A Pressure Regulator Valve Ensures That:
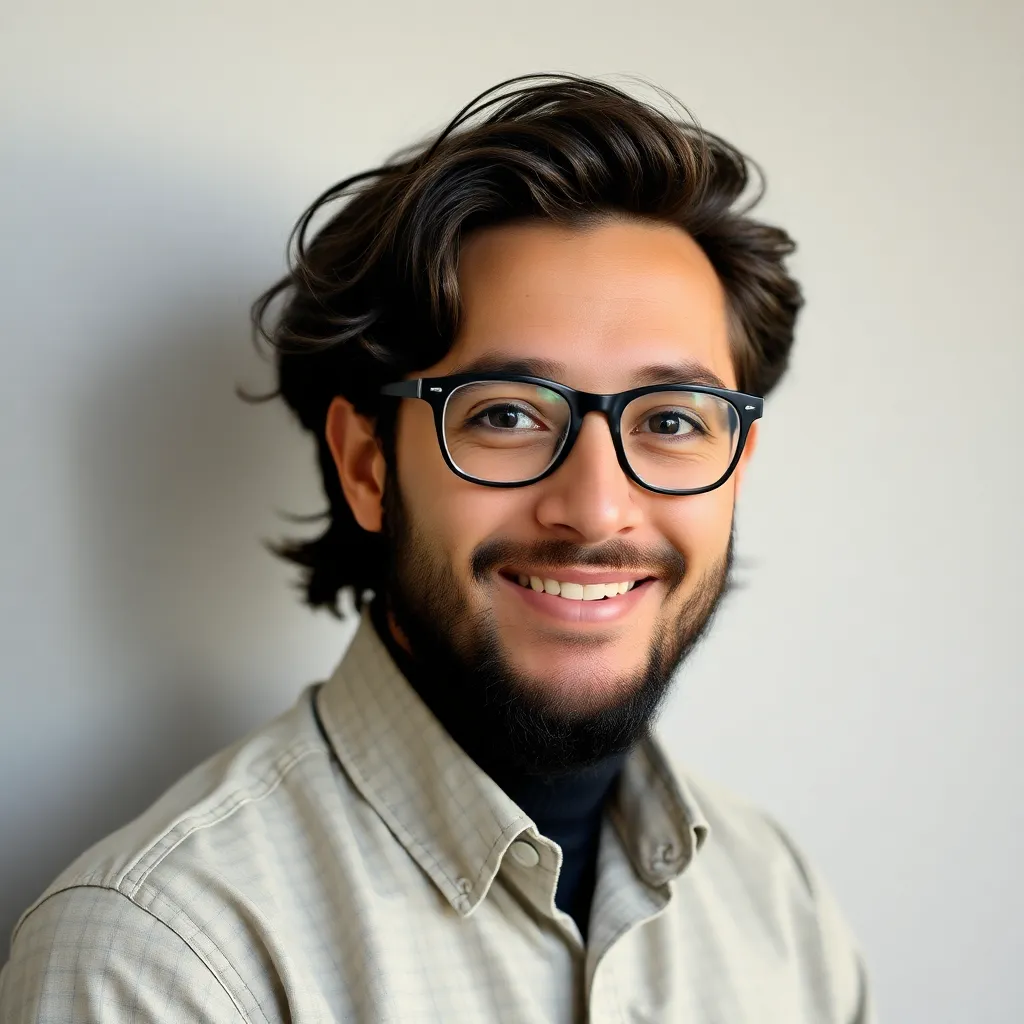
Onlines
May 10, 2025 · 6 min read
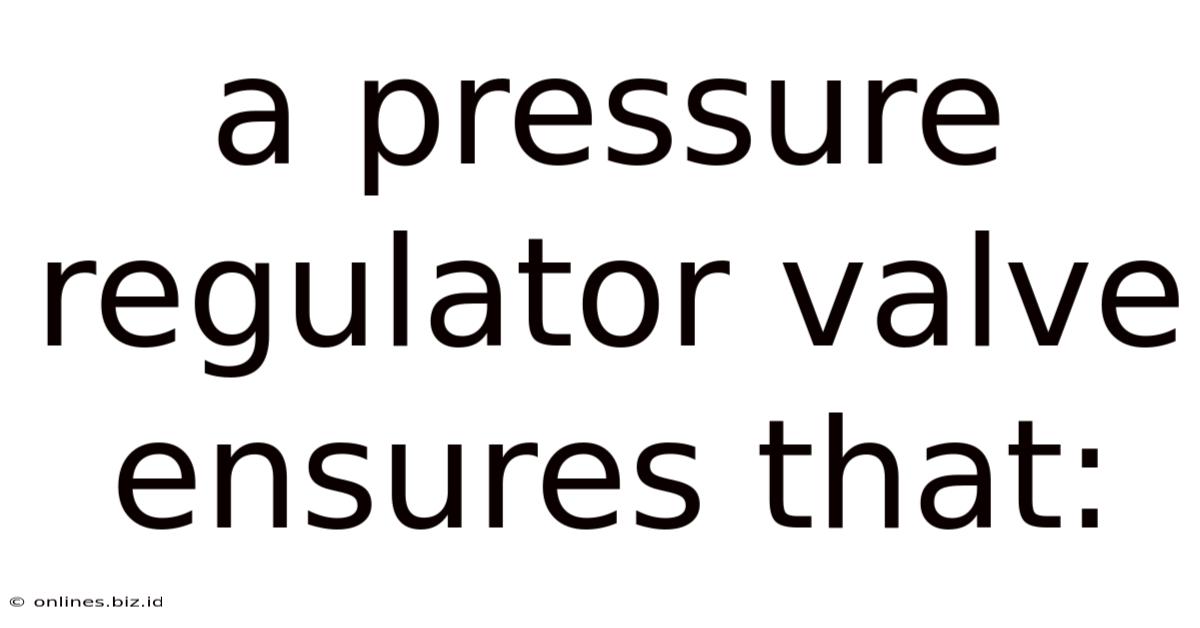
Table of Contents
A Pressure Regulator Valve Ensures: Consistent Performance and Safety in Your Systems
Pressure, a fundamental force in numerous industrial and domestic applications, demands precise control for optimal performance and safety. A pressure regulator valve, a crucial component in countless systems, plays a pivotal role in maintaining this control. Its primary function is to reduce and stabilize high-pressure input to a desired lower output pressure, regardless of fluctuations in the supply. This article delves into the intricacies of pressure regulator valves, exploring their mechanisms, applications, types, and the critical role they play in ensuring consistent performance and safety across diverse industries.
Understanding the Function of a Pressure Regulator Valve
At its core, a pressure regulator valve is a sophisticated control device that automatically maintains a consistent downstream pressure. It achieves this by modulating the flow of a fluid (gas or liquid) based on the pressure difference between the inlet and outlet sides. When the downstream pressure drops below the setpoint, the valve opens wider, increasing the flow. Conversely, if the downstream pressure rises above the setpoint, the valve constricts, reducing the flow. This continuous feedback loop ensures stable pressure output despite variations in upstream pressure or downstream demand.
Key Components and Operating Principles
Pressure regulator valves utilize several key components to achieve this precise control:
- Diaphragm: A flexible membrane that acts as a pressure-sensing element. Changes in downstream pressure cause the diaphragm to deflect, influencing the valve's opening.
- Spring: A calibrated spring counteracts the pressure exerted by the diaphragm. The spring tension determines the setpoint pressure.
- Valve Seat and Poppet: The valve seat provides a seal to control fluid flow, while the poppet is a movable element that opens and closes the valve orifice, regulating the flow rate.
