- Electrical Safety: Welding equipment operates at high voltages. Welders must be properly trained in electrical safety procedures.
- Eye Protection: The intense light emitted during welding can cause severe eye damage. Always use appropriate eye protection.
- Emergency Procedures: Welders should be aware of the emergency procedures in case of accidents, including how to use fire extinguishers and first-aid equipment.
Applications of Welding in Various Industries
Welding is a vital process across numerous industries, playing a key role in manufacturing, construction, and repair.
1. Automotive Industry:
Welding is essential for assembling car bodies and chassis, joining various metal components. Processes such as spot welding, MIG welding, and laser welding are commonly used.
2. Construction Industry:
Welding is used extensively in constructing steel structures, bridges, and pipelines. SMAW, GMAW, and FCAW are frequently employed for this purpose.
3. Aerospace Industry:
Welding is critical in fabricating aircraft and spacecraft components, requiring precise and high-quality welds. GTAW is frequently used due to its ability to produce high-quality welds.
4. Shipbuilding Industry:
Welding plays a vital role in constructing ships and other marine structures. SMAW, GMAW, and SAW are commonly used due to their high deposition rates.
5. Manufacturing Industry:
Welding is used extensively in manufacturing various products, including machinery, equipment, and consumer goods. A variety of welding processes are employed depending on the specific application.
Advanced Welding Techniques and Considerations
As technology advances, new welding techniques continue to emerge, leading to improved efficiency, precision, and weld quality.
1. Laser Welding:
Laser welding uses a highly focused laser beam as a heat source. It offers high precision and speed, making it ideal for intricate and critical applications.
2. Electron Beam Welding (EBW):
EBW uses a high-velocity beam of electrons as a heat source. It's a high-precision process often used in vacuum environments for critical applications, such as aerospace components.
3. Friction Stir Welding (FSW):
FSW is a solid-state welding process that uses friction to generate heat and join materials. It doesn't involve melting, making it ideal for materials susceptible to cracking or distortion during conventional welding.
Conclusion
Welding is a crucial fabrication process with applications spanning a wide range of industries. A thorough understanding of welding principles, processes, and safety procedures is essential for anyone involved in welding. While accessing specific textbooks like the "Welding Principles and Applications, 9th Edition" PDF might require purchasing the official version due to copyright restrictions, this comprehensive guide has provided a detailed overview of the core concepts and applications, effectively bridging the information gap for learners and professionals alike. Remember, continuous learning and adherence to safety standards are paramount in the field of welding.
Latest Posts
Latest Posts
-
The Two Main Divisions Of The Trade Industry Are
Apr 05, 2025
-
The Story Of Us Episode 3 Westward Answers
Apr 05, 2025
-
Advanced Hardware Lab 1 4 Use Tools From The Technicians Toolkit
Apr 05, 2025
-
How Many Chapters Are In It
Apr 05, 2025
-
4 6 Isosceles And Equilateral Triangles Worksheet
Apr 05, 2025
Related Post
Thank you for visiting our website which covers about Welding Principles And Applications 9th Edition Pdf Free Download . We hope the information provided has been useful to you. Feel free to contact us if you have any questions or need further assistance. See you next time and don't miss to bookmark.