Which Rivet Is Used For Riveting Magnesium Alloy Structures
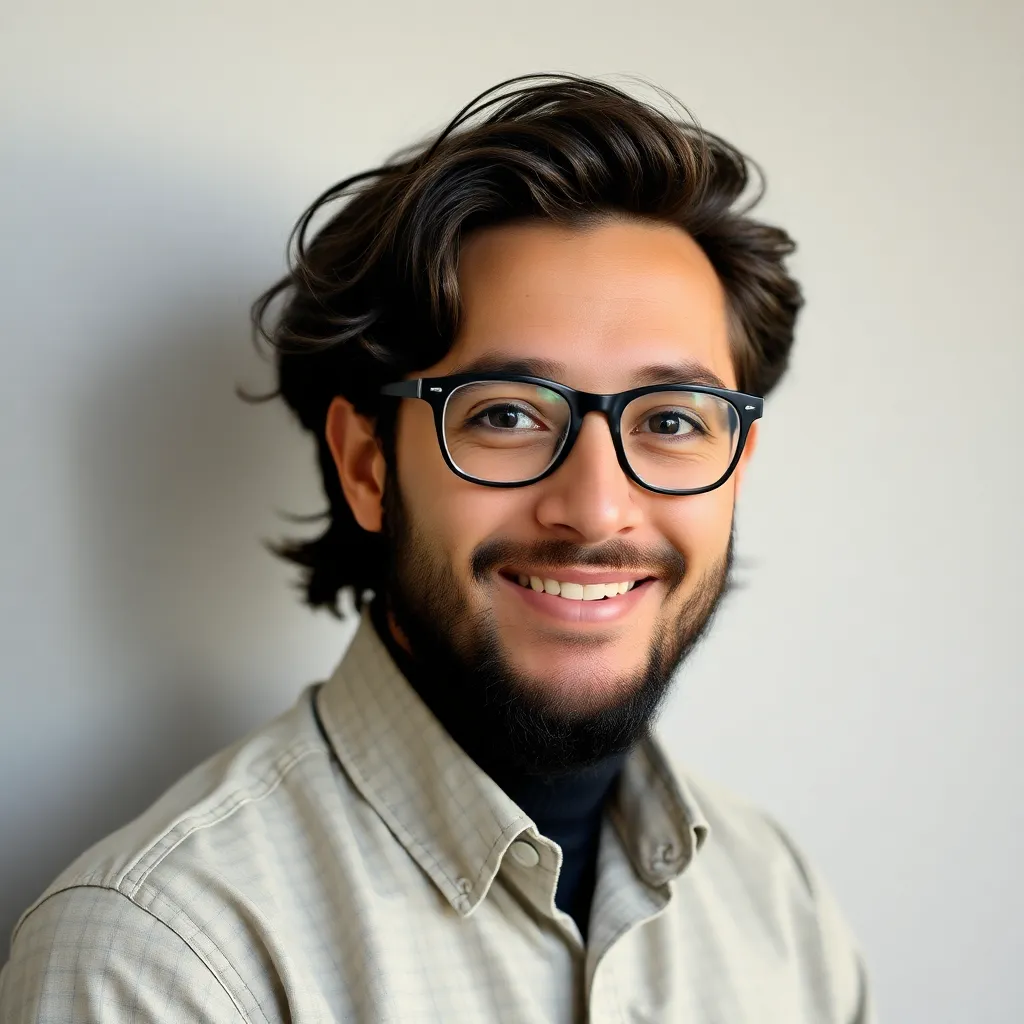
Onlines
May 11, 2025 · 6 min read
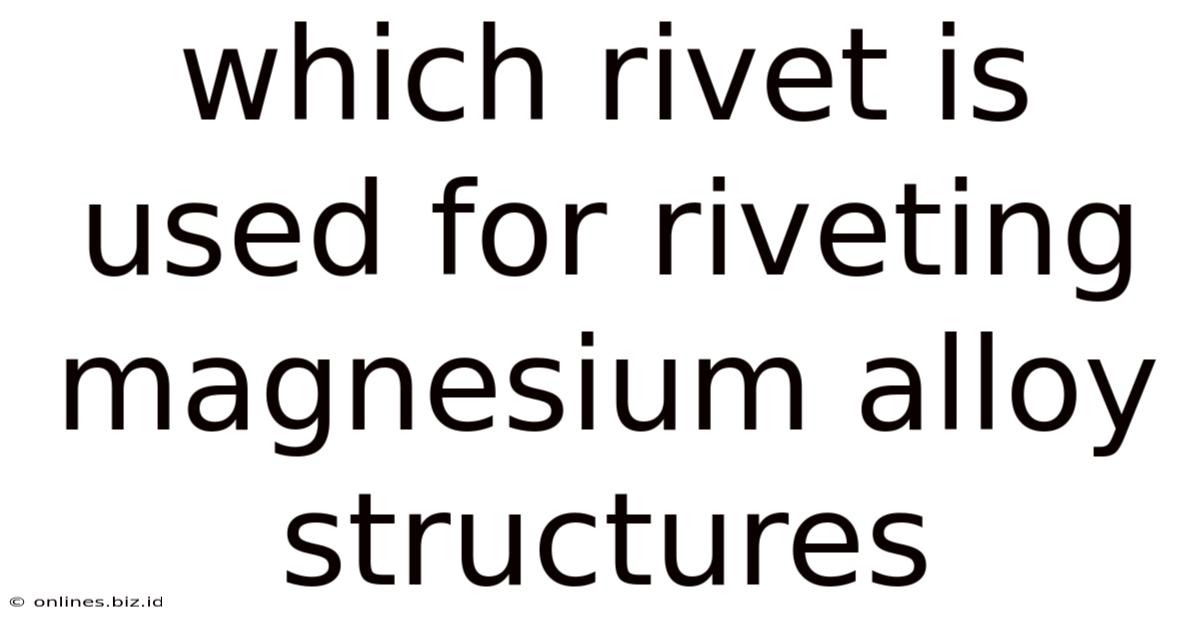
Table of Contents
Which Rivet is Used for Riveting Magnesium Alloy Structures?
Magnesium alloys, known for their exceptional strength-to-weight ratio and excellent corrosion resistance, find widespread use in aerospace, automotive, and electronics industries. However, their unique properties necessitate careful consideration when selecting fasteners, particularly rivets. Choosing the incorrect rivet can lead to joint failure, compromising the structural integrity of the entire assembly. This comprehensive guide delves into the specifics of riveting magnesium alloy structures, exploring the ideal rivet types, considerations for successful joining, and potential challenges.
Understanding Magnesium Alloys and Their Riveting Challenges
Magnesium alloys are relatively soft and ductile compared to other metals like aluminum or steel. This ductility, while beneficial in certain applications, presents challenges during riveting. The softness can lead to rivet squishing or excessive deformation under high clamping forces, potentially weakening the joint. Moreover, magnesium's susceptibility to galvanic corrosion when coupled with dissimilar metals requires careful selection of rivet materials to prevent premature joint failure. The inherent reactivity of magnesium also demands consideration of the riveting process itself, as improper techniques can lead to material damage and compromised joint strength.
The Importance of Proper Rivet Selection
