What Are Engineered Plans For Motors Pumps
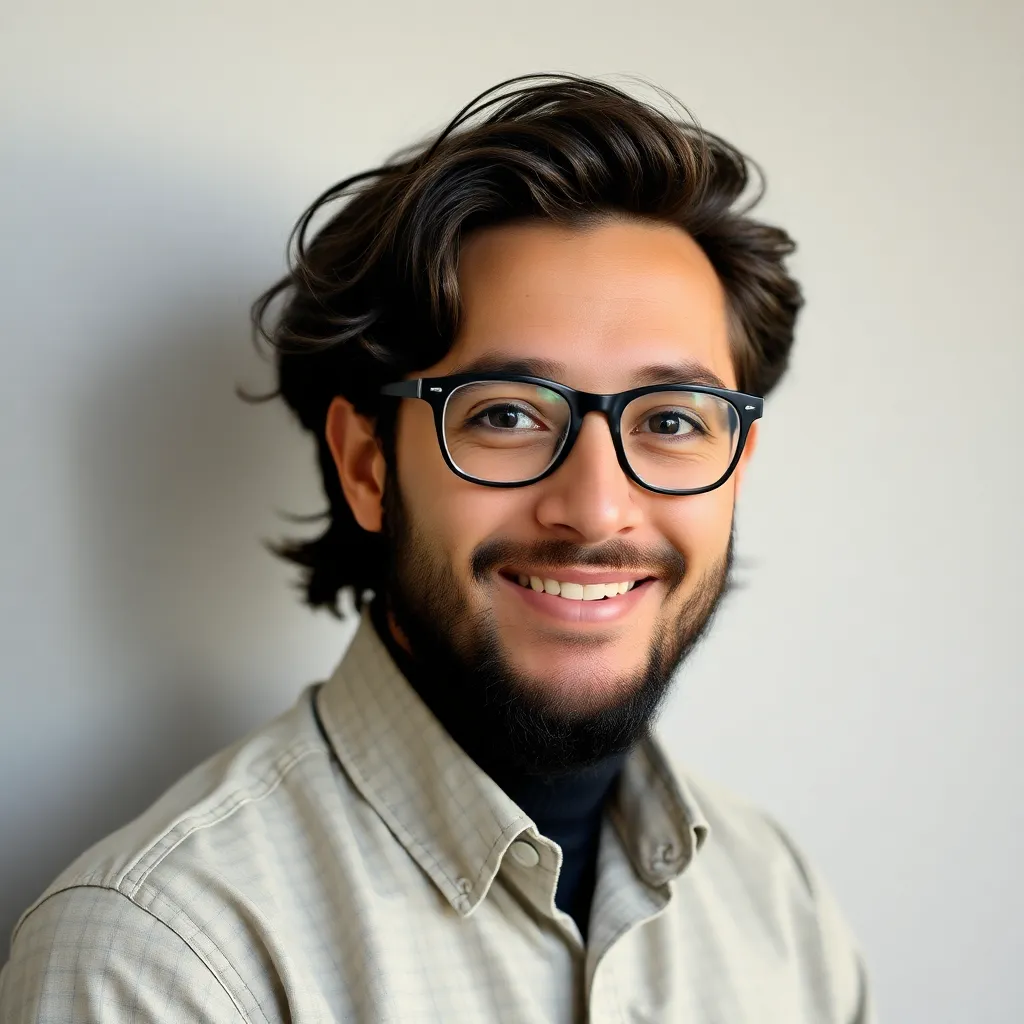
Onlines
May 10, 2025 · 6 min read
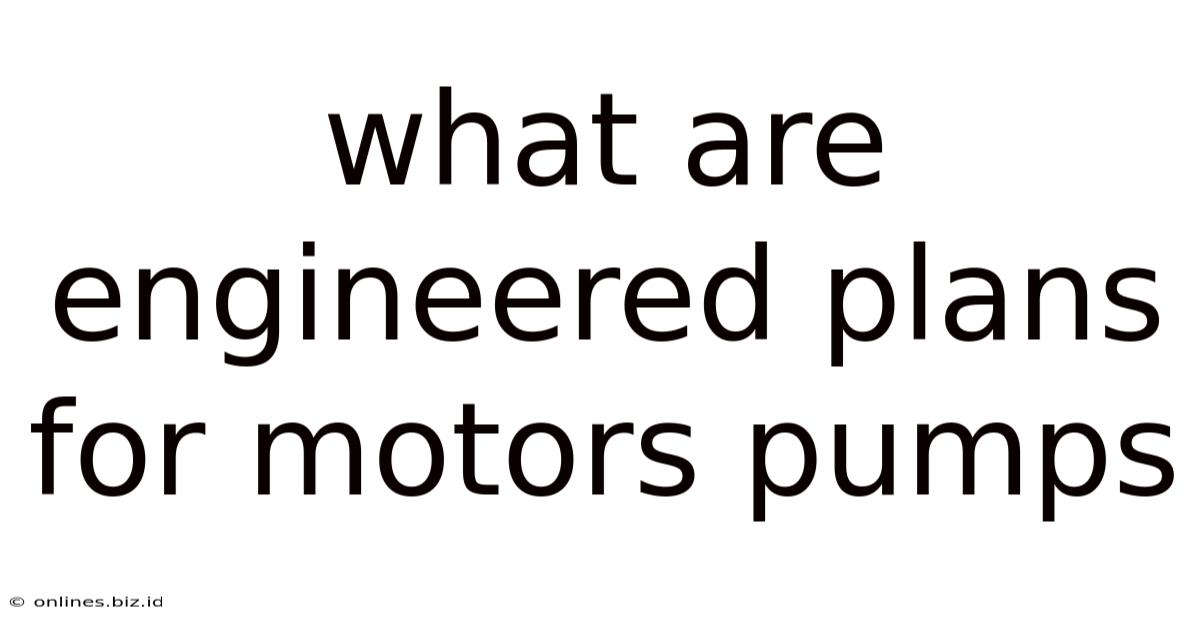
Table of Contents
Engineered Plans for Motors and Pumps: A Comprehensive Guide
Engineered plans for motors and pumps are crucial for ensuring efficient, reliable, and safe operation within any system. These plans go far beyond a simple schematic; they encompass detailed specifications, calculations, and analyses necessary to select, integrate, and maintain these critical components. This comprehensive guide delves into the various aspects of creating robust engineered plans for motors and pumps, covering everything from initial assessment to ongoing maintenance considerations.
I. Understanding the Scope of Engineered Plans
An engineered plan for motors and pumps isn't a single document but a collection of interrelated components, all working together to define a complete system. Key aspects include:
1. System Requirements Definition: The Foundation
Before any design work begins, a thorough understanding of the system's requirements is paramount. This includes:
- Flow Rate: The volume of fluid to be moved per unit of time (e.g., gallons per minute, liters per second).
- Head Pressure: The vertical distance the fluid needs to be lifted, along with frictional losses within the piping system.
- Fluid Properties: Viscosity, density, temperature, and any corrosive or abrasive characteristics.
- Operating Conditions: Ambient temperature, duty cycle (continuous, intermittent), and potential environmental hazards.
- Power Requirements: The energy needed to achieve the desired flow rate and head pressure.
- Safety Standards: Compliance with relevant industry regulations and safety codes.
2. Motor Selection: Powering the System
Choosing the right motor is critical for efficiency and longevity. Considerations include:
