Which Of The Following Is Not A Typical Inspection Point
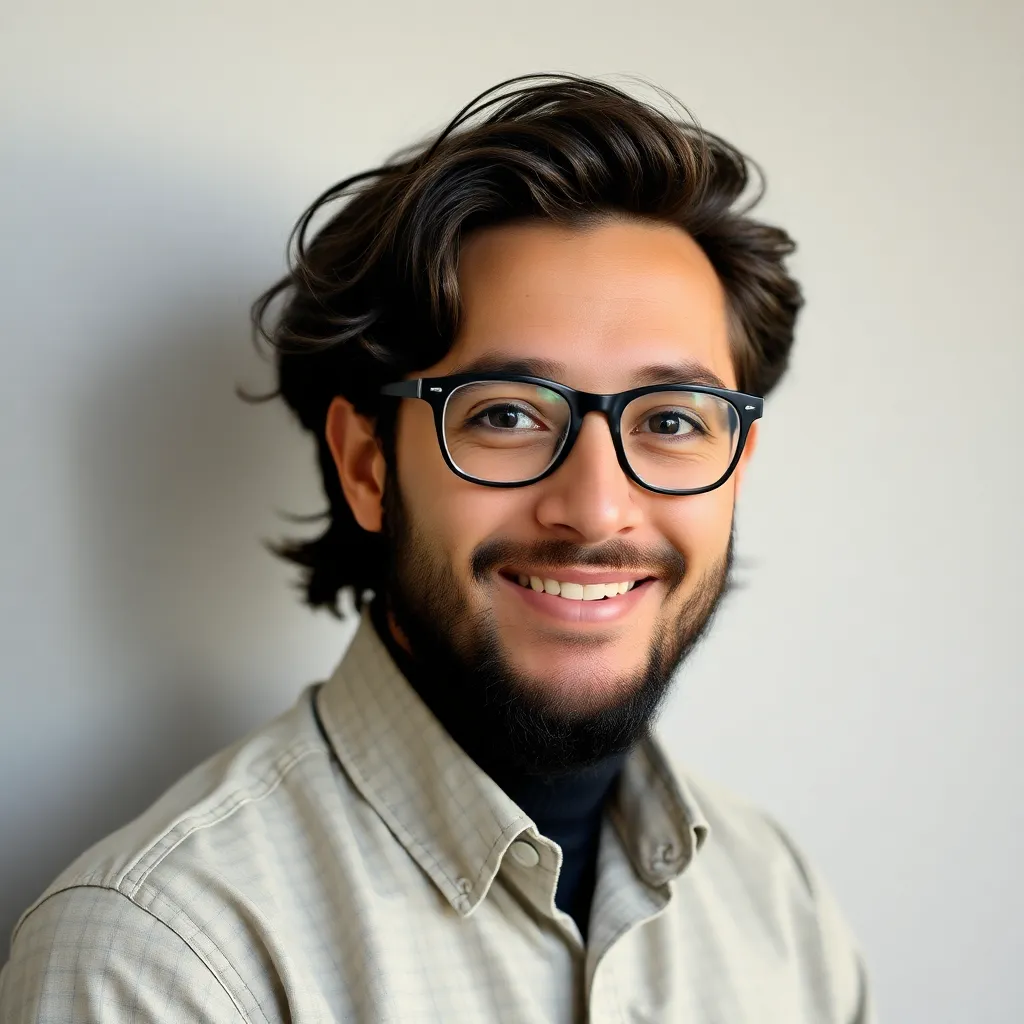
Onlines
May 08, 2025 · 5 min read
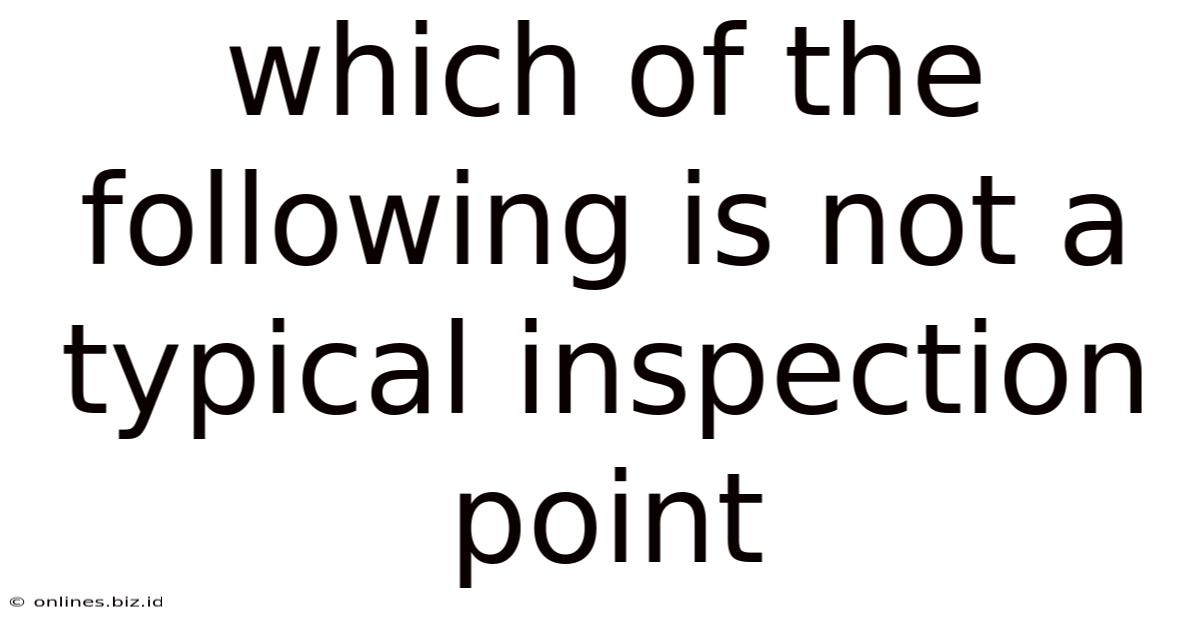
Table of Contents
Which of the Following is NOT a Typical Inspection Point? A Comprehensive Guide to Inspection Procedures
This article delves deep into the world of inspections, exploring common inspection points across various industries and highlighting what typically isn't included. We'll cover diverse fields, from manufacturing and construction to automotive and healthcare, providing a comprehensive understanding of inspection procedures and their critical role in quality assurance and safety.
Understanding Inspection Points: A Foundation
Before we dive into atypical inspection points, let's establish a firm grasp on what constitutes a typical one. Inspection points are specific locations, components, or processes within a system or product that are systematically examined to ensure compliance with predetermined standards, specifications, or regulations. These points are selected based on criticality, potential failure modes, and historical data. The goal is to identify defects, inconsistencies, or deviations early in the process, preventing costly rework, recalls, or even catastrophic failures.
Common Examples Across Industries:
- Manufacturing: Dimensionality of parts, material composition, surface finish, weld integrity, functionality of moving parts.
- Construction: Foundation integrity, structural framing, electrical wiring, plumbing systems, adherence to building codes.
