What Is Wrong With The Mechanism Shown
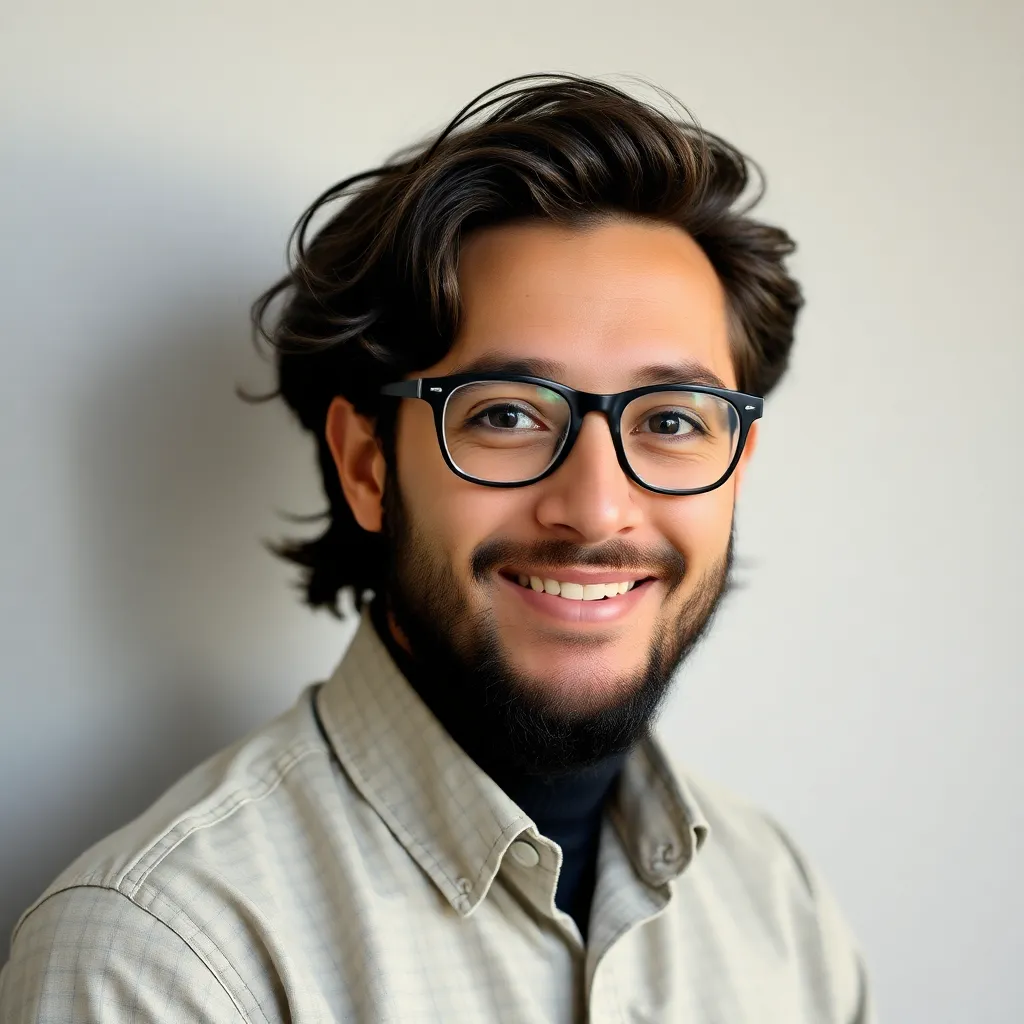
Onlines
Mar 16, 2025 · 5 min read
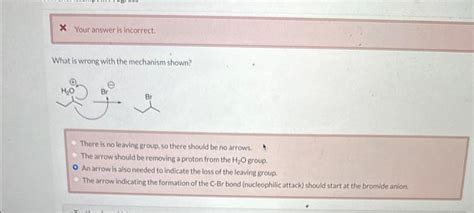
Table of Contents
What's Wrong with the Mechanism Shown? A Deep Dive into Mechanical Failure Analysis
This article delves into the critical process of mechanical failure analysis, focusing on identifying flaws within a given mechanism. Since no specific mechanism is provided, we will explore common issues affecting various mechanical systems, providing a framework for analyzing any presented design. We'll cover material selection, design flaws, manufacturing defects, operational limitations, and preventative maintenance strategies. Understanding these aspects is crucial for engineers, designers, and anyone involved in the lifecycle of mechanical systems.
The Importance of Thorough Mechanism Analysis
Before we dive into specific problems, it's important to understand the why behind thorough analysis. A seemingly minor flaw can lead to catastrophic failure, resulting in:
- Financial losses: Repair costs, downtime, and potential product recalls can be incredibly expensive.
- Safety hazards: Malfunctioning mechanisms can cause injuries or even fatalities.
- Reputational damage: Failure to deliver reliable products can severely impact a company's image and customer trust.
- Environmental impact: Failures can lead to environmental damage, especially in large-scale industrial applications.
Therefore, meticulous analysis is not just good practice; it's essential for safety, efficiency, and long-term sustainability.
Common Problems in Mechanical Mechanisms: A Comprehensive Overview
Let's explore some of the most frequent culprits behind mechanical failures:
1. Material Selection and Degradation:
- Incorrect Material Choice: Selecting a material unsuitable for the operating conditions (temperature, stress, corrosion, etc.) is a primary cause of failure. For example, using a low-carbon steel in a highly corrosive environment will lead to rapid deterioration. Understanding material properties – tensile strength, yield strength, fatigue resistance, and creep resistance – is critical.
