Which Of The Following Is Used For Piping Natural Gas
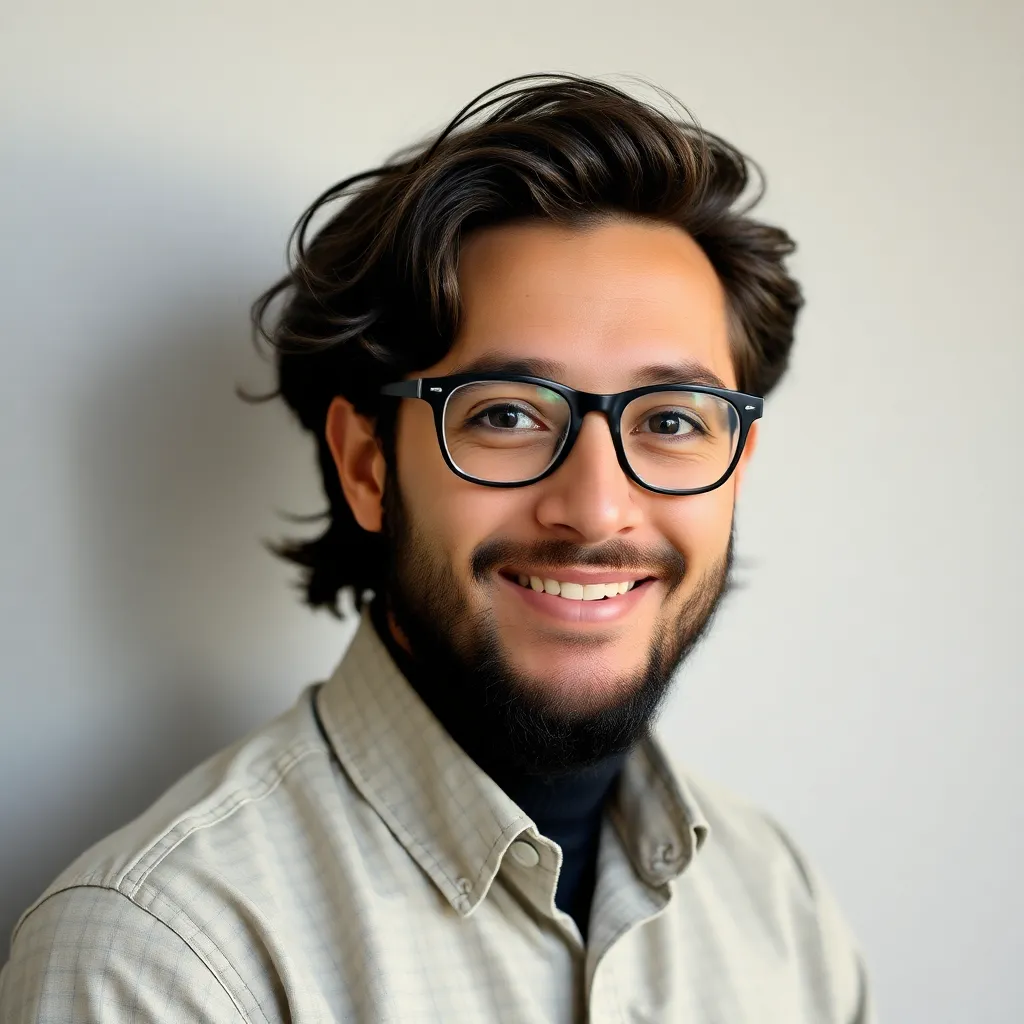
Onlines
May 10, 2025 · 6 min read
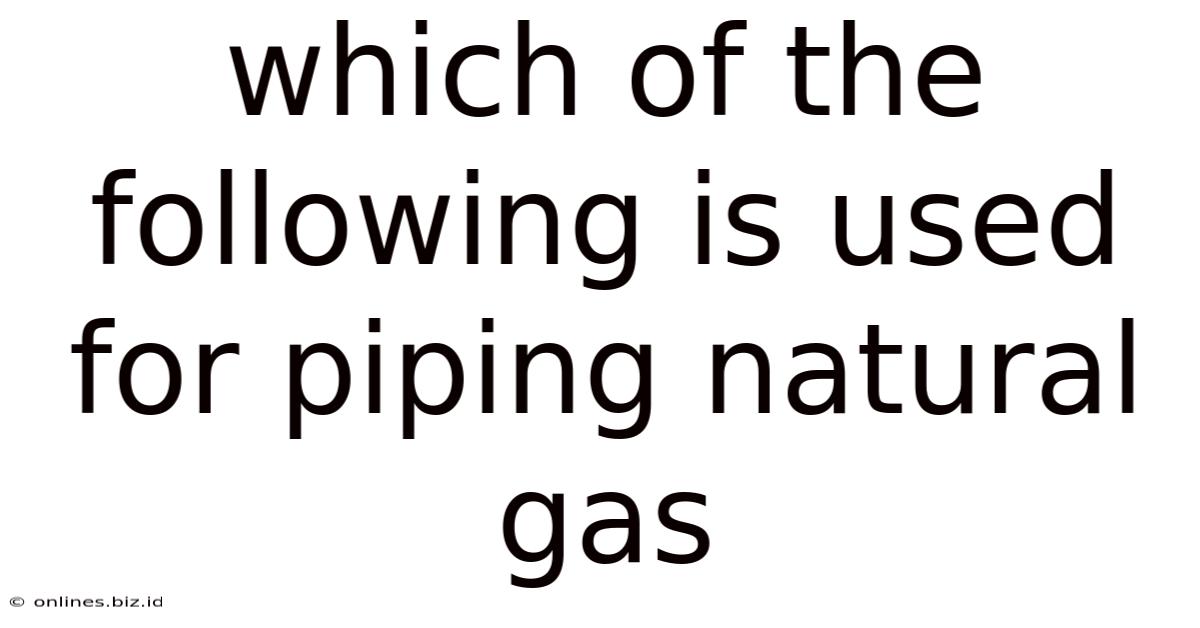
Table of Contents
Which of the Following is Used for Piping Natural Gas? A Deep Dive into Pipeline Materials and Construction
Natural gas, a crucial energy source globally, requires robust and efficient transportation systems to reach consumers. Pipelines are the backbone of this infrastructure, playing a vital role in safely and reliably delivering this valuable resource. But what materials are best suited for this demanding task? This comprehensive guide delves into the specifics of natural gas piping, examining various materials and their suitability, considering factors like cost, durability, safety, and environmental impact.
Understanding Natural Gas Transportation: More Than Just Pipes
Before diving into the materials themselves, it's crucial to understand the broader context of natural gas transportation. The process isn't simply about selecting a pipe and connecting it; it involves a complex network of considerations:
1. Pipeline Design and Engineering: A Critical First Step
The design phase is paramount. Engineers must consider numerous factors including:
- Pressure: Natural gas pipelines operate under varying pressures, depending on the distance and terrain. High-pressure pipelines require materials with exceptional strength and resistance to stress.
- Diameter: Pipe diameter is crucial for flow rate and capacity. Larger diameter pipelines are needed for transporting large volumes of gas over long distances.
- Terrain: The pipeline route significantly impacts material selection. Mountainous or unstable terrain necessitates pipes with increased strength and resistance to ground movement.
- Environmental Considerations: Minimizing environmental impact is crucial. This involves choosing materials with low environmental footprints and employing construction methods that reduce habitat disruption.
