If A Technician Suspects A Repeat Repair
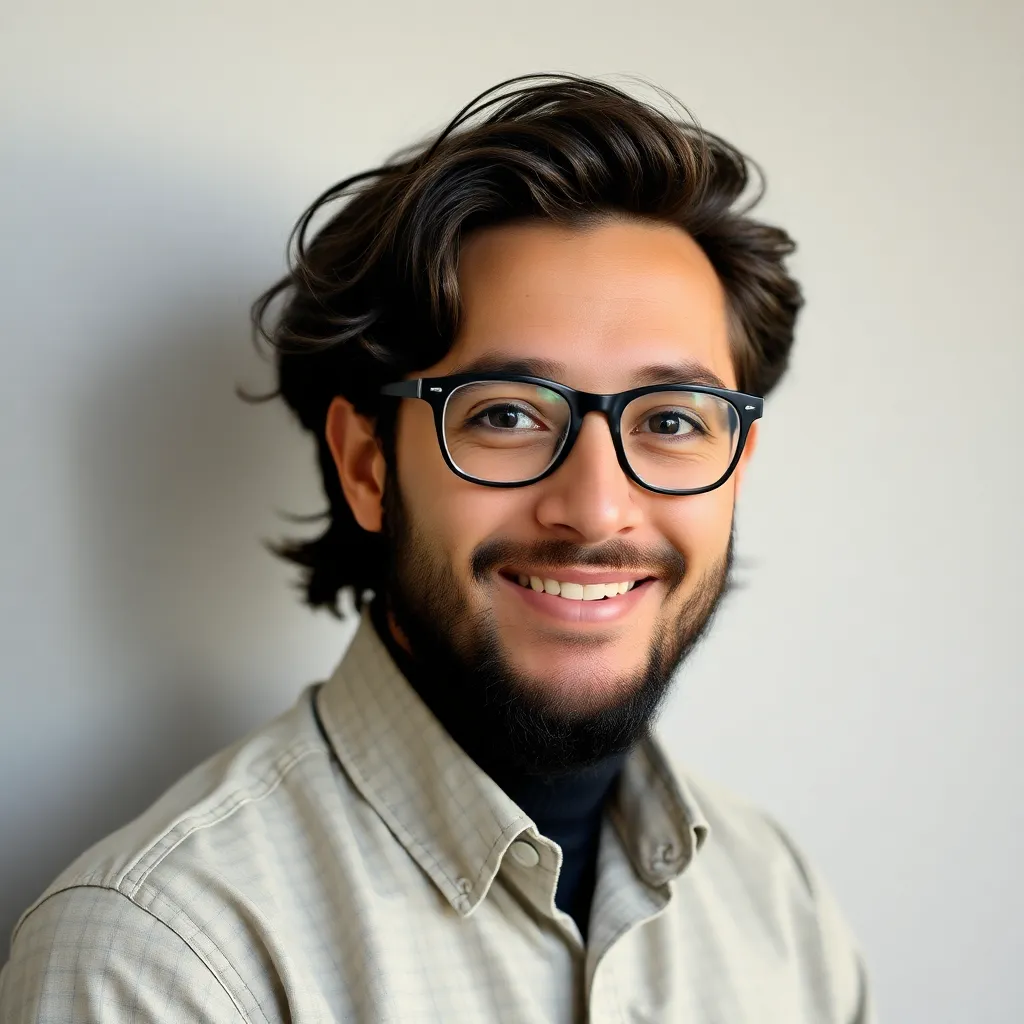
Onlines
Mar 18, 2025 · 6 min read
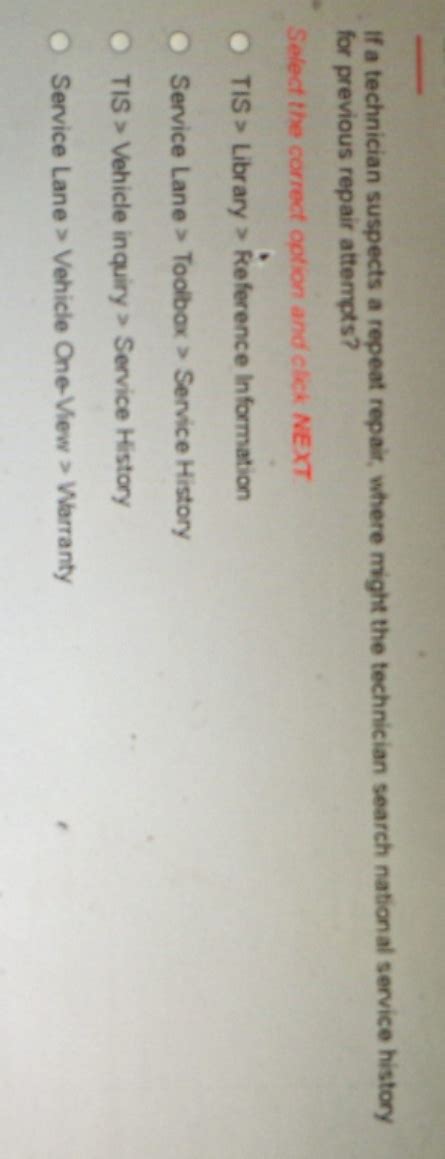
Table of Contents
If a Technician Suspects a Repeat Repair: Proactive Strategies for Prevention and Customer Satisfaction
Repeat repairs are a common headache for technicians and businesses alike. They represent lost time, wasted resources, and potentially unhappy customers. While some repeat repairs are unavoidable due to unforeseen circumstances or product defects, many can be prevented with proactive strategies. This article delves into identifying the signs of potential repeat repairs, implementing preventative measures, and fostering strong customer relationships to minimize this costly issue.
Identifying the Signs of a Potential Repeat Repair
Before a repair even leaves the workshop, a technician can often identify factors that might predict a future return visit. These are critical indicators to watch for:
1. Incomplete Repairs:
This is perhaps the most obvious sign. If a repair isn't completed thoroughly, addressing only the immediately visible problem without diagnosing and addressing underlying issues, a repeat repair is almost guaranteed. Lack of comprehensive testing after repairs is a major contributor. A thorough check of all relevant systems and functionalities is crucial before declaring the repair complete.
- Example: A customer brings in a laptop with a malfunctioning keyboard. The technician replaces the faulty key, but doesn't check for potential driver conflicts or other software issues that might have contributed to the problem. The customer returns when the issue reappears due to the unresolved root cause.
2. Inadequate Documentation:
Poor record-keeping is another significant factor leading to repeat repairs. Detailed and accurate documentation is essential for tracking the repair process, identifying potential problems, and facilitating future troubleshooting. If the previous repair's details are unclear or missing, diagnosing the issue upon a second visit becomes significantly harder, potentially leading to an incorrect or incomplete fix.
- Example: A technician fails to record the specific model number of a replaced component. During a future repair, identifying the correct replacement part becomes difficult, potentially leading to further issues.