- Material Degradation: Even with proper material selection, materials can degrade over time due to factors like fatigue, creep, corrosion, and wear. Fatigue occurs when a material is subjected to repeated cyclic loading, eventually leading to crack initiation and propagation. Creep is a time-dependent deformation under constant stress, often observed at high temperatures. Corrosion weakens materials through chemical or electrochemical reactions, while wear is the gradual removal of material due to friction. Regular inspection and preventative maintenance are crucial to mitigating these issues.
2. Design Flaws:
- Stress Concentrations: Sharp corners, abrupt changes in cross-section, and holes can create stress concentrations, leading to premature failure. Proper design techniques – such as using fillets and generous radii – can significantly reduce these concentrations.
- Inadequate Bearing Selection: Choosing inappropriate bearings for the load, speed, and operating environment can result in premature bearing failure, leading to system malfunction. Understanding bearing types and their capabilities is paramount.
- Insufficient Safety Factors: Designs should incorporate safety factors to account for uncertainties in material properties, loads, and manufacturing tolerances. A proper safety factor ensures the mechanism can withstand unexpected stresses.
- Resonance and Vibration: If the natural frequency of a component matches the excitation frequency, resonance can occur, leading to excessive vibrations and potentially catastrophic failure. Proper design and analysis techniques can help avoid resonance.
- Oversimplification: Sometimes, designers may oversimplify a mechanism to reduce cost or complexity, overlooking critical factors that can compromise functionality and durability.
3. Manufacturing Defects:
- Improper Heat Treatment: Incorrect heat treatment can alter the material's microstructure, reducing its strength and toughness. Rigorous quality control during manufacturing is essential to ensure proper heat treatment.
- Welding Defects: Poor welds can create stress concentrations and weaken the structure. Non-destructive testing (NDT) techniques like radiography and ultrasonic testing are used to detect welding defects.
- Surface Finish Issues: Rough surface finishes can promote fatigue crack initiation and wear. Proper machining and finishing techniques are necessary to achieve optimal surface quality.
- Dimensional Inaccuracies: Inaccuracies in dimensions can lead to misalignments, increased stress, and premature failure. Precise manufacturing processes and quality control are vital.
4. Operational Limitations:
- Overloading: Exceeding the design load capacity can lead to immediate or gradual failure. Proper load monitoring and control are crucial.
- Improper Lubrication: Inadequate lubrication leads to increased friction, wear, and heat generation, accelerating component failure. Regular lubrication and maintenance are essential.
- Environmental Factors: Extreme temperatures, humidity, corrosive atmospheres, and dust can significantly impact the lifespan of mechanical components. Designing mechanisms to withstand these environmental factors is critical.
- Lack of Maintenance: Neglecting regular maintenance can lead to gradual deterioration and eventual catastrophic failure. Implementing a preventative maintenance program is vital for the longevity of any mechanical system.
5. Assembly Errors:
- Incorrect Part Installation: Incorrect installation of components can lead to misalignment, binding, and premature wear. Clear and detailed assembly instructions are crucial.
- Missing or Damaged Components: Missing or damaged parts during assembly will obviously result in malfunction or failure. Thorough inspection and quality control during assembly are essential.
- Improper Torqueing: Applying incorrect torque during assembly can damage components or compromise the structural integrity of the mechanism. Proper torque specifications must be followed.
Analyzing a Mechanism for Potential Problems: A Step-by-Step Guide
Analyzing a mechanism requires a systematic approach:
- Identify the Mechanism's Function: Clearly define the intended purpose and operating conditions of the mechanism.
- Create a Free Body Diagram (FBD): Draw a diagram showing all forces and moments acting on each component.
- Perform Stress Analysis: Calculate the stresses on each component under various operating conditions. Consider both static and dynamic loads.
- Assess Material Selection: Evaluate the suitability of the selected materials for the anticipated stresses, temperatures, and environmental conditions.
- Examine the Design for Potential Weaknesses: Look for stress concentrations, potential points of failure, and inadequate safety factors.
- Consider Manufacturing Processes: Assess the impact of manufacturing processes on the final product's quality and integrity.
- Evaluate Operational Limitations: Determine the mechanism's capacity and limitations under various operating conditions.
- Develop a Preventative Maintenance Plan: Establish a schedule for regular inspections, lubrication, and component replacement.
Conclusion: Preventing Mechanical Failures Through Proactive Measures
Preventing mechanical failures isn't solely about reacting to problems; it's about implementing proactive strategies. By carefully considering material selection, meticulously designing for durability, ensuring proper manufacturing processes, and establishing a rigorous maintenance program, you can significantly enhance the reliability and lifespan of your mechanical systems. Remember, a thorough understanding of the potential failure points within a mechanism is the first step towards creating robust, safe, and long-lasting designs. The cost of prevention is far less than the cost of failure. Regular inspection, meticulous documentation, and continuous improvement are key components of a proactive approach to maintaining mechanical integrity. By investing time and resources in these preventative measures, you are safeguarding against costly downtime, safety hazards, and reputational damage, paving the way for more successful and sustainable engineering endeavors.
Latest Posts
Latest Posts
-
4 3 Activity Firewall And Access Control
Mar 16, 2025
-
Gathering Accurate Data On Water Flow
Mar 16, 2025
-
Add The Text Slow Start To The Shape
Mar 16, 2025
-
No Portion Of This Ad Shows What This Thing Does
Mar 16, 2025
-
How Much Does A Sandwich Bag Weigh
Mar 16, 2025
Related Post
Thank you for visiting our website which covers about What Is Wrong With The Mechanism Shown . We hope the information provided has been useful to you. Feel free to contact us if you have any questions or need further assistance. See you next time and don't miss to bookmark.