2. Material Selection: A Balancing Act
The choice of material is a critical decision, balancing factors like:
- Strength and Durability: The pipe must withstand high internal pressures, external forces (like soil movement), and corrosion.
- Cost-Effectiveness: Balancing material cost with long-term maintenance and operational costs is essential.
- Safety: The material must be inherently safe and resistant to failure, minimizing the risk of leaks and explosions.
- Corrosion Resistance: Natural gas pipelines are often exposed to corrosive environments, requiring materials that can withstand these conditions.
Common Materials Used for Natural Gas Pipelines: A Comparative Analysis
Several materials are commonly employed for natural gas pipelines, each possessing unique characteristics and advantages:
1. Steel: The Workhorse of Natural Gas Pipelines
Steel remains the most prevalent material for natural gas pipelines, particularly for long-distance, high-pressure applications. Its strengths include:
- High Strength-to-Weight Ratio: Steel offers excellent strength, enabling it to withstand high internal pressures.
- Weldability: Steel pipes can be easily welded together to form long continuous pipelines.
- Established Infrastructure and Expertise: Decades of experience and established infrastructure support the use of steel pipelines.
- Cost-Effective (in many scenarios): While the initial cost can be substantial, steel pipelines often prove cost-effective over their long lifespan.
However, steel pipelines also present drawbacks:
- Susceptibility to Corrosion: Steel is prone to corrosion, especially in harsh environments, requiring protective coatings and regular maintenance.
- Potential for Leaks: While rare with proper maintenance, steel pipelines can suffer leaks due to corrosion or damage.