The success of riveting magnesium alloy structures hinges on choosing the appropriate rivet type and material. The wrong choice can compromise joint strength, lead to premature failure, and potentially cause catastrophic consequences, especially in high-stress applications. Factors such as the alloy's specific properties, the required joint strength, and the environmental conditions must all be considered.
Types of Rivets Suitable for Magnesium Alloy Structures
Several rivet types exhibit characteristics suitable for magnesium alloy applications. However, some are more preferable than others depending on the specific needs of the project. Let's explore the common choices:
1. Aluminum Rivets
Aluminum rivets are often considered for joining magnesium alloys, primarily due to their relatively low cost and ease of installation. However, the galvanic corrosion potential must be carefully evaluated. Using an appropriate corrosion inhibitor or sealant is crucial when pairing aluminum with magnesium. Anodized aluminum rivets may offer improved corrosion resistance compared to standard aluminum rivets. The selection of aluminum alloy is also critical; those with higher strength and corrosion resistance are preferable. Consider the 2024-T3 or 6061-T6 aluminum alloys for increased durability.
2. Magnesium Rivets
Ideally, using magnesium rivets is the best solution for minimizing galvanic corrosion. These rivets offer excellent compatibility with magnesium alloys, ensuring minimal risk of corrosion-induced joint failure. However, magnesium rivets can be more challenging to install due to their softer nature, demanding careful control of the riveting process to prevent excessive deformation. The selection of the specific magnesium alloy for the rivet is crucial, prioritizing those with superior strength and formability characteristics.