- Automotive: Tire pressure and tread depth, brake system functionality, fluid levels, lights and signals, steering and suspension components.
- Healthcare: Sterility of medical equipment, proper calibration of devices, medication dosages, patient records accuracy, hygiene protocols.
- Food safety: Temperature control, sanitation practices, expiry dates, ingredient labeling, presence of contaminants.
Typical Inspection Point Categories: A Closer Look
To better understand what is not a typical inspection point, let's categorize common inspection activities:
1. Visual Inspection:
This is the most basic and often the first step. It involves a thorough visual examination to detect obvious defects such as scratches, cracks, dents, discoloration, or misalignment. This is typical for almost all inspection procedures.
2. Dimensional Inspection:
Measurements are taken to verify that components conform to specified dimensions, tolerances, and specifications. This is crucial in manufacturing, construction, and engineering. Calipers, micrometers, and other precision measuring instruments are commonly used.
3. Functional Inspection:
This involves testing the functionality of a component or system to ensure it performs as intended. This can involve simple tests like turning a switch or more complex procedures requiring specialized equipment. Functional testing is critical in ensuring overall system performance.
4. Material Inspection:
This involves verifying the composition and properties of materials used in the manufacturing process. This might include chemical analysis, tensile strength testing, or other material characterization methods. This ensures the quality and suitability of the materials used.
