Which Of The Following Are Related To Lean Production
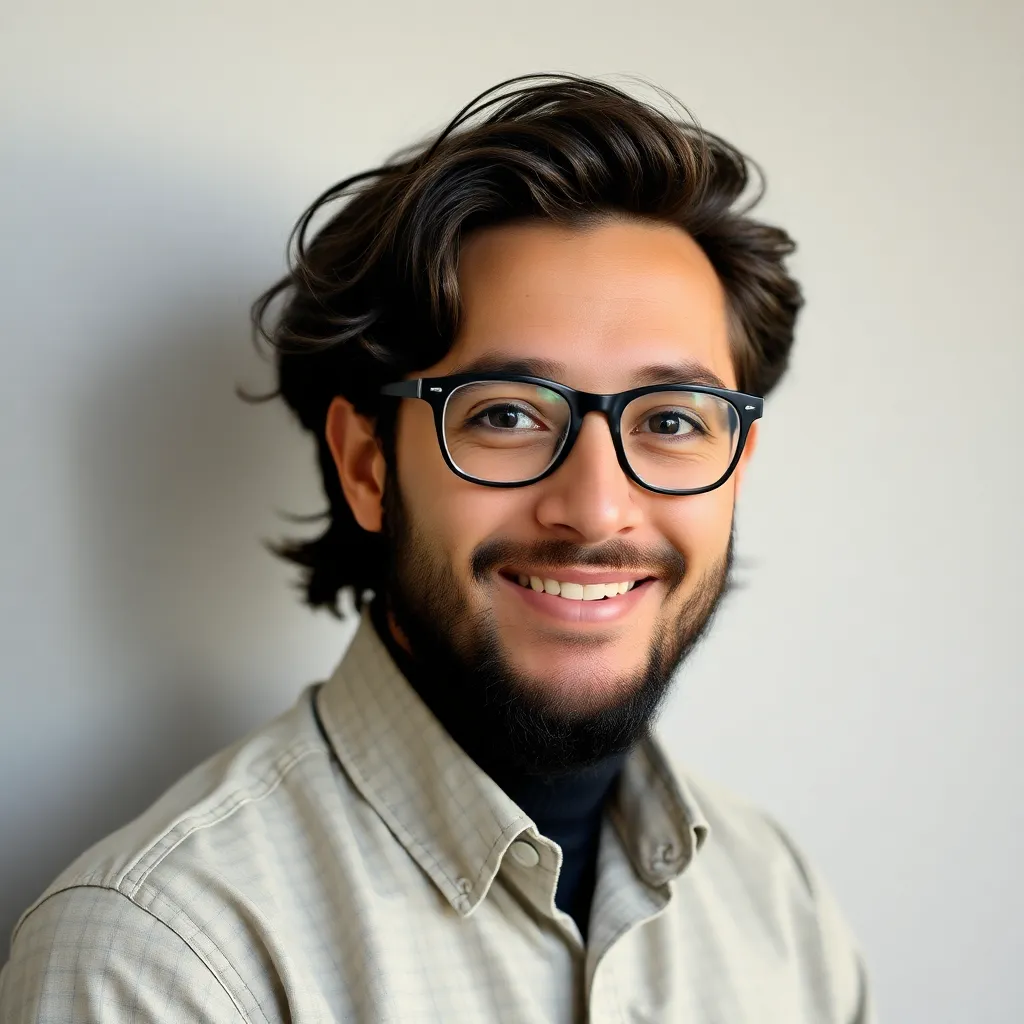
Onlines
May 08, 2025 · 7 min read
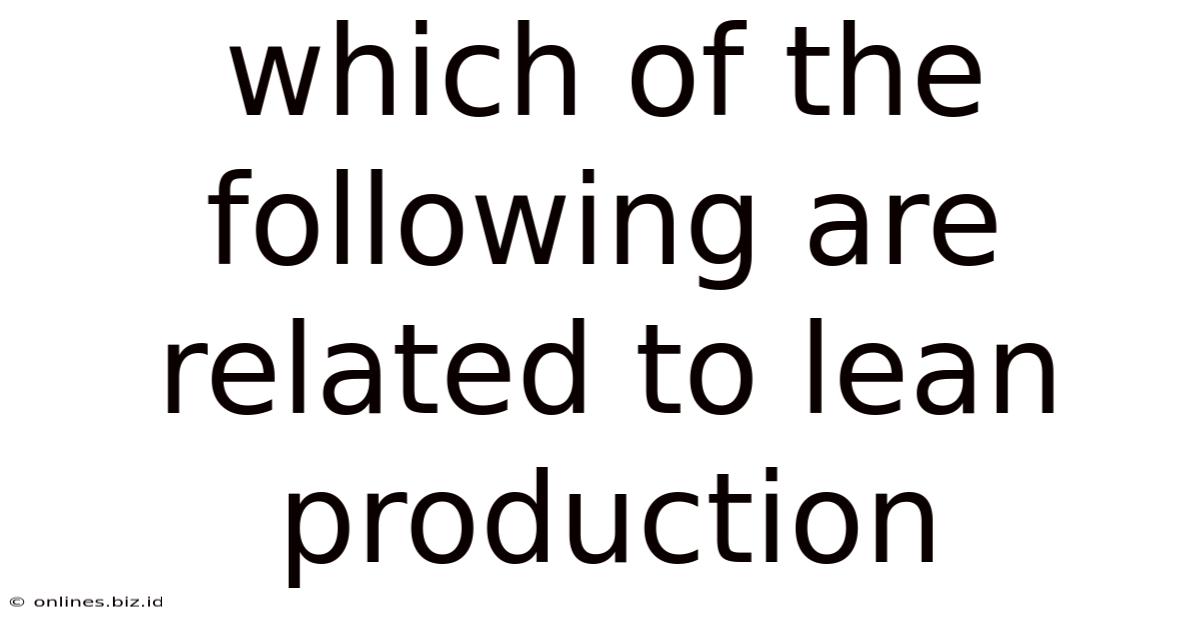
Table of Contents
Which of the Following are Related to Lean Production? A Deep Dive into Lean Principles
Lean production, also known as lean manufacturing, is a systematic method for minimizing waste and maximizing value in a manufacturing process. It's not just about reducing costs; it's about optimizing the entire value stream to deliver exactly what the customer wants, when they want it, with minimal waste. But what exactly is considered "waste" in a lean context, and which practices directly contribute to a lean production system? Let's explore.
Understanding Waste in Lean Production (Muda)
Before delving into specific practices, we need a firm grasp of the concept of muda, the Japanese word for waste. Lean thinking identifies seven major types of waste, often remembered with the acronym DOWNTIME:
- Defects: Products or services that don't meet quality standards, leading to rework, scrap, and customer dissatisfaction.
- Overproduction: Producing more than is needed or demanded, tying up resources and potentially leading to obsolete inventory.
- Waiting: Idle time for materials, equipment, or personnel, delaying the production process.
- Non-Utilized Talent: Failing to use the skills and knowledge of employees effectively. This includes not empowering employees to solve problems or make improvements.
- Transportation: Unnecessary movement of materials or products within the production process, adding time and cost.
- Inventory: Excess materials, work-in-progress, or finished goods tying up capital and increasing storage costs. This includes obsolete stock.
- Motion: Unnecessary movement of people or equipment during the production process, reducing efficiency.
Beyond these seven, some lean thinkers include an eighth type of waste: Over-processing. This refers to doing more work than is necessary to meet customer requirements. It's about streamlining processes to their most efficient form.
Key Principles and Practices of Lean Production
