Which Of The Following Is Not Accurate Regarding Fmea
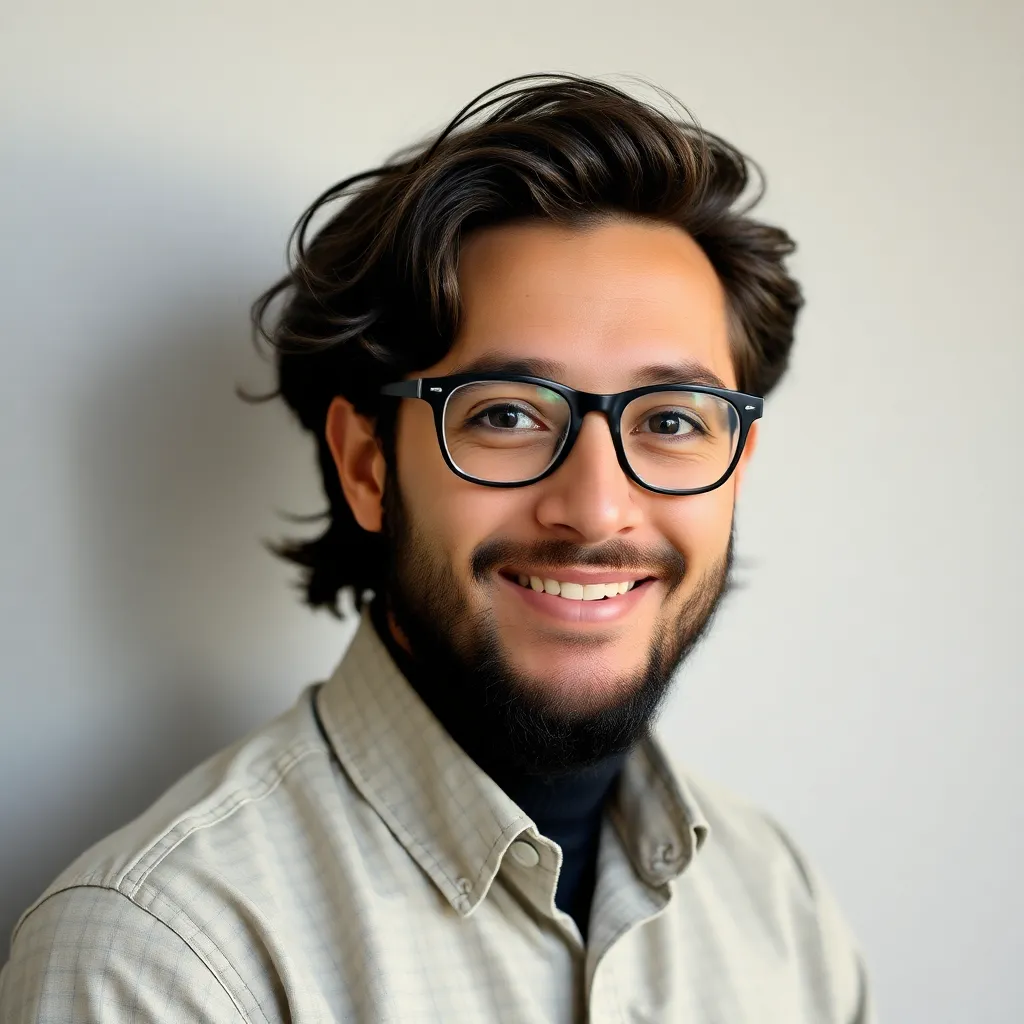
Onlines
Apr 23, 2025 · 7 min read

Table of Contents
Which of the following is NOT Accurate Regarding FMEA?
Failure Mode and Effects Analysis (FMEA) is a crucial proactive risk assessment and mitigation tool widely used across various industries. Understanding its nuances is vital for effective implementation. This article delves deep into common misconceptions about FMEA, clarifying what statements are inaccurate and highlighting the correct understanding of this powerful technique. We'll explore various aspects, from its purpose and methodology to its limitations and applications.
Misconception 1: FMEA is only for identifying potential failures.
This is incorrect. While FMEA excels at identifying potential failure modes, its true power lies in the proactive mitigation of risks. It's not merely a list of potential problems; it's a structured process for:
- Identifying potential failure modes: Pinpointing how a product, process, or service could fail.
- Analyzing the effects of those failures: Understanding the consequences of each failure mode, both internally and externally.
- Assessing the severity, occurrence, and detection of failures: Quantifying the risk associated with each failure mode using a Risk Priority Number (RPN).
- Developing actions to mitigate risks: Implementing preventative and corrective actions to reduce the likelihood or severity of failures.
- Documenting the entire process: Maintaining a record of identified risks, their mitigation strategies, and responsibilities for their implementation.
FMEA is a continuous improvement tool. The process isn't concluded after the initial analysis; it's an iterative process requiring regular review and updates as the product, process, or service evolves.
Misconception 2: A high RPN automatically signifies a critical failure.
False. The Risk Priority Number (RPN), calculated by multiplying Severity, Occurrence, and Detection, is a helpful indicator of risk, but it's not a definitive measure of criticality. Several limitations exist:
- Subjectivity in scoring: The scoring of Severity, Occurrence, and Detection often involves subjective judgments, which can lead to inconsistencies. Two different teams analyzing the same failure mode might arrive at different RPN values.
- Ignoring potential cascading effects: RPN calculation focuses on individual failure modes in isolation. It may not adequately capture the impact of multiple failures occurring simultaneously or cascading effects where one failure triggers another.
- Oversimplification of complex risks: Reducing complex risk profiles to a single number can oversimplify the situation and mask crucial nuances.