3. Substandard Parts or Materials:
Using low-quality components or materials may seem cost-effective initially, but this strategy often backfires. Substandard parts are more prone to failure, leading to early replacements and customer dissatisfaction. This necessitates a commitment to using high-quality, reputable parts to minimize the risk of repeat repairs.
- Example: A technician uses a cheap, generic replacement part instead of an original manufacturer's part. The generic part fails prematurely, resulting in the customer needing to return for another repair.
4. Incorrect Diagnosis:
Misdiagnosis is arguably the most frustrating cause of repeat repairs. Accurate diagnosis requires thorough investigation, including symptom analysis, testing, and potentially using diagnostic tools. A hurried or superficial diagnosis can lead to an ineffective repair and a subsequent return visit.
- Example: A technician attributes a computer's slow performance to insufficient RAM without investigating potential malware infections or hard drive problems. The customer returns when the slow performance persists after simply adding RAM.
5. Customer Misuse or Neglect:
While not directly the technician's fault, understanding how a customer uses the equipment can help prevent repeat repairs. Identifying potential misuse or a lack of proper maintenance can prevent future problems. Educating the customer on proper care and use is a crucial part of this.
- Example: A customer continually drops their phone, resulting in repeated screen repairs. Educating them on the importance of a protective case could reduce future repair requests.
Proactive Strategies for Preventing Repeat Repairs
Preventing repeat repairs requires a multi-faceted approach, encompassing various strategies within the repair process and beyond:
1. Comprehensive Diagnostics and Root Cause Analysis:
This should be the cornerstone of any repair strategy. Instead of simply addressing the visible symptom, dig deeper to identify the underlying cause. Use diagnostic tools, perform thorough testing, and rule out other potential issues. This prevents a symptom-based approach from masking the root problem.