- Inlet and Outlet Ports: Connections for the high-pressure input and the controlled, lower-pressure output.
The operating principle typically involves a balance of forces between the downstream pressure acting on the diaphragm and the spring force. The diaphragm's movement directly controls the poppet's position, which dictates the degree of flow restriction. This dynamic equilibrium maintains the desired downstream pressure.
Types of Pressure Regulator Valves
Pressure regulator valves come in a wide variety of designs, each tailored to specific applications and fluid characteristics. Some of the most common types include:
1. Spring-Loaded Pressure Regulators:
These are the most prevalent type, utilizing a spring to counteract the downstream pressure. They are simple, reliable, and cost-effective, making them suitable for a wide range of applications. Their simplicity also contributes to their ease of maintenance.
2. Pilot-Operated Pressure Regulators:
Pilot-operated regulators offer superior control and accuracy, particularly in high-pressure or high-flow applications. They utilize a small pilot valve to sense and regulate the main valve's operation, allowing for precise pressure control and faster response times. This makes them ideal for applications demanding tighter pressure tolerances.
3. Self-Relieving Pressure Regulators:
These regulators incorporate a relief valve mechanism to prevent over-pressurization of the downstream system. If the downstream pressure exceeds the setpoint, the relief valve opens, releasing excess pressure and protecting the system from damage. This feature enhances safety in applications where pressure surges are possible.
4. Back Pressure Regulators:
Unlike the aforementioned regulators, which control downstream pressure, back pressure regulators maintain a consistent pressure upstream of the valve. They are used to prevent excessive pressure buildup in a pipeline or system.
5. Pressure Reducing Valves (PRVs):
Often used interchangeably with pressure regulator valves, PRVs specifically focus on reducing pressure from a higher inlet pressure to a lower, controlled outlet pressure. They are commonly found in water supply systems and industrial processes requiring consistent pressure reduction.
