Why Should A Carburizing Flame Be Avoided When Welding Steel
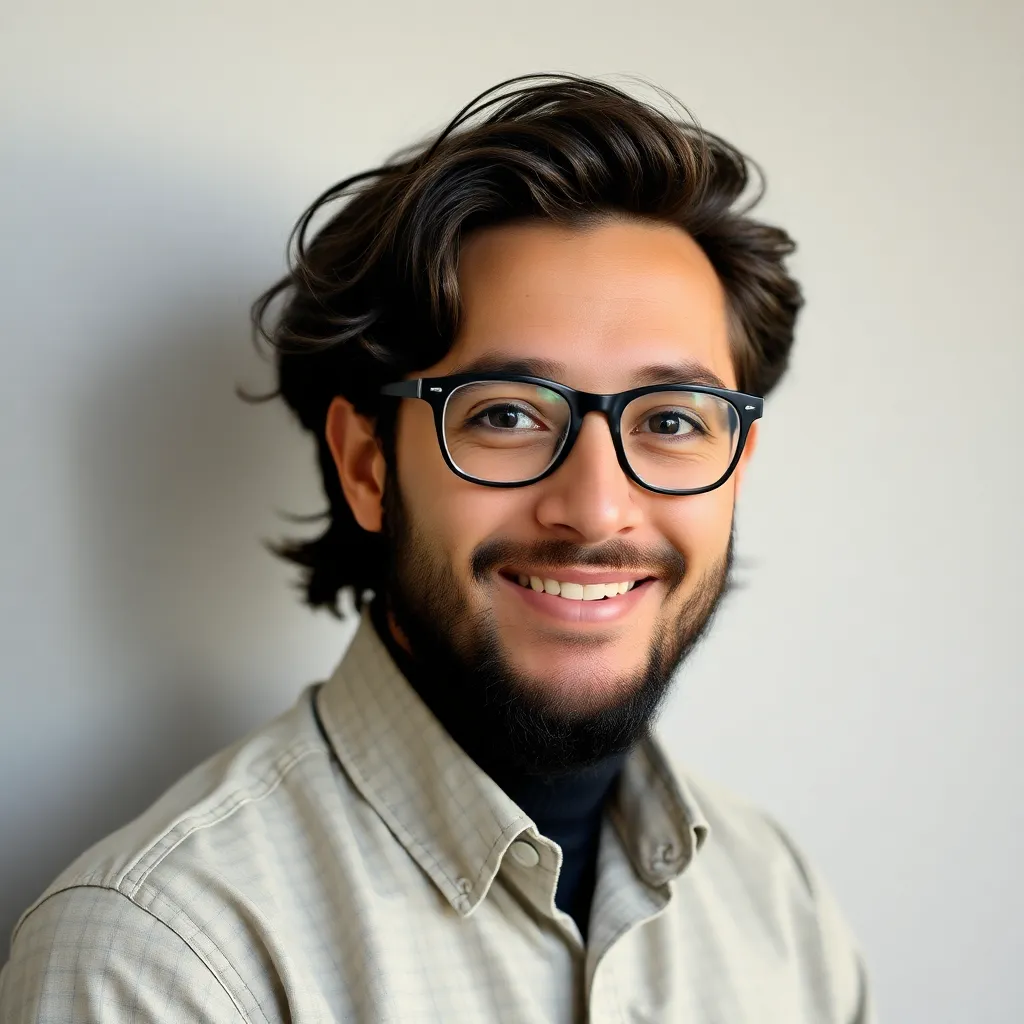
Onlines
May 10, 2025 · 6 min read
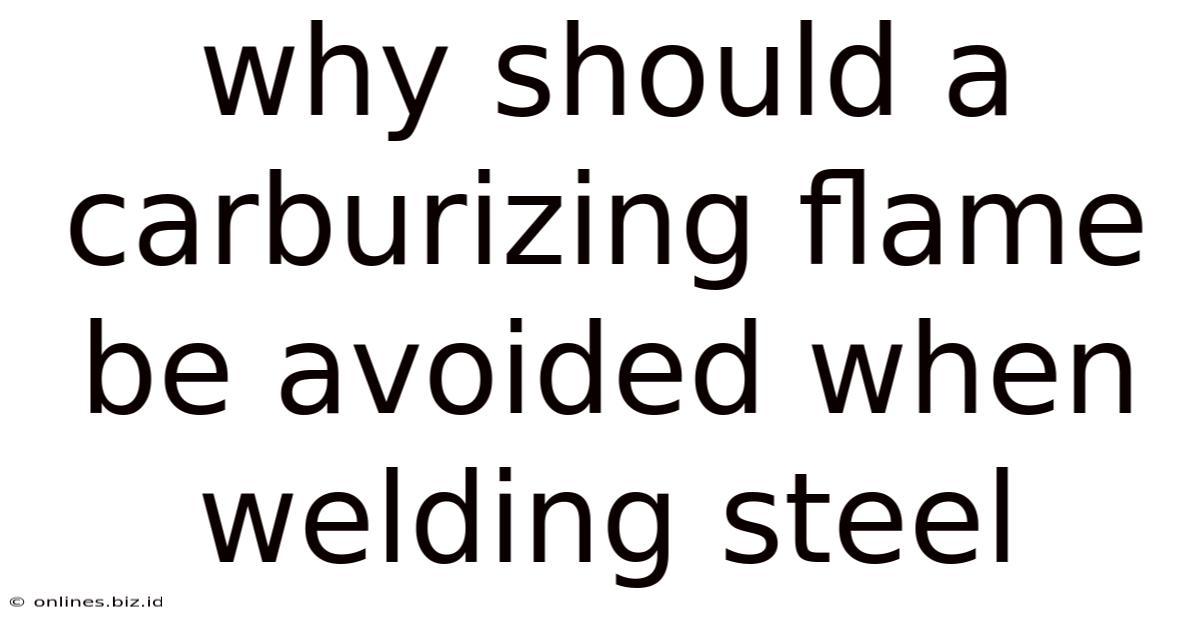
Table of Contents
Why You Should Avoid a Carburizing Flame When Welding Steel
Carburizing flames, while sometimes used in other metalworking processes, are detrimental to the quality and integrity of welds in steel. Understanding why this is crucial for welders of all skill levels. This article delves deep into the reasons behind avoiding carburizing flames during steel welding, exploring the negative consequences and offering practical alternatives for achieving strong, reliable welds.
Understanding Flame Types in Welding
Before discussing why carburizing flames should be avoided, let's clarify the different types of flames used in gas welding:
1. Neutral Flame: The Gold Standard
A neutral flame is characterized by its balanced fuel-to-oxygen ratio. It's the ideal flame for most steel welding applications because it provides the necessary heat without introducing significant chemical changes to the base metal. The inner cone is sharply defined, and the flame is relatively short and blue. A neutral flame minimizes oxidation and carbonization, leading to cleaner, stronger welds.
2. Oxidizing Flame: Too Much Oxygen
An oxidizing flame occurs when there's an excess of oxygen in the mixture. This leads to excessive oxidation of the molten steel, weakening the weld and potentially creating porosity. The flame is characterized by a long, pointed inner cone and a wispy, pale blue outer cone. Oxidizing flames are generally avoided, except in specific circumstances where surface oxidation is desired for a particular effect (not common in standard steel welding).
3. Carburizing Flame: Too Much Fuel
