A Standard Vacuum Pump Designed Specifically For Evacuation And Dehydration
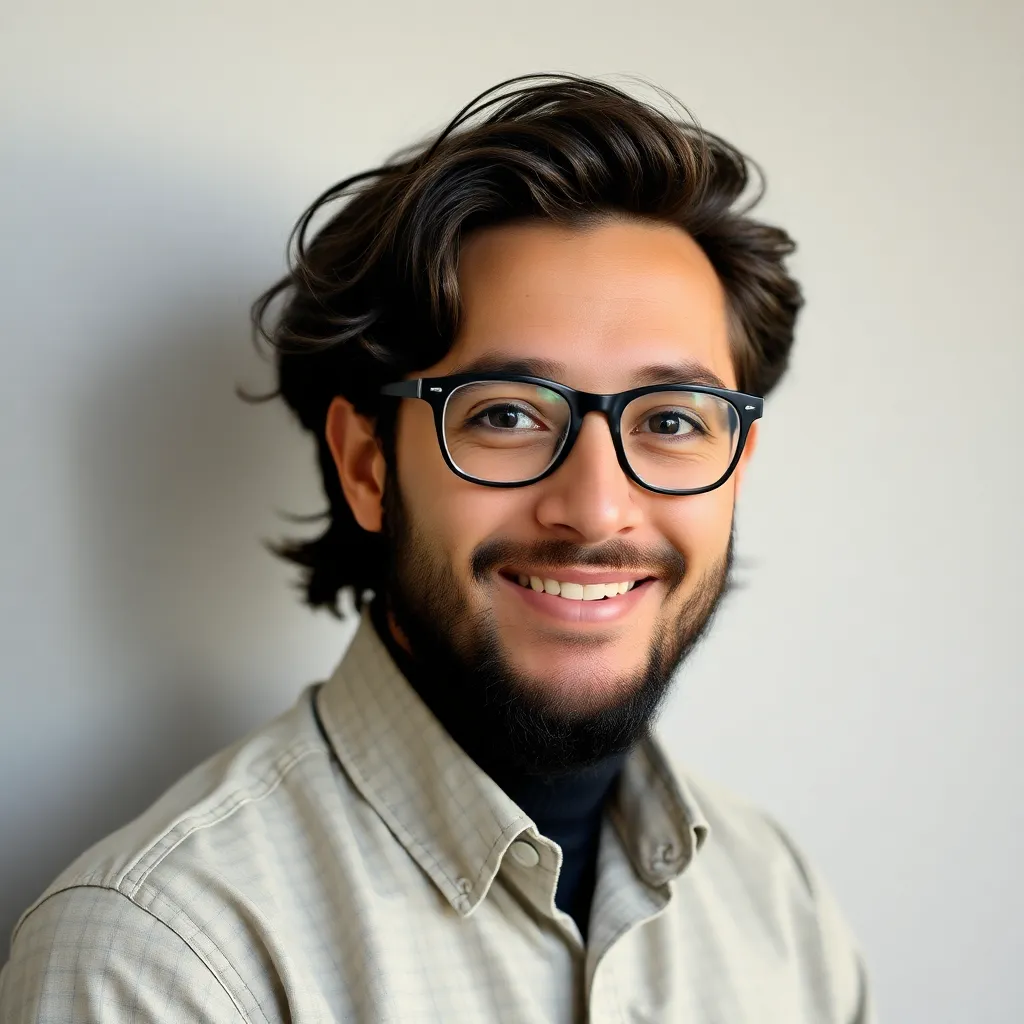
Onlines
Apr 06, 2025 · 6 min read
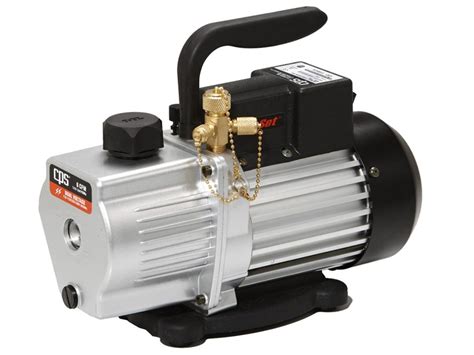
Table of Contents
Standard Vacuum Pumps for Evacuation and Dehydration: A Comprehensive Guide
Vacuum pumps are essential tools in various industries, playing a crucial role in processes requiring the removal of air or other gases from a specific space. One critical application is evacuation and dehydration, where the goal is to create a low-pressure environment to remove moisture and volatile organic compounds (VOCs) from materials or systems. This article delves into the intricacies of standard vacuum pumps designed for this specific purpose, exploring their design, functionality, applications, and critical selection considerations.