2. Detailed and Accurate Documentation:
Maintain detailed records of every repair, including:
- Date and time of repair: Essential for tracking repair history.
- Customer information: Name, contact details, and relevant account information.
- Device information: Make, model, serial number, and other relevant details.
- Problem description: A clear and concise explanation of the reported problem.
- Diagnosis: A detailed explanation of the identified problem and its root cause.
- Repair procedure: A step-by-step description of the repair process.
- Parts used: Including part numbers and manufacturer information.
- Testing performed: Detailed description of the testing conducted after the repair.
- Technician's signature or identification: Ensuring accountability and traceability.
Utilize a robust repair management system – whether digital or paper-based – to ensure consistency and clarity in documentation.
3. Quality Parts and Materials:
Always opt for high-quality, reputable parts and materials. While initial costs might be higher, the long-term cost savings from avoiding repeat repairs far outweighs this upfront investment. This includes adhering to manufacturers' specifications and recommendations.
4. Thorough Testing and Quality Control:
Before returning a device to the customer, conduct rigorous testing to ensure the repair has been successful and that no new problems have been introduced. This includes stress testing and functionality checks under various operating conditions. A final quality check before release is crucial in preventing immediate returns.
5. Customer Education and Training:
Educate the customer on proper use and maintenance of the device. This can involve providing written instructions, offering training sessions, or simply having a conversation about preventing future issues. Empowering customers with knowledge minimizes the likelihood of misuse or neglect.
6. Continuous Improvement and Training:
Regularly review repair data to identify trends and patterns in repeat repairs. This helps pinpoint areas needing improvement, whether it’s refining diagnostic procedures or updating technician training. Invest in ongoing professional development for technicians to keep their skills sharp and up-to-date with technological advancements.
7. Proactive Communication and Follow-up:
After the repair, follow up with the customer to ensure they are satisfied and that the repair is performing as expected. A simple phone call or email can significantly impact customer satisfaction and prevent potential repeat visits due to minor issues that were overlooked. This also provides valuable feedback that contributes to continuous improvement.
Building Strong Customer Relationships to Minimize Repeat Repairs
Customer relationships are paramount in minimizing repeat repairs. A satisfied customer is less likely to seek a second opinion or return with frivolous complaints.
1. Excellent Customer Service:
Treat every customer with respect and professionalism. Listen attentively to their concerns, explain the repair process clearly, and answer their questions thoroughly. A positive customer experience fosters trust and loyalty, reducing the likelihood of disputes and repeat repairs.
2. Transparency and Communication:
Keep customers informed throughout the repair process. Provide regular updates on the progress of the repair and address any concerns or questions promptly. Transparency builds trust and reduces customer anxiety.
3. Warranty and Guarantees:
Offer a reasonable warranty or guarantee on repairs. This demonstrates confidence in the quality of the work and provides customers with peace of mind. A well-defined warranty reduces the risk of disputes and increases customer satisfaction.
4. Feedback Mechanisms:
Implement a system for gathering customer feedback, such as surveys or feedback forms. This enables you to identify areas for improvement and address potential issues before they lead to repeat repairs or negative reviews. Act upon the feedback received to show customers their opinions are valued.
5. Conflict Resolution:
Establish a clear process for handling customer complaints and resolving conflicts. Address complaints promptly and fairly, striving to find mutually acceptable solutions. A fair and transparent complaint resolution process demonstrates professionalism and commitment to customer satisfaction.
By combining robust diagnostic procedures, comprehensive documentation, quality control measures, and excellent customer service, technicians can significantly reduce the frequency of repeat repairs. This leads to increased efficiency, improved profitability, and enhanced customer satisfaction. Remember, prevention is always better than cure, and proactive strategies are key to building a reputation for quality and reliability.
Latest Posts
Latest Posts
-
Nurse Toni Is Reviewing The Handout About Iv Pain
Mar 18, 2025
-
Procedure 1 Tracing Blood Flow Patterns
Mar 18, 2025
-
E 5 Analyze Rhetorical Strategies In Historical Texts Set 1
Mar 18, 2025
-
Who Should Be Contacted Before Starting New Construction
Mar 18, 2025
-
5 06 Unit Test Critical Skills Practice 3
Mar 18, 2025
Related Post
Thank you for visiting our website which covers about If A Technician Suspects A Repeat Repair . We hope the information provided has been useful to you. Feel free to contact us if you have any questions or need further assistance. See you next time and don't miss to bookmark.