A carburizing flame is the opposite of an oxidizing flame. It has an excess of fuel, resulting in an abundance of unburned carbon. This excess carbon is absorbed into the molten weld pool, significantly altering its composition and properties. This flame is easily identified by its long, feathery inner cone and a luminous, yellow outer cone. This is the flame type that needs to be meticulously avoided during steel welding.
The Detrimental Effects of a Carburizing Flame on Steel Welds
Using a carburizing flame during steel welding can have several severe negative consequences:
1. Increased Carbon Content: Hardening and Brittleness
The most significant problem with a carburizing flame is the increased carbon content in the weld. The excess carbon in the flame diffuses into the molten steel, increasing its carbon concentration locally. This leads to a phenomenon called carburization. In many types of steel, this significantly increases the hardness of the weld zone. While increased hardness might seem beneficial, it unfortunately comes at the cost of reduced ductility and increased brittleness. This makes the weld significantly more susceptible to cracking under stress, dramatically decreasing its structural integrity and reliability.
2. Weld Cracking: A Major Structural Risk
The increased brittleness caused by carburization drastically increases the risk of weld cracking. Even minor stresses, either during the welding process itself or during subsequent service, can cause cracks to propagate through the brittle weld zone. These cracks can lead to catastrophic failure, especially in applications where the welded component experiences significant load or vibration. This is a major safety concern, particularly in critical engineering applications.