- Focus on frequency over impact: While occurrence is a factor, a low-occurrence, high-severity failure might still require urgent attention, even if the RPN isn't extremely high.
Therefore, while a high RPN warrants attention, it shouldn't be the sole determinant of prioritizing actions. A thorough risk assessment needs to consider qualitative factors and potential consequences beyond the numerical RPN. A comprehensive risk management strategy should consider both the quantitative RPN and qualitative assessments of potential impact.
Misconception 3: FMEA is only applicable to complex systems.
Incorrect. FMEA's applicability spans a wide range of complexities, from simple processes to intricate systems. While its comprehensive application might be more time-consuming for complex systems, its fundamental principles remain the same. Even seemingly simple processes can benefit from FMEA, helping identify potential issues and improve reliability.
For example, a small bakery might use FMEA to analyze the process of making bread, identifying potential failures like oven malfunction, ingredient spoilage, or incorrect baking times. Similarly, a large manufacturing facility might employ FMEA to assess the complex assembly line of a sophisticated machine.
The key is to tailor the scope and depth of the FMEA to the specific complexity of the product, process, or service under consideration. Simplicity doesn't negate the potential benefits of a well-executed FMEA.
Misconception 4: FMEA guarantees the elimination of all failures.
This is absolutely false. FMEA is a powerful tool, but it's not a guarantee against all failures. Its purpose is to proactively identify and mitigate risks, reducing the likelihood and impact of failures, but it cannot eliminate all possibilities entirely. There will always be unforeseen circumstances and unknown unknowns.
Factors beyond the scope of the initial FMEA analysis might still contribute to failures. New technologies, unexpected external factors, or human errors can always introduce new risks. Therefore, FMEA should be considered a continuous improvement process, requiring regular review and updates to reflect changes and incorporate lessons learned from real-world experiences.
Misconception 5: FMEA is a one-time activity.
Incorrect. Effective FMEA is an iterative process. It should be performed at various stages of a product's lifecycle, from design and development to manufacturing and operation. Moreover, it should be updated regularly to reflect changes, incorporate lessons learned, and address emerging risks.
Simply completing an FMEA once and filing it away is ineffective. Regular reviews are crucial to ensure that the analysis remains relevant and accounts for changes in the system or process. This iterative approach ensures that the FMEA serves as a dynamic tool for risk management and continuous improvement, adapting to evolving needs and circumstances.
Misconception 6: Only engineers and technical experts can conduct FMEA.
False. While technical expertise is helpful, FMEA is most effective when a multidisciplinary team participates. Involving individuals from various departments, including operations, quality, marketing, and even customers, provides diverse perspectives and insights.
This cross-functional approach ensures that all potential failure modes and their effects are considered holistically. Diverse perspectives lead to more comprehensive risk identification and more creative solutions for risk mitigation. Engaging a wider team enhances buy-in and ownership, fostering a culture of proactive risk management.
Misconception 7: The FMEA process is overly complex and time-consuming.
While a thorough FMEA can be involved, its complexity is relative to the product or process being analyzed. Simplified FMEA approaches exist for straightforward systems, and various software tools can streamline the process significantly, minimizing the time and effort required. The investment of time and resources is justified by the potential benefits of preventing costly failures and improving overall system reliability. Focusing on prioritization and using appropriate tools can make the process manageable even for complex systems.
Furthermore, the benefits gained by preventing costly failures and improving the overall reliability of a product or process often far outweigh the investment made in conducting a thorough FMEA.
Misconception 8: FMEA replaces other risk assessment methods.
False. FMEA is a valuable tool, but it shouldn't replace other risk assessment methods. It's most effective when integrated into a broader risk management strategy that includes other techniques like Hazard and Operability Studies (HAZOP), Fault Tree Analysis (FTA), and others. Each method has its strengths and limitations, and using them in combination provides a more robust and comprehensive approach to risk management.
A well-rounded risk management program uses various methods to provide a holistic view of potential risks and develop effective mitigation strategies. Choosing the right tool depends on the specific application and the nature of the risks being assessed.
Misconception 9: FMEA is solely a reactive measure.
This is completely incorrect. FMEA is fundamentally proactive. It focuses on anticipating potential failures before they occur, allowing for preventive actions and minimizing the impact of any failures that might still happen. While it can certainly inform reactive responses to actual failures, its primary purpose is to anticipate and prevent problems from arising in the first place.
By identifying potential failure modes and implementing preventative measures, FMEA plays a key role in building robust and reliable systems. Its forward-thinking approach to risk management makes it a vital component of any effective quality management system.
Conclusion:
FMEA is a powerful and versatile tool for proactive risk management. Understanding its proper application and avoiding common misconceptions is crucial for successful implementation. By embracing its iterative nature, leveraging multidisciplinary teams, and integrating it with other risk assessment methods, organizations can harness the full potential of FMEA to enhance product reliability, improve processes, and prevent costly failures. Remember that while FMEA offers significant benefits, it's a tool, and its effectiveness relies heavily on proper execution and understanding. Continuous improvement and adaptation are essential for sustained success in utilizing this invaluable risk management technique.
Latest Posts
Latest Posts
-
7 65 Draw The Shear And Moment Diagrams For The Beam
Apr 23, 2025
-
Saying No Contingent Upon A Learners Response
Apr 23, 2025
-
Which Of The Following Best Defines Effective Listening
Apr 23, 2025
-
Sexual Dysfunctions And Problems Can Be Caused By
Apr 23, 2025
-
Print Reading For Industry Review Activity 10 1
Apr 23, 2025
Related Post
Thank you for visiting our website which covers about Which Of The Following Is Not Accurate Regarding Fmea . We hope the information provided has been useful to you. Feel free to contact us if you have any questions or need further assistance. See you next time and don't miss to bookmark.