Which Storage Device Uses Aluminum Platters For Storing Data
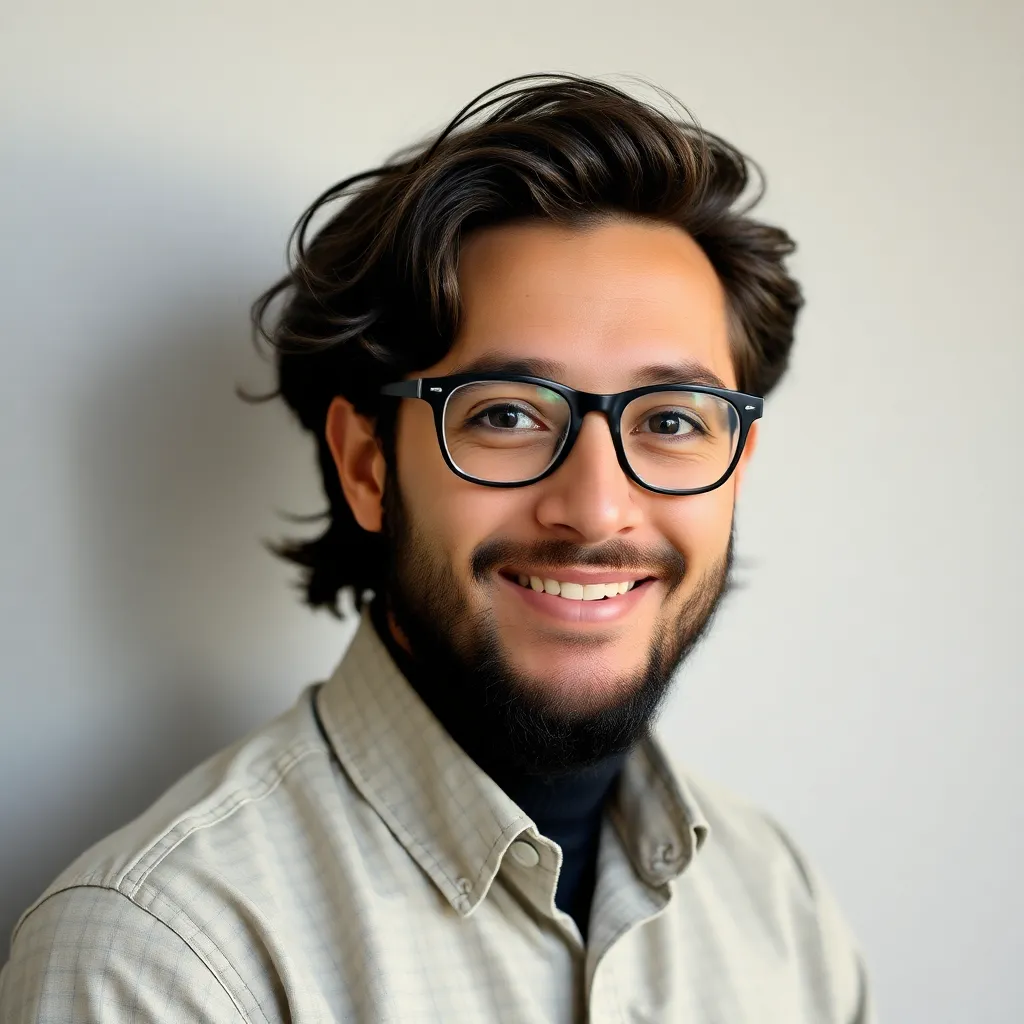
Onlines
Apr 22, 2025 · 6 min read

Table of Contents
Which Storage Device Uses Aluminum Platters for Storing Data?
The world of data storage is constantly evolving, with new technologies emerging to meet the ever-increasing demands for capacity and speed. While solid-state drives (SSDs) are rapidly gaining popularity, understanding the history and continued relevance of traditional hard disk drives (HDDs) remains crucial. One key component that defines the architecture of HDDs, and sets them apart from SSDs, is the use of aluminum platters for storing data. This article delves deep into the specifics of HDDs, exploring why aluminum is the preferred material, the manufacturing process, and the ongoing relevance of this technology in a modern context.
Understanding Hard Disk Drives (HDDs)
Hard disk drives, often referred to as HDDs, are electromechanical data storage devices that use magnetic storage to store and retrieve digital information using one or more rigid rapidly rotating platters coated with magnetic material. These platters are the heart of the HDD, responsible for holding the actual data. Unlike SSDs, which rely on flash memory, HDDs use a physical mechanism for reading and writing data, making them fundamentally different in their operation and performance characteristics. Crucially, these platters are almost universally made from aluminum.
The Role of Aluminum Platters
Aluminum's properties make it exceptionally well-suited for HDD platters. Several key characteristics contribute to its widespread adoption:
-
Lightweight yet Durable: Aluminum offers a good balance of strength and lightness. This is crucial for the high-speed rotation of the platters within the HDD casing. The platters need to be strong enough to withstand the centrifugal forces generated during rotation, yet lightweight enough to minimize power consumption and mechanical stress.
-
Cost-Effective: Compared to other materials with similar properties, aluminum is relatively inexpensive to produce and manufacture into the precise shapes required for HDD platters. This cost-effectiveness is vital for maintaining the affordability of HDDs, especially for large-capacity drives.
-
Excellent Thermal Conductivity: Aluminum possesses high thermal conductivity, which helps to dissipate heat generated during the drive's operation. This is essential for maintaining optimal operating temperatures and preventing performance degradation or data loss due to overheating.
