Family Furniture Corporation Incurred The Following Costs
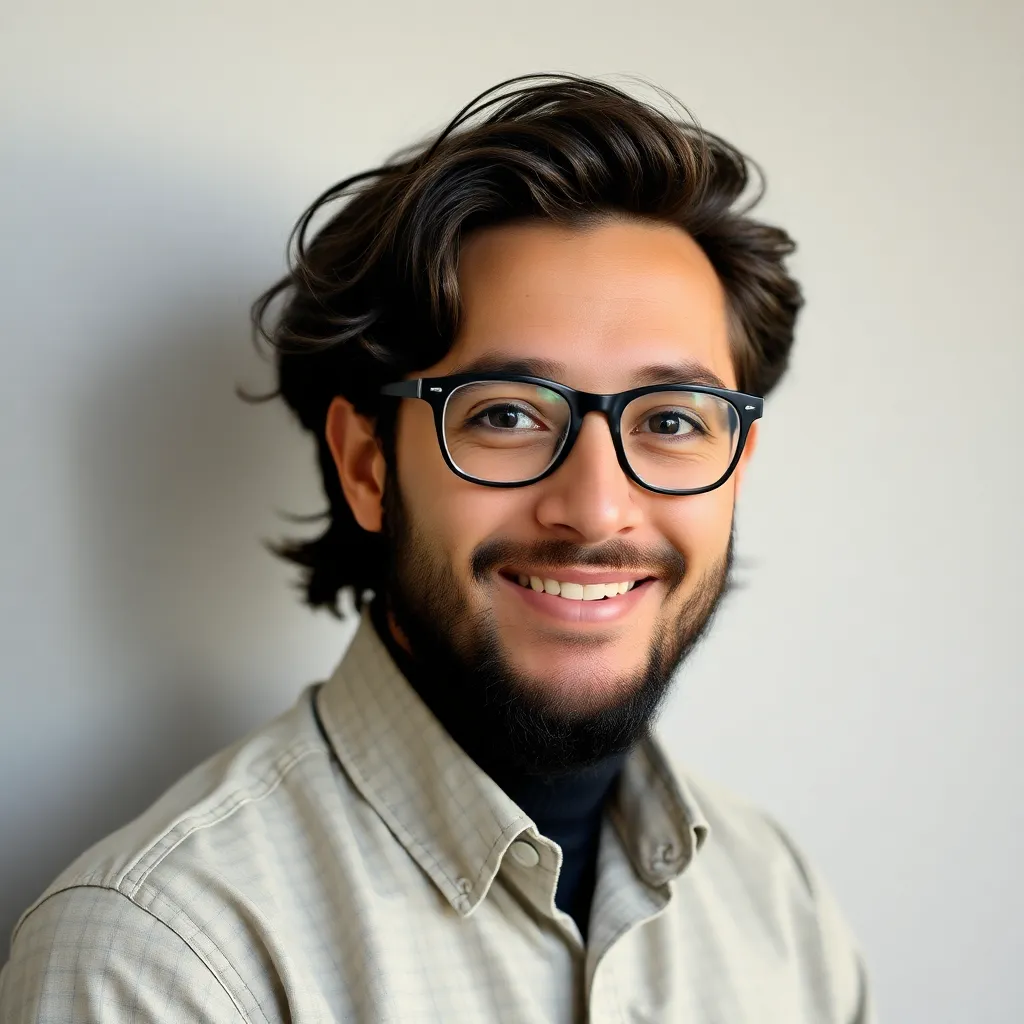
Onlines
Apr 02, 2025 · 6 min read
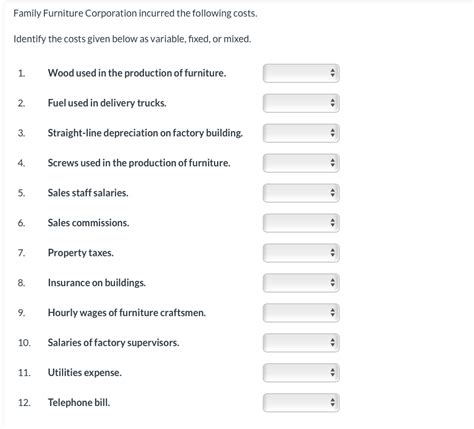
Table of Contents
Decoding Family Furniture Corporation's Costs: A Deep Dive into Financial Analysis
Family Furniture Corporation, like any business, incurs a variety of costs in its operations. Understanding these costs is crucial for effective financial management, strategic decision-making, and ultimately, profitability. This in-depth analysis will explore the various cost categories Family Furniture Corporation likely faces, examining their implications and providing insights into how these costs can be managed for optimal performance.
