At Which Area Of The Oblong Does Molding Begin
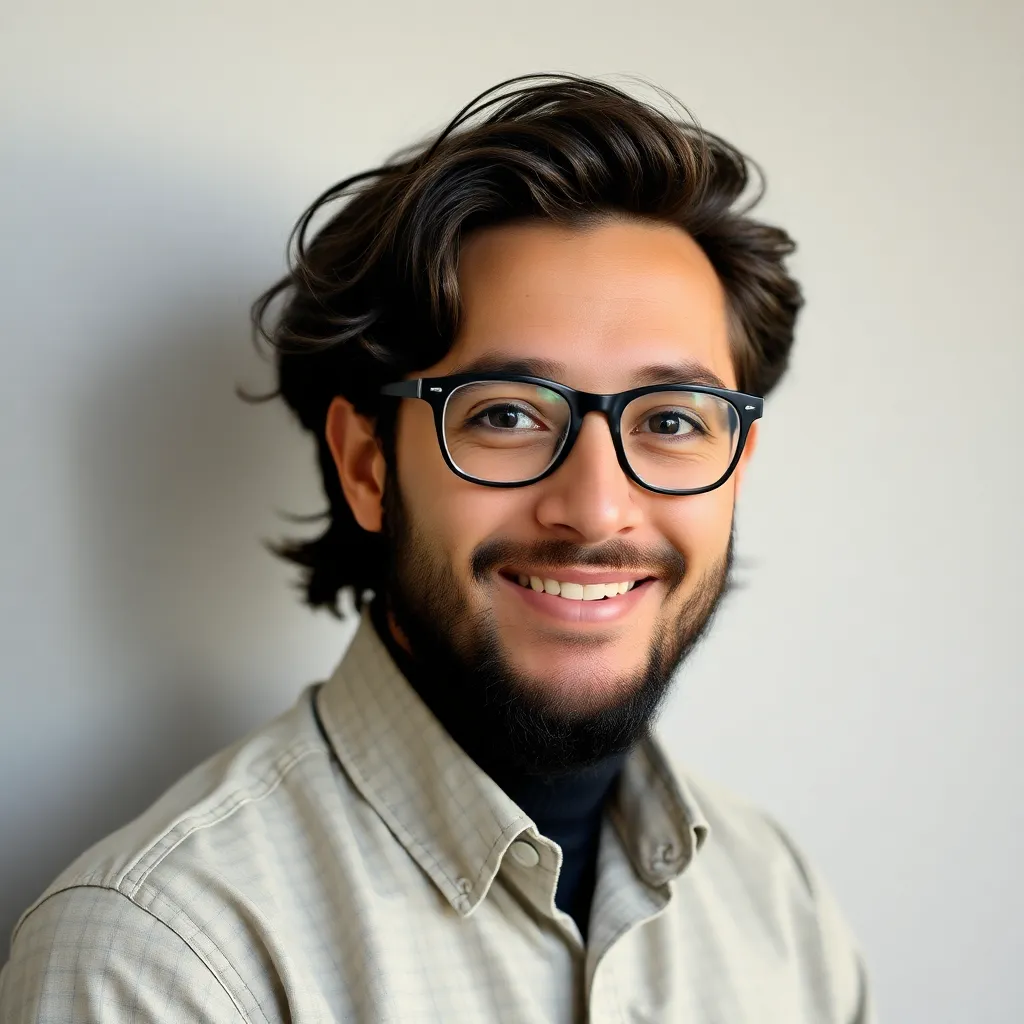
Onlines
Mar 19, 2025 · 5 min read
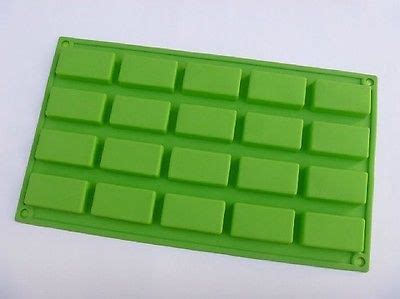
Table of Contents
Where Does Molding Begin on the Oblong? A Comprehensive Guide to Molding Techniques and Considerations
Molding, a fundamental process in manufacturing and artistic creation, involves shaping a material into a desired form using a mold. The "oblong," referring to a rectangular or elongated shape, presents unique challenges and opportunities in molding. Understanding where molding begins on an oblong, and the factors influencing this decision, is crucial for successful outcomes. This in-depth guide explores the intricacies of oblong molding, covering various techniques, materials, and design considerations.
Defining the Oblong and its Molding Challenges
Before delving into the specifics of molding initiation, let's define our subject. An oblong, in the context of molding, signifies a three-dimensional object with a rectangular or elongated profile. This shape presents several challenges compared to simpler geometries:
- Complex Surface Area: Oblongs often have multiple sides and potentially intricate details, demanding precise mold design and placement.
- Uniformity Challenges: Achieving consistent material distribution and thickness across all faces of the oblong requires careful planning and execution.
- Parting Line Considerations: The parting line, where the mold halves separate to release the molded part, must be strategically chosen to minimize defects and ensure clean release. This is especially critical on oblong shapes with sharp corners or detailed features.