Understanding the Fundamentals of Vacuum Pumps for Evacuation and Dehydration
Before diving into the specifics, let's establish a foundational understanding. Evacuation, in this context, refers to the complete or partial removal of gases from a sealed chamber or container. Dehydration, often a consequence of evacuation, involves the removal of moisture content from a material or system. The combination of these processes is crucial in many applications requiring a dry, inert environment.
Standard vacuum pumps employed in these processes typically fall into several categories, each with its strengths and limitations:
1. Rotary Vane Pumps
These pumps are among the most prevalent types used for evacuation and dehydration. They feature a rotating rotor with vanes that slide within a cylindrical housing. As the rotor turns, it traps pockets of gas and pushes them out of the pump, creating a vacuum. Rotary vane pumps excel in handling higher gas flow rates and achieving relatively high vacuum levels, making them suitable for a wide range of applications. However, they are generally less effective at achieving ultra-high vacuum levels. Additionally, the vanes are subject to wear and tear, requiring periodic maintenance and replacement.
Advantages of Rotary Vane Pumps:
- High pumping speed: Effectively removes large volumes of gas quickly.
- Relatively high ultimate vacuum: Can achieve a decent vacuum level, although not ultra-high vacuum.
- Robust design: Generally durable and reliable.
- Wide range of applications: Suitable for numerous evacuation and dehydration tasks.
Disadvantages of Rotary Vane Pumps:
- Maintenance requirements: Vanes require periodic replacement.
- Oil lubrication: Often use oil for lubrication, potentially contaminating the process.
- Limited ultimate vacuum: Not suitable for applications demanding ultra-high vacuum.
2. Diaphragm Pumps
Diaphragm pumps employ a flexible diaphragm to create a vacuum. The diaphragm moves back and forth, increasing and decreasing the volume of the pump chamber, drawing in and expelling gas. These pumps are known for their oil-free operation, making them ideal for applications where contamination is a critical concern. However, they typically offer lower pumping speeds and achieve lower ultimate vacuum levels compared to rotary vane pumps.
Advantages of Diaphragm Pumps:
- Oil-free operation: Prevents contamination of the process.
- Chemical compatibility: Often resistant to a wide range of chemicals.
- Simple design: Relatively straightforward maintenance.
Disadvantages of Diaphragm Pumps:
- Lower pumping speed: Slower evacuation compared to rotary vane pumps.
- Lower ultimate vacuum: Cannot achieve the same high vacuum levels as rotary vane pumps.
- Limited lifespan: Diaphragms can wear out and require replacement.
3. Scroll Pumps
Scroll pumps are becoming increasingly popular, especially in applications requiring quiet operation and high reliability. They utilize two spiral-shaped scrolls that rotate against each other, trapping and compressing gas before venting it. Scroll pumps offer excellent performance in terms of quiet operation and long lifespan, while also providing a relatively high pumping speed. However, they typically cannot achieve extremely high vacuum levels.
Advantages of Scroll Pumps:
- Quiet operation: Ideal for noise-sensitive environments.
- Long lifespan: Durable and require minimal maintenance.
- High pumping speed: Efficiently removes large volumes of gas.
Disadvantages of Scroll Pumps:
- Limited ultimate vacuum: Cannot reach ultra-high vacuum levels.
- Higher initial cost: Generally more expensive than rotary vane or diaphragm pumps.
Critical Selection Considerations for Vacuum Pumps in Evacuation and Dehydration
Choosing the right vacuum pump for evacuation and dehydration depends on various factors. These include:
-
Required vacuum level: The ultimate pressure the system needs to reach. This dictates whether a rotary vane, diaphragm, or scroll pump is appropriate. Ultra-high vacuum applications require specialized pumps not discussed in this overview.
-
Pumping speed: The volume of gas the pump needs to remove per unit time. This is critical for determining the efficiency and overall processing time.