Numerous principles and practices contribute to the implementation of lean production. Let's examine some of the most crucial ones, categorizing them for better understanding.
1. Value Stream Mapping (VSM)
Value stream mapping is a powerful tool for visualizing the entire flow of materials and information in a production process. It helps identify areas of waste and bottlenecks, providing a roadmap for improvement. The map shows all steps, from raw materials to finished product, including both value-adding and non-value-adding activities. By analyzing the VSM, teams can pinpoint opportunities for optimization and streamlining. This is crucial because it offers a holistic view of the process.
2. Kaizen (Continuous Improvement)
Kaizen, meaning "change for the better," is the philosophy of continuous improvement. It emphasizes small, incremental changes implemented regularly rather than large, disruptive changes. Kaizen encourages employee involvement, empowering them to identify and solve problems within their areas of expertise. This fosters a culture of ongoing improvement and innovation. It's not about revolutionary change; it's about continuous, evolutionary progress.
3. Just-in-Time (JIT) Manufacturing
Just-in-time (JIT) manufacturing aims to produce only what is needed, when it is needed. This minimizes inventory, reduces waste, and improves responsiveness to customer demand. It relies on precise scheduling and efficient material handling to ensure a smooth flow of materials through the production process. JIT significantly reduces the risk of obsolescence and storage costs. However, it requires close coordination with suppliers and a robust inventory management system.
4. 5S Methodology
The 5S methodology is a workplace organization method that focuses on creating a clean, organized, and efficient work environment. The five S's are:
- Sort (Seiri): Eliminate unnecessary items from the workplace.
- Set in Order (Seiton): Arrange necessary items in a logical and easily accessible manner.
- Shine (Seiso): Clean the workplace regularly to maintain a clean and safe environment.
- Standardize (Seiketsu): Establish standards for maintaining cleanliness and organization.
- Sustain (Shitsuke): Maintain the standards and continuously improve the process.
