Which Of The Following Is True Of Gma Spot Welding
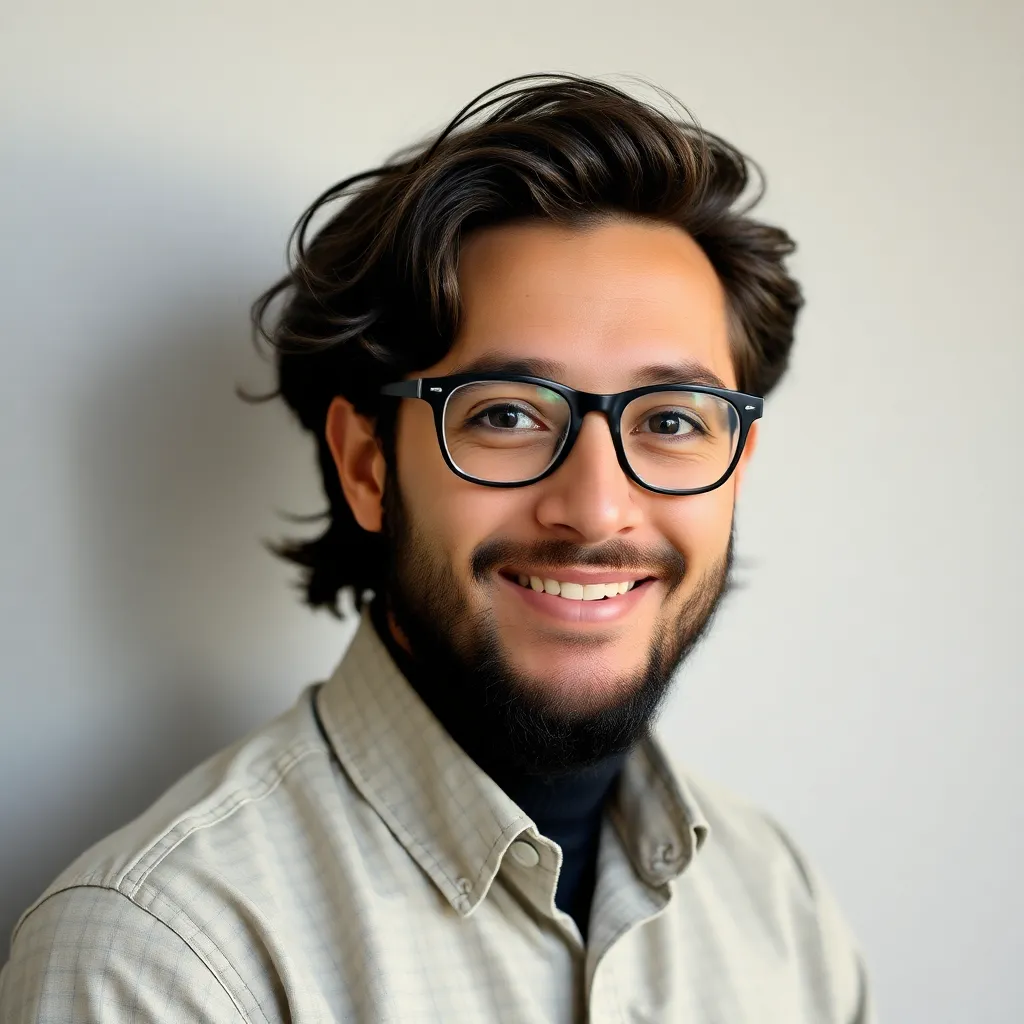
Onlines
Apr 17, 2025 · 5 min read

Table of Contents
Which of the Following is True of GMA Spot Welding? A Deep Dive into the Process
Spot welding, a fundamental resistance welding technique, has seen significant advancements. Among these, Gas Metal Arc (GMA) spot welding, also known as MIG spot welding, stands out as a promising alternative to traditional resistance spot welding. This article delves deep into GMA spot welding, exploring its characteristics, advantages, disadvantages, and applications, ultimately answering the question: which of the following is true of GMA spot welding? We'll examine several potential statements and analyze their validity.
Understanding GMA Spot Welding: A Primer
Before diving into specific true/false statements, let's establish a solid foundation of understanding. GMA spot welding utilizes a continuous wire feed of consumable electrode wire, typically steel, to create welds. Unlike traditional resistance spot welding, which uses non-consumable electrodes, GMA spot welding employs the arc generated between the electrode wire and the workpiece to melt the base metals and form a weld nugget. The process often involves a shielding gas, such as argon or CO2, to protect the weld from atmospheric contamination.
This process offers several key advantages over traditional methods, making it suitable for diverse applications where flexibility and adaptability are paramount.
Key Features of GMA Spot Welding:
- Consumable Electrode: This eliminates the need for frequent electrode dressing and replacement, a significant advantage in high-volume production.
- Versatile Materials: GMA spot welding can be applied to a broader range of materials compared to resistance spot welding, including dissimilar metals.
