Air Contained Within A Piston-cylinder Assembly Is Slowly Compressed
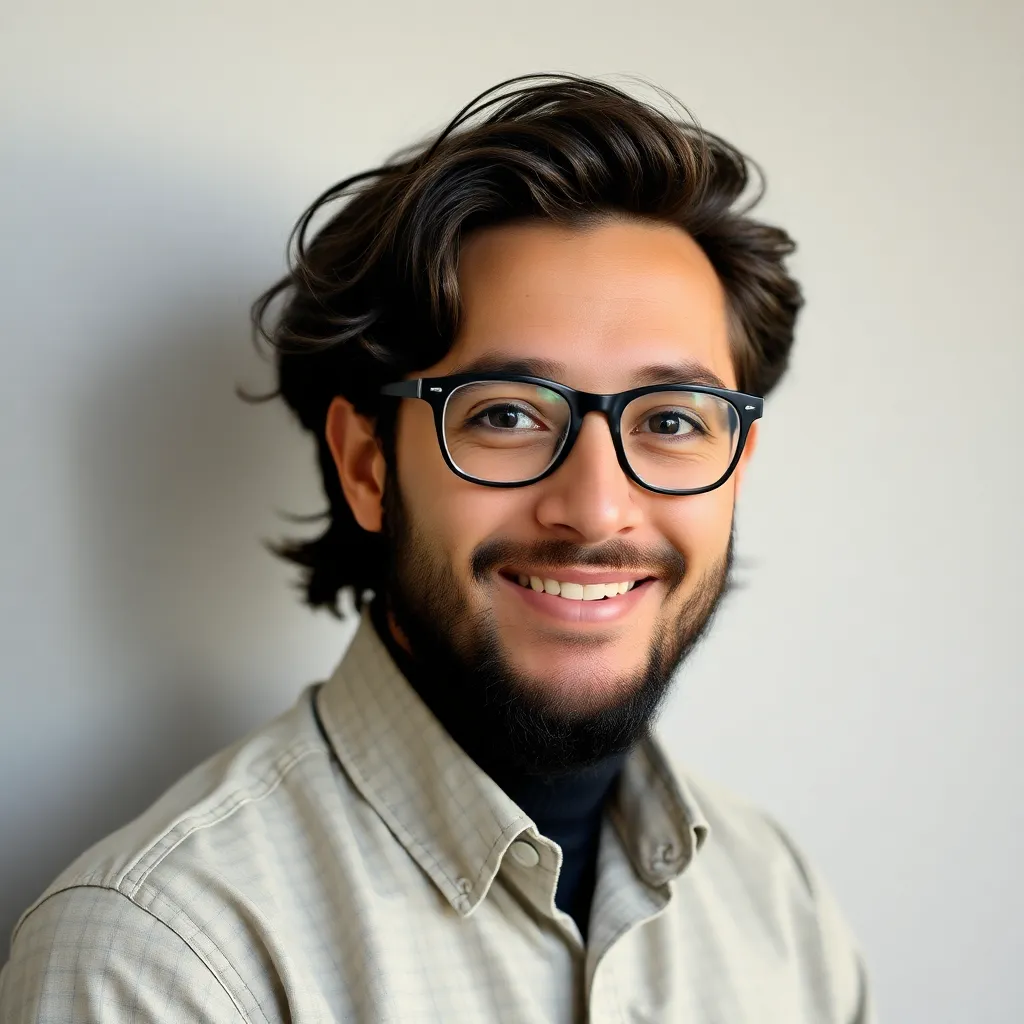
Onlines
May 10, 2025 · 6 min read
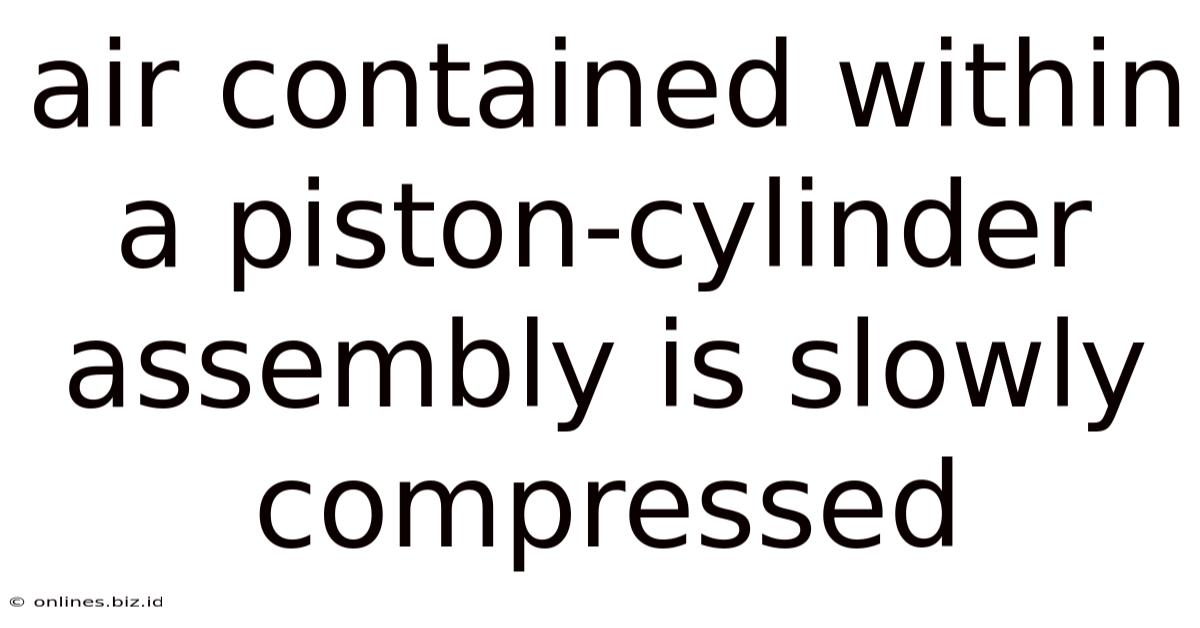
Table of Contents
Air Contained Within a Piston-Cylinder Assembly is Slowly Compressed: A Deep Dive into Thermodynamics
The seemingly simple scenario of air slowly compressed within a piston-cylinder assembly belies a rich tapestry of thermodynamic principles and practical applications. This process, fundamental to countless engineering systems, offers a fertile ground for exploring concepts like work, heat transfer, internal energy, and entropy. This detailed exploration delves into the intricacies of this process, examining various scenarios and their implications.
Understanding the Fundamentals: Ideal Gas Law and Assumptions
Before embarking on a detailed analysis, it's crucial to establish the foundational principles governing the behavior of the air within the piston-cylinder assembly. We will primarily employ the ideal gas law, a cornerstone of thermodynamics:
PV = nRT
Where:
- P represents pressure.
- V represents volume.
- n represents the number of moles of air.
- R represents the ideal gas constant.
- T represents temperature.
This equation assumes the air behaves as an ideal gas, meaning its molecules are point masses with negligible volume and interactions. While real air deviates from ideality, particularly at high pressures and low temperatures, the ideal gas assumption provides a reasonable approximation for many practical scenarios, especially when the compression process is slow, allowing for sufficient heat exchange with the surroundings.
Furthermore, we'll consider several simplifying assumptions throughout this discussion:
- The piston is frictionless: This eliminates energy losses due to friction between the piston and the cylinder walls.
- The cylinder is perfectly insulated (adiabatic process) or perfectly conductive (isothermal process): This allows for simplified analyses of adiabatic and isothermal compression, two key scenarios.
- The air is a closed system: No mass exchange occurs between the air within the cylinder and its surroundings.
