Which Item Must Be Rejected When Inspecting A Delivery
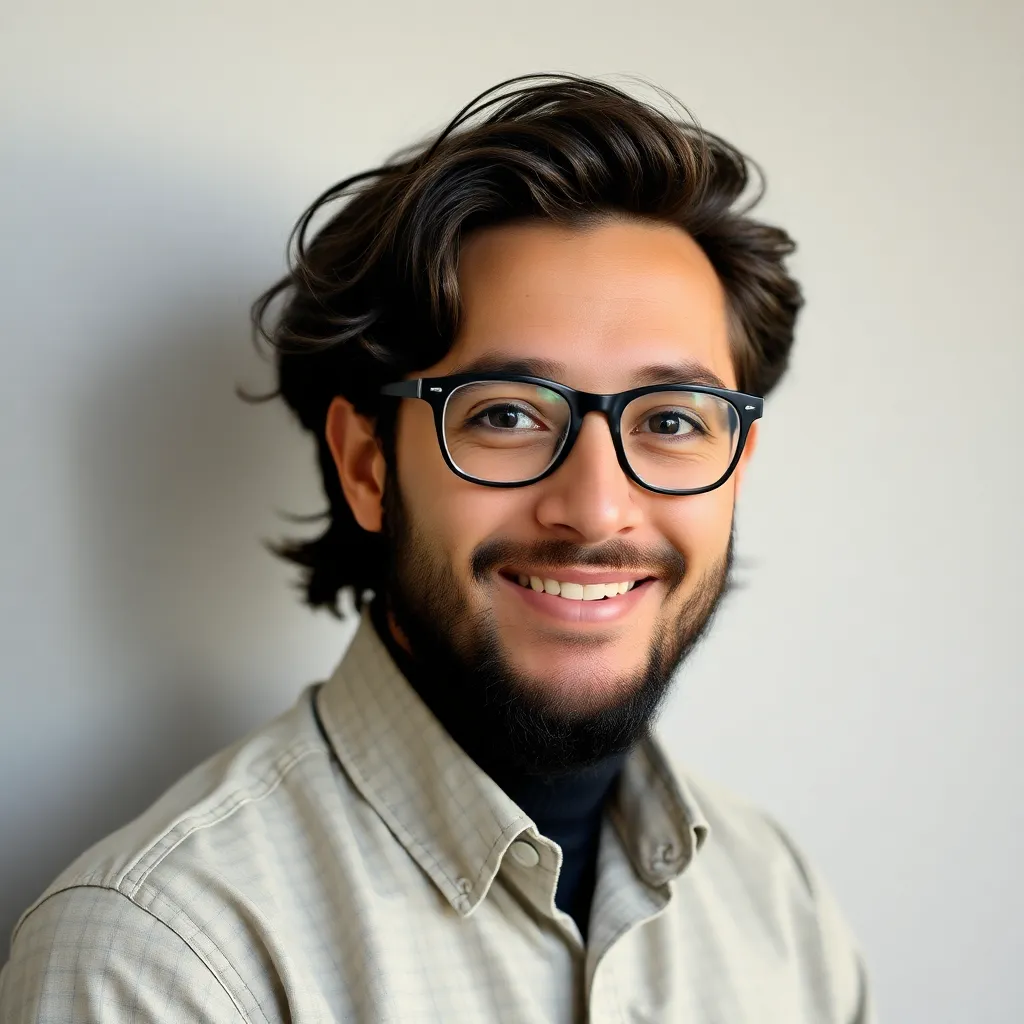
Onlines
Apr 25, 2025 · 5 min read

Table of Contents
Which Items Must Be Rejected When Inspecting a Delivery?
Receiving a delivery is only half the battle; ensuring the goods are in perfect condition is the other, equally crucial half. A thorough inspection upon delivery is paramount for protecting your business from potential losses, delays, and damaged reputations. Rejecting faulty goods promptly is a vital part of this process. This comprehensive guide will detail the various situations and specific criteria that warrant rejection of a delivery, focusing on different product categories and common issues.
Understanding Your Rights and Responsibilities
Before diving into specifics, it's crucial to understand your legal rights and responsibilities regarding damaged or faulty goods. Your rights depend heavily on the terms of your contract with the supplier. However, most jurisdictions offer basic consumer protections, ensuring that goods are of merchantable quality and fit for their intended purpose. Always thoroughly review your purchase order and any accompanying documentation. Documentation is key to proving your case if disputes arise.
Key Factors Determining Rejection
Several factors contribute to the decision to reject a delivery. These factors encompass the condition of the goods themselves, the discrepancies between the order and the delivery, and the overall impact on your operations. Let's explore these in detail:
1. Visible Damage to Packaging
The first thing to inspect is the packaging. Significant damage, such as:
- Crushed or severely dented boxes: This indicates potential internal damage to the goods. Even if the contents appear intact, the structural integrity might be compromised.
- Torn or ripped packaging: This exposes the contents to damage from moisture, dirt, or other contaminants.
- Packaging that is excessively wet or shows signs of water damage: This could indicate exposure to rain or flooding during transit, leading to spoilage or malfunction of the goods.
- Packaging that is improperly sealed or tampered with: This raises concerns about theft or product substitution. Reject immediately and report to the authorities if you suspect theft.