3. Titanium Rivets
Titanium rivets provide excellent strength, corrosion resistance, and high-temperature capabilities. Their use in magnesium alloy structures, however, is typically limited to high-performance applications where superior strength and corrosion resistance are paramount, due to their higher cost. Titanium's compatibility with magnesium is relatively good, reducing the risk of galvanic corrosion. However, proper surface preparation and potentially the application of a suitable sealant are still recommended for optimum performance.
Critical Considerations for Riveting Magnesium Alloys
Successful riveting of magnesium alloys extends beyond the selection of the right rivet. Several crucial factors influence the overall integrity and longevity of the joint:
1. Surface Preparation: A Crucial Step
Thorough surface preparation is paramount. The magnesium surfaces must be clean, free from oxides, and properly prepared before riveting. This usually involves cleaning with a suitable solvent, followed by mechanical cleaning techniques such as brushing or blasting to remove any contaminants. Proper surface preparation significantly enhances the bond between the rivet and the magnesium alloy, improving joint strength and preventing corrosion.
2. Rivet Installation Techniques
The riveting process itself requires precise control to avoid damaging the relatively soft magnesium alloy. Excessive force can lead to rivet squishing or deformation, compromising the joint's strength. The use of properly calibrated riveting tools and experienced personnel is essential to ensure a consistent and accurate riveting process. Careful monitoring of rivet head formation is necessary to prevent squeezing the magnesium alloy excessively.
3. Corrosion Prevention
Galvanic corrosion is a major concern when riveting magnesium alloys, particularly when using dissimilar metals. Implementing appropriate corrosion prevention strategies is essential for the longevity of the joint. This might include using corrosion inhibitors, sealants, or applying protective coatings to the joint after riveting. The selection of the coating should be based on the specific application and environmental conditions.
4. Joint Design and Analysis
The design of the rivet joint itself significantly impacts its strength and reliability. Finite element analysis (FEA) or similar methods are often employed to optimize joint design, considering factors such as rivet diameter, pitch, and edge distance. This approach ensures that the joint can withstand the expected loads and environmental conditions throughout its service life. Proper joint design significantly reduces the likelihood of premature failure.
5. Quality Control and Inspection
Rigorous quality control and inspection procedures are crucial throughout the riveting process. Visual inspection of the rivet heads and the surrounding magnesium alloy is essential. Techniques such as radiographic inspection or ultrasonic testing may be used to detect internal flaws or defects within the joint. Implementing robust quality control protocols ensures the integrity and reliability of the riveted structure.
Choosing the Right Rivet: A Case-by-Case Approach
The "best" rivet for a magnesium alloy structure depends heavily on several interconnected factors:
- Application: High-stress aerospace components necessitate stronger and more corrosion-resistant rivets (titanium) than less demanding applications (aluminum).
- Budget: Magnesium rivets might be preferable from a corrosion perspective, but aluminum rivets often represent a more cost-effective solution.
- Environmental Conditions: Exposure to harsh environments may demand superior corrosion protection, favoring titanium or meticulously sealed aluminum rivets.
- Maintenance Requirements: Ease of maintenance might sway the decision towards a rivet type that is easier to replace or repair.
Conclusion: A Holistic Approach to Riveting Magnesium Alloys
Riveting magnesium alloy structures requires a meticulous and comprehensive approach. While several rivet types are suitable, the ultimate selection must consider a multitude of factors, from the alloy's specific properties and the application's demands to the environmental conditions and cost constraints. Surface preparation, meticulous installation techniques, and robust corrosion prevention strategies are equally crucial for ensuring the long-term integrity and reliability of the riveted structure. A thorough understanding of these aspects, coupled with rigorous quality control measures, is paramount for the success of any magnesium alloy riveting project. Remember that consulting with materials engineers and experienced professionals is highly recommended to determine the optimal rivet type and process for specific applications, especially for those demanding high structural integrity and reliability. This holistic approach minimizes the risk of joint failure and ensures the successful and safe performance of the final product.
Latest Posts
Latest Posts
-
The Average Manufacturing Overhead Cost Per Unit Tends To
May 12, 2025
-
Salvation Is Only Experienced In Fullness In The Future
May 12, 2025
-
The Cpr Coach Role Can Be Blended
May 12, 2025
-
What Is A Major Tenet Of Pure Land Buddhism
May 12, 2025
-
A C Way Reen Request Must Be Submitted
May 12, 2025
Related Post
Thank you for visiting our website which covers about Which Rivet Is Used For Riveting Magnesium Alloy Structures . We hope the information provided has been useful to you. Feel free to contact us if you have any questions or need further assistance. See you next time and don't miss to bookmark.