Isothermal Compression: Constant Temperature
In an isothermal compression, the temperature (T) remains constant throughout the process. This necessitates heat exchange with the surroundings to maintain a constant temperature as the air is compressed. The work done on the gas during an isothermal compression is given by:
W = nRT ln(V<sub>initial</sub>/V<sub>final</sub>)
Where:
- W represents the work done on the gas.
- V<sub>initial</sub> represents the initial volume.
- V<sub>final</sub> represents the final volume.
The key characteristic here is that the work done depends solely on the initial and final volumes and the temperature. A slower compression process will allow for more efficient heat transfer, leading to a closer approximation of isothermal conditions. The system’s internal energy remains constant because temperature remains constant, and any work done on the gas is released as heat to the surroundings. The process is reversible under ideal conditions.
Applications of Isothermal Compression
Isothermal compression finds applications in various industrial processes:
- Refrigeration cycles: The compression stage in many refrigeration cycles approximates isothermal conditions, aiming for efficient cooling.
- Chemical processes: Maintaining constant temperature is crucial in some chemical reactions, and isothermal compression may be employed to control reaction conditions.
- Gas storage: Although not perfectly isothermal, the slow compression of gases into storage tanks often aims to minimize temperature changes.
Adiabatic Compression: No Heat Transfer
In contrast to isothermal compression, adiabatic compression occurs without any heat exchange between the system (the air) and its surroundings. This means the process is thermally isolated, preventing heat transfer, which is achieved with perfectly insulating walls. The relationship between pressure and volume in an adiabatic process is governed by:
PV<sup>γ</sup> = constant
Where:
- γ represents the ratio of specific heats (C<sub>p</sub>/C<sub>v</sub>). For diatomic gases like air, γ is approximately 1.4.