-
Gas composition: The type of gases being removed. Certain pumps are better suited for specific gases than others. For example, some pumps are more resistant to corrosive gases.
-
Contamination concerns: The need to prevent contamination of the process. Oil-free pumps are essential in many applications.
-
Budget: The cost of the pump, including initial investment, maintenance, and replacement parts.
-
Maintenance requirements: The level of maintenance needed, considering the frequency and cost of repairs or part replacements.
-
Noise levels: The acceptable noise level for the application. Scroll pumps excel in noise reduction.
-
Environmental considerations: The pump's environmental impact, such as energy consumption and potential emissions.
Applications of Vacuum Pumps in Evacuation and Dehydration
The applications of vacuum pumps in evacuation and dehydration are extensive and span numerous industries:
1. Food Processing:
Vacuum pumps are used to remove air and moisture from food products, extending their shelf life and preserving their quality. This includes applications like freeze-drying, vacuum packaging, and the dehydration of fruits and vegetables. Oil-free pumps are often preferred to avoid contaminating the food.
2. Pharmaceutical Industry:
In pharmaceutical manufacturing, vacuum pumps play a crucial role in various processes, including drying powders and removing solvents from drug formulations. Maintaining a clean and sterile environment is paramount, making oil-free pumps frequently necessary.
3. Electronics Manufacturing:
Vacuum pumps are essential for removing gases and moisture from electronic components during manufacturing. This ensures optimal performance and prevents corrosion. The precision required in electronics often necessitates specialized pumps capable of achieving high vacuum levels.
4. Chemical Processing:
Vacuum pumps are used in various chemical processes, including distillation, evaporation, and the removal of volatile organic compounds. The ability to handle aggressive chemicals is a crucial selection factor in this area.
5. Material Science:
Vacuum pumps are utilized in materials science for processes such as degassing, sintering, and the creation of thin films. Controlling the vacuum level is critical for achieving the desired material properties.
Maintenance and Troubleshooting of Vacuum Pumps
Proper maintenance is crucial for ensuring the longevity and efficient operation of vacuum pumps. Regular maintenance tasks include:
-
Checking oil levels (for oil-lubricated pumps): Maintaining the correct oil level is vital to prevent damage to the pump's internal components.
-
Replacing filters: Filters prevent contaminants from entering the pump, extending its lifespan.
-
Inspecting seals and gaskets: Worn seals and gaskets can lead to leaks and reduced vacuum performance.
-
Monitoring pump performance: Regularly checking the pump's vacuum level and pumping speed can help identify potential issues early on.
Troubleshooting common issues involves identifying the source of the problem:
-
Low vacuum level: This could be caused by leaks in the system, worn pump components, or insufficient pump capacity.
-
High vibration or noise: This could indicate problems with bearings, seals, or other internal components.
-
Overheating: Overheating could be due to excessive use, insufficient cooling, or a malfunctioning component.
Conclusion: Selecting the Right Vacuum Pump for Your Needs
Choosing the appropriate vacuum pump for evacuation and dehydration requires a thorough understanding of the specific application and its requirements. This includes considering the required vacuum level, pumping speed, gas composition, contamination concerns, budget, and maintenance requirements. By carefully assessing these factors, you can select a vacuum pump that ensures efficient, reliable, and safe operation for your process. While this guide provides a comprehensive overview, it's essential to consult with vacuum pump experts and manufacturers for specific guidance and tailored recommendations based on your unique application. Remember to prioritize safety and adhere to all relevant safety regulations when operating and maintaining vacuum pumps.
Latest Posts
Latest Posts
-
1 2 5 Mechanical System Efficiency Answers
Apr 07, 2025
-
Introduction To Community Population Public And Global Health
Apr 07, 2025
-
Sariyah Sets Challenging Sales Targets For Her Team
Apr 07, 2025
-
Which Publication Covers Army Sop Requirements And Responsibilities
Apr 07, 2025
-
The Theme Of The Secret Garden
Apr 07, 2025
Related Post
Thank you for visiting our website which covers about A Standard Vacuum Pump Designed Specifically For Evacuation And Dehydration . We hope the information provided has been useful to you. Feel free to contact us if you have any questions or need further assistance. See you next time and don't miss to bookmark.