I. Cost Categories at Family Furniture Corporation:
Family Furniture Corporation's cost structure can be broadly categorized into several key areas:
A. Cost of Goods Sold (COGS): The Foundation of Furniture Production
COGS represents the direct costs associated with producing the furniture sold by Family Furniture Corporation. These costs are directly tied to the creation and delivery of the finished product. For Family Furniture Corporation, this category includes:
-
Raw Materials: This encompasses the lumber, fabrics, foam, hardware, and other materials directly used in furniture manufacturing. Fluctuations in raw material prices significantly impact COGS, making effective sourcing and inventory management critical. Strategic sourcing, negotiating favorable contracts with suppliers, and exploring alternative materials can mitigate price volatility.
-
Direct Labor: This refers to the wages and benefits paid to employees directly involved in furniture production, including carpenters, upholsterers, and assembly line workers. Optimizing production processes, investing in automation, and providing employee training to increase efficiency are crucial for controlling labor costs.
-
Manufacturing Overhead: This includes indirect costs associated with production, such as factory rent, utilities, machinery maintenance, and depreciation of manufacturing equipment. Careful budgeting, regular maintenance, and exploring energy-efficient technologies can help manage these overhead costs.
Analyzing COGS Trends: Analyzing COGS over time reveals crucial insights into production efficiency and pricing strategies. A rising COGS percentage compared to revenue signals potential issues, requiring a thorough review of raw material costs, labor efficiency, and manufacturing overhead.
B. Operating Expenses: Keeping the Business Running Smoothly
Operating expenses are costs incurred in running the business outside of direct production. These are vital but indirect costs that support the overall operations of Family Furniture Corporation. They include:
-
Selling, General, and Administrative (SG&A) Expenses: This broad category encompasses various costs associated with sales, marketing, administration, and general business operations. It includes:
-
Sales and Marketing Costs: Advertising, marketing campaigns (online and offline), sales commissions, and promotional expenses fall under this category. Effective marketing strategies, leveraging digital marketing tools, and data-driven campaign optimization can improve ROI on marketing spend.
-
Administrative Costs: This includes salaries for administrative staff, office rent, utilities, insurance, legal fees, and accounting expenses. Streamlining administrative processes, utilizing technology to automate tasks, and outsourcing non-core functions can help reduce these costs.
-
Research and Development (R&D): If Family Furniture Corporation invests in new designs, materials, or production techniques, these costs fall under R&D. This is crucial for long-term competitiveness and innovation. Balancing R&D investment with current profitability is a key strategic decision.
-
-
Distribution and Delivery Costs: The costs associated with transporting finished furniture to retail stores or directly to customers. This includes transportation expenses, warehousing costs, and handling fees. Optimizing delivery routes, using efficient logistics solutions, and negotiating favorable contracts with carriers are crucial for managing these costs.
Managing Operating Expenses: Regularly reviewing and analyzing operating expenses is crucial. Identifying areas of inefficiency, negotiating better contracts with suppliers, and implementing cost-saving measures are essential for improving profitability.
C. Financial Expenses: The Cost of Capital
Financial expenses represent the costs associated with financing the business. These costs are incurred irrespective of the production and sales activities. For Family Furniture Corporation, this could include:
-
Interest Expense: Costs associated with borrowing money, including loans, lines of credit, or bonds. Maintaining a healthy debt-to-equity ratio and exploring various financing options can help minimize interest expense.