- Environmental Impact of Production: Steel production is energy-intensive and contributes to greenhouse gas emissions.
2. High-Density Polyethylene (HDPE): A Growing Alternative
HDPE is increasingly used, especially in lower-pressure applications and shorter distances. Its advantages include:
- Excellent Corrosion Resistance: HDPE is highly resistant to corrosion, eliminating the need for protective coatings.
- Lightweight and Flexible: HDPE pipes are easier to handle and install, especially in challenging terrains.
- Longer Lifespan: HDPE pipes often boast longer lifespans than steel pipes, reducing long-term maintenance costs.
- Lower Environmental Impact: HDPE production has a lower carbon footprint compared to steel production.
Despite its benefits, HDPE also has limitations:
- Lower Pressure Tolerance: HDPE pipes are generally not suitable for extremely high-pressure applications.
- Susceptibility to UV Degradation: HDPE can degrade when exposed to prolonged UV radiation, requiring protective measures.
- Limited Temperature Resistance: HDPE has a lower temperature tolerance compared to steel.
3. Other Materials: Exploring Niche Applications
While steel and HDPE dominate the natural gas pipeline landscape, other materials find niche applications:
- Cast Iron: Historically used, cast iron is rarely used in new natural gas pipelines due to its susceptibility to corrosion and fragility.
- Ductile Iron: A more modern alternative to cast iron, ductile iron offers improved strength and ductility. However, it still faces limitations compared to steel and HDPE.
- Concrete: Concrete pipes are occasionally used for certain applications, offering good compressive strength and resistance to corrosion. However, their weight and inflexibility limit their application.
Pipeline Construction: A Multi-Stage Process
The construction of natural gas pipelines is a meticulous process:
1. Route Planning and Surveying: Minimizing Environmental Impact
Careful route planning is essential to minimize environmental disruption and optimize pipeline efficiency. Surveys assess the terrain, identifying potential obstacles and environmental concerns.
2. Site Preparation and Excavation: Preparing the Ground
The pipeline route is cleared and excavated, creating a trench of sufficient depth and width to accommodate the pipe.
3. Pipe Laying and Joining: Connecting the Sections
Pipes are laid in the trench, joined using welding (for steel) or fusion bonding (for HDPE). Quality control is paramount to ensure strong and leak-free joints.
4. Backfilling and Testing: Ensuring Integrity
Once laid, the pipes are carefully backfilled, ensuring proper compaction and support. Rigorous testing is conducted to verify pipeline integrity, identifying and rectifying any leaks or defects before operation.
5. Commissioning and Monitoring: Ensuring Safe Operation
After successful testing, the pipeline is commissioned and integrated into the broader natural gas distribution network. Ongoing monitoring systems track pressure and flow rates, detecting any anomalies.
Safety and Environmental Considerations: Prioritizing Responsible Practices
Natural gas pipeline safety and environmental protection are paramount:
- Leak Detection and Prevention: Regular inspections, advanced leak detection technologies, and robust maintenance programs are essential.
- Emergency Response Plans: Comprehensive emergency response plans address potential pipeline incidents, ensuring swift and effective action.
- Minimizing Environmental Impact: Pipeline routes are carefully selected to minimize damage to ecosystems and habitats. Erosion and sediment control measures are employed during construction.
- Community Engagement: Open communication and engagement with communities along pipeline routes is essential to address concerns and build trust.
Conclusion: A Complex System, Demanding Careful Consideration
The choice of material for natural gas pipelines is a complex decision, requiring a thorough understanding of the project's specific requirements, including pressure, distance, terrain, and environmental considerations. While steel remains the dominant material, HDPE and other materials are gaining prominence in specific applications. The continued development of advanced materials and construction techniques will further enhance the safety, efficiency, and environmental sustainability of natural gas pipeline infrastructure. The focus should always be on responsible development, ensuring reliable and safe delivery of this vital energy resource while minimizing environmental impact.
Latest Posts
Latest Posts
-
Long Term Capacity Planning Deals With Which Of The Following Factors
May 10, 2025
-
Evaluating The Results Of A Marketing Decision Involves
May 10, 2025
-
Filter The Chart So The Misc Data Series Is Hidden
May 10, 2025
-
Which Of The Following Describe Internal Consulting Activity
May 10, 2025
-
All Of The Following Were Regulars At Cbgb Except
May 10, 2025
Related Post
Thank you for visiting our website which covers about Which Of The Following Is Used For Piping Natural Gas . We hope the information provided has been useful to you. Feel free to contact us if you have any questions or need further assistance. See you next time and don't miss to bookmark.