2. Discrepancies Between Order and Delivery
Accuracy is vital. Compare the delivery against your purchase order, paying close attention to:
- Quantity: Check if the number of items received matches the quantity ordered. Shortages are a common issue.
- Item Numbers: Ensure each item received corresponds to the specific item number on the order. Incorrect items are a serious problem.
- Product Specifications: Verify that the delivered items meet the specifications outlined in your order, including size, color, and other relevant details. Incorrect specifications make the goods unsuitable for their intended purpose.
- Batch Numbers or Serial Numbers: For specific items, check that the batch or serial numbers match the information on your purchase order. This is crucial for tracking and warranty purposes.
3. Damaged or Defective Goods
Beyond packaging, thoroughly inspect the goods themselves. Reject items exhibiting:
- Physical damage: Scratches, dents, cracks, or broken parts are clear indicators of damage.
- Malfunction: If the item is electronic or mechanical, test its functionality. Reject any item that fails to operate as expected.
- Defective components: Inspect for missing parts, faulty wiring, or other manufacturing defects.
- Expired goods: Check the expiry dates of perishable or time-sensitive items. Expired goods are unusable and should be rejected.
- Poor quality: If the goods are of inferior quality compared to samples or previous orders, you have grounds for rejection. This could include substandard materials, poor workmanship, or inconsistencies in quality.
4. Documentation Issues
Errors in the accompanying documentation can also justify rejection. These include:
- Missing documentation: Delivery notes, invoices, and certificates of authenticity are essential.
- Incorrect documentation: Check that the documentation accurately reflects the items received.
- Incomplete documentation: Incomplete information can hinder your ability to track and manage the goods.
Rejection Procedures: A Step-by-Step Guide
The process of rejecting a delivery should be documented meticulously. This safeguards your business and provides evidence in case of disputes.
- Detailed Inspection Report: Create a comprehensive report detailing each rejected item, including item number, quantity, reason for rejection, and supporting photographic evidence.
- Contact the Supplier: Immediately contact the supplier, informing them of the issues and providing your detailed rejection report. Retain a copy of this communication.
- Refusal to Accept: Clearly refuse to accept the delivery of the rejected items. If possible, have the delivery driver sign the report confirming the rejection.
- Storage of Rejected Goods: If the supplier agrees to collect the goods, store them securely and safely to prevent further damage. Do not dispose of the rejected goods without the supplier's authorization.
- Follow Up: Follow up with the supplier regarding the return or replacement of the rejected goods. Maintain detailed records of all communication.
Rejection Based on Product Category
Rejection criteria can vary based on the nature of the goods. Here are examples for specific product categories:
Food and Beverage Products:
- Damaged packaging: Any dents, tears, or leaks should lead to immediate rejection.
- Expired products: Products past their expiry dates are unsafe and must be rejected.
- Signs of spoilage: Unusual smells, discoloration, or visible signs of mold are indicators of spoilage.
- Temperature violations: Products requiring refrigeration should be rejected if the cold chain has been broken.
Electronics and Appliances:
- Physical damage: Scratches, dents, or cracks on the casing.
- Malfunction: The product does not power on or functions improperly.
- Missing components: Essential accessories or parts are missing.
Clothing and Textiles:
- Damage to fabric: Rips, tears, stains, or discoloration.
- Defective stitching: Loose or uneven stitching.
- Incorrect sizes or colors: Items that do not match the order specifications.
Furniture and Fixtures:
- Damage to the structure: Cracks, splinters, or other structural damage.
- Defects in the finish: Scratches, dents, or imperfections in the paint or varnish.
- Missing or damaged components: Missing screws, bolts, or other essential parts.
Preventing Delivery Issues: Proactive Measures
While rejection is a necessary recourse for faulty deliveries, proactive measures can significantly reduce the frequency of such issues:
- Establish clear communication with suppliers: Ensure accurate order specifications, delivery timelines, and quality expectations are clearly defined.
- Choose reliable suppliers: Select suppliers with a proven track record of quality and timely delivery.
- Regularly review supplier performance: Track delivery performance metrics to identify trends and address potential issues.
- Require comprehensive quality control: Insist that suppliers implement robust quality control procedures throughout their manufacturing and delivery processes.
Conclusion
Rejecting a delivery is not a simple matter of refusing a package. It's a crucial step in maintaining quality control, safeguarding your business, and protecting your reputation. By understanding your rights, meticulously inspecting deliveries, and implementing clear rejection procedures, you can mitigate the risks associated with faulty or damaged goods and ensure the smooth operation of your business. Remember, thoroughness and documentation are key throughout the entire process.
Latest Posts
Latest Posts
-
Which Of The Following Is Omitted In A Barter Transaction
Apr 25, 2025
-
Operational Decisions Bump Up Your Bumper
Apr 25, 2025
-
Pulmonary Choking Agents Primarily Enter The Victim By What Means
Apr 25, 2025
-
Algebra Nation Section 6 Topic 7 Answers
Apr 25, 2025
-
Unit 4 Progress Check Frq Part A
Apr 25, 2025
Related Post
Thank you for visiting our website which covers about Which Item Must Be Rejected When Inspecting A Delivery . We hope the information provided has been useful to you. Feel free to contact us if you have any questions or need further assistance. See you next time and don't miss to bookmark.