Logisctix Company Had The Following Tiems
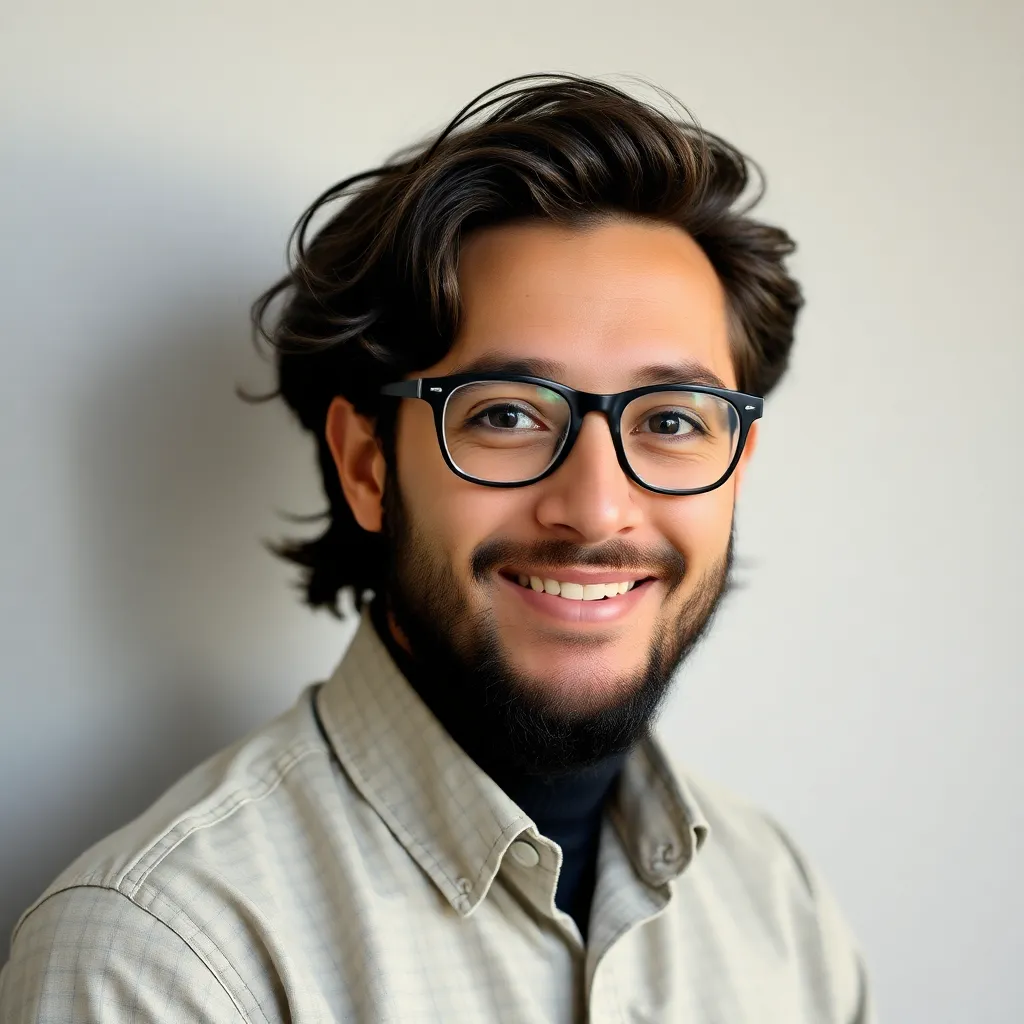
Onlines
Mar 09, 2025 · 6 min read
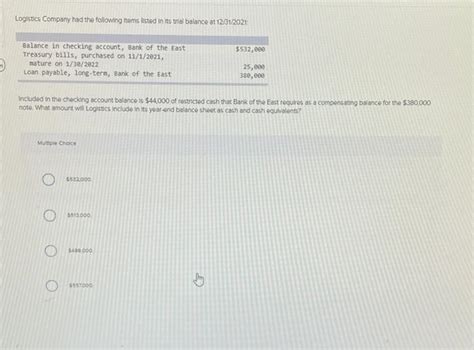
Table of Contents
Logistix Company Inventory Management: A Deep Dive into Optimization Strategies
Logistix Company, a hypothetical entity for the purposes of this article, faces the common challenge of effectively managing its inventory. This article delves into various aspects of inventory management, exploring strategies and techniques that Logistix (and other similar companies) can implement to optimize their processes, reduce costs, and improve overall efficiency. We'll cover topics ranging from inventory control methods to advanced analytics and the role of technology in modern logistics.
