1.1 5 Gears Pulley Drives And Sprockets
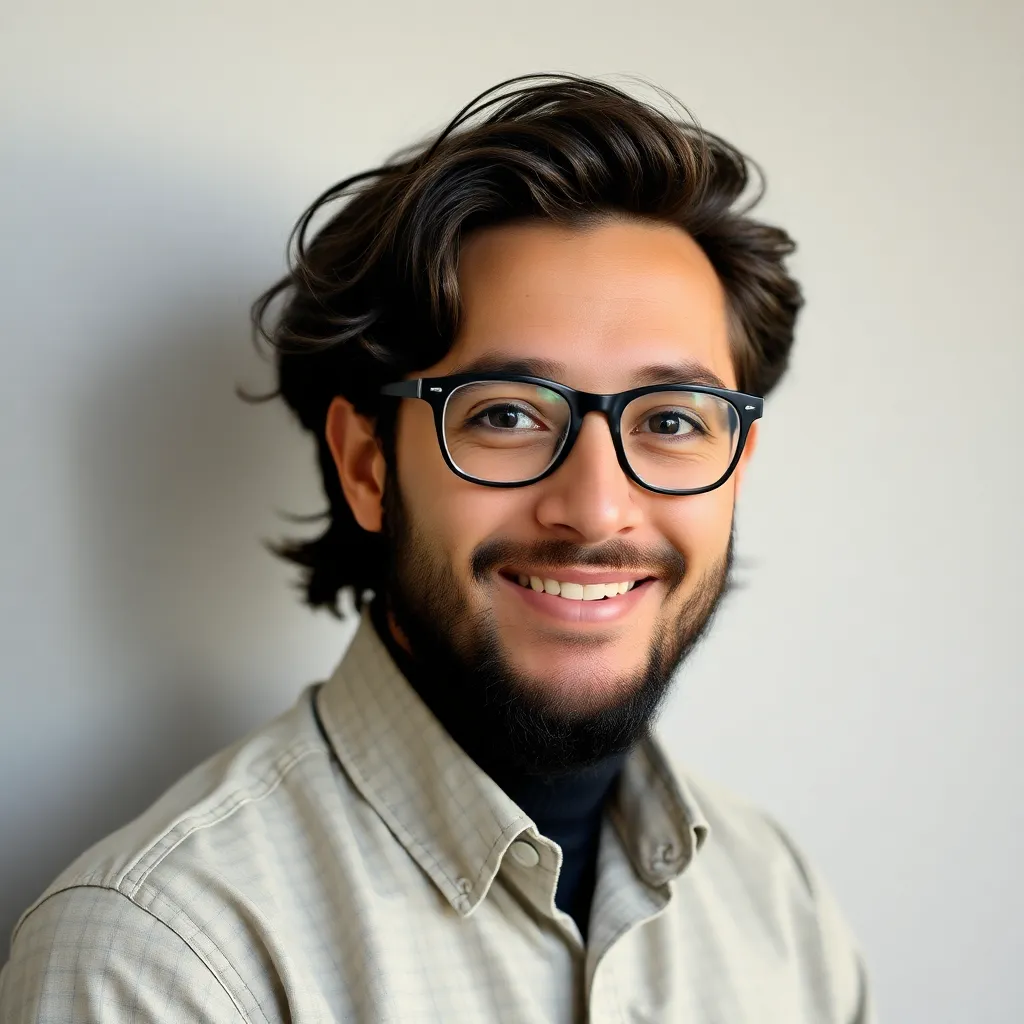
Onlines
Mar 28, 2025 · 6 min read

Table of Contents
1.1 5 Gears: Pulley Drives and Sprockets: A Deep Dive into Mechanical Power Transmission
The world of mechanical power transmission is a fascinating blend of engineering principles and practical applications. Understanding the different methods for transferring power from one rotating shaft to another is crucial in various industries, from automotive manufacturing to robotics and beyond. Among these methods, pulley drives and sprocket systems, often employing multiple gears, play a vital role. This article delves deep into the intricacies of 5-gear systems utilizing both pulleys and sprockets, exploring their design, applications, advantages, disadvantages, and considerations for optimal performance.
Understanding Pulley Drives
Pulley drives rely on the principle of friction to transmit power. A belt, typically made of rubber, leather, or other durable materials, wraps around two or more pulleys, transferring rotational motion from a driver pulley to a driven pulley. The diameter of the pulleys dictates the speed and torque ratios. Larger pulleys result in lower speed but higher torque, while smaller pulleys achieve higher speed with lower torque.
Types of Pulley Drives:
- Open Belt Drives: The belt runs on the outside of both pulleys, with the pulleys rotating in opposite directions.
- Cross Belt Drives: The belt crosses over between the pulleys, resulting in the pulleys rotating in the same direction.
- Quarter Turn Belt Drives: The pulleys are positioned at 90-degree angles, allowing for a change in the direction of power transmission.
Understanding Sprocket Drives
Sprocket drives, unlike pulley drives, utilize positive engagement. A chain, typically roller chain, meshes with teeth on the sprockets, providing a more reliable and precise power transmission. Sprocket drives are known for their higher efficiency and ability to handle heavier loads compared to belt drives. The speed and torque ratios are determined by the number of teeth on the sprockets.
Types of Sprocket Drives:
- Roller Chain Drives: The most common type, utilizing roller chains that engage with the teeth on the sprockets. These drives are highly efficient and robust, capable of withstanding significant loads.