- Material Flow: Controlling material flow within the mold cavity is essential to prevent voids, air pockets, or incomplete filling. This is particularly relevant with viscous materials or complex oblong designs.
Where Molding Begins: A Multifaceted Decision
Determining where molding begins on an oblong isn't a simple answer. The ideal starting point depends on several interconnected factors:
- Molding Process: The selected molding technique (injection molding, compression molding, rotational molding, etc.) heavily influences the starting point. Each process has its own peculiarities regarding material flow, pressure application, and mold design.
- Mold Design: The configuration of the mold itself, including the gate (material entry point), runners (channels directing material flow), and sprue (main channel leading to the mold cavity), dictates the molding sequence. Strategic placement of these elements is vital for optimal material distribution.
- Material Properties: The viscosity, flow characteristics, and shrinkage behavior of the molding material directly affect the starting point and filling process. Highly viscous materials may require multiple gates or a carefully optimized starting location to ensure complete filling.
- Parting Line Strategy: The placement of the parting line plays a pivotal role. It should be located where it minimizes stress on the mold and the molded part during opening and closing. Complex oblong shapes may need multiple parting lines for intricate features.
- Desired Surface Finish: The desired surface finish of the molded oblong impacts the choice of starting point. Smooth surfaces may require a carefully controlled flow, potentially necessitating a different starting position than a textured finish.
Different Molding Techniques and Their Starting Points
Let's examine several common molding techniques and how the starting point is determined in each case:
1. Injection Molding:
In injection molding, the molten material is injected into the mold cavity through a gate, typically located at one end of the oblong. The starting point, in this case, is the gate itself. Careful consideration must be given to gate placement to prevent short shots (incomplete filling) and to ensure uniform filling across the entire oblong. The gate location often minimizes flow disturbances and promotes a smooth surface finish.
2. Compression Molding:
Compression molding involves placing the material into the mold cavity and then applying pressure to shape it. The starting point in compression molding is less defined than in injection molding. The material is often pre-formed before being placed in the mold, so the "starting point" could be considered the initial positioning of the pre-form within the cavity. Uniform pressure distribution is key to ensure even compaction and prevent defects.
3. Rotational Molding:
Rotational molding uses a hollow mold that rotates to distribute molten material evenly across the inner surface. In this case, there is no distinct "starting point" in the same way as injection molding. The material is initially placed inside the mold before the rotation begins, and the centrifugal force during rotation is responsible for distributing the material evenly across the oblong shape. Uniform material distribution is paramount to avoiding thin spots or excess build-up in specific areas.
4. Vacuum Forming:
Vacuum forming uses a heated plastic sheet that is drawn down over a mold by a vacuum. The starting point in vacuum forming is the heated plastic sheet itself. The sheet is initially positioned above the mold, and the vacuum draws it down, conforming it to the oblong shape. Careful control of temperature and vacuum pressure is essential for preventing wrinkles or other defects.
Optimizing Molding Processes for Oblong Shapes
Several strategies can optimize the molding process for oblong shapes:
- Multiple Gates: Using multiple gates for injection molding can improve material flow, especially for large or complex oblongs. This ensures that the material reaches all parts of the mold cavity simultaneously, minimizing voids and improving consistency.
- Optimized Runner and Sprue Design: Efficient runner and sprue designs minimize material waste and improve flow characteristics. This is especially crucial in oblong molds to ensure consistent filling even in areas furthest from the gate.
- Cooling Channels: Strategically placed cooling channels within the mold can control the cooling rate of the molded part, preventing warping or stress cracking. This is critical for oblong shapes with larger surface areas and potentially uneven cooling rates.
- Material Selection: The selection of appropriate molding material is crucial for achieving desired properties and ensuring successful molding. Material properties like viscosity, shrinkage, and thermal conductivity will directly impact the starting point and overall molding process.
- Mold Material: The choice of mold material (e.g., steel, aluminum) affects its durability and thermal characteristics, influencing both the molding process and the longevity of the mold.
Conclusion: A Holistic Approach to Oblong Molding
Determining where molding begins on an oblong is a complex decision, far from a simple point on the shape. It's a holistic process involving meticulous planning, careful consideration of various factors, and a deep understanding of the chosen molding technique. By carefully analyzing the interplay between mold design, material properties, and process parameters, manufacturers and artists can optimize their processes, minimizing defects, maximizing efficiency, and achieving consistently high-quality results in their oblong molding projects. The starting point is but one piece of the larger puzzle of successful oblong molding. Understanding the complete picture is essential for mastering this intricate craft.
Latest Posts
Latest Posts
-
Which Of The Following Best Describes The Graph Below
Mar 19, 2025
-
Transport In Cells Pogil Answer Key
Mar 19, 2025
-
Signing Naturally 3 7 Identify And Draw Answers
Mar 19, 2025
-
Post Test The Early And Mid Nineteenth Century Romanticism
Mar 19, 2025
-
Nystrom Atlas Of World History Worksheets Answer Key Pdf
Mar 19, 2025
Related Post
Thank you for visiting our website which covers about At Which Area Of The Oblong Does Molding Begin . We hope the information provided has been useful to you. Feel free to contact us if you have any questions or need further assistance. See you next time and don't miss to bookmark.