- Deep Penetration: The arc's ability to generate higher heat input allows for deeper penetration, leading to stronger welds in certain applications.
- High-Speed Capability: The continuous wire feed system allows for high-speed welding, improving productivity.
- Reduced Electrode Wear: The consumable nature of the electrode minimizes electrode wear and maintenance.
Limitations of GMA Spot Welding:
- Higher Heat Input: While this can lead to deeper penetration, it can also result in greater heat-affected zones (HAZ), potentially impacting material properties.
- Increased Complexity: GMA spot welding setups are more complex than resistance spot welding systems, requiring sophisticated control parameters.
- Greater Spatter: The arc process inherently produces more spatter, requiring careful cleaning and post-weld finishing.
- Weld Quality Variability: Achieving consistent weld quality requires precise control of several parameters, such as wire feed speed, voltage, and shielding gas flow.
- Cost: The initial investment in equipment and skilled labor can be higher than for traditional resistance spot welding.
Evaluating True/False Statements about GMA Spot Welding
Now, let's tackle several statements about GMA spot welding and determine their veracity.
Statement 1: GMA spot welding produces stronger welds than traditional resistance spot welding.
Partially True: While GMA spot welding can achieve deeper penetration, leading to potentially stronger welds in some cases, this is not universally true. The strength of a weld depends on numerous factors, including material properties, weld geometry, and process parameters. Resistance spot welding, when properly optimized, can produce equally strong, or even stronger welds, depending on the specific application. The "stronger" claim is too generalized and context-dependent.
Statement 2: GMA spot welding is more suitable for dissimilar metals than resistance spot welding.
True: GMA spot welding's versatility makes it better suited for joining dissimilar metals. The arc process allows for greater control over the melting and fusion process, making it easier to handle the different thermal properties and melting points of varied materials. Resistance spot welding faces challenges when joining dissimilar metals due to differences in electrical conductivity and thermal properties.
Statement 3: GMA spot welding requires less maintenance than resistance spot welding.
True: The consumable electrode in GMA spot welding reduces the frequency of electrode dressing and replacement, significantly lowering maintenance requirements compared to resistance spot welding, where electrode tip wear necessitates frequent attention.
Statement 4: GMA spot welding is always faster than resistance spot welding.
False: While GMA spot welding can be faster due to continuous wire feed, this is not always the case. The actual welding speed depends on several factors, including material thickness, desired weld strength, and specific equipment capabilities. In certain scenarios, resistance spot welding might be faster due to its simpler setup and more straightforward process.
Statement 5: GMA spot welding is less expensive than resistance spot welding.
False: The initial investment in GMA spot welding equipment is generally higher than for resistance spot welding. The cost of consumable wire also adds to the overall operating expense. While long-term maintenance might be lower, the upfront cost and consumable usage often make GMA spot welding more expensive initially.
Statement 6: GMA spot welding produces less spatter than resistance spot welding.
False: GMA spot welding is known for producing more spatter than resistance spot welding. This is a direct consequence of the arc process. While techniques exist to minimize spatter, it remains a greater challenge in GMA spot welding than in resistance spot welding.
Statement 7: GMA spot welding is ideal for high-volume production of thin sheet metal.
Partially True: While GMA spot welding can be used for thin sheet metal, it may not be the optimal choice for high-volume production of very thin sheets. The higher heat input could lead to excessive heat distortion or burn-through in extremely thin materials. Resistance spot welding, with its precise control over heat input, is often preferred in such cases.
Statement 8: GMA spot welding is always the best choice for all spot welding applications.
False: GMA spot welding is a valuable technique, but it is not universally superior. The best choice depends on the specific application, considering factors such as material type, thickness, required weld strength, production volume, cost considerations, and available equipment.
Conclusion: Choosing the Right Spot Welding Technique
This comprehensive examination of GMA spot welding reveals its strengths and limitations. While GMA spot welding offers several advantages, including versatility in material handling and reduced maintenance, it's not a one-size-fits-all solution. The optimal choice between GMA spot welding and traditional resistance spot welding hinges on a careful assessment of the specific requirements of the application. By understanding the nuances of each technique, manufacturers can make informed decisions to ensure optimal weld quality, production efficiency, and cost-effectiveness. Understanding the "truth" regarding GMA spot welding involves a nuanced understanding of its capabilities and limitations within the context of its specific application.
Latest Posts
Latest Posts
-
Lesson Quiz 1 2 What Is Economics
Apr 19, 2025
-
The Man Who Would Be King Summary
Apr 19, 2025
-
Doy A La Profesora Los Libros De Espanol
Apr 19, 2025
-
Charlie And The Chocolate Factory Book Chapters
Apr 19, 2025
-
Lab Safety Scenarios Worksheet Answer Key Pdf
Apr 19, 2025
Related Post
Thank you for visiting our website which covers about Which Of The Following Is True Of Gma Spot Welding . We hope the information provided has been useful to you. Feel free to contact us if you have any questions or need further assistance. See you next time and don't miss to bookmark.