- Silent Chain Drives: These chains run more quietly and smoothly than roller chains, often favored in applications requiring quieter operation.
5-Gear Systems: Combining Pulleys and Sprockets
Integrating five gears into a power transmission system can offer a variety of benefits, including:
- Precise Speed and Torque Ratios: A multi-gear system provides flexibility in achieving the desired speed and torque ratios for a specific application.
- Increased Efficiency: Strategic arrangement of gears can minimize energy losses due to friction.
- Enhanced Durability: Properly designed systems can distribute load more effectively, leading to increased component lifespan.
Example of a 5-Gear System using Pulleys and Sprockets:
Imagine a system designed for a conveyor belt mechanism. This system might utilize:
- A motor driving a small pulley: This provides the initial power source.
- A belt drive connecting the motor pulley to a larger pulley: This step reduces speed and increases torque.
- A sprocket connected to the larger pulley: This converts the rotational motion to a chain drive.
- A chain drive connecting two intermediate sprockets: These sprockets can be used to adjust the speed and torque further or change the direction of rotation.
- A final sprocket connected to the conveyor belt: This sprocket drives the conveyor belt at the required speed.
This example demonstrates how the combination of pulleys and sprockets allows for a versatile and efficient power transmission system. The size and number of teeth on each sprocket, as well as the pulley diameters, are carefully calculated to achieve the desired output speed and torque for the conveyor belt.
Advantages and Disadvantages of Using 5-Gear Systems
Employing 5-gear systems brings several advantages but also presents some challenges.
Advantages:
- Precise Control: The ability to manipulate speed and torque through multiple gear ratios provides superior control over the output power.
- High Efficiency: In well-designed systems, losses due to friction can be minimized, leading to high overall efficiency.
- Versatility: These systems can be adapted to a wide range of applications by carefully choosing the gear ratios and types of drives (pulleys or sprockets).
- Load Distribution: The load is distributed across multiple components, enhancing system durability and reducing wear on individual components.
Disadvantages:
- Complexity: A 5-gear system is more complex than a simpler system and requires careful design and assembly.
- Cost: The higher complexity translates into potentially higher manufacturing and maintenance costs.
- Space Requirements: More gears require more space for the system's physical layout.
- Synchronization Challenges: Ensuring proper synchronization between gears is crucial for optimal performance, and misalignment can lead to premature wear and failure.
Design Considerations for 5-Gear Systems
Designing a robust and efficient 5-gear system requires careful consideration of several factors:
- Gear Ratios: The selection of gear ratios is critical in determining the overall speed and torque of the system. This requires a thorough understanding of the application's requirements.
- Gear Materials: The material selection for the gears and other components must be based on the anticipated loads, speeds, and environmental conditions. Steel, aluminum, and various composites are common choices.
- Lubrication: Proper lubrication is essential to minimize friction and wear, extending the life of the system components.
- Alignment: Precise alignment of gears, pulleys, and shafts is crucial to prevent premature wear and ensure smooth operation. Misalignment can introduce excessive stress and lead to catastrophic failure.
- Safety Features: Incorporate safety features such as guards, overload protection, and emergency stops to ensure operator safety.
Applications of 5-Gear Systems
5-gear systems find application across various industries, including:
- Automotive Manufacturing: Used in assembly lines for precise control of machinery speed and torque.
- Robotics: Power transmission systems in robotic arms and manipulators require precise control and often utilize complex gear arrangements.
- Conveyor Systems: As previously mentioned, conveyor belts benefit from the control over speed and torque that multiple gears provide.
- Material Handling Equipment: Many material handling systems rely on multi-gear systems to optimize efficiency and prevent overloading.
- Packaging Machinery: The precise control of speed and torque in packaging machines is crucial for consistent output, and multi-gear systems are often employed.
Maintenance and Troubleshooting
Regular maintenance is crucial for extending the life of a 5-gear system:
- Lubrication Checks: Regularly inspect and replenish the lubricant as needed.
- Alignment Checks: Periodically check for gear misalignment and correct as necessary.
- Wear Inspection: Regularly inspect gears, pulleys, and chains for wear and tear. Replace worn components before they cause further damage.
- Noise Monitoring: Unusual noises can indicate problems such as misalignment, wear, or lubrication issues. Investigate any unusual sounds immediately.
Conclusion
5-gear systems utilizing pulleys and sprockets provide a versatile and efficient solution for various power transmission applications. While more complex than simpler systems, the advantages in terms of precise control, high efficiency, and load distribution make them ideal for many demanding tasks. However, careful consideration of design parameters, material selection, and regular maintenance are vital to ensuring the system's longevity and optimal performance. Understanding the intricacies of these systems allows engineers and technicians to effectively utilize their capabilities while mitigating potential challenges. The continuous advancement in materials science and manufacturing processes continues to refine the capabilities and reliability of these power transmission systems.
Latest Posts
Latest Posts
-
An Evemt Planning Company Hired A New Marketing
Mar 31, 2025
-
Stopping Is Prohibited At Which Of The Following
Mar 31, 2025
-
The Operating Principle Of Float Type Carburetors Is Based On The
Mar 31, 2025
-
Cellular Respiration Escape Room Answer Key
Mar 31, 2025
-
What Are Larger Data Rooms Also Known As
Mar 31, 2025
Related Post
Thank you for visiting our website which covers about 1.1 5 Gears Pulley Drives And Sprockets . We hope the information provided has been useful to you. Feel free to contact us if you have any questions or need further assistance. See you next time and don't miss to bookmark.