-
Corrosion Resistance: While aluminum is susceptible to corrosion under certain conditions, it is generally resistant to the types of corrosion that would significantly impact the integrity of the platter surface. Proper coatings and manufacturing processes mitigate potential corrosion issues.
-
Precise Machining Capabilities: Aluminum can be easily machined to the precise tolerances required for creating the highly accurate surface finish necessary for reliable data storage. The smooth surface of the platter is critical for achieving high data density and minimizing read/write errors.
The Manufacturing Process of Aluminum Platters
The creation of aluminum platters for HDDs is a complex and precise process, involving several critical stages:
-
Aluminum Ingot Preparation: The process begins with high-purity aluminum ingots. These ingots are carefully inspected for defects and impurities that could compromise the quality of the final platter.
-
Rolling and Annealing: The aluminum ingots are then rolled into thin sheets using specialized rolling mills. This rolling process reduces the thickness of the aluminum to the desired level for the platters. Annealing, a heat treatment process, is used to relieve internal stresses and improve the mechanical properties of the aluminum sheet.
-
Cutting and Machining: Once the aluminum sheet reaches the desired thickness, it is precisely cut into circular blanks using high-precision cutting tools. These blanks are then further machined to achieve the exact dimensions and surface finish required for the platters. This step involves meticulous control over factors like surface roughness and flatness to ensure data integrity.
-
Coating and Polishing: The aluminum platters are then coated with a thin layer of magnetic material, typically a mixture of metallic alloys or magnetic oxides. This coating is essential for the magnetic recording of data. After the coating is applied, the platters undergo a polishing process to achieve an extremely smooth and even surface, further enhancing the accuracy of data storage and retrieval.
-
Inspection and Testing: Throughout the entire manufacturing process, rigorous quality control measures are employed to ensure that the platters meet stringent specifications. This includes inspections for surface defects, dimensional accuracy, and magnetic properties. Only platters that pass these stringent tests are used in HDDs.
-
Assembly into HDDs: Finally, the manufactured aluminum platters are assembled into the hard disk drive, along with the read/write heads, spindle motor, and other components. The entire assembly is then rigorously tested to ensure its reliability and performance.
Alternatives to Aluminum and their Limitations
While aluminum is the dominant material for HDD platters, research into alternative materials continues. However, no material has yet effectively surpassed aluminum in terms of cost-effectiveness, performance, and overall suitability.
Some potential alternatives have been explored, but each presents significant limitations:
-
Glass: Glass offers excellent dimensional stability and could potentially support higher data densities. However, it is far more brittle and expensive than aluminum, making it impractical for mass production.
-
Ceramics: Similar to glass, ceramics possess high dimensional stability. However, they are even more expensive and challenging to manufacture to the required tolerances for HDD platters.
-
Other Metals: Other metals have been investigated, but they often lack the desirable combination of cost-effectiveness, lightweight strength, and thermal conductivity that aluminum provides.
The Ongoing Relevance of Aluminum Platters
Despite the rise of SSDs, HDDs remain a significant player in the data storage market, particularly for applications requiring massive storage capacity at a relatively low cost. This continued relevance is directly tied to the effectiveness and affordability of aluminum platters. While SSDs excel in speed and durability, their cost per gigabyte remains significantly higher than HDDs, especially at the higher capacities.
The future of HDD technology will likely involve continued refinements in platter technology, focusing on:
-
Increased Platter Density: Techniques like heat-assisted magnetic recording (HAMR) and microwave-assisted magnetic recording (MAMR) are being developed to increase the data density on the platters, allowing for even larger storage capacities in the same physical space.
-
Improved Manufacturing Processes: Ongoing advancements in manufacturing processes will continue to improve the precision, efficiency, and cost-effectiveness of aluminum platter production.
-
Hybrid Technologies: We can also expect to see more hybrid storage solutions, combining the speed of SSDs with the high capacity and low cost of HDDs to provide a balance between performance and price.
Conclusion: Aluminum's Enduring Role in Data Storage
The use of aluminum platters in hard disk drives is a testament to the material's exceptional properties and its crucial role in enabling affordable, high-capacity data storage. While SSD technology is rapidly advancing, the inherent cost-effectiveness and performance characteristics of HDDs, largely enabled by the use of aluminum, ensure their continued relevance in the data storage landscape. Ongoing innovations in manufacturing and recording technologies will further enhance the capabilities of aluminum platters, maintaining their importance for years to come. The enduring legacy of aluminum in data storage is a clear indication of its enduring suitability and importance within the technology sector. As technology continues to evolve, the fundamental role of aluminum platters in HDDs will remain a critical component of the data storage ecosystem.
Latest Posts
Latest Posts
-
Comparing Mitosis And Meiosis Color By Answer
Apr 22, 2025
-
The Last Sentence Of The First Paragraph That Months Rent
Apr 22, 2025
-
How Often Should Tf Cbt Treatment Sessions Be Conducted
Apr 22, 2025
-
Completa Cada Oracion Con El Imperfecto Del Verbo Indicado
Apr 22, 2025
-
Rn Learning System Gerontology Final Quiz
Apr 22, 2025
Related Post
Thank you for visiting our website which covers about Which Storage Device Uses Aluminum Platters For Storing Data . We hope the information provided has been useful to you. Feel free to contact us if you have any questions or need further assistance. See you next time and don't miss to bookmark.