Which Statement Is True Regarding Flattening Of Tubing In Bends
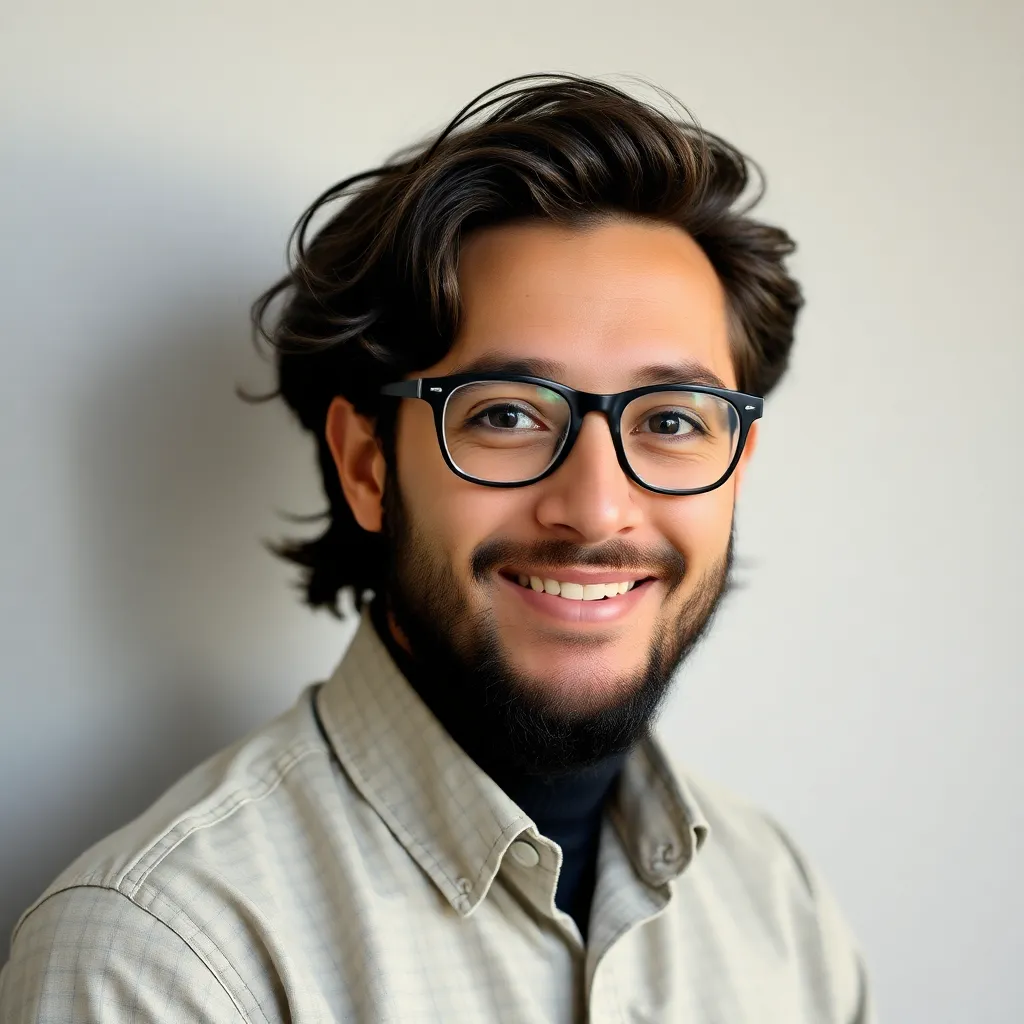
Onlines
May 09, 2025 · 5 min read
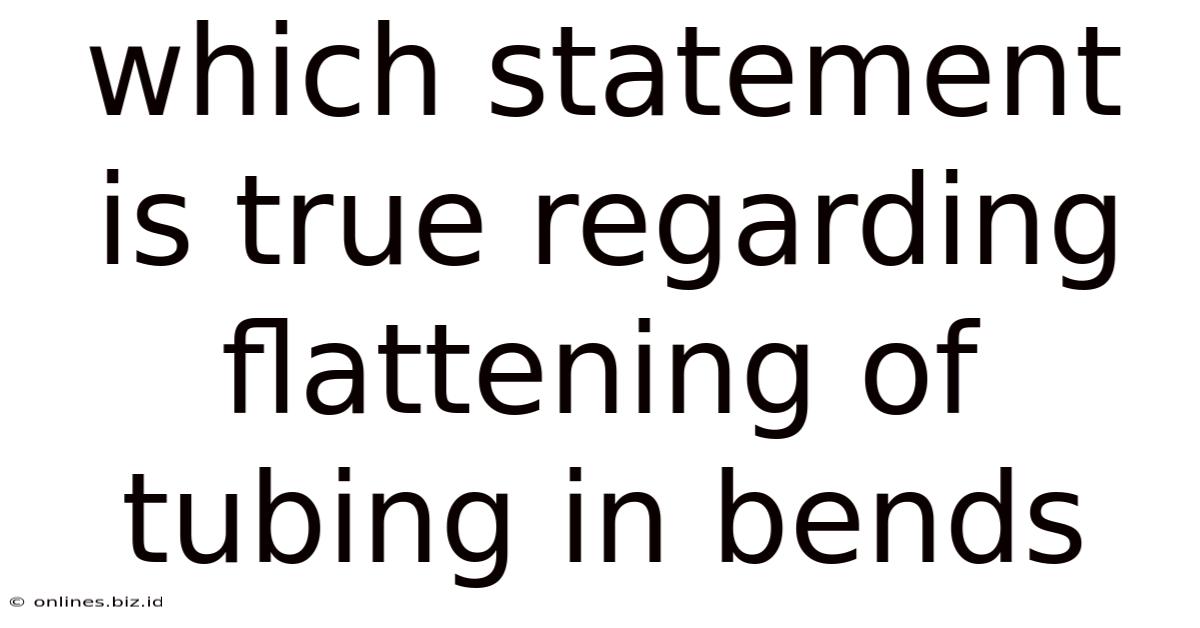
Table of Contents
Which Statement is True Regarding Flattening of Tubing in Bends? A Comprehensive Guide
Tube bending is a crucial process across numerous industries, from automotive and aerospace to medical devices and furniture manufacturing. Understanding the potential for defects, such as flattening in bends, is paramount for ensuring product quality, safety, and longevity. This comprehensive guide explores the complexities of tubing flattening during bending, examining various contributing factors, mitigation techniques, and the ultimate truth behind common statements regarding this phenomenon.
Understanding Tube Flattening in Bends
Tube flattening, also known as collapse or ovalization, occurs when the circular cross-section of a tube deforms into an elliptical or flattened shape during the bending process. This deformation can significantly weaken the tube, reducing its structural integrity and potentially leading to failure under pressure or stress. The degree of flattening is influenced by several interacting factors, making it a complex issue requiring careful consideration.
Factors Contributing to Tube Flattening
Several factors can contribute to the flattening of tubing in bends. These include:
-
Bend Radius: The most significant factor is the bend radius. A smaller bend radius leads to higher stresses on the outer and inner walls of the tube, increasing the likelihood of flattening. Conversely, a larger bend radius allows for a more gradual bend, reducing stress and minimizing flattening.
-
Tube Wall Thickness: Thicker-walled tubes generally exhibit greater resistance to flattening. Thinner-walled tubes, however, are more susceptible due to their reduced structural rigidity. This is because thinner walls have less material to resist the compressive forces acting on the inner radius during bending.
-
Tube Material: The material properties of the tube significantly influence its susceptibility to flattening. Ductile materials are more resistant to flattening compared to brittle materials. The material's yield strength, tensile strength, and Young's modulus all play a critical role in determining its response to bending stresses.
-
Bending Process: The method used for bending also plays a role. Mandrel bending, which utilizes a mandrel to support the inside of the tube during bending, significantly reduces the risk of flattening. Conversely, free bending, where no internal support is used, is more likely to result in flattening.
-
Bending Equipment: The precision and condition of the bending equipment can impact the final product. Poorly maintained or improperly calibrated equipment can increase the likelihood of flattening.
-
Lubrication: Insufficient lubrication during the bending process can increase friction and lead to increased stress concentration, promoting flattening. Adequate lubrication reduces friction and allows for a smoother, more controlled bend.
Debunking Common Statements
Several statements regarding tube flattening circulate within the manufacturing industry. Let's examine the truth behind some of these:
Statement 1: "All tubing will flatten to some degree during bending."