3. Formation of Hard Spots: Localized Weakness
The carburized areas within the weld will be significantly harder than the surrounding base metal. These hard spots are highly susceptible to cracking and represent localized zones of weakness in an otherwise hopefully strong weld. The difference in hardness between the carburized weld and the surrounding metal creates internal stresses, making the weld prone to cracking and failure under stress.
4. Reduced Weldability: Challenging Subsequent Operations
The altered microstructure and increased hardness resulting from carburization significantly impact the weld's weldability. Subsequent welding or other metalworking operations (like machining) on a carburized weld become significantly more challenging and may even lead to further cracking or damage. This can increase manufacturing costs and lead to significant delays in the production process.
5. Loss of Tensile Strength: Compromised Structural Integrity
The increased brittleness and the formation of hard spots lead to a reduction in the overall tensile strength of the weld. Tensile strength is a critical material property, representing the maximum stress a material can withstand before failing under tension. A carburized weld's reduced tensile strength undermines its structural integrity, compromising its load-bearing capacity. This poses a significant risk, especially in structures and components designed to withstand heavy loads.
Practical Alternatives to Carburizing Flames
Avoiding carburizing flames during steel welding is paramount. The following measures are crucial for ensuring high-quality welds:
1. Proper Flame Adjustment: Mastering the Neutral Flame
The most important step is to master the art of adjusting the gas mixture to achieve a perfectly neutral flame. This requires practice and attention to detail, observing the flame's characteristics and making adjustments to the gas flow until a sharply defined, short, blue inner cone is obtained. Consistent monitoring is essential, as slight fluctuations in gas pressure can easily alter the flame's character.
2. Using Proper Welding Techniques: Minimizing Contamination
Maintaining a consistent welding speed and technique is crucial to prevent contamination from the flame. Avoid prolonged heating of the base metal, which can lead to increased carbon absorption even with a near-neutral flame. Proper joint preparation, including cleaning and beveling, also minimizes the risk of introducing contaminants.
3. Choosing the Right Welding Rod: Matching the Base Metal
Selecting the appropriate welding rod is also vital. The welding rod should be chosen to match the base metal's chemical composition as closely as possible. This will minimize the possibility of significant chemical changes in the weld pool, even if a slightly oxidizing or carburizing flame is present momentarily (though this should still be avoided).
4. Post-Weld Heat Treatment: Addressing Minor Carburization
In some cases, despite the best efforts, minor carburization may still occur. In such situations, post-weld heat treatment can be employed to alleviate the negative effects of the increased carbon content. This heat treatment often involves carefully controlled annealing or normalizing processes to reduce the hardness and brittleness of the weld zone, improving its overall ductility and toughness.
5. Regular Inspection and Quality Control: Identifying Potential Defects
Regular inspection of welds during and after the welding process is essential for detecting any signs of carburization or other defects. Non-destructive testing techniques, such as visual inspection, magnetic particle inspection, and ultrasonic testing, are invaluable tools for ensuring the quality and integrity of the welds.
Conclusion: Prioritizing Weld Quality and Safety
Carburizing flames pose a significant threat to the quality, safety, and reliability of steel welds. The increased carbon content resulting from their use can lead to increased brittleness, cracking, reduced tensile strength, and difficulty in subsequent operations. Avoiding a carburizing flame is not merely a best practice; it's a critical requirement for producing strong, durable, and safe welds. By understanding the detrimental effects of carburization and employing the proper techniques and preventative measures discussed in this article, welders can ensure the integrity of their work and minimize the risk of catastrophic weld failures. Prioritizing weld quality and safety should always be the paramount concern.
Latest Posts
Latest Posts
-
Calculus Early Transcendentals 7th Edition Answers
May 10, 2025
-
Urbanization Began To Grow Especially Quickly After The
May 10, 2025
-
The Things They Carried Table Of Contents
May 10, 2025
-
Eliminating The Use Of Personality Tests In Employment Screening Will
May 10, 2025
-
Geologic Structures Maps And Block Diagrams Answer Key
May 10, 2025
Related Post
Thank you for visiting our website which covers about Why Should A Carburizing Flame Be Avoided When Welding Steel . We hope the information provided has been useful to you. Feel free to contact us if you have any questions or need further assistance. See you next time and don't miss to bookmark.