- Motor Type: Various types exist, including induction motors (most common), synchronous motors, and DC motors. Each has its own strengths and weaknesses in terms of efficiency, cost, and controllability.
- Power Rating: Must meet or exceed the calculated power requirements, with a safety margin to account for unforeseen circumstances.
- Voltage and Frequency: Must match the available power supply.
- Enclosure Type: Protection against environmental factors such as dust, moisture, and corrosive gases.
- Efficiency Rating: Higher efficiency ratings translate to lower operating costs and reduced environmental impact. Look for motors with high IE (International Efficiency) ratings.
3. Pump Selection: The Heart of the System
The pump is the core component, responsible for moving the fluid. Careful selection is crucial:
- Pump Type: Centrifugal pumps are the most common, but others like positive displacement pumps (e.g., piston, gear, diaphragm) may be more suitable depending on the application.
- Performance Curves: These curves illustrate the relationship between flow rate, head pressure, and power consumption. They are essential for selecting a pump that meets the system requirements while operating at its most efficient point.
- Materials of Construction: Must be compatible with the fluid being pumped, considering corrosion resistance, wear resistance, and temperature limitations.
- Seal Type: Ensures that the pumped fluid doesn't leak out of the pump. Various seal types exist, each with its own advantages and disadvantages in terms of reliability and maintenance.
4. Piping System Design: Ensuring Efficient Flow
The piping system is just as critical as the pump and motor. Proper design ensures efficient fluid transport and minimizes energy losses. Key aspects include:
- Pipe Sizing: Determining the appropriate pipe diameter to minimize pressure drop and maximize flow.