5. Process Inspection:
This focuses on the processes involved in manufacturing or construction rather than the final product. It checks if procedures are being followed correctly and that equipment is operating within specified parameters. This is vital for maintaining consistent quality and preventing defects from occurring in the first place.
Identifying Atypical Inspection Points: Where the Unusual Lies
Now, let's shift our focus to those elements that are typically not included as formal inspection points, though they might be considered in a broader quality management system:
1. Employee Morale and Job Satisfaction:
While crucial for overall workplace productivity and product quality, employee morale and job satisfaction aren't directly considered inspection points in the traditional sense. Though indirect, low morale can affect the quality of work, leading to more errors, but it’s not a typical direct inspection point.
2. Environmental Impact of Production:
While environmentally conscious companies increasingly prioritize sustainable practices, the environmental impact of production isn't usually a specific inspection point during the manufacturing process itself. Environmental audits are separate from product or process inspections.
3. Corporate Social Responsibility Initiatives:
A company's commitment to ethical sourcing, fair labor practices, and community involvement, while important for brand reputation and stakeholder engagement, doesn't typically fall under the scope of a product or process inspection.
4. Marketing and Sales Performance:
How well a product sells or how effective the marketing campaign is are business metrics, not inspection points related to product quality or conformity to specifications.
5. Long-Term Product Durability Under Extreme Conditions:
While testing product durability is part of some rigorous quality assurance processes, the assessment of long-term durability under extreme (and often unpredictable) conditions is usually done through separate and extensive field testing or simulations, not as a routine inspection point.
6. Supplier Relationship Management:
Maintaining positive relationships with suppliers is critical for a consistent supply chain. However, this is a business management function, not a direct inspection point in product manufacturing or quality control.
7. Executive Management Decisions:
While strategic decisions of the executive team influence the overall quality management system, their specific choices are not inspection points themselves.
8. Customer Feedback (Without Specific Metrics):
While vital for continuous improvement, general customer feedback alone (unless quantified with metrics and linked to specific aspects of the product or process) is not a typical inspection point. Data collected from customer surveys, however, can inform future inspection procedures.
9. Office Environment & Ergonomics:
While a comfortable and safe work environment is crucial for employee wellbeing and productivity, this is primarily addressed through workplace safety and health regulations and assessments, not as routine inspection points for a manufactured product.
10. Software Code Quality (In Hardware Inspections):
In hardware inspections, the quality of the embedded software might be assessed indirectly through functional testing, but a deep dive into software code quality itself is usually handled by a separate software testing team. These are often separate inspection procedures.
The Importance of Clearly Defined Inspection Points
Having clearly defined and documented inspection points is crucial for several reasons:
-
Consistency: It ensures that all products or processes are inspected to the same standard, eliminating inconsistencies and potential biases.
-
Traceability: It enables the tracing of defects back to their root cause, facilitating effective corrective and preventive actions.
-
Efficiency: It streamlines the inspection process, focusing resources on the most critical aspects.
-
Compliance: It helps meet regulatory requirements and industry standards, avoiding potential penalties or legal issues.
-
Continuous Improvement: Data gathered from inspections helps identify areas for improvement in the design, manufacturing, or service processes.
In conclusion, understanding which elements are not typical inspection points, in addition to the typical points, is just as crucial as understanding what is. A comprehensive quality management system requires a holistic view, encompassing all aspects of the business, but the formal inspection process must be precisely defined for effective and efficient quality control. This holistic view allows for proactive measures to ensure high-quality products and services, contributing to a strong and sustainable business.
Latest Posts
Latest Posts
-
An Edible History Of Humanity Chapter Summary
May 08, 2025
-
An Echo Sonnet To An Empty Page Analysis
May 08, 2025
-
Main Characters In Catcher In The Rye
May 08, 2025
-
A Short Term Creditor Would Be Most Interested In
May 08, 2025
-
The Dolls House Katherine Mansfield Summary
May 08, 2025
Related Post
Thank you for visiting our website which covers about Which Of The Following Is Not A Typical Inspection Point . We hope the information provided has been useful to you. Feel free to contact us if you have any questions or need further assistance. See you next time and don't miss to bookmark.