-
Bank Charges: Fees charged by banks for services such as account maintenance, wire transfers, and loan processing. Negotiating favorable terms with banks and exploring alternative banking solutions can reduce these charges.
Minimizing Financial Expenses: A sound financial strategy is paramount. Careful budgeting, effective cash flow management, and a well-structured capital structure can significantly impact financial expenses.
II. Cost Accounting Methods for Family Furniture Corporation:
Understanding how Family Furniture Corporation tracks and allocates its costs is important. Several cost accounting methods can be employed:
A. Job Order Costing: Tracking Costs for Individual Furniture Pieces
Job order costing is ideal for businesses that produce customized or unique furniture pieces. Each furniture piece (the "job") is tracked separately, allowing for accurate cost determination for each individual item. This method offers excellent precision but can be labor-intensive for high-volume production.
B. Process Costing: Averaging Costs for Mass-Produced Furniture
Process costing is more suitable for mass-produced furniture items where many identical pieces are manufactured. Costs are averaged across the entire production process, providing a cost per unit. This method is efficient for high-volume production but may not capture variations in costs across individual pieces.
C. Activity-Based Costing (ABC): A More Refined Approach
ABC allocates costs based on activities involved in production and sales. It provides a more detailed understanding of cost drivers, allowing for better cost control and decision-making. ABC is more complex than job order or process costing but offers superior accuracy in cost allocation.
Choosing the Right Method: The most appropriate cost accounting method for Family Furniture Corporation depends on its production process, product mix, and the level of detail needed for cost management.
III. Cost-Volume-Profit (CVP) Analysis: Forecasting Profitability
CVP analysis is a valuable tool for Family Furniture Corporation to forecast profitability. By analyzing the relationship between costs, volume, and profit, the company can:
- Determine the break-even point: The point at which revenue equals total costs (both fixed and variable).
- Analyze the impact of changes in sales volume on profitability: Understanding how changes in sales affect profit margins.
- Assess the impact of changes in costs on profitability: Determining the sensitivity of profit to changes in fixed and variable costs.
CVP analysis helps in strategic planning, pricing decisions, and resource allocation.
IV. Cost Control and Reduction Strategies:
Effective cost management is essential for Family Furniture Corporation’s long-term success. Strategies include:
-
Lean Manufacturing: Implementing lean principles to eliminate waste in production processes, improving efficiency, and reducing costs.
-
Supply Chain Optimization: Improving the efficiency of the supply chain, including sourcing, logistics, and inventory management.
-
Technology Adoption: Utilizing technology to automate processes, improve efficiency, and reduce labor costs.
-
Negotiating with Suppliers: Negotiating favorable terms with suppliers to secure better prices for raw materials.
-
Pricing Strategies: Implementing effective pricing strategies to maximize profitability while remaining competitive.
V. Conclusion:
Understanding and managing costs is crucial for Family Furniture Corporation's financial health and long-term sustainability. By employing appropriate cost accounting methods, performing regular CVP analysis, and implementing strategic cost control measures, Family Furniture Corporation can improve its profitability, enhance its competitive position, and achieve its business objectives. Continuous monitoring, analysis, and adaptation to market conditions are essential for sustained success in the dynamic furniture industry. This detailed analysis provides a framework for Family Furniture Corporation to delve deeper into its cost structure, identify areas for improvement, and ultimately, achieve greater profitability.
Latest Posts
Latest Posts
-
Secondary Math 2 Module 1 Answers
Apr 03, 2025
-
The Grapes Of Wrath Character List
Apr 03, 2025
-
When Stacking Materials Such As Bricks Ratio
Apr 03, 2025
-
A Recommended Procedure Regarding Decontamination Is To
Apr 03, 2025
-
Medical Terminology Crossword Puzzle Answer Key
Apr 03, 2025
Related Post
Thank you for visiting our website which covers about Family Furniture Corporation Incurred The Following Costs . We hope the information provided has been useful to you. Feel free to contact us if you have any questions or need further assistance. See you next time and don't miss to bookmark.