- Pipe Material: Selecting a material that is compatible with the fluid and operating conditions.
- Valves and Fittings: Selecting the appropriate valves and fittings for control and safety.
- Pressure Drop Calculations: Accurate calculation of pressure drop throughout the system is crucial to ensure that the pump can deliver the required flow rate and head pressure.
II. Detailed Calculations and Analyses: The Engineering Backbone
The engineered plans involve detailed calculations and analyses to ensure optimal design and performance. These include:
1. Hydraulic Calculations: Flow and Pressure
Hydraulic calculations are fundamental to ensure the pump and piping system can handle the required flow rate and pressure. These calculations involve:
- System Curve: A graphical representation of the relationship between flow rate and head pressure for the entire system.
- Pump Curve Matching: Overlaying the pump curve onto the system curve to find the operating point of the system.
- NPSH Calculations: Net Positive Suction Head (NPSH) calculations are vital to prevent cavitation (formation of vapor bubbles) in the pump, which can lead to damage and reduced efficiency.
2. Mechanical Calculations: Stress and Vibration
Mechanical calculations ensure that the components can withstand the stresses and vibrations during operation. These calculations consider:
- Shaft Design: Determining the appropriate shaft diameter to withstand bending moments and torsional loads.
- Bearing Selection: Selecting appropriate bearings to support the rotating components and minimize wear.
- Vibration Analysis: Analyzing the potential for vibration and taking steps to mitigate it.
3. Electrical Calculations: Power and Control
Electrical calculations ensure that the motor and control system are properly sized and protected. These calculations include:
- Motor Starting Current: Determining the starting current to ensure that the power supply can handle the initial surge.
- Motor Overload Protection: Implementing appropriate overload protection to prevent motor damage.
- Control System Design: Designing a control system to start, stop, and regulate the speed of the motor and pump.
III. Integrating the System: A Holistic Approach
The engineered plans must integrate all components into a cohesive, functional system. This involves:
1. Component Selection and Integration: Compatibility and Efficiency
Careful selection of each component – motor, pump, piping, valves – is vital to ensure compatibility and efficiency. Mismatched components can lead to reduced performance, increased wear, and potential failure.
2. Baseplate Design: Structural Support
The baseplate provides structural support for the pump and motor, ensuring proper alignment and minimizing vibration. The design must consider weight, forces, and stability.
3. Instrumentation and Control: Monitoring and Regulation
Instrumentation, including pressure gauges, flow meters, and temperature sensors, provides crucial data for monitoring system performance. The control system allows for regulation of flow rate, pressure, and other parameters.
IV. Maintenance and Lifecycle Considerations: Long-Term Efficiency
The engineered plans should address long-term maintenance and lifecycle considerations. This includes:
1. Maintenance Schedules: Preventative Measures
Developing a preventative maintenance schedule minimizes downtime and extends the lifespan of the components. This schedule should include regular inspections, lubrication, and component replacement.
2. Spare Parts Inventory: Minimizing Downtime
Having a sufficient inventory of spare parts on hand minimizes downtime in case of component failure. The inventory should be based on the criticality of the components and their expected lifespan.
3. Documentation and Manuals: A Comprehensive Guide
Comprehensive documentation, including detailed drawings, specifications, and maintenance manuals, is essential for ease of operation, maintenance, and troubleshooting.
V. Conclusion: The Importance of Comprehensive Engineered Plans
Creating robust engineered plans for motors and pumps is essential for ensuring efficient, reliable, and safe operation. These plans go beyond simple schematics, encompassing detailed calculations, analyses, and lifecycle considerations. Investing in comprehensive engineering upfront translates to significant long-term benefits, including reduced downtime, improved efficiency, lower operating costs, and enhanced safety. By meticulously addressing all aspects, from system requirements to ongoing maintenance, you ensure the optimal performance of your motor and pump systems.
Latest Posts
Latest Posts
-
Research On Interviewing Has Shown That
May 10, 2025
-
Which Of The Following Violates The Rules For Curved Arrows
May 10, 2025
-
Match The Fungal Structure With Its Description
May 10, 2025
-
Brave New World Chapter 17 Summary
May 10, 2025
-
A Relatively Stable Pleasing Combination Of Notes
May 10, 2025
Related Post
Thank you for visiting our website which covers about What Are Engineered Plans For Motors Pumps . We hope the information provided has been useful to you. Feel free to contact us if you have any questions or need further assistance. See you next time and don't miss to bookmark.