Understanding the Inventory Landscape at Logistix Company
Before diving into optimization strategies, let's first understand the scope of the inventory challenge at Logistix. We'll assume, for illustrative purposes, that Logistix handles a diverse range of items, including:
-
Raw Materials: These are the basic inputs required for production, potentially including various metals, plastics, electronics components, textiles, or agricultural products depending on Logistix's industry. Effective management of raw materials is crucial to prevent production delays and ensure a consistent supply chain.
-
Work-in-Progress (WIP): This category includes partially finished goods that are still undergoing processing or assembly. Tracking WIP inventory helps Logistix monitor production progress and identify potential bottlenecks.
-
Finished Goods: These are the completed products ready for sale and distribution. Efficient management of finished goods is vital to meet customer demand while minimizing storage costs and preventing obsolescence.
-
Maintenance, Repair, and Operations (MRO) Supplies: These are items necessary for maintaining equipment and facilities, ensuring smooth operation. This category might include tools, spare parts, cleaning supplies, and lubricants.
-
Packaging Materials: Logistix needs packaging materials – boxes, fillers, labels, and tape – to protect and prepare finished goods for shipment. Efficiently managing these materials is essential for cost control and order fulfillment.
The complexity of this diverse inventory presents Logistix with the need for sophisticated inventory management strategies.
Core Inventory Management Techniques for Logistix
Several key techniques are essential for Logistix to effectively manage its inventory:
1. Inventory Control Systems: The Foundation of Efficiency
A robust inventory control system is paramount. This system should incorporate:
-
Accurate Data Tracking: Real-time visibility into inventory levels, location, and movement is crucial. This involves utilizing barcodes, RFID tags, or other technologies for item identification and tracking. Manual data entry should be minimized to reduce errors.
-
Regular Stock Takes: Periodic physical counts of inventory ensure that the recorded data accurately reflects the physical reality. This helps identify discrepancies and rectify any data inaccuracies. Cycle counting, where a smaller portion of the inventory is counted regularly, is more efficient than a full inventory count.
-
First-In, First-Out (FIFO): This method ensures that the oldest items are sold first, minimizing the risk of spoilage or obsolescence, especially crucial for perishable goods or products with short shelf lives.
-
Last-In, First-Out (LIFO): While less common for many industries, LIFO can be relevant in certain situations, particularly when dealing with commodities whose prices fluctuate significantly.
-
Just-in-Time (JIT) Inventory: This approach minimizes inventory levels by receiving materials only when needed for production. JIT requires close coordination with suppliers and accurate demand forecasting. It's highly effective in reducing storage costs but demands a high degree of precision and responsiveness in the supply chain.
2. Demand Forecasting: Predicting the Future
Accurate demand forecasting is critical for preventing stockouts or overstocking. Logistix can employ various forecasting techniques:
-
Simple Moving Average: This method averages demand over a specific period. It’s easy to calculate but may not be accurate for products with seasonal or irregular demand patterns.
-
Weighted Moving Average: This assigns different weights to demand data from different periods, giving more weight to recent data. This improves accuracy compared to a simple moving average.
-
Exponential Smoothing: This method assigns exponentially decreasing weights to older data, making it more responsive to recent trends.
-
ARIMA Models: These are more advanced statistical models that can capture complex patterns in demand data. They require more expertise to implement but can provide more accurate forecasts.
-
Machine Learning: Advanced machine learning algorithms can analyze vast datasets to predict future demand with higher accuracy, considering various external factors.
3. Inventory Optimization Software: Leveraging Technology
Logistix should consider implementing inventory optimization software. This software can:
-
Automate tasks: Software can automate data entry, tracking, and reporting, freeing up human resources for more strategic tasks.