5S contributes to a safer, more efficient, and more productive work environment. It facilitates smoother workflows and minimizes wasted time searching for tools or materials.
5. Kanban
Kanban is a visual signaling system used to manage workflow and inventory. It uses cards or other visual signals to indicate the demand for materials or products. This helps to prevent overproduction and ensures that materials are available when needed. Kanban systems promote smoother workflow and enhance communication between different stages of the production process. Its visual nature helps in quick identification of bottlenecks and areas needing attention.
6. Poka-Yoke (Mistake-Proofing)
Poka-yoke, meaning "mistake-proofing," focuses on designing processes and equipment to prevent errors from occurring. This can involve using jigs, fixtures, or other devices to guide workers and prevent mistakes. Poka-yoke is about creating a system that is inherently resistant to human error, thus minimizing defects and rework. It's a proactive approach to quality control.
7. Andon
Andon is a visual signaling system used to alert management to problems on the production line. This allows for quick response and resolution of issues, preventing them from escalating and causing further disruptions. Andon systems promote transparency and facilitate immediate problem-solving, minimizing downtime and ensuring continuous flow.
8. Cellular Manufacturing
Cellular manufacturing organizes production into self-contained cells, where each cell produces a specific family of parts or products. This reduces material handling, transportation, and waiting time, leading to improved efficiency and reduced lead times. Cellular manufacturing improves team collaboration and accountability as teams are responsible for their entire production cell.
9. Total Productive Maintenance (TPM)
Total Productive Maintenance (TPM) involves proactive maintenance of equipment to prevent breakdowns and maximize uptime. It emphasizes employee involvement in maintenance activities, fostering a culture of ownership and responsibility for equipment maintenance. TPM is all about minimizing downtime and extending the lifespan of equipment. It also promotes efficiency and reduces production disruptions.
Which of the Following are Related to Lean Production? Examples
Now let's look at some examples and determine their relevance to lean production:
Scenario 1: A company implements a system where workers can stop the production line if they identify a problem.
Answer: This is directly related to lean production. It aligns with the principles of Andon and Kaizen, empowering employees to identify and address problems immediately, preventing larger issues down the line.
Scenario 2: A manufacturing plant uses a software system to track inventory levels in real-time and automatically orders more materials when needed.
Answer: This is closely related to lean production, specifically to Just-in-Time (JIT) manufacturing. Real-time tracking and automated ordering help minimize inventory levels while ensuring that materials are available when needed.
Scenario 3: A company redesigns its production line to reduce the number of steps required to manufacture a product.
Answer: This directly supports lean principles. Reducing steps reduces motion, waiting, and potentially over-processing, streamlining the value stream.
Scenario 4: Employees participate in regular meetings to discuss ways to improve efficiency and eliminate waste.
Answer: This aligns with the Kaizen philosophy of continuous improvement. Regular meetings and employee involvement are key to identifying and addressing inefficiencies and waste.
Scenario 5: A company keeps large amounts of finished goods in its warehouse to ensure it can meet unexpected spikes in demand.
Answer: This is contrary to lean principles. Holding large amounts of finished goods constitutes excess inventory, a major type of waste in lean thinking.
Scenario 6: A company trains its employees on problem-solving techniques and empowers them to make decisions related to their work.
Answer: This is highly relevant to lean production. It addresses the waste of non-utilized talent by empowering employees and leveraging their expertise to improve processes.
Scenario 7: A company uses a system of visual cues to signal when more materials are needed for a particular process.
Answer: This is directly related to Kanban, a key lean tool for managing workflow and inventory.
Conclusion: Embracing Lean for Continuous Improvement
Lean production is a holistic approach to manufacturing and service delivery, aiming for continuous improvement and the elimination of waste in all its forms. By understanding the seven (or eight) types of muda and implementing the various principles and practices discussed above, organizations can dramatically improve efficiency, reduce costs, improve quality, and boost customer satisfaction. The key is commitment to continuous improvement, employee empowerment, and a systematic approach to identifying and eliminating waste throughout the entire value stream. Remember, lean is not a destination, but a journey of continuous optimization.
Latest Posts
Latest Posts
-
A Strictly Fermentative Bacterium Produces Energy
May 11, 2025
-
With Amazon Virtual Private Cloud What Is The Smallest
May 11, 2025
-
In Single Celled Organisms Materials Are Stored Primarily In
May 11, 2025
-
The Executing Process Group Generally Requires The Most Resources
May 11, 2025
-
The Slope Of The Blue Curve Measures The Planes
May 11, 2025
Related Post
Thank you for visiting our website which covers about Which Of The Following Are Related To Lean Production . We hope the information provided has been useful to you. Feel free to contact us if you have any questions or need further assistance. See you next time and don't miss to bookmark.