The work done during an adiabatic compression is more complex than in the isothermal case and is given by:
W = (P<sub>final</sub>V<sub>final</sub> - P<sub>initial</sub>V<sub>initial</sub>) / (1 - γ)
Due to the absence of heat transfer, the work done on the air directly increases its internal energy, leading to a temperature increase. This process is also irreversible unless infinitesimally slow.
Applications of Adiabatic Compression
Adiabatic compression plays a crucial role in:
- Internal combustion engines: The compression stroke in an internal combustion engine approximates adiabatic conditions, leading to a significant temperature rise that initiates combustion.
- Diesel engines: Diesel engines rely heavily on adiabatic compression to reach the high temperatures required for auto-ignition of the fuel.
- Jet engines: The compression stage in jet engines is a complex process, but adiabatic compression principles are central to its operation.
Polytropic Compression: A General Case
Both isothermal and adiabatic processes are idealizations. In reality, most compression processes fall somewhere between these two extremes. A polytropic process describes a more general case where the pressure-volume relationship follows:
PV<sup>n</sup> = constant
Where:
- n is the polytropic index, a constant that depends on the specific process. n = 1 for isothermal compression and n = γ for adiabatic compression.
The work done during a polytropic process can be calculated as:
W = (P<sub>final</sub>V<sub>final</sub> - P<sub>initial</sub>V<sub>initial</sub>) / (1 - n)
The polytropic index, 'n', allows for modeling processes with varying degrees of heat exchange, offering a more realistic representation of actual compression processes.
Effect of Compression Speed
The speed of compression significantly influences the process’s characteristics. A slow compression process allows more time for heat exchange, leading to a process closer to isothermal. Conversely, a rapid compression minimizes heat exchange, approaching adiabatic conditions. Therefore, the compression speed dictates how close the actual process aligns with idealized isothermal, adiabatic, or polytropic models.
Factors Affecting the Compression Process
Beyond the idealized scenarios, several factors influence the actual compression of air within a piston-cylinder assembly:
- Heat transfer rate: The rate of heat transfer to or from the surroundings significantly affects the process's path. Efficient heat transfer leads towards isothermal conditions, while poor heat transfer leads towards adiabatic conditions.
- Friction: Friction between the piston and cylinder walls causes energy losses, reducing the efficiency of the compression process and impacting the final temperature and pressure.
- Leakage: Leakage of air from the cylinder reduces the effective compression ratio and introduces inaccuracies in the calculations.
- Non-ideal gas behavior: At high pressures and low temperatures, air deviates from the ideal gas law, requiring more complex equations of state for accurate modeling.
Practical Applications and Engineering Significance
Understanding the compression of air within a piston-cylinder assembly is critical across various engineering disciplines:
- HVAC systems: Compressors in air conditioners and refrigerators rely on the principles of gas compression for cooling.
- Pneumatic systems: Pneumatic tools and systems use compressed air for power and actuation.
- Power generation: Many power generation systems, including internal combustion engines and gas turbines, employ air compression as a crucial step in their operation.
- Chemical engineering: Compression processes are essential in various chemical processes for controlling reaction conditions and product separation.
Conclusion: A Dynamic Process
The compression of air within a piston-cylinder assembly, while conceptually simple, presents a nuanced and complex thermodynamic process. The ideal gas law serves as a foundational framework, but real-world scenarios demand consideration of factors such as heat transfer rates, friction, leakage, and non-ideal gas behavior. Understanding these complexities is crucial for designing and optimizing various engineering systems that rely on the efficient and controlled compression of gases. Whether it's the precisely controlled compression in a refrigeration system or the rapid, forceful compression in an internal combustion engine, mastery of these principles remains paramount. The journey from simple compression to a deep understanding of the underlying thermodynamic laws represents a significant step toward effective engineering design and problem-solving. Furthermore, advancements in computational fluid dynamics (CFD) are allowing for increasingly accurate modelling of these complex processes, leading to further optimization and efficiency gains.
Latest Posts
Latest Posts
-
A First Course In The Finite Element Method 6th Edition
May 10, 2025
-
What Is The Value Of X 105o 115o 125o 135o
May 10, 2025
-
Commercial Agriculture In South America Is Best Typified By
May 10, 2025
-
At What Time Must A Policyowner Have Insurable
May 10, 2025
-
Which Theme Best Represents Vonneguts Story Harrison Bergeron
May 10, 2025
Related Post
Thank you for visiting our website which covers about Air Contained Within A Piston-cylinder Assembly Is Slowly Compressed . We hope the information provided has been useful to you. Feel free to contact us if you have any questions or need further assistance. See you next time and don't miss to bookmark.