Truth: This statement is partially true. While some degree of deformation is almost inevitable in most bending processes, the extent of flattening is highly variable and depends heavily on the factors mentioned earlier. Careful process control can minimize, but not always eliminate, flattening entirely. Optimized bending parameters and the use of appropriate techniques can significantly reduce, and in many cases, prevent noticeable flattening.
Statement 2: "Mandrel bending always prevents flattening."
Truth: This statement is generally true, but not always. While mandrel bending is highly effective at reducing or preventing flattening, the effectiveness depends on the correct selection of mandrel size and material. An improperly sized or designed mandrel can actually worsen the problem by creating additional stress points. Therefore, careful consideration of mandrel selection is crucial for successful flattening prevention.
Statement 3: "Thicker-walled tubing is immune to flattening."
Truth: This statement is false. While thicker-walled tubing offers greater resistance to flattening, it's not entirely immune. Extremely tight bend radii, even with thick-walled tubing, can still result in some degree of flattening. The relationship between wall thickness and flattening resistance is not linear; there's a point of diminishing returns where further increases in wall thickness yield minimal improvement in flattening resistance.
Statement 4: "Material type has no significant impact on flattening."
Truth: This statement is false. The material's inherent properties significantly influence its susceptibility to flattening. Ductile materials, such as aluminum and copper, are generally more resistant to flattening compared to brittle materials, such as cast iron or some types of steel. The elastic and plastic properties of the material define its behavior under stress.
Statement 5: "Increasing bend radius always solves flattening issues."
Truth: This statement is mostly true. Increasing the bend radius reduces the stresses on the tube wall, thereby minimizing flattening. However, there might be design constraints that limit the feasible bend radius. Furthermore, even with a large bend radius, other factors like material properties and bending techniques still play crucial roles.
Mitigation Techniques for Tube Flattening
Several effective techniques can help mitigate tube flattening during the bending process:
-
Mandrel Bending: This technique utilizes a mandrel to support the inside of the tube during bending, effectively preventing collapse. Proper mandrel selection is vital for success.
-
Wavy Mandrel Bending: Utilizing a wavy mandrel, instead of a smooth one, can help further reduce flattening issues, particularly on tighter bends.
-
Fillers: Using fillers, such as sand, resin, or water, inside the tube can provide internal support and reduce the risk of flattening. The filler must be carefully chosen based on the tube material and process.
-
Proper Lubrication: Adequate lubrication during the bending process is crucial for minimizing friction and preventing excess stress concentration.
-
Controlled Bending Speed: Maintaining a slow and controlled bending speed can prevent sudden stress buildup and reduce the risk of flattening.
-
Pre-bending and Post-bending Processes: These processes involve careful preparation and finishing to minimize or correct minor imperfections.
-
Optimized Bending Parameters: Careful selection of bending parameters based on the specific tube material, dimensions, and desired bend radius is crucial for success.
Conclusion: The Importance of Precision and Control
The occurrence of tube flattening during bending is a complex issue influenced by various interacting factors. While some degree of deformation might be unavoidable, implementing the appropriate mitigation strategies and understanding the limitations of different statements can significantly minimize this issue. Careful selection of the bending process, materials, equipment, and parameters is crucial for achieving high-quality, defect-free bends. Precision and control are paramount in preventing tube flattening and ensuring the structural integrity and longevity of the final product. Prioritizing these factors through careful planning and execution is key to success in tube bending operations. The overarching truth is that a combination of understanding the contributing factors and employing appropriate mitigation strategies is the most effective approach to minimizing or eliminating tube flattening.
Latest Posts
Latest Posts
-
Assumptions Can Help You When Taking A Test
May 11, 2025
-
Research Suggests That Women Are More Skilled Than Men At
May 11, 2025
-
Which Letter In Figure 1 Represents Meiosis Why
May 11, 2025
-
All Of These Artists Recorded For Sun Records Except
May 11, 2025
-
Which Task Requires Da Pam 700 107 Guidance
May 11, 2025
Related Post
Thank you for visiting our website which covers about Which Statement Is True Regarding Flattening Of Tubing In Bends . We hope the information provided has been useful to you. Feel free to contact us if you have any questions or need further assistance. See you next time and don't miss to bookmark.