Applications Across Industries
The versatility of pressure regulator valves extends across a vast spectrum of industries and applications. Their critical role in ensuring safe and efficient operation makes them indispensable components in many systems.
1. Industrial Applications:
- Chemical Processing: Maintaining consistent pressures in reaction vessels and pipelines.
- Oil and Gas: Regulating pressures in pipelines, refineries, and processing plants.
- Manufacturing: Controlling pneumatic systems, hydraulic presses, and other machinery.
- Power Generation: Regulating steam and gas pressures in turbines and boilers.
2. Commercial Applications:
- HVAC Systems: Controlling air pressure in heating, ventilation, and air conditioning systems.
- Water Treatment: Regulating water pressure in distribution networks and treatment plants.
- Fire Suppression Systems: Maintaining consistent water pressure for effective fire suppression.
3. Domestic Applications:
- Natural Gas Supply: Regulating gas pressure for home appliances.
- Water Supply: Reducing water pressure to prevent damage to household plumbing.
- Irrigation Systems: Controlling water pressure for efficient irrigation.
Importance of Regular Maintenance and Inspection
Regular maintenance and inspection of pressure regulator valves are crucial for ensuring their continued reliable operation and preventing potential safety hazards. Neglecting maintenance can lead to:
- Inaccurate Pressure Control: Leading to inefficient operation and potential system damage.
- Leaks and Spills: Resulting in wasted resources and potential environmental hazards.
- System Failures: Causing disruptions in operations and potentially leading to safety incidents.
- Premature Valve Failure: Reducing the lifespan of the valve and increasing replacement costs.
A proper maintenance schedule should include regular visual inspections, checking for leaks and corrosion, and verifying that the valve is operating within its specified parameters. In many cases, professional servicing and calibration may be necessary to ensure the valve is functioning optimally.
Selecting the Right Pressure Regulator Valve
Choosing the appropriate pressure regulator valve for a specific application requires careful consideration of several factors:
- Fluid Type: Gas, liquid, or other media will dictate valve material compatibility and design.
- Pressure Range: The inlet and outlet pressure requirements will determine the valve's capacity.
- Flow Rate: The volume of fluid to be regulated will influence valve size and design.
- Accuracy and Stability: The desired level of pressure control will impact the choice between spring-loaded and pilot-operated regulators.
- Environmental Conditions: Temperature, humidity, and other environmental factors may affect valve performance and material selection.
- Safety Requirements: Applications with strict safety regulations may necessitate valves with additional safety features, such as relief valves.
Consulting with a qualified specialist can assist in determining the most appropriate valve for your specific application.
Safety Precautions When Handling Pressure Regulator Valves
Pressure regulator valves, while essential for system control, can pose safety risks if not handled properly. Always adhere to the following precautions:
- Follow Manufacturer's Instructions: Always carefully review and follow the manufacturer's instructions for installation, operation, and maintenance.
- Pressure Relief: Ensure that adequate pressure relief mechanisms are in place to prevent over-pressurization.
- Proper Installation: Ensure correct installation to avoid leaks and ensure proper valve functionality.
- Personal Protective Equipment (PPE): Wear appropriate PPE, such as safety glasses and gloves, when handling or working on pressure regulator valves.
- Lockout/Tagout Procedures: Implement lockout/tagout procedures before performing maintenance or repair work to prevent accidental activation.
- Regular Inspection: Regularly inspect the valve for leaks, corrosion, and damage.
Conclusion: Ensuring System Integrity Through Precise Pressure Control
Pressure regulator valves are indispensable components in countless systems across diverse industries. Their ability to maintain consistent downstream pressure, despite fluctuations in upstream supply or downstream demand, is crucial for optimal performance, efficiency, and safety. Understanding the various types of pressure regulator valves, their operating principles, and the importance of regular maintenance is paramount for ensuring the reliable and safe operation of any system that employs them. By carefully selecting the appropriate valve and adhering to safety precautions, you can effectively manage pressure, enhance system integrity, and prevent potential hazards. Investing in proper maintenance and understanding the nuances of pressure regulation is crucial for maintaining optimal performance and safeguarding against potential risks.
Latest Posts
Latest Posts
-
When Total Steering Failure Occurs You First Should
May 10, 2025
-
Give The Major Organic Product Of The Following Reaction
May 10, 2025
-
Complete The Doubledown Function To Return Twice The Initialvalue
May 10, 2025
-
Which Of The Boxes Represents A Carbon Source
May 10, 2025
-
Adventures Of Huckleberry Finn Chapter 7 Summary
May 10, 2025
Related Post
Thank you for visiting our website which covers about A Pressure Regulator Valve Ensures That: . We hope the information provided has been useful to you. Feel free to contact us if you have any questions or need further assistance. See you next time and don't miss to bookmark.