-
Optimize ordering: Software can analyze demand forecasts and inventory levels to determine optimal order quantities and timing.
-
Improve forecasting accuracy: Sophisticated software can incorporate various data sources and advanced algorithms to improve demand forecasting accuracy.
-
Reduce storage costs: Software can help optimize warehouse layout and space utilization to minimize storage costs.
-
Enhance supply chain visibility: Software can integrate with various systems throughout the supply chain, providing a holistic view of inventory flow.
Advanced Strategies for Logistix's Inventory Management
Beyond the core techniques, Logistix can leverage more advanced strategies:
1. ABC Analysis: Prioritizing Inventory
ABC analysis categorizes inventory items based on their value and consumption. High-value items (A) require tight control and frequent monitoring, while low-value items (C) require less attention. This prioritization allows Logistix to allocate resources effectively.
2. Safety Stock Management: Buffering Against Uncertainty
Maintaining a safety stock is crucial to mitigate risks associated with unexpected demand fluctuations or supply chain disruptions. Determining the optimal safety stock level involves considering factors such as lead time, demand variability, and service level requirements.
3. Vendor-Managed Inventory (VMI): Collaboration with Suppliers
VMI involves transferring responsibility for inventory management to a supplier. This can lead to reduced inventory costs and improved supply chain efficiency, but requires a high degree of trust and collaboration with suppliers.
4. Warehouse Management Systems (WMS): Optimizing Warehouse Operations
A WMS is a software system that manages and optimizes warehouse operations, including receiving, put-away, picking, packing, and shipping. It helps improve efficiency, reduce errors, and optimize space utilization.
5. RFID Technology: Enhancing Tracking and Visibility
Radio-frequency identification (RFID) technology uses tags to track items throughout the supply chain, providing real-time visibility into inventory location and movement. This significantly improves accuracy and efficiency compared to barcode systems.
The Role of Data Analytics in Logistix's Inventory Success
Data analytics plays a crucial role in optimizing Logistix's inventory management. By analyzing historical data, Logistix can identify patterns, trends, and anomalies that can inform better decision-making. This includes:
-
Identifying slow-moving items: Analytics can help pinpoint items that are not selling well, allowing Logistix to adjust pricing, promotion, or discontinue the product.
-
Optimizing order quantities: Data analysis can help determine the optimal order quantities to minimize carrying costs while ensuring sufficient inventory to meet demand.
-
Predicting future demand: Advanced analytics techniques can improve the accuracy of demand forecasts, leading to better inventory planning.
-
Improving supply chain efficiency: Analytics can identify bottlenecks and inefficiencies in the supply chain, enabling Logistix to optimize processes and reduce costs.
-
Detecting anomalies: Data analysis can help detect unusual patterns or anomalies that could indicate potential problems, such as theft, damage, or inaccurate data entry.
Conclusion: Building a Resilient and Efficient Inventory System for Logistix
Effective inventory management is crucial for Logistix's success. By implementing the strategies and techniques discussed in this article – from fundamental inventory control methods to advanced analytics and technology integration – Logistix can build a resilient and efficient inventory system. This will lead to reduced costs, improved customer service, and a stronger competitive advantage in the marketplace. Continuous monitoring, adaptation, and a commitment to data-driven decision-making are vital for long-term success in managing the complexities of inventory. Remember that the best approach is tailored to the specific needs and characteristics of Logistix's business, industry, and inventory profile. Regular review and refinement of strategies are key to ongoing optimization and success.
Latest Posts
Latest Posts
-
What Is Sindbad Most Motivated By In This Passage
Mar 09, 2025
-
Out Of The Silent Planet Book Summary
Mar 09, 2025
-
Which Revision Of The Sentence Uses Parallel Structure 2 4 3
Mar 09, 2025
-
Eating Soup That Has Been Time Temperature Abuse Can Result In
Mar 09, 2025
-
The Image Was Created Most Directly In Response To
Mar 09, 2025
Related Post
Thank you for visiting our website which covers about Logisctix Company Had The Following Tiems . We hope the information provided has been useful to you. Feel free to contact us if you have any questions or need further assistance